7 tips for making a profit from farm-scale Christmas turkeys
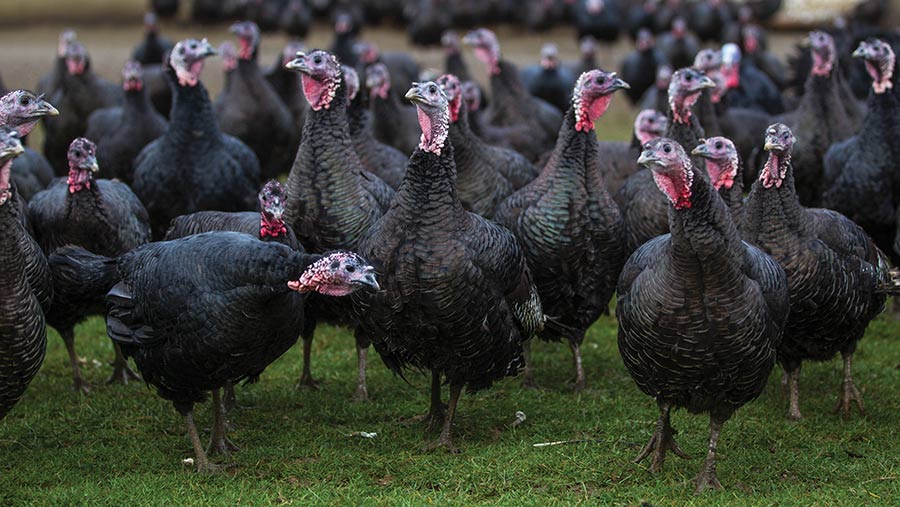
About 18% of the Christmas turkeys sold to UK consumers are produced on a small scale by farmers independent of the big players.
It can generate a good income, often making use of existing resources by growing birds in housing used for different purposes at other times of year.
In addition, the labour requirement is low and turnaround quick – turkeys can be grown in as little as 12 weeks and for up to 24 weeks, depending on requirements at point of sale.
See also: So you want to… sell produce at a farmers market?
However, avian flu and higher feed prices have introduced new challenges, so if the figures are to stack up, producers cannot afford mistakes at any stage in the process.
Rebecca Tierney, poultry adviser at Irish advisory, education and research body Teagasc, says turkeys are highly responsive to the effects of management.
“Birds with the same apparent housing, nutrition and facilities are capable of giving vastly different results, depending on the care taken with management,’’ she says.
Rebecca gives her top tips on factors that will maximise health and minimise losses.
1. Source healthy poults
Buy from a reliable source with a good track record for supplying healthy birds.
Poults should arrive on farm with a good covering of clean feathers, be free of discharge around their eyes and nose, and have no soiling around the back passage.
Check foot pads are healthy – they should not be hard and scaly.
Salmonella can be an issue in young birds, but pre-movement faecal sampling can test for it.
Ideally, take delivery of poults at six weeks old, because at that age they are sufficiently well-feathered to be able to thrive without the aid of artificial heat if the building has no draughts.
2. Housing must be fit for purpose
More often than not, turkeys are housed in a shed that would otherwise lie idle at that time of the year. A controlled environment is not essential for Christmas turkeys but is a must for year-round production.
Turkeys grow and perform well in house temperatures of 15-17C, although they require a slightly higher temperature, 17-19C, until about nine weeks of age.
Use a shed that can be fully cleaned and disinfected, make sure it has sufficient ventilation, is warm enough, free of draughts, and wild bird and vermin proof.
It should also be free of cracks and crevices where dirt can build up and have no gaps in the roof, because disease from wild bird droppings can be carried in with rainwater.
Use a broad-spectrum disinfectant with proven efficacy for salmonella control, once surfaces have been cleaned and dried. Excess water will dilute the disinfectant and reduce its efficacy.
Use good litter or bedding, such as chopped straw or white wood shavings.
Poults are prone to respiratory illnesses so will need good ventilation, but cover inlets with mesh to prevent birds and vermin getting in.
Cover access points, such as under doors, with a suitable material.
3. Keep free-ranging land fallow before use
If land is being used for other purposes before turkey production, it must not be grazed or stocked by another type of animal or poultry for a minimum of four weeks before it is accessed by turkeys, for disease control.
4. Protect from predators
Predator exclusion fences are essential in a free-range system, but will only work if they are well-designed and well-maintained, as foxes can breach even the best barriers.
Barrier type and electrified anti-predator fences can be used separately or in combination.
For a gold star system, use nine strands of high-tensile wire up to a height of 1.25m, with wires alternating between earth and live and spaced at intervals ranging from 5cm to 25cm.
5. Use only water from potable sources
Do not use a rainwater harvesting system water for drinking water because of the risk of contamination by wild birds via diseased droppings on roofs.
Use mains or borehole water, with some form of treatment if it is from a borehole, and ideally test it to ensure it is fit for consumption.
Where turkeys have access to a range, all drinking water and feed should be inside the building.
6. Use good feed management protocols to keep disease at bay
Most feed is supplied in non-resealable bags, so decant into an airtight feed bin to exclude vermin.
Clean up spillages promptly and bin them.
Never feed a broiler ration as this contains coccidiostats that will cause major health problems in turkeys.
When birds are younger, feed a high-protein ration to develop the skeletal frame to hold weight; thereafter, prioritise energy for growth.
