What is lean management and how can it improve pig farming?
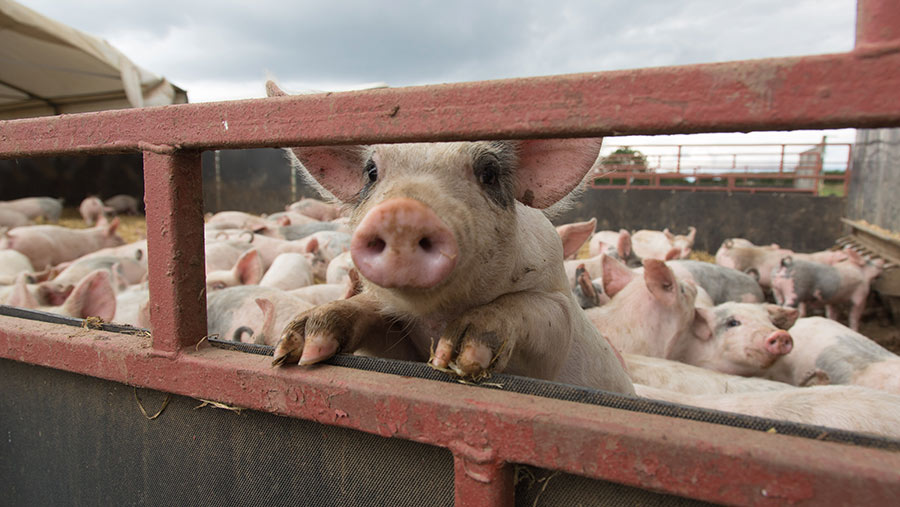
Lean management is a general business improvement technique that originated in the car manufacturing industry.
The concept is successfully being applied to 12 pig farming businesses through the AHDB’s Smart Pork programme to help them reduce waste.
Neil Fedden, a lean management consultant involved with the programme, explains the main principles and how they can be applied to pig farms.
See also: Glassers disease in pigs: Signs, treatment and prevention
1. Identify the value
What activities add value to the product you produce?
Determine where cost is being added to your business for no benefit. For example, how many pigs are out of specification? Identify waste in your processes and free up this time to focus more on the added-value activities.
2. Value stream mapping
Map out your business workflow. This should involve thinking about the exact protocols used for specific tasks and who is involved.
Pick a process you do on the farm every day – this is where the opportunity lies to make the biggest difference. This could involve cleaning or moving pigs, for example.
Use colour-coded notes for value-added and non-value-added tasks. This will make it easy to see which parts of the process deliver the most value and should highlight where waste can be reduced to improve production.
Get employees to suggest what they can do to improve workflow, so they take ownership.
Once you take a step back, break down processes and challenge each stage, you will get a good understanding of where the problems lie.
Make easy, high-priority tasks your main concern.
3. Develop continuous workflows
Next, create a continuous workflow – visualise the workflow and divide it into smaller subsections to prevent any breakdowns.
For example, if mistakes are made on a car production line, people must come in and strip the car down and solve the defects. You want to avoid this.
If there has been an issue, use “fishbone analysis” to work backwards and look at what caused it.
Get the team to identify as many contributing factors as possible to the problem and then highlight the three most critical causes and focus your action on these.
The idea is to eliminate as much waste as possible so you get better flow in routine jobs such as cleaning and feeding. That routine will then become quicker and more efficient for the individual doing it.
This is a concept known as “effortless effort” and is like driving to a destination without realising how you got there.
Top tips
- Involve your whole team – before you start, ask them where they would invest more time in preparation for making time savings
- Get “back to the floor” to help identify where day-to-day improvements can be made
4. Create a ‘pull system’
Create output based on demand instead of relying on forecasts.
For example, if you have a contract to produce a certain number of pigs every three or five weeks, that sets the clock speed for the business.
Sequence everything around this, from raw materials to the allocation of labour.
This will help with cashflow, so you are not bringing in materials too early.
5. Seek perfection with continuous improvements
Plan, do, check, act.
If the process hasn’t worked, go back to the start.
Once you start to see waste, you can’t unsee it. Just because you have always done something one way doesn’t mean it makes sense to continue.
Often, a system was implemented because there were constraints on the business – such as technology wasn’t available or it was cost-prohibitive – which are no longer there.
Case study: David Childerhouse, Suffolk
Outdoor weaner producer David Childerhouse is at an early stage of applying lean management principles to his business, but he is already seeing big improvements.
He likens it to a “sword-sharpening exercise”. “You will cut the wood quicker if you stop to sharpen the sword,” he explains.
He has already identified where he can reduce waste by producing fewer out-of-specification pigs.
“I’m trying to produce a 7kg weaner for sale, and if we end up with a sub-6kg pig at the end of the process, it is too late.”
He says he was proud of the “fantastic facility” he had for underweight pigs, but realised he was better off putting that energy and time into reducing the number of small pigs he was producing in the first place.
Mr Childerhouse carried out a fishbone analysis with his team to pinpoint all the possible causes.
Closer investigation revealed water availability to be the main contributing factor to out-of-spec pigs.
“It came down to water provision in the last 10 days on individual paddocks,” he says.
To rectify the problem, he used some long porridge troughs – one placed between two paddocks – and pumped them full of water.
“The good thing about pigs is you get the chance every week to change something around, and we saw an immediate result with a tremendous increase in weaning weight.”
Underweight pigs have reduced from 10% to less than 5%.
Mr Childerhouse has also made improvements to save time when feeding the pigs.
Rather than filling 20 hoppers every week, the capacity of the hoppers has been increased, and now 10 are filled every other week.
“It takes half the time and half the labour, and this was just plucked from one of the first exercises we did. We saw the benefits immediately.”