Egg producer harnesses renewables to achieve low energy costs
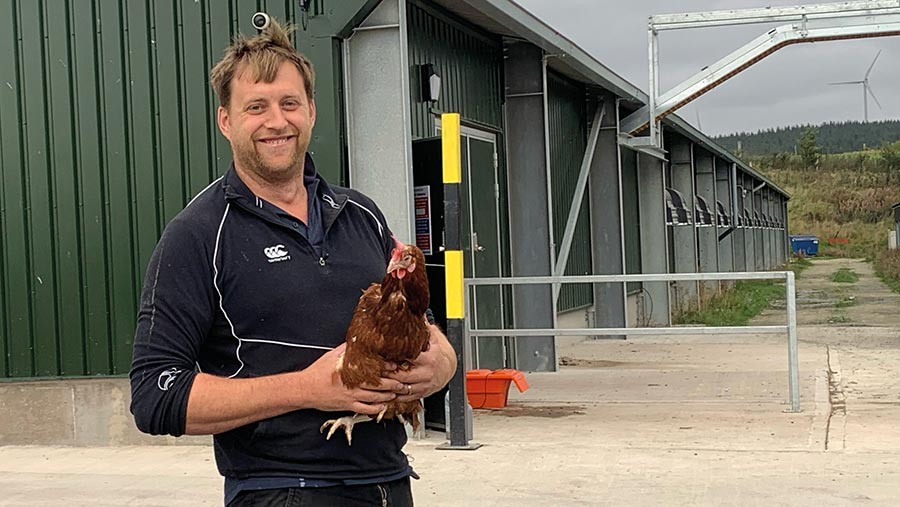
Llyr Jones doesn’t need a carbon calculator to confirm the green credentials of his free-range egg business. His monthly electricity bill does that for him.
Across the entire business – poultry, sheep and beef – that bill is never more than £400 thanks to renewable systems harnessing energy from water, sun and soil.
See also: 12 ways poultry farmers can tackle net zero
“Our electricity bills would be thousands of pounds a month without the renewables,’’ says Mr Jones, who farms at Derwydd, in Conwy, in partnership with his mother, Iola.
His two 16,000-bird poultry sheds would have accounted for a big chunk of that cost, because they need constant heat and ventilation.
Farm facts: Derwydd, Llanfihangel Glyn Myfyr, Conwy
- 647ha (1,600-acre) farm
- Eggs supplied to Tesco on cost-of-production contract
- 1,100 Mules and Nelson-type Welsh ewes
- 250 heifers
- Produces cold-pressed rapeseed oil sold under the Blodyn Aur brand
- Self-catering cottage
Mr Jones has also put in place several measures to reduce greenhouse gas emissions from the system as he drives his business towards being carbon-neutral.
“The technology is definitely there to help us; as farmers we have to be a bit brave and just do it,’’ he says.
“People think I am green, but I am just tight – being green helps make the bank balance black.’’
Below, Mr Jones talks through those measures and the benefits they bring to the cost of producing 10.5 million eggs annually.
Hydro, solar and ground-source energy
A 30kW hydro energy system was installed on a stream on the farm in 2012.
We have a huge amount of rainfall and big hills, which are the perfect ingredients for producing hydroelectricity.
24kW of photovoltaic panels provide a backup source of renewable energy when dry weather reduces the flow of water to the hydro system.
An 80kW ground- and air-source heat pump – which cost about £55,000 including the pipework, fitting out and all the internal works – pumps warm air into the two poultry sheds, heating them to 18C.
This is good for both bird welfare and productivity, because they use less energy to keep warm and, as a result, they can put more energy into laying eggs.
It also means the hens eat 3g a head a day less feed, and that is saving us 35t of feed and £14,000/year.
Those two fewer lorry deliveries a year further reduces the carbon footprint of our eggs.
We would like to replace the soya in that feed with our home-grown rapeseed, but it is a different type of protein so we are still at the research stage with that.
We don’t want to rush it, as you have to be careful with changing diets and we don’t produce enough at this stage anyway to satisfy the feed requirements of 32,000 hens.
Litter management
In 2021, when we built our second shed, we fitted it with a muck dryer. It works by capturing heat from the hens as it rises and forcing that air back down on to the muck belt.
It removes about 25% of the moisture from the muck, and drier muck means considerably less ammonia, too.
