How a layer unit expanded rapidly with focus on welfare
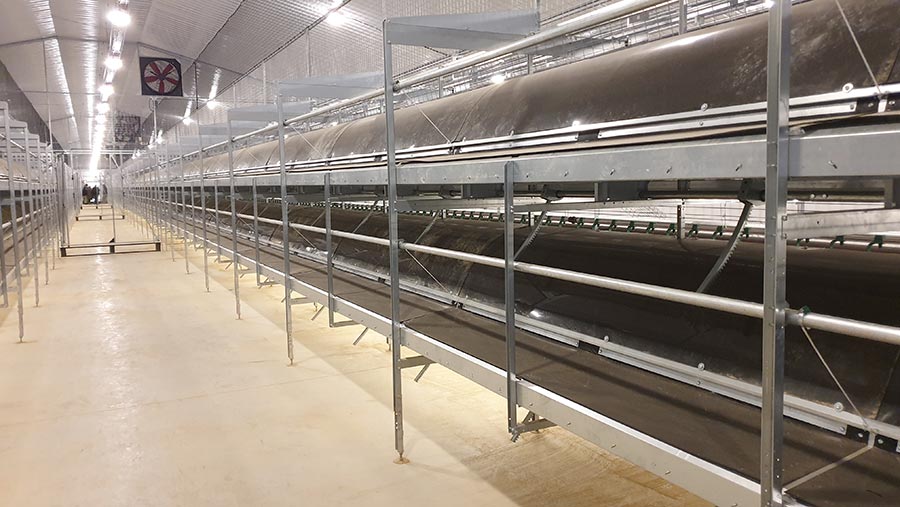
A Devon poultry farm has grown from 6,000 bird places to 22,000 in just eight months, and hopes its new modern unit will improve egg numbers and bird health.
Clayewater Farms produces premium free-range eggs at Rollestone Farm, Umberleigh, on contract to Stonegate.
Historically, the flock comprised Burford Browns and Cotswold Legbars, producing, on average, 317 eggs a bird a year.
They are depopulated at about 72 weeks, allowing an empty period of four weeks for deep cleaning.
See also: 9 ways to have disease-free poultry ranges in winter
The Webber family’s free-range egg business started out more than half a century ago with the supply of eggs to locals from the home farm.
Today, Clayewater Farms remains a family business, headed up by owner Brian Webber, with his children Anya and Hayden as operational managers.
Old setup
The old setup comprised two flat-deck systems, each housing 3,000 layers, with large scratching areas.
Egg production and quality were good, while mortality and disease challenges were low.
But although the birds were happy and healthy, the site and system were limited for expansion, so the family decided to develop the business at Higher Down Farm with a new modern unit.
Modern multi-tier unit
The family chose the Vencomatic Veranda Aviary 2 system because of the high-welfare features built into its design.
Miss Webber explains: “When we were looking at systems, it was really important for us to have a high-welfare system that would stand the test of time.
The multi-tier system mimics a hens’ natural woodland environment and encourages step-up and perching, with nest boxes, feedlines and nipple drinkers on each elevation.
Allowing birds to behave naturally significantly reduces stress, which affects health and productivity, says Jason Docherty, national sales manager at Vencomatic.
Health and welfare features
Ramps and step-up tubes on each level enable birds to get on and off the system without straining themselves and sustaining injuries such as keelbone damage.
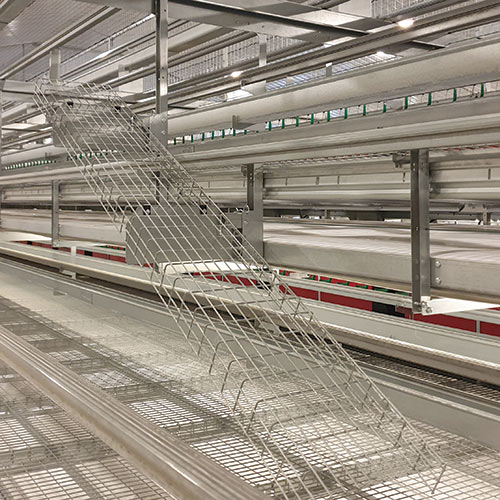
Ramps and perches inside poultry shed
The system also includes Vencomatic’s Miteperch, designed to increase bird stability and help control red mite by emitting a low current that kills mites as they emerge, without harming or disturbing the birds.
The system also has automated nest boxes, which help to manage bullying and discourage broodiness by limiting the amount of time a hen can stay in the nest and shutting off nests to achieve a summer lay pattern.
Enrichment benefits
To provide enrichment, the family installed pecking pans containing oyster shell throughout the shed.
These offer a calcium source for shell quality, and research suggests they can reduce injurious pecking.
“We will be installing enrichment tools like climbing frames in the scratching area and provide the birds with toys such as footballs,” says Miss Webber.
“The benefits of providing enrichment are huge – the birds are happy and contented, and this is reflected in their productivity and the quality of the eggs they produce.”
VentilationÂ
Proper ventilation in poultry houses is crucial, as inadequate airflow can increase the risk of disease and mortality, says Mr Docherty.
The ECO Unit ventilation system installed at Higher Down Farm is multifunctional.
It can provide sufficient ventilation and maintain a consistent house temperature without heaters.
It runs on 80% efficiency – if it is 0C outside and 20C in the house, it draws stale air out of the house, preheats fresh air and recycles it into the house at 16C.
“A cold bird will eat more; a difference of 1.5C will affect feed consumption by 1g a bird a day,” explains Mr Docherty.
“That additional consumption will soon add up on the feed bill.”
Packing and processing
In the packing area, the Prinzen PSPC 30 can automatically sort, print and pack eggs from up to 32,000 birds.
The eggs arrive via rollers from the bird house, and an Ovoprint stamps them with the producer code.
Eggs are then moved via suction to the 30-cell trays before they pass into the PS4 tray stacker to be stacked six high.
“The system is simple, but it is very efficient,” says Ben McGill, operations manager at Vencomatic.
“The equipment placement allows fast processing – 18,000 eggs an hour – while maintaining gentle handling to reduce damage in this final stage.”
The new shed will house 16,000 Leghorns, with partitions to ensure a maximum 4,000 birds per section.
The Webbers expect the first pullets to arrive before Christmas at 16 weeks old. The hens will come into lay at a slightly delayed 23 weeks, to encourage higher bodyweights.
This is because the Leghorns can be kept up to 92 weeks, boosting anticipated peak yields to 330 eggs a bird a year.
Planning and construction tips
- Consider using a planning consultant
- Seek financial advice
- Have a short- and long-term business plan
- Find mentors with relevant experience who can help you navigate your project
- Visit several farms with systems that are relevant to your project
- Planning permission – ensure a project meets planning approval criteria before investing
- Location and road networks – consider access for construction vehicles and build materials, as well as egg collection lorries
- Elevation – is the site easily flooded or at risk from high winds?
- Wind direction – affects building orientation; poor placement could compromise ventilation
- Insulation – cold birds consume more feed
- Future-proofing – consider potential future expansion or alteration to comply with changing consumer demands