How a broiler unit slashed energy costs by collecting data
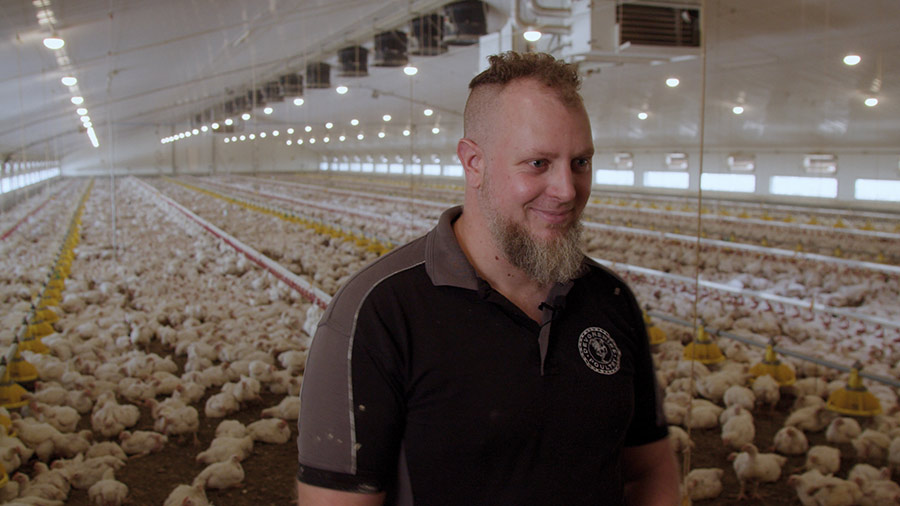
Adopting real-time data collection technology has helped one broiler producer halve energy inputs, improve bird health and performance, and reduce emissions.
Since joining Devonshire Poultry in 2021, farm manager David Dos Santos has made key changes to the 120,000-bird broiler unit at Chaffcombe Farm near Chard in Somerset.
See also: Farming careers: Working as a poultry manager
With rising energy costs and pressure to make farming more sustainable, Mr Dos Santos aimed to improve the business’s resilience by cutting inputs and increasing performance.
At the outset it was clear both the efficiency and sustainability of the unit could be improved.
The key target was to get the farm into the top performing 5% of UK broiler flocks by improving its level of efficiency, Mr Dos Santos says.
Central to that aim has been a tightening of the management process, using real-time data collection to underpin evidence-based decisions.
Devonshire Poultry owner-director Robert Lanning has invested in wireless sensors on other units in the business’s six-farm portfolio to provide and collate real-time data.
The investment has improved broiler flock performance and achieved a more cost-effective and energy-efficient management strategy.
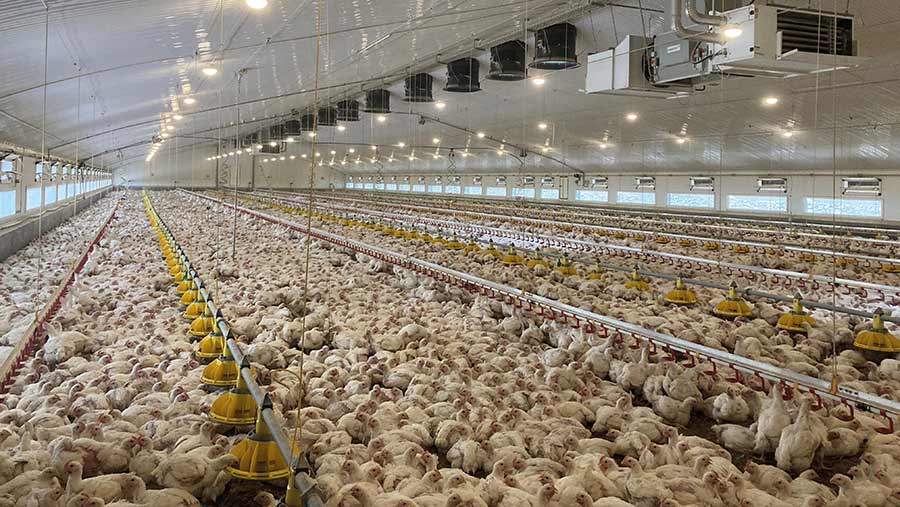
© Devonshire Poultry
How the sensor system works
As a result of the data collected at Chaffcombe Farm, Mr Dos Santos has already cut electricity and gas expenditure by monitoring and managing ventilation and temperature more closely.
Temperature, air quality and air flow are invisible to the human eye but, crucially, they affect bird activity and feed intake.
“By installing sensors and monitoring changes to the birds, we can pick up any effects much earlier than a stockperson could,” Mr Dos Santos explains.
“It means we can tackle problems as soon as they arise and before they affect flock performance.”
The company has installed 30 humidity and temperature sensors spaced evenly across each 30,000-bird shed. Along with these sensors, a further three carbon dioxide and light (lux) monitors have been fitted.