When we muck out the sheds it means one load less – two instead of three – reducing tractor and diesel usage.
Bird breed
In February next year we are switching from a Lohmann Brown to a white layer, also a Lohmann, because they have a longer productive life and therefore produce more eggs.
We currently depopulate at 72 weeks but with the whites it will be 100 weeks – the eggs produced per bird in each cycle will increase from 330 to 500.
It means that for every four crops of birds we would have had with the Lohmann Brown, we will have three – and that has all sorts of benefits, including reducing the number of times we need to clean out the sheds from four to three.
One major downside is that the white hens produce white eggs; the customer can be quite fickle about that.
Borehole water supply
We don’t use any mains water in the poultry business, it all comes from a borehole on the farm. But we do have mains water as a backup, just in case a pump breaks down.
Scrubbers to reduce ammonia emissions
Air from the hen shed is pushed into the air scrubber where it is sprayed with sulphuric acid.
The acid attaches itself to ammonia, and water is then added to reduce the pH level to neutral. With this system we can produce fertiliser with a nitrogen value of 20%.
The saving in the cost of buying in fertiliser easily pays for the cost of running the scrubber, but the disadvantage is the capital cost – it needs to be made of stainless steel so it costs around £90,000.
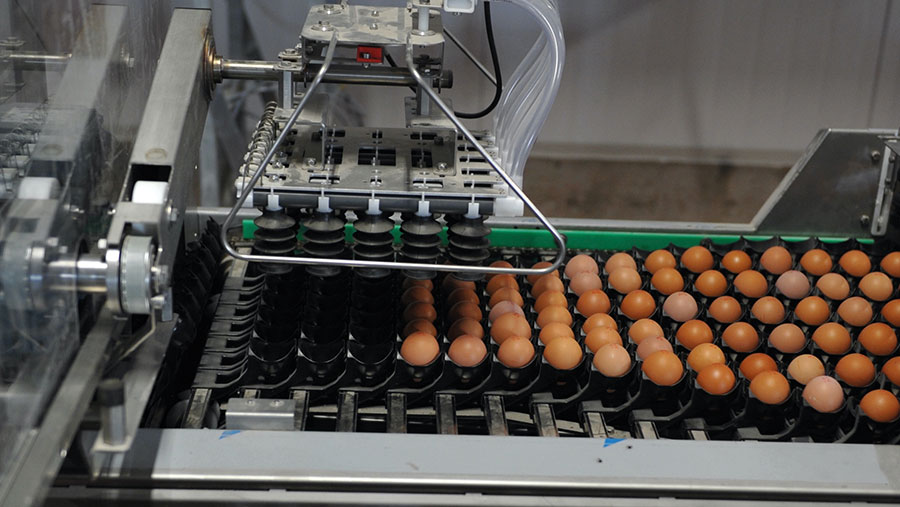
© Debbie James
Planting trees
We have planted hundreds of trees on our 40-acre range because the hens love foraging among them; they are jungle creatures, after all.
At 9am each day, the doors of the sheds open and the hens go out and spend the day in the woods.
We have also planted thousands of trees on the farm. There is always an unproductive corner or somewhere where you can plant a tree to make it productive.
Electric vehicles
The solar panels on the hen sheds power our electric ATV.
It will run for about 30 miles on a single charge, depending on how fast we drive it or whether we are towing a trailer.
We’ve also bought a car that only uses the excess energy. For instance, it won’t draw from the system first thing in the morning when we need that energy for the poultry shed.
Otherwise we would have to buy in electricity to replace what it had taken out.
Even though the car is more expensive than any I have ever bought, I am saving £200/month – my finance repayments on my previous vehicle were £500/month but we were spending £400/month on diesel.
The new car costs us £700 a month.
I had looked at batteries to store excess energy and couldn’t make the figures stack up, but the car is literally a storage battery on wheels.
Agri-environment schemes
We have a Glastir contract to manage 404ha (1,000 acres) of heather moorland where we have black grouse breeding.
The heather is regularly cut to keep it lighter in strips to help the grouse to express themselves. There is also taller heather, places where they can hide from predators.
We also have 12ha (30 acres) of peatland, which needs to be kept moist – we have done this by blocking drains to stop the water seeping away.
We make sure there are no trees growing on it, as they will suck the moisture out of the ground.
It’s important that we look after these peatlands because they store thousands of tonnes of carbon – they’re great carbon sinks.