Advice for poultry farmers considering a shed refurbishment
It is possible to get top performances from older poultry sheds – but certainly more difficult – and the reality is many broiler farms in the UK are past their best.
A modern structure is easier to keep free of disease, and contemporary systems allow for more precise management of bird environments.
See also: Advice on cleaning free-range poultry sheds
However, building from scratch can cost about 64% more than the average refurbishment, making the latter a good option.
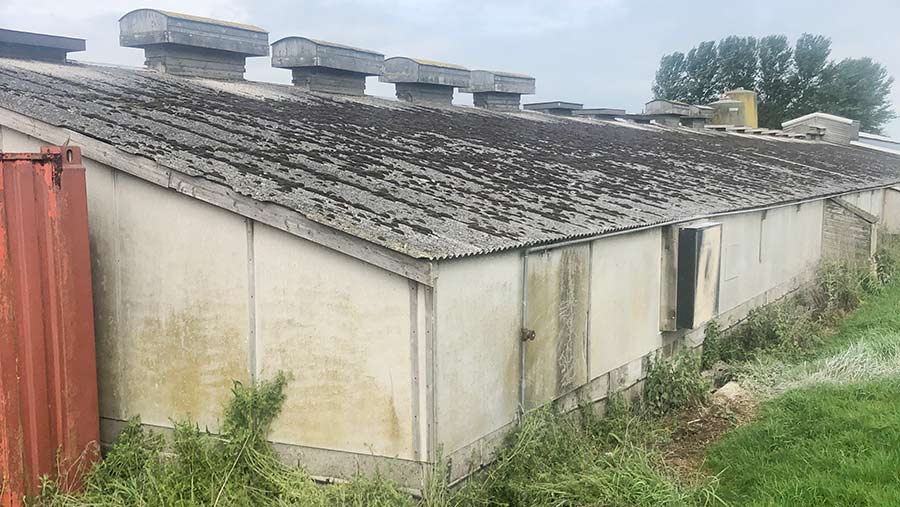
Poultry shed before refurbishment
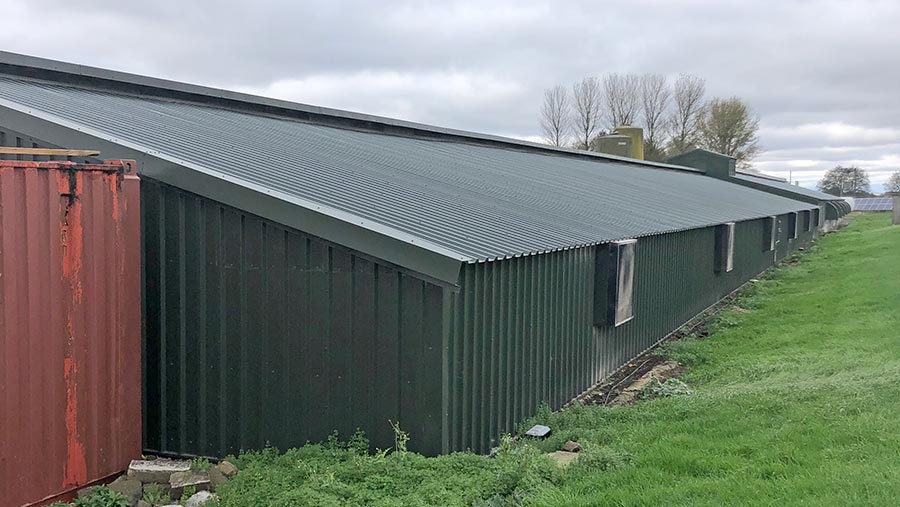
Poultry shed after refurbishment
Sam Drummond, poultry farmer and director of building specialist Coverhill, has been refurbishing sheds within the family farming business for many years, and for the past four he has offered this service to other farmers.
Costings
- The costs of refurbishing a shed vary, but the average is £8/sq ft, depending on its condition. That compares with at least £22/sq ft for a complete new build.
- There are also significant tax advantages to refurbishing poultry sheds. As a repair, rather than a new build, 100% tax relief is available – and 150% tax relief can be claimed against the cost of removing asbestos.
Shed floor
He says the first thing to assess is whether the shed can be refurbished. It will need to be structurally sound and have a concrete floor that is in a good state.
It is possible to repour concrete, but often a damaged floor will mean the shed needs a total rebuild.
Other reasons for rebuilding will be where the eaves are too low to accommodate modern machinery, or if the total floor space of a shed makes it uneconomical to continue rearing birds.
If the shed is structurally sound, however, it can be refurbished: “We will usually pour new concrete walls to strengthen it,” explains Mr Drummond.
Putting in windows
Windows will often be installed as well, to meet with new Red Tractor rules. Roofing in older sheds can contain asbestos, which needs a qualified team to remove it.
Red Tractor compliance pointers
- From 1 October 2020, all broiler farms in the Red Tractor standard must have windows installed in dwarf walls equivalent to 3% of the floor space.
- Farms with 1% installed – common in the North where the climate is colder – will have to retrofit windows to the larger area by 1 October 2023.
Mr Drummond says Coverhill regularly recommends increasing the amount of insulation, too, taking it up to 150mm from the more common 100mm.
Once the structure is secured, fixtures and fittings should be replaced with modern equivalents.
