Pig farms making small changes see savings of £250k/year
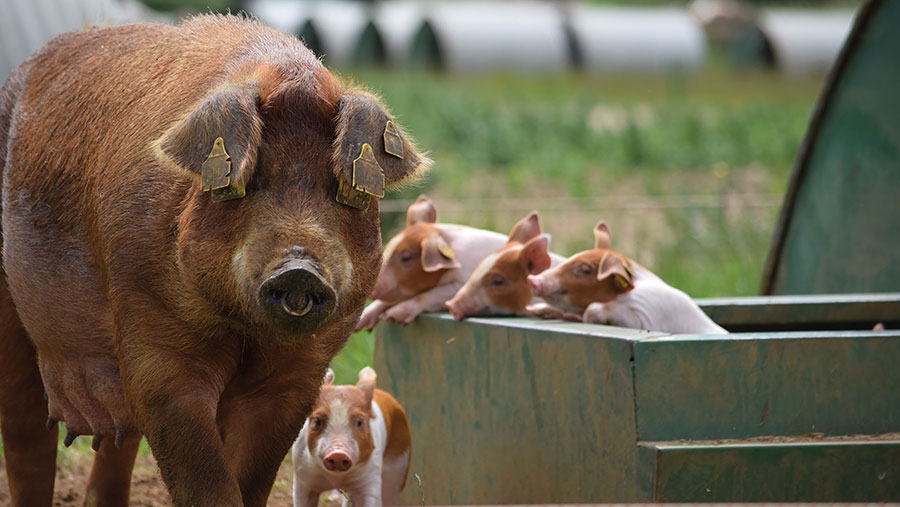
Small changes can have a big impact over time, a two-year AHDB Pork project adapting lean management principles on six pig farms has shown.
Taking a step back from the daily routine to analyse their businesses – rather than working on a hunch – has helped these farmers improve efficiency and profitability, saving as much as £250,000/year (see “AHDB SmartPork savings”).
The key driver to success was involving farm staff in adopting “lean management” principles.
Staff were asked for ideas to challenge established routines and look for ways to improve productivity and save money, says AHDB Pork’s knowledge exchange manager, Andrew Palmer, who worked on the project with lean management consultant Neil Feddon.
See also: What is lean management and how can it improve pig farming?
Part of the process involved taking a waste walk around the farm and itemising specific jobs in the routine.
Each step was timed and travelling distances were added up.
The data set was then used to work out areas of waste, as well as measure the results of improvements.
Lean management process
- Reducing waste
- Adding value to assets
- Gains usually small and incremental: 1% rather than 20-30%
- Waste walk
- Analyse data
- Map out routines step by step
Key areas for the six businesses were:
- Out-of-spec pigs (linked to feed and weighing)
- Identifying the cost of small pigs (and how they are managed)
- Gathering data (to focus on improving parity).
While some farms had multiple areas where they made changes and saw benefits, others focused on a particular problem, says Andrew.
The farms tackled labour efficiency and automation, plus basic routines such as weaning, mucking out, bedding up and moving pigs.
The forklift schedule was another, he says. “On one farm with breeding, rearing and finishing operations, it was ‘can you just…?’, so [the forklift] was here and there, with no jobs finished and elongated routines.
“Once it was put on a time schedule, it was better utilised.”
Andrew says a classic improvement for many farms is the use of a shadow board for tool storage. People can then find the right tool to do the job quickly and easily, rather than hunting around for a missing spanner.
AHDB SmartPork savings |
|||
Farm |
Annual savings |
Cost (one-off) |
Areas identified |
A |
£50,500 |
£15,000 |
New feed lines; water provision; tools and maintenance; white boards; daily routine improvements; moving and handling equipment; small pig impact trial; improving finishing-pig transport logistic planning with contract haulier |
B |
£241,500 |
£14,600 |
New ad-lib hoppers in farrowing paddocks Reduction in sow herd owing to improved breeding performance |
C |
£58,600 + £143,000 |
£30,000 |
New gilt housing and subsequent improved breeding herd parity profile, gilt retention, productivity and increased sales |
D |
£20,000 |
|
Change of diet specification, weighing and P2 backfat-measuring of pigs |
E |
£4,500 |
|
Small pig impact trial – ongoing. Weaned smalls reared in two different ways: on sow at £10.04 a pig, compared with rearing on transition feeder at £3.39 a pig |
F |
Saving 1.5 hours on the routine x four people = six hours/week x 52 = 312 hours/year |
|
Weaning routine |
“One farm spent £1,500 on a tool board and tools, but [despite this cost] within a couple of weeks the maintenance man’s workload had halved. It’s starting with little things but looking at them differently.
