How heat exchangers can benefit both environment and poultry
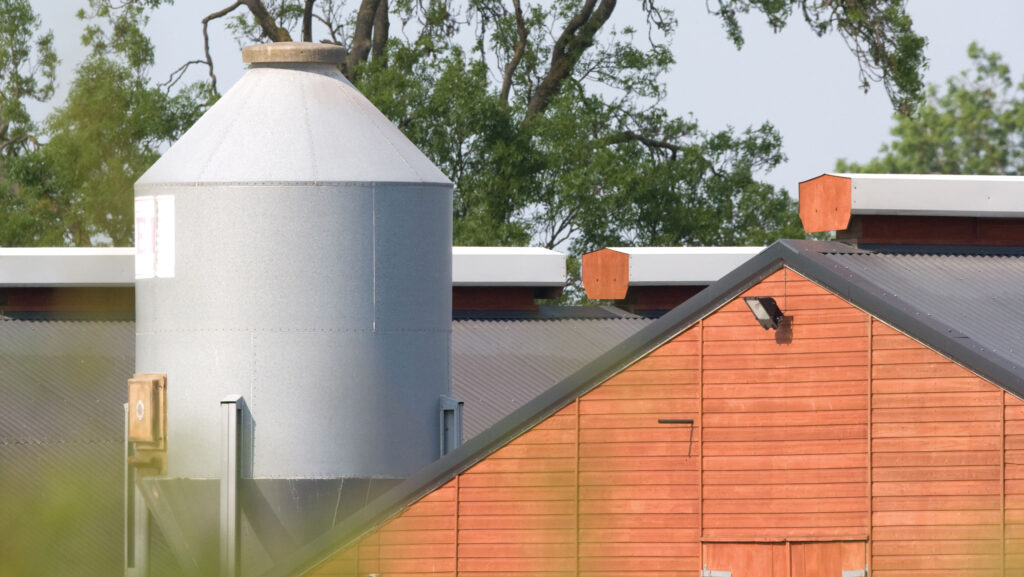
It makes a lot of sense to reuse heat that is present in poultry housing. Warming up the incoming fresh air to provide the necessary ventilation keeps the internal atmosphere clean and the litter dry.
Heat recovery units work by exchanging heat between stale air that is extracted from a shed and fresh air drawn into the indoor environment.
Circulation fans then distribute that fresh air through the house, reducing heating costs and improving the climate for birds.
See also: New poultry units – planning and environmental permissions advice
Poultry generate a lot of heat to recycle and some systems suitable for broiler and laying hen sheds claim to cut heating costs by up to 60%.
Heating the incoming ambient air in winter prevents exposing birds to cold, damp and draughts. It also avoids fluctuations in the indoor climate, thereby protecting health and performance.
Heat exchangers specifically tested in poultry sheds can also be a viable alternative to an ammonia scrubber.
This has become more the case as the industry has introduced measures to improve the indoor environment; lower stocking densities, carefully balanced diets, and good husbandry and management techniques mean these is less ammonia in sheds.
Ammonia reduction factor
Natural Resources Wales, which is responsible for regulating intensive poultry systems in the country, says that when applied to broilers, heat exchangers have an ammonia reduction factor of 35%, and 15% to 20% in layer housing.
Furthermore, unlike scrubbers, which are a direct cost and can add £100,000 or more to the infrastructure of a new shed, exchangers reduce energy costs, so they have tangible benefits.
Some producers have even secured planning consent by incorporating heat exchangers into their planning application.
In the past 18 months, use of heat exchangers appears to have been growing as environmental regulators increasingly see their benefit in lowering emissions, says planning consultant Graham Clark, of Berrys.
“When I joined Berrys at the end of 2014 and started working on poultry applications, heat exchangers were considered more of an ‘older style’ part of the heat and ventilation systems.
“I can’t recall them being used widely at all on new-build units, it was just the standard roof ventilation fans, but that now seems to be changing,” he says.