Gas and water piping should be switched from metal to plastic, for example, and it is worth removing individual header tanks and investing in a central pressurised water system, says Mr Drummond.
Planning pointers
- As a repair, there is no automatic need to apply for planning, but it is worth seeking advice from a specialist or the local council if unsure.
- Local authorities have differing views on such work, and there have been times that replacing a wooden cladding with more modern tin has met with objection.
LED lighting is also a good investment when refurbishing, as are feeder pans to replace track systems.
It is possible to install new biosecurity measures, though simply concreting outdoor areas and making cleaning easier contributes to improved disease control.
The finishing touch is a layer of insulation over the dwarf wall and green tin cladding to cover everything up. “The aim is to make it look like a new shed,” says Mr Drummond.
Case study: The Chilterns Farm, High Wycombe
Retrofitting modern ventilation systems in older sheds is not always straightforward, as one refurbishment for Aviagen Turkeys demonstrated.
The turkey genetics giant wanted to bring three 450sq m sheds at one of its grandparent rearing farms back into operation, after they had been empty since the 1990s. Not using the units meant the company was missing out on rearing space for 4,000 birds.
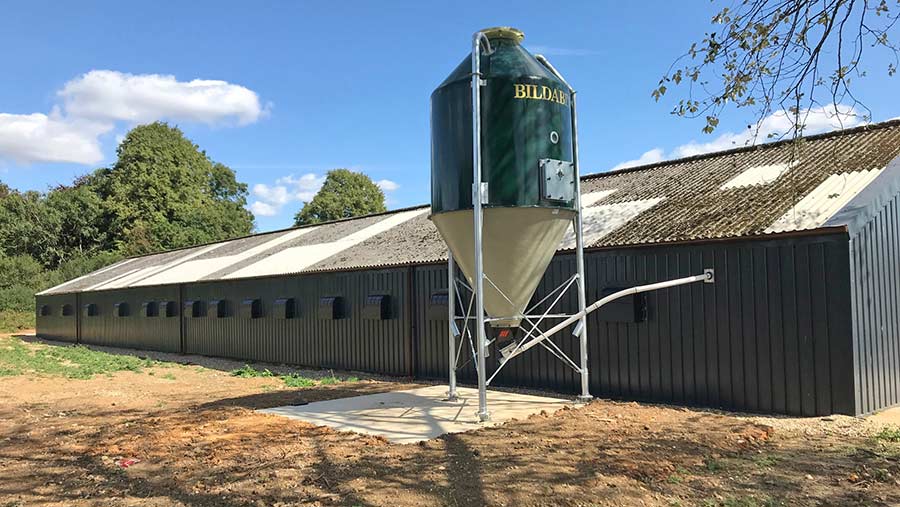
Chilterns Farm poultry shed
The site is based near High Wycombe, and planning restraints made the option of knocking down the buildings and starting again unfeasible, so a refurbishment was commissioned.
Knights Construction completed the groundwork while Powells handled the refurbishment of the building. The roof insulation was bolstered by foam spray supplied by Websters but, crucially, the structure would not support ventilation in the ceiling – the most conventional setup for modern poultry units.
Instead, ventilation specialist Hydor was commissioned to explore alternatives, and the firm’s John Lack devised a longitudinal system that drew air into the gable end.
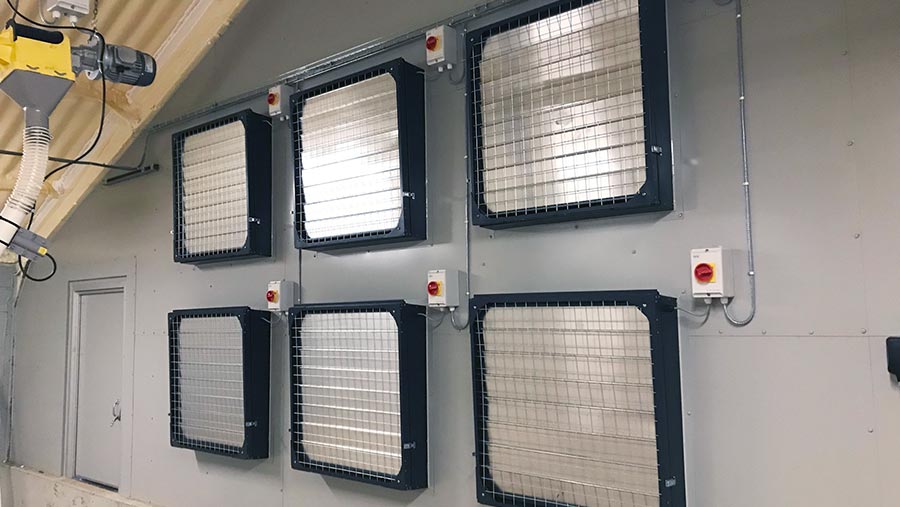
Chilterns Farm poultry shed vents
It needed to have the capacity to effectively ventilate a shed full of valuable adult grandparent stock, he explains.
Defra warns that a rise in body temperature of just 4C can result in mortality, and birds can take as long as five days to acclimatise to warmer temperatures.
In total, each shed was fitted with six four-stage ventilation fans in the gable end. Along the dwarf wall, 30 inlets were installed to allow fresh air to enter and gearbox winch units and stainless-steel rodding systems were installed to allow for their control.