How to convert from colony to barn eggs and hit retail specs
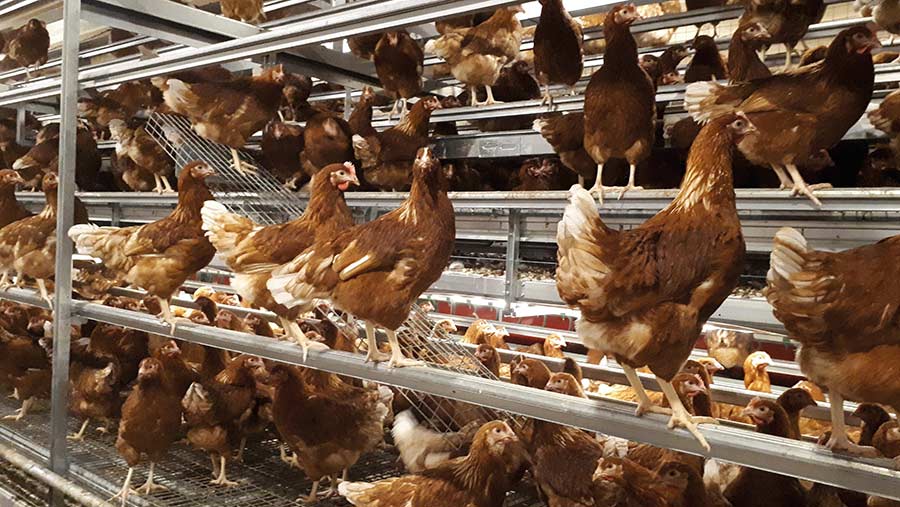
Colony egg producers who supply major retailers are facing deadlines to convert to an alternative system, with barn the proposed value egg option.
Morrisons supermarket has already switched to offer all shell eggs from cage-free systems.
The others in the big six – Tesco, Aldi, Lidl, Sainsbury’s and Asda – are committed to ban colony-produced shell eggs by 2025.
See also: 4 key poultry management factors influencing egg size
Given that some colony producers may still be paying off investments made in 2012, when colony egg units replaced conventional battery cages, producers should weigh up the return on investment and ensure they have a market to sell into, says Ms Hiscock.
Some processors are actively encouraging conversion, and colony sheds are more suited to barn production than to free-range.
A Lion Code standard was agreed in November 2019, and the British Egg Industry Council (BEIC) set out new standards for barn units (see What are the barn egg standards? below).
These standards apply to all converted and newly built barns, with a derogation for existing units until 31 December 2025.
What’s the market?
According to the BEIC, colony eggs made up 42% of the total egg market in 2019, compared to 56% free-range and just 2% barn.
Processing and foodservice comprised 41% of the market, against retail at 59%.
For those supplying eggs for processing it is not all upheaval as there is still a market, explains Lily Hiscock, partner at Andersons consultants.
It is within the retail sector where big change is coming.
Retailers sold 67% free-range eggs, 32% colony and just 1% barn eggs in 2019, so a significant number of colony producers will need to change tack, and converting to barn production is one option. But the numbers need to stack up, warns Miss Hiscock.
“Retailers are looking at barn to provide the value egg instead of colony. Although barn eggs will command a higher price, if they are to fill the value egg gap, then supermarkets can’t pay much more than for colony eggs.”
But the cost of producing barn eggs is 10-15p per dozen higher than colony – so unless producers can find efficiencies that gap might be hard to fill.
When budgeting for a potential conversion, it’s important to consider that fewer birds can be kept per shed due to stocking density standards.
A colony shed capable of housing 100,000 birds could only house half that number in a barn system. Added to that the conversion cost itself is about £16-£18 a bird.
If the numbers stack up and a buyer is in place, what are the stages of a conversion?