“A small efficiency change multiplies up over a year and, all of a sudden, those numbers start to get bigger,” he says.
Getting everyone in the team involved spread the workload and got more buy-in, says Andrew.
“Ideas that have most success come from people on the ground doing the job – small, bite-sized stuff where staff can do it themselves and get on with it,” he adds.
Another benefit of the process came from writing it all down, says Andrew.
“Once you put a number to [farm processes] on paper, it gives you a structure and an actual cost. One farm replaced its ad-lib hoppers and when they worked out the actual feed saving, they could see beyond the initial investment.”
Case study: Dingley Dell Pork
Farm facts
- 720-sow outdoor unit
- Developed own breed, Suffolk Red, based on Red Duroc
- Bred for marbling for taste and flavour
- Sell to restaurants
- Wean 11.4 pigs a litter
- Weaned at 35 days for past 25 years
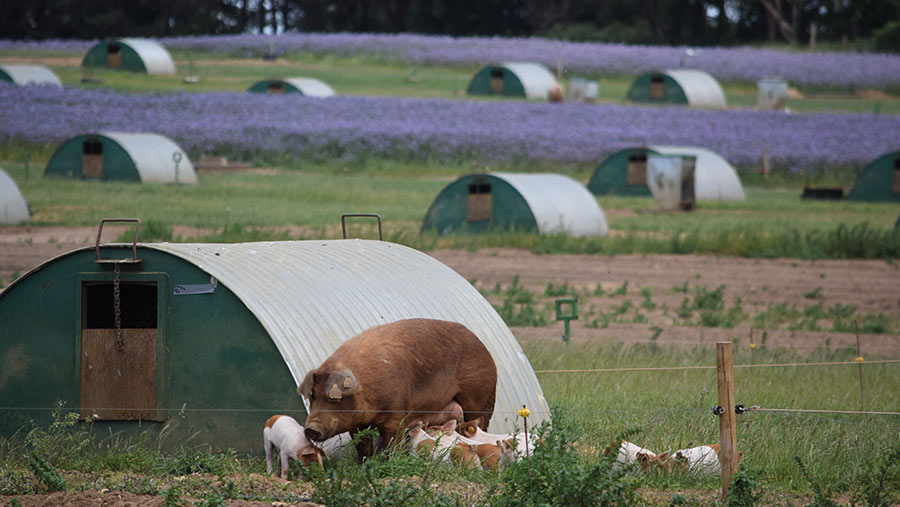
© Mark Hayward
A quicker, slicker routine has shaved 1.5 hours off weekly weaning for the team at Dingley Dell Pork near Woodbridge, Suffolk.
It has also reduced staff required in the weaning team from four to three.
At a basic minimum wage rate, this would save more than £3,200/year.
More importantly, for business owner Mark Hayward, it is time saved, improved farm efficiency and a boost to staff morale.
“People can finish work early or have more time off. Man hours can be put into an extra job, or maintenance jobs that don’t necessarily get done regularly, such as cleaning out water troughs.
“And we have time to pay more attention to stock,” he says.
Mark was keen to improve efficiency. He got his total staff of seven involved following a team talk on “lean management” by AHDB’s knowledge exchange manager, Andrew Palmer.
He was interested in how his staff could look at the farm’s processes and current communication to bring some structure to the business, as well as more productive work routines.
As one of the farm’s main tasks, weaning was the natural starting point. It is a job best carried out in natural daylight, to be more in tune with animal behaviour and reduce stress levels, says Mark.
“Sows are very protective of their babies and when they are in daylight, they are more relaxed and happier because they can see properly.
“But weaning was taking from 5.30am to 9.30am or, on a bad day, 10am, because we might not have had a trailer on a tractor, not enough people, or someone might have been late.”
He set his team the challenge of shortening weaning time. Using the lean process, the team spent two to three weeks discussing the jobs and writing each step down, considering options and variations to try out, he says.
“By formalising the process, everyone thinks more about it. They talked through it, one step at a time, and came up with the answers.
“We looked at having stuff in place, the right people needed, and timed it. Staff [also] discussed the implications of lateness. Now it’s quicker and more efficient.”
At 2.5 hours instead of four, weaning is a smarter operation. The night before, the trailer is hooked to the tractor and in the right place for the job.
“We’ve now got what we need – and where we need it – which has reduced time. We have, on a good day, shaved two hours off the process.
“Also using a feeder just ahead of the trailer picking up sows encourages the sow out of the ark, so picking her up is a lot quicker,” says Mark.