Air quality, odour and dust consultant Matt Stoaling, of Isopleth, says while ammonia scrubbers will perform better than a heat exchanger in reducing ammonia emissions, as an “end of pipe” solution they do not improve the environment in the shed.
Litter quality dictates the shed environment, and whatever ammonia levels are in the shed, the scrubber will filter these from the air as it is transferred outside.
“That’s good for the environment, but what the farmer also wants is for the atmosphere inside the house to be good because it means a happier chicken – and a better quality chicken for the consumer,’’ he says.
Controlling the temperature
By controlling the temperature in the house and reducing moisture, heat exchangers improve the quality of air inside.
This negates the need for a scrubber in some instances because the ammonia levels are not as high as they would be without an exchanger.
Matt says that the now commonplace use of other measures has, in many cases, designed out the need for scrubbers.
These include formulating balanced protein diets to reduce the amount of ammonia excreted and a lower stocking density from 38kg/sq m to the Freedom Foods stipulation of 30kg/sq m.
“Some of the testing data in bigger modern sheds show that the levels of ammonia that were present 20 years ago no longer exist,’’ he adds.
Although planners in countries such as Germany still insist on scrubbers, in the UK there is an increasing acknowledgement that heat exchangers are a viable alternative.
“They save energy for the business, improve the air quality for birds and have environmental benefits, so provide a ‘win win’ for everyone,” says Matt.
By improving the climate for poultry, through reducing moisture in the shed environment, heat exchangers ultimately help cut respiratory issues and improve foot score.
As well as the benefits of reducing ammonia and improving air quality health, it follows that flock performance can increase and the feed conversion ratio fall.
There are various types of heat exchangers that can circulate different levels of air, up to 30,000 cu m/hour, and there are numerous ways to distribute it.
In some, preheated air can be introduced into the shed through a louvre unit, or through aeration tubes.
These approaches pull preheated air to the centre of the shed and, in conjunction with downward fans, direct heat to bird level.
In the past, high humidity and dust levels in poultry sheds presented challenges for heat exchangers, but as management and cleaning techniques have improved, these have been reduced.
However, the units still need regular cleaning to remove the dirt and dust that accumulate over time, although some models come with an automatic cleaning option (see “Heat exchange models for poultry”).
Heat exchange models for poultry
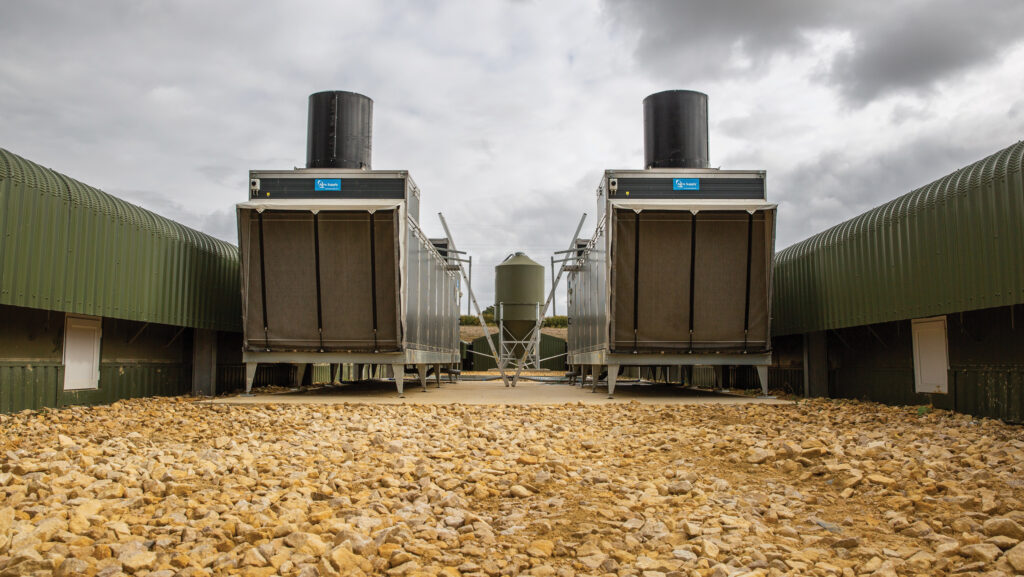
© Manio Photography
Vencomatic ECO Unit
Processing up to 30,000 cu m/hour of air, this unit promises a 35% reduction in ammonia emissions and a thermal efficiency of up to 80%.