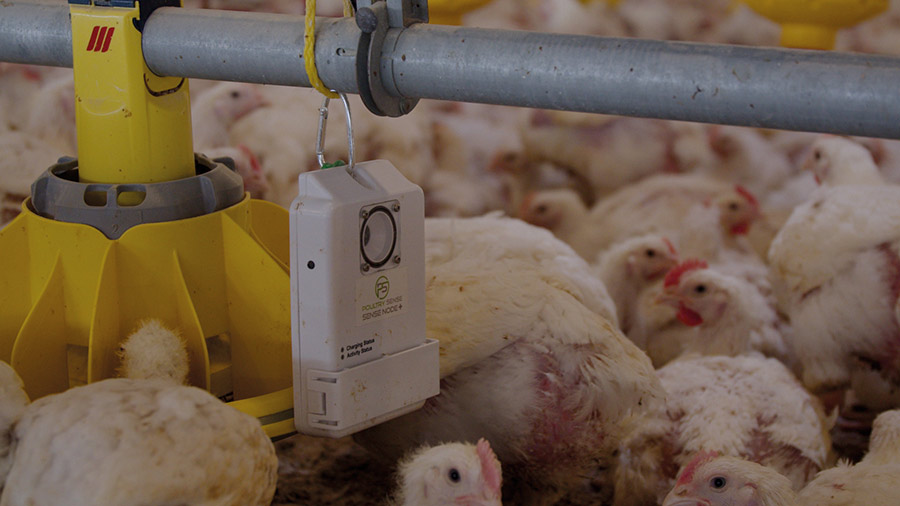
One of the sensor nodes installed at Chaffcombe Farm © Cande Group
These are backed up with weighing platforms that monitor bird activity in different areas of the shed and provide feedback on flock distribution.
This is crucial to identify any possible cold spots or draughts that would quickly reduce performance.
A number of sensor systems for flocks are available, but Devonshire Poultry chose one manufactured by Poultry Sense that allowed the shed to be monitored in sections.
“Instead of assessing the shed as a whole, we can break it up into smaller areas,” says Mr Dos Santos.
There are eight different zones in the shed, each one containing four or five sensors depending on the number of birds.
Splitting up the shed in this way has provided accurate data in the different zones that has then been used to tweak temperatures and humidity.
In the first flock after installing the system, Mr Dos Santos began to reduce the starting and running temperatures from previous levels of 33C.
Close monitoring of bird behaviour and growth rates allowed further gradual reductions to 29C. This was achieved without any performance penalty.
A similar process has been applied to humidity percentages when the chicks arrive.
Managing levels more precisely helps the birds adjust gradually to the temperature changes, because they come from incubators that are at 80-90% humidity.
“By doing this we have seen better chick growth rates at the start of a crop, with decreased health issues throughout the lifecycle,” Mr Dos Santos adds.
Tailoring ventilation and temperature to better meet bird requirements has resulted in a significant increase in bird activity.
Birds are eating and drinking more often and displaying more natural behaviour patterns such as scratching and preening, he reports.
What are the savings?
As a result of the closer monitoring, Chaffcombe has seen dramatic cuts in gas and electricity used to heat the sheds. At certain times of the year, energy inputs have dropped by as much as half compared to the previous consumption level.
Contributing to the electricity reduction, the farm no longer runs energy-hungry fans for as long because monitoring revealed the sheds were being over-ventilated.
Lighting use has also been cut back and operated more efficiently. The gas and electricity savings have not only helped cut costs, but have reduced the farm’s dependency on fossil fuels.
Mr Dos Santos says environmental sustainability is a topic which keeps rising up the agenda, with increasing pressure from the rest of the supply chain to demonstrate improvements.
To improve its carbon footprint still further, Chaffcombe Farm has also invested in solar panels on shed roofs and supplies chicken manure as a feedstock for local anaerobic digester (AD) plants.
The solar panels have been a factor in reducing bought-in electricity and gas. This has helped protect the farm from recent energy price spikes.
Supplying manure as a feedstock for AD plants means emissions that would otherwise have resulted from manure heaps have been reduced.
How bird performance has been improved
While Chaffcombe Farm has cut energy inputs and improved its carbon footprint, the business has also seen an increase in bird performance.
“Since installing the sensors, the farm has had its highest ever European Production Efficiency Factor (EPEF) result this year, and its best feed conversion rate (FCR) ever,” Mr Dos Santos explains.
By improving the EPEF and FCR the shed where the sensors have been installed has achieved its best margin to date.
Chaffcombe Farm KPI figures |
|||
Before sensors installed |
With Poultry Sense sensors |
Target |
|
EPEF |
414 |
426 |
440 |
FCR |
1.53 |
1.5 |
1.46 |
Temperature |
33C |
29C |
– |
“Many of the improvements we’ve seen have been down to using the real-time data to tweak the environmental conditions within the houses.” he says. “This has reduced bird stress and enabled them to perform better.
“While our EPEF has improved, our target is to reach the gold standard of 440. However, reaching this figure means there is no room for error,” he adds.
Mr Dos Santos believes this will be achievable with the information and knowledge gained from the sensors.
“If we want to meet and exceed targets, the use of real-time data will be invaluable for us in the future.”
Monitoring further parameters
The aim is to begin rolling out sensor systems across more of Devonshire Poultry’s units after the positive results achieved at Chaffcombe Farm.
Access to this data across sites will enable comparisons between sheds or flocks to identify variations, helping to iron out issues and drive bird performance over the wider business.
At the Chaffcombe site the success of the temperature, humidity and carbon dioxide monitoring is driving the business to look at collecting data on other factors.
One of these is efficiency of water use by installing meters. Water intakes are crucial to maximise feed intakes, which in turn drive growth rates.
Other water-monitoring factors could include the individual locations most frequently used by birds and the average quantity consumed.
The data will be analysed to see where improvements can be made to encourage birds to drink more water.
The business views identifying further areas for analysis as a necessity to stay ahead and improve margins.
Mr Dos Santos believes the adoption of technology, including sensor systems, will be widespread among the top-performing farms and ultimately will become standard practice.
Everyone in the supply chain will be asking for more data on a wide range of production factors in the future, he suggests.
“Anything we can do to increase efficiency by cutting costs and emissions, while improving bird health and welfare, will offer a return on investment, and we must stay ahead,” Mr Dos Santos adds.