Video: Producer solves piglet crushing issue with moving crate floor
A Lincolnshire farm has seen piglet mortality fall as low as 0.5% in farrowing houses through investment in mechanised, sow-activated, crate flooring.
When farm manager Ian Smith started working at Patrick Dean Piggery, Lincolnshire, 19 years ago, piglet mortality in the old-fashioned, solid-floor farrowing units stood at 13-15%, with overlaying in the four days after birth the main cause, killing about 10%.
Watch the video of how the crate works and read the detail below.
Overlaying – defined as crushing of piglets by treading, trapping and lying – is one of the most frequently recorded causes of death in newborn piglets in indoor and on outdoor pig units.
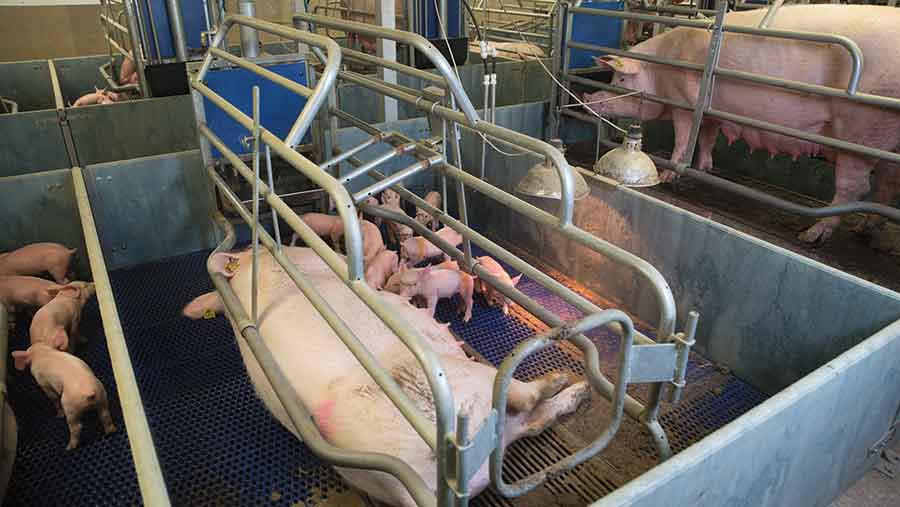
© Tim Scrivener
See also: Slatted housing found to harm piglet survival rate
On slatted floors, which were later partly installed in two farrowing rooms of 24 as part of a herd expansion, overall piglet mortality due to crushing fell to 7%, and overall to 10%.
“There used to be solid floors, they didn’t have saver bars, and they used to have to muck it out twice a day, which meant a high labour input and power washing. It took twice as long and the mortality rate was 13-15%,” says Mr Smith.
“Even with slatted floors we had a mortality rate of 6-7% of born alive – not the 1% we were told these rising crates would give us.”
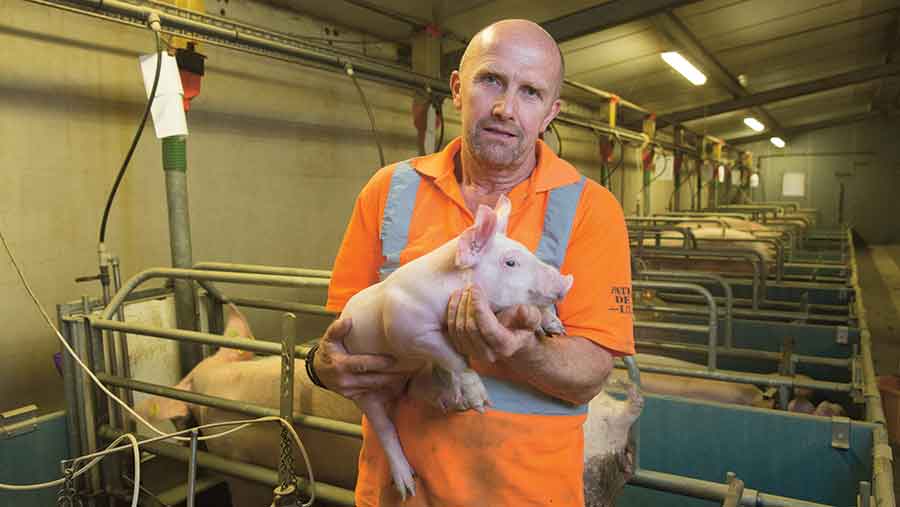
Ian Smith © Tim Scrivener
Then, 12 years ago in early 2004, Patrick Dean Piggery became one of the first farms in the UK to invest in the Nooyen Balance Crate.
Widely used in the Netherlands, the Dutch systems are designed to reduce piglet mortality caused by overlaying.
When the sow stands to eat or drink she activates a switch, causing the sow slat and piglet slat to move to different levels.
When she lies down again, the sow slat and the piglet slat move back to the same level, giving piglets essential access to milk.