It has an automatic cleaning system, and any dust that remains is discharged by the built-in washing installation.
Condensation that forms in the unit is stored and reused for washing to keep water consumption to a minimum.
Each unit is manufactured to a farm’s specific requirements and is priced accordingly.
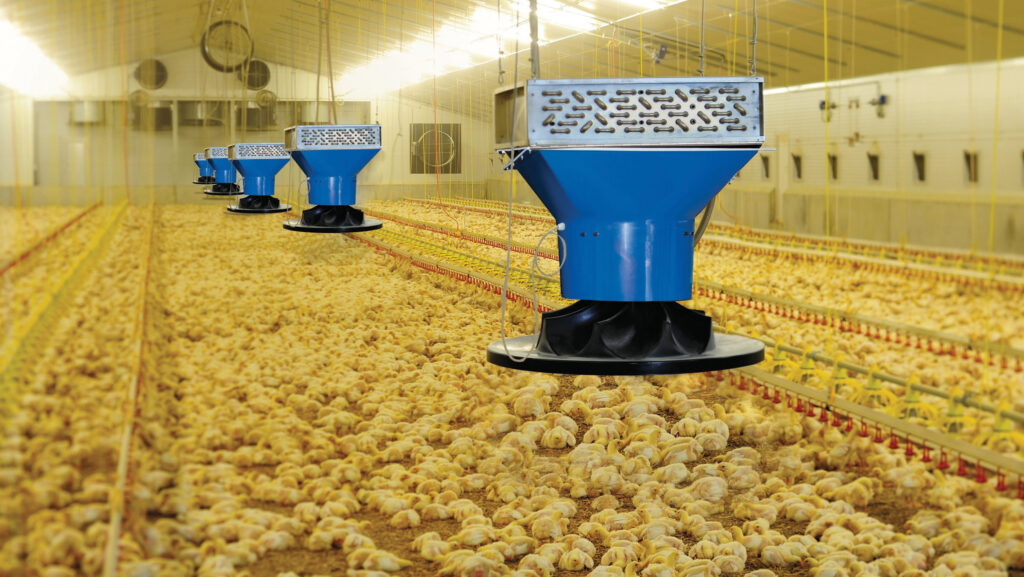
© Munters
Munters Heat-X type H/V
As one of the more commonly used heat exchangers in UK poultry systems, the Munters Heat-X air-to-water model has been shown to halve energy costs.
It can be adapted to be compatible with horizontal and vertical air guidance systems. Users report it is easy to clean, while use of stainless steel for the pipe system enhances durability.
ITB Climate AIR2-DSK
This heat exchanger has an additional feature of a sprinkler system for the summer cooling function. This allows temperatures in the poultry shed to be lowered by 4°C to 10°C.
The manufacturer suggests that it will reduce energy use by 50%.
In combination with recirculation fans, the Air2-DSK is manufactured to reduce ammonia by 70%, and particulate matter and carbon dioxide by up to 50%.
Recov-Aire
This model has a smaller intake fan to help with heat recovery. The number of units required depends on the size of the shed, but is usually no more than two.
When the core is clean, it claims to achieve 50% efficiency and be very simple to operate.
ESA-1000
Unlike some models with two motors (requiring double the electricity to operate), the ESA-1000 has a patented ventilation system with a single motor.
This pushes air in both directions and requires only single-phase power and 2.6 amps a unit.
It pre-warms incoming winter air by between 15°C and 20°C. Cleaning in between flocks is a swift job – the manufacturer says it can be done in 10 minutes.