A guide to improving poultry shed insulation
Good insulation will keep poultry housing at an even temperature throughout the seasons, reducing heating and ventilation costs. However, older types of insulation may be less efficient due to outdated design and standards or through deterioration.
We asked Jason Powell, director at Powell Buildings, for advice on the types of insulation available and how to assess whether your shed needs an upgrade.
See also: A step-by-step guide to cleaning your poultry shed
Why is improving insulation important?
Insulation in poultry sheds is essential in both summer and winter to maintain a comfortable temperature.
A well-insulated shed will encourage even flock spread and ensure there are no draughts, which can cause the birds to gather in warmer spots.
There are financial savings to be had, too, and not just in reduced heating bills. Cold birds eat more – leading to higher feed costs and potential overfeeding.
What are the existing standards?
There are no standards for insulation within the poultry sector, but with farmers increasingly wanting to save energy, deeper insulation is becoming more common.
Producers are also considering the environmental impact; reducing the energy used for heating can help to lower carbon emissions.
What are the signs of inefficiency?
The main signs can be seen on a cold morning. If you notice a frosty roof that is thawing out in patches, that normally means certain parts of it are letting heat through the insulation to the outer surface.
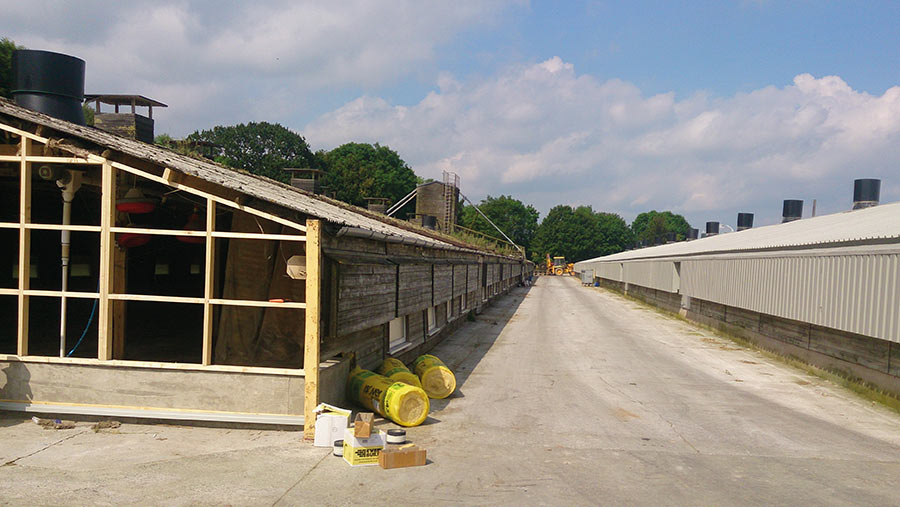
Removing old insulation usually means stripping back and recladding the shed © Powell Buildings
What types of insulation are available?
The most common type of insulation in poultry housing is a fibreglass quilt roll. This is mainly used within the roof, due to the vast area to be covered and the thickness normally required. It can also be applied to the sides and gables, but insulation blocks could be another option here.
An insulated panel can be used on the roof, but because of the area’s size, it is unlikely to be cost-effective.
Free-range sheds do not need as much wall insulation because the birds have access to the outside and roam in and out.
But a broiler shed has to be capable of maintaining temperatures of 32C so polystyrene or Styrofoam board are often used on walls.
The floors are not normally insulated but often sheds have ground-source heat pumps, which operate in a similar way to domestic underfloor heating.
How does insulation work?
All insulation has a U value that indicates its thermal transmittance – how it conducts heat energy from the inside to the outside of a building.
Thermal transmittance is determined by the layers either side of the insulation and the air gaps.
Insulation blocks heat movement, rather than transmits it, so the lower the U value, the better the insulation.Â
What efficiency levels are achievable?
This is determined by the material layers used either side of the insulation and the thickness of insulation used.