7. Establish a market before getting started
Establish some form of market before going into production: this might be family, friends or local butchers; farmers’ markets can be a good place to pick up business.
After the first year, a good product will be the best reference for business in future years.
Case study: Bryn Farm, Cowbridge
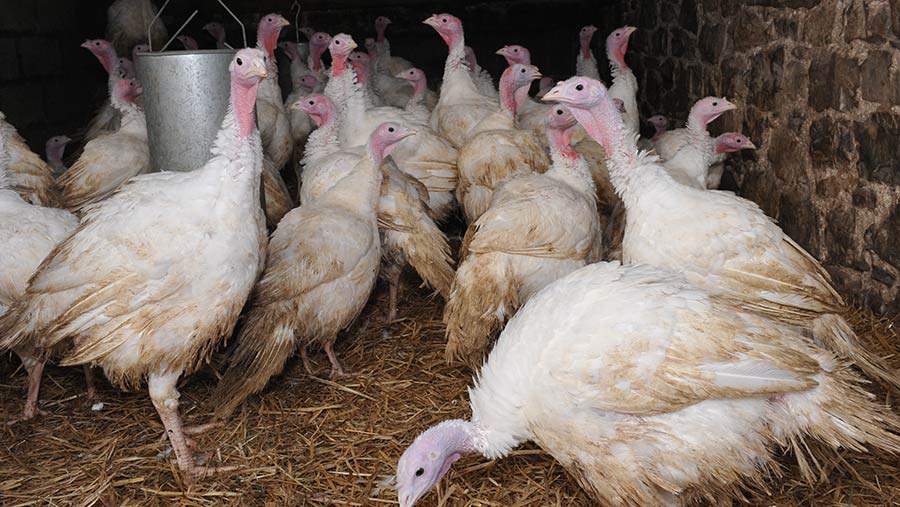
© Debbie James
Barn-reared turkeys for the Christmas market have been produced for 70 years at Bryn Farm near Cowbridge in South Wales.
Despite higher feed and labour costs, it remains a profitable enterprise for DH Rees and Sons, which predominately farms beef, sheep and arable.
Minimising bird losses, producing efficiently and maximising sales are all key to achieving a profit margin.
The business takes delivery of 200 six-week-old white poults in September, sourced from a producer at Craven Arms.
Buying from a known breeder with a good reputation for supplying healthy birds is important, says third generation farmer Tom Rees.
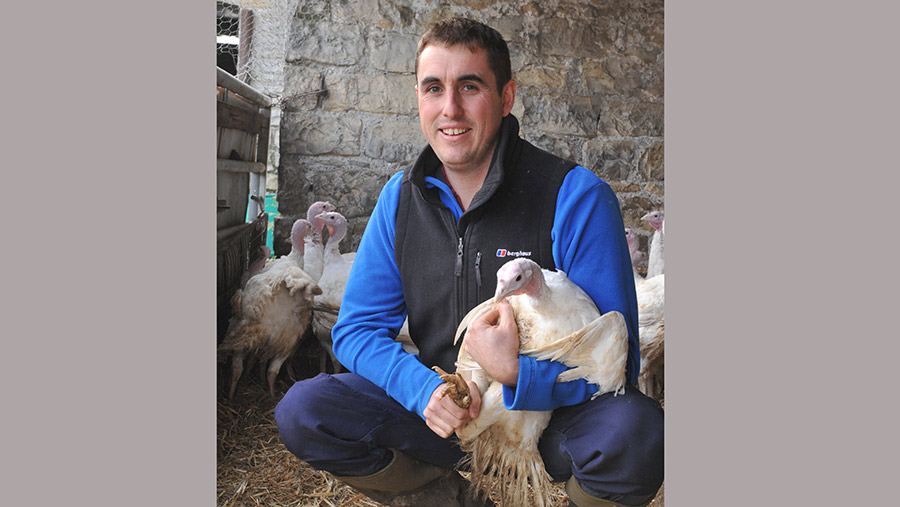
Tom Rees © Debbie James
“For years, we used a supplier less than a mile from the farm and after he stopped, he recommended our current supplier.
“That is worth a lot because you need to be sure that the birds have had a good start,’’ says Tom, who farms with father Robert, uncle Edward, brother David and cousin Owen.
The poults are housed on straw in two buildings that are used as calving sheds at other times of the year; these are washed and disinfected before the poults arrive.
Sheds are protected with wire mesh to keep wild birds and predators out.
Feed is initially a crumb, followed by a 19.5% protein rearer pellet and finally, three weeks before slaughter, a finishing pellet, all sourced from a feed merchant.
One of the biggest challenges is achieving the range of weights specified by individual customers, but most buyers accept that there will be some variation on what they have ordered.
The majority are repeat customers, with some families buying their turkey from Bryn Farm every year since they were first sold, so little marketing is needed to secure sales. Word of mouth draws in most new customers.
The turkeys fit well with other demands on the farm, housing availability, and the capacity of the cold room, says Tom.
“Slaughtering and dressing take two days and we can just about manage to fit that in around all the other work at that time of the year.”
Farm facts: Bryn Farm, Cowbridge, Vale of Glamorgan
- 384ha farmed, including 16ha spring and winter barley, 10ha maize
- 120 Aberdeen Angus cross Friesian and Hereford cross Friesian suckler cows
- 60 dairy beef calves bought in annually to rear and finish or retain as herd replacements
- 500 Mule ewes tupped to Suffolk and Texel rams