Advice on developing a well-trained poultry team

A team can make or break any business, and a poor poultry team can affect production as well as efficiency.
NFU Poultry Board member Will Lea helps deliver staff training and compliance under the Lion Code for Country Fresh Pullets alongside running a 32,000-bird free-range layer enterprise near Much Wenlock in Shropshire.
He says he could see there were training gaps in his specialist areas of rearing and layer production, but quickly identified that this was a problem affecting the whole of the poultry sector.
See also: Farming careers: Working as a poultry manager
Will has been working with Country Fresh Pullets for seven years as a production manager, and the company was approved under the Lion Code Training Scheme to offer training to its producers in 2020.
“[We found] poultry was a subject that wasn’t really taught in depth [at university], so through the training, that’s what we’re trying to fix,” he says.
“Most layer farms are registered with the Lion Code scheme, which introduced training under the Lion Code Passport Scheme.
“We run and implement that training across our own producer base, and to anyone else that needs it. We have a large number of birds in our contract producer group, so that’s a lot of people.”
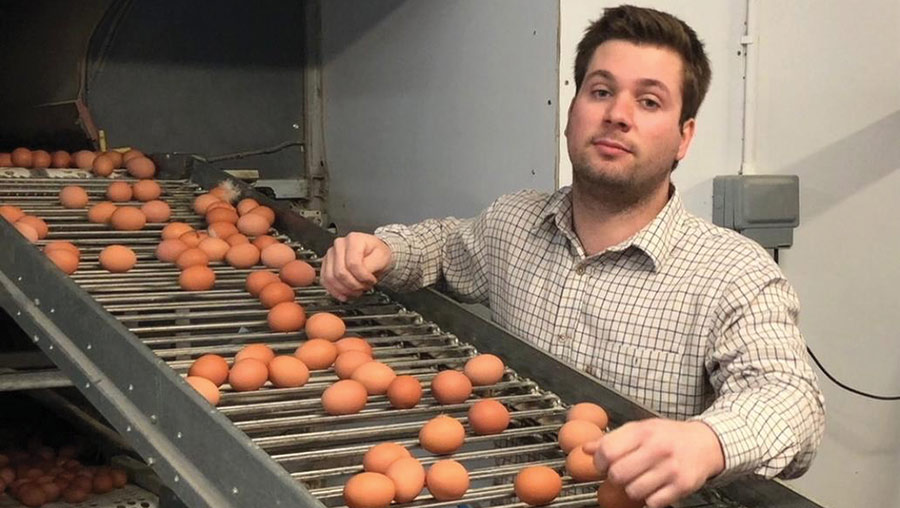
© Will Lea
Knowledge transfer
Will says there also seemed to be a gap in the quantity and quality of knowledge being passed down through the staffing chain.
“There are always farm managers, and ultimately, it’s whether the staff below them know everything they need to know.
“We found quite often that wasn’t the case, and they didn’t know why they were doing certain things.”
This was an issue that the Lion Code wanted to address. However, uptake on training had been a challenge in the past.
“Training is now in the code standards, so that has really helped getting people into it,” he explains.
“Everything we do, apart from First Aid, is done online as an e-learning course. It works better for farmers because they can do it at any time that suits them; they can go in for a coffee break and complete parts of it, or log in on an evening.
“It’s as good as doing it in person: it’s still very thorough – it just suits farmers a lot better.”
Training passport
A poultry passport training scheme was introduced for the broiler sector in 2009.
This was followed by the Lion Training Passport scheme (established by the British Egg Industry Council, Poultec Training and Lantra in 2020) to create a consistent level of training for the industry and assist with assurance scheme compliance.
Poultry workers can hold different levels of poultry passports, depending on their job role:
- Level 3 Manager, chargehand, assistant manager
- Level 2 Senior egg collector, stockperson, multi-skilled hatchery operative
- Level 1 Egg collector/grader, single-skilled hatchery operative.
The delivery of the training is carried out by approved providers and tutors.
Training courses
Staff employed on Lion-registered egg farms and hatcheries can register for a Lion Training Passport.
There are minimum training requirements depending on the individual role.
1. Health and welfare – Levels 1, 2 and 3
A poultry health and welfare course includes:
- Legislative requirements – codes of practice, alongside Lion Code Passport and industry standards
- Equipment requirements – for bird welfare and enrichment
- Litter conditions, accommodation, environmental conditions and shelter
- Feed and water quality
- Emergency procedures – fire, flood and disease
- Record keeping
- Approved culling techniques and disposal of fallen stock
- The Five Freedoms
- Bird handling
- Identification of normal and abnormal behaviour.
Vaccines, however, can often be a stumbling block when it comes to health and welfare.
“Vaccine training is important, and it’s a good reminder for everyone – it’s easy to be in your own bubble and miss things,” says Will.
“For example, if you’re not putting the vaccine through with enough time to drain and prime the waterlines, the vaccines aren’t actually reaching the birds.
“Particularly if the water hasn’t been tested, and the dosing system has chlorinated water, then the vaccine is killed.
“It’s all the little things perhaps people weren’t doing, or didn’t realise they had to do, or weren’t understanding why they were doing them.”
2. Biosecurity – Levels 1, 2 and 3
Biosecurity is hugely important because of bird flu, says Will. “Everyone has focused on that in the past year, which is good. For me, biosecurity was the biggest knowledge gap.
“When delivering training, or as a rep, you see lots of examples of good and bad biosecurity. But producers can’t go and see other poultry farms, so they aren’t seeing that.”
The biosecurity course includes:
- Definition of biosecurity
- Reasons for biosecurity
- Procedures, equipment and disease control
- Legislation, code of practice, Lion Code and industry standards
- Personal hygiene, personal protective equipment
- Record keeping, monitoring and auditing
- Measures for salmonella and campylobacter control as well as identification of poultry diseases and control measures
- Disposal of spent products and solutions.
3. Food safety
Food safety is important because, ultimately, poultry producers are working with food products.
“We have created a food safety training course specifically for the egg industry, touching on the importance of temperatures, coolers, egg rooms and rodents. It has been really successful,” Will says.
The course includes:
- Definition of food safety
- Personal hygiene/personal protective equipment and staff procedures
- Cleaning methods and chemical usage
- Temperature control
- Traceability requirements and record keeping
- Pest control management and identification.
Implementing a training plan
When it comes to conducting training, it is always more interesting to tailor it to the individual farm, says Will. “I know that’s what people are looking for. Just engaging them can make it less onerous.
“Lots of information can be generic, so making it more specific can keep people engaged.”
Communication is key. “I think there has been a lack of communication in the past,” he says. “I think now people realise it’s important to discuss training with the team and get everyone involved.
“It’s not just bringing someone in to do the lower paid, less skilled jobs – you need everyone involved.”
Following this process can help identify where skills gaps lie and improve morale across the whole farm, he adds.
And it is something he has successfully implemented on his own farm.
“A girl I went to university with is managing the farm day to day, and she reports back to me.
“It works very well, and it allows me to be out on farm advising people, because I have a brilliant manager – but it wouldn’t work without good communication.”