Depending on the width and size of the shed, a void in a side panel of 150mm can be filled with 100mm or 150mm of insulation.
But trying to squash 200mm in there will stop the insulation from working effectively – it needs air to run through it.
What is involved in replacing insulation?
In most poultry units, the area where insulation often needs replacing is the roof. What’s involved is determined by the type of unit – timber-posted or clear-span steel – as well as the materials on the internal ceiling lining and external roof cladding.
Removing insulation can be complicated as the process requires a complete roof area to be cleared, then replaced with new cladding.
Be aware that if the existing roof has any asbestos content, costs can mount up as everything must be removed correctly according to health and safety guidelines.
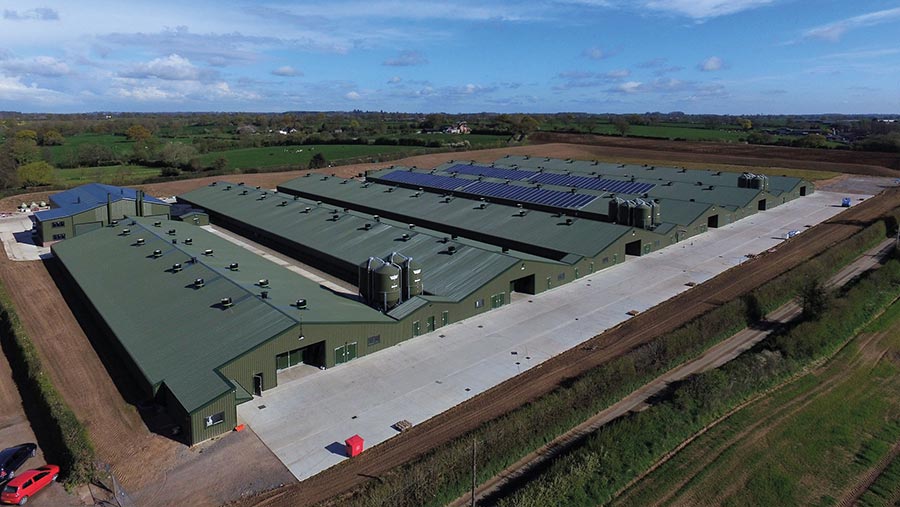
Replacement insulation is commonly most needed in the roof area © Powell Buildings
What are the costs?
The lower its U value, the more effective – and therefore expensive – the insulation.
On a standard poultry unit, 116m long x 24.4m wide, a 200mm thickness of fibreglass roll in the roof and 150mm in the sides, walls and gables would cost approximately ÂŁ9,000 plus installation.
Panels are more expensive than fibreglass, but are quicker and easier to install and there are no gaps to let the cold in.
What are the cost savings and return on investment?
In older sheds, where the insulation’s properties have more or less failed completely, farm businesses are burning fuel all the time just to maintain the internal temperature.
So while having a new insulated roof supplied and fitted for ÂŁ40,000 is a high cost initially, over two to three years the investment will be returned by fuel savings.
Using less fuel also helps to reduce the carbon footprint of the farm, making it a more environmentally friendly business.
All-in-one panelling
Another insulation option is an all-in-one panelling, which offers the usual benefits of insulation while being easier to clean and install. Typically, panels are also thin, light and meet fire safety specifications.
“As building controls tighten and insurers focus on fire safety, it makes sense for farmers to build to the highest possible standards,” says Tom Verhaest, agricultural specialist at Recticel Insulation.
Unlike other insulation types, these panels have facings that are resistant to ammonia, which can erode and destabilise standard insulation boards.
Most insulation boards have a white reflective facing, which – while beneficial in many sheds – causes an unnatural glare in buildings lit by daylight. This can stress birds because their vision is sensitive to a different light spectrum to humans.
A dark-coloured panel – which can create an ideal environment for the flock, reducing stress by absorbing light and preventing glare – is also available as an option.