4 tips for effective cleaning between free-range flocks
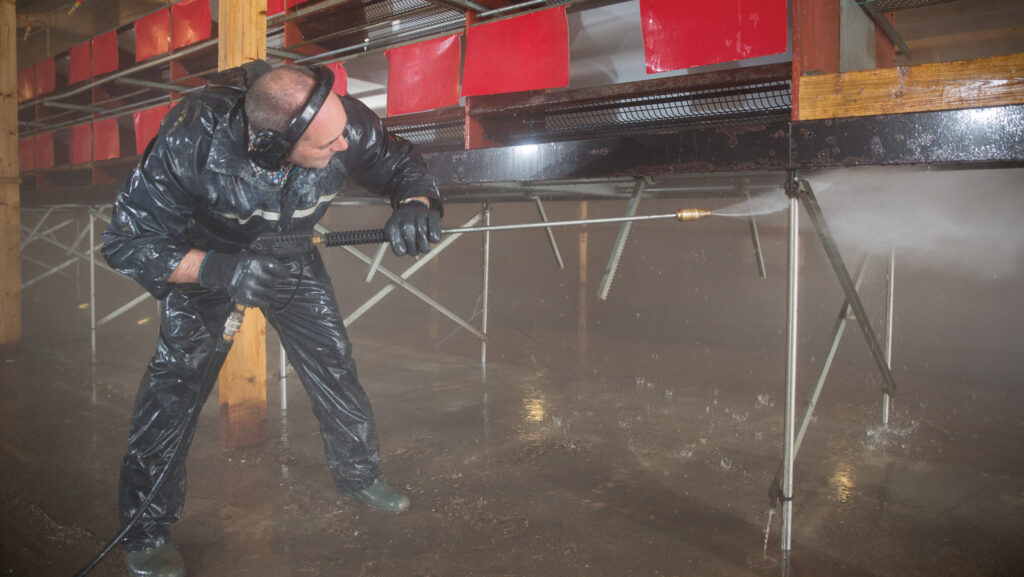
A subdued supply of free-range eggs on the market is putting poultry producers under pressure to manage tighter turnarounds between flocks.
At the same time, they are having to contend with stricter salmonella checks in their pre-housing swabs to comply with version eight of the British Lion Code of Practice.
David Clegg, biosecurity adviser with Coventry Chemicals, says having a clear plan and sticking to it is critical to success when cleaning and disinfecting free-range poultry housing between flocks.
See also: How an organic egg producer eliminated nuisance flies in sheds
David advises focusing on four key points when tackling these tasks.
1. Thoroughly remove organic matter
“It’s a case of thinking logically about the process,” he says, estimating that 80% of the effectiveness of a clean comes from removing organic matter.
“If you want to do red mite treatment, remember there will be places where they can hide in the muck.
“The first thing you need to do is a proper dry clean and remove as much of the organic matter as you can. This includes litter from the floor and anything on the muck and egg belts. Get it as empty as you can.”
Once a thorough dry clean has been completed, he recommends applying a detergent to lift residual dirt from surfaces.
2. Use appropriate products
Not all disinfectants are the same, says David. Chemicals have a range of attributes, and some will be more effective against certain types of pathogen than others.
He suggests asking the following: “What are you trying to achieve? Do you have any challenges within your farm that you are trying to eradicate and is there a product that might help you to do that more effectively?”
He recommends a two-stage disinfection process, where complementary chemicals can be used separately to create the most effective knock-down of pathogens.
“If you want a belt-and-braces approach, you can use two disinfectants and a fog at the end,” he adds. “There is a time consideration, but the fog will likely reach any areas you might have missed.”
Producers should make sure they are aware of all the available options and are getting value for money.
David advises speaking to a range of suppliers to see what rates are possible with different chemicals and check that the proposed product is fit for purpose.
3. Apply disinfectants at the correct rate
Any supplier of chemical cleaning products should be able to provide producers with a plan that calculates the appropriate amount of chemical and water for each shed, he says.
“Whoever does the disinfection needs to stick to that,” he emphasises. “That is really important. If there’s too little, it won’t be effective against pathogens; if there’s too much, you are wasting money.
The dilution rates are there for a reason.”
Adding disinfectant to a water bowser with a defined volume can be a good way to be certain the amount of solution is correct. If a dosing pump is used to mix the chemical, care is required.
“You need to make sure it is set at the right level, and it is working correctly,” he says.
4. Is a cleaning contractor or DIY best for your setup?
There are pros and cons to doing the cleaning in-house. David says the advantage is knowing a good job will be done.
“You’re going to spend the time to do it properly. Cleaning companies are usually paid by the shed and often they want to get through it as quickly as possible.”
The downside is that time farm staff spend using a pressure washer during turnaround is time not spent elsewhere.
“The reality is, as turnarounds become tighter, and particularly if you have a lot of sheds, are you really going to be able to do it on top of everything else required of you at such a busy time?” he says.
Using a cleaning contractor will still require a level of input: management time is required to make sure the process is being completed to the correct standard.
“Do not presume they are going to do a good job. Check they are using the correct dosing rates, and they are removing that organic matter properly,” he says.
A vet’s view on turnaround management
Vet Charlotte Cole, who manages St Davids Poultry Team’s Yorkshire practice, says turnaround is a really important time when farmers can get on top of pathogens and limit the carryover of disease from one flock to another.
“Every flock is different and has its own disease burden,” she says.
“Some farms will have repeated issues with certain pathogens. For example, pasteurella can be quite difficult to get rid of as there are lots of things that can carry it over.”
She also singles out E coli as having an effect on many flocks, coming to the fore when birds become stressed.
“These are high-performing animals, so the risk of them getting stressed is high. We see some farms that may have resistant E coli.
“If the producer doesn’t clean the sheds properly, that can carry over from flock to flock, leading to peritonitis and elevated mortality,” she says.
She also highlights red mite, which not only causes problems during production, but can also be a vector for disease:
“If you’ve got red mite hanging around in your shed, they will carry over certain diseases,” says Charlotte.
“Using disinfectants that kill mite eggs are really helpful. Also think about timing your red mite control close to turnaround to reduce the risk of disease transmission.”
Effect of stocking density
She says while free-range birds do go outside, the disease risk from the range is quite different to that in the housing.
Birds will be exposed to a wide range of pathogens on the range, but stocking density is lower than inside, and the effect of any harmful bacteria is diluted by the number of other less-pathogenic organisms.
Inside, conditions are very different and the pressures for disease to build are increased.
“Stocking density is key,” says Charlotte. “Where birds are denser, there will be a higher build-up of pathogens – for example, around your feeders, drinkers and nest boxes.
“We know bacteria are everywhere, and having a wide range is good for both human and bird health. When we are exposed to one pathogen at an extremely high level, that is when we get issues.”
Mistakes to avoid
Charlotte says the most common mistakes she sees with turnarounds on free-range sites are:
- Not using enough detergent to remove organic matter before a disinfectant is applied
- Forgetting to clean ancillary areas such as the egg packing room and the toilet, leaving behind dust and dirt, which can undo the hard work of cleaning the space where the poultry are
- Failing to reinstate biosecurity measures as soon as disinfection has taken place.
“Once the shed has been disinfected, the doors should be closed and all the biosecurity measures should be back in place – as if you have brand-new birds in the shed,” she says.