The conversion process
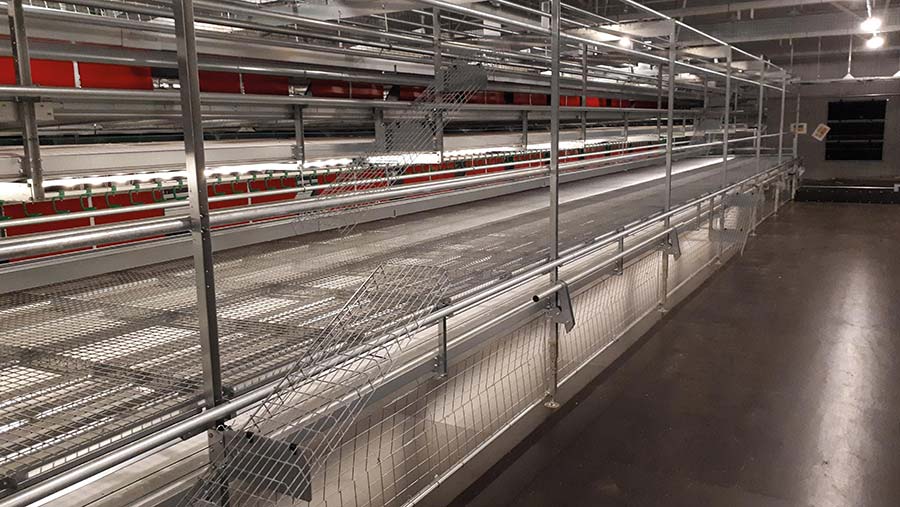
© Vencomatic UK
1. Discuss plans and choose a contractor
The first thing to do is discuss plans with your packer, then research costs, contractors, equipment suppliers and project management, says Ben McGill, technical director at Vencomatic Poultry.
The changeover should take about six months, but conversions are notoriously difficult, and there is a strong chance unforeseen issues will arise.
For example, a piece of equipment could get damaged and need replacing, or weather and access can cause difficulties. Covid-19 and Brexit may also reduce labour availability or delays in supplies. Mr McGill advises factoring in around 10% extra contingency for the total project cost.
Given the heavy lifting equipment, personnel and contractors required, health and safety and site management are critical.
Assess potential principal contractors carefully because they need to provide assurance that they are capable of managing this. Look at companies that have done conversions before.
2. Full or part conversion?
A decision has to be taken about how much of the colony installation needs to be ripped out.
Starting with a blank canvas inside the sheds, with only mains water and electricity supply, is the ideal setup when converting.
“You are spending good money on refitting, so don’t leave in one bit of old equipment that will let the new system down,” says Mr McGill.
The gable end wall might need to be removed, with the cages taken out chunk by chunk. Stripping the shed could take up to six weeks – and costs will vary according to the amount of scrap disposal required.
3. Get the right system and layout
Based on BEIC guidance, the equipment for barns should be tailored to maximise floor space.
This may mean opting for an aviary system, so that nine birds a sq m of usable space matches as closely as possible to the maximum 16.5 birds a sq m of floor space. This will make the most of bird numbers, efficiencies and margins.
Utilising the height of the building is another way to do this, by constructing fully isolated and individually ventilated floors.
“Remember that these floors need to be workable for staff, user friendly and easy to manage – you will likely be keeping this setup for the next 20 years,” says Mr McGill.
Ventilation will need to be changed to account for the switch from having manure belts under cages to a floor covered in litter.
The design process and supplier are key; explore air scrubbers and other mitigating factors to reduce ammonia and fine dust emissions.
Aside from the essentials, systems can be tailored to include further welfare options and enrichment. “This will provide a point of difference and give you something to shout about to your packing company,” says Mr McGill.
Producers should also ensure their pullets are trained to move from floor to system and between perches.
This is best achieved through a purpose-built multi-tier aviary rearing system with the same lighting, to ensure a smooth transition to the laying environment.
4. Equipment installation
Equipment costs will depend on bird numbers and the size of the project, as well as the system options that producers go for.
“It’s very tricky to put a figure on: The key is to maximise bird numbers, ensure barns are easy to manage, require little labour, are easily maintained and are built for longevity,” he says.
When assessing the kit you require, factor in what is needed for clean-out and turnaround.
Under-system scrapers are great during the flock cycle for controlling potential floor eggs, and at turnaround in both single- and multi-layered barn systems. They are a much simpler solution than getting a mini-excavator, such as a Bobcat, on to the third floor of a barn.
What are the barn egg standards?
The EU Welfare of Laying Hens Directive barn standards
- Nine hens a sq m max usable area (includes slatted area on system)
- 15cm of perch a hen
- One-third of ground surface must be litter
- One nest box for five hens or communal nests
- 120 birds a sq m of floor area
- Linear feeders provide 10cm a hen
- Circular feeders provide 4cm a hen
- Water and feeding troughs must be raised
- Electric lighting for optimum day length (16 hours max)
Additional Lion Code barn requirements
- 16.5 hens a sq m max floor space
- Two enrichments for 1,000 birds
- Maximum colony size of 6,000 birds
- Superior nest boxes – solid-sided and no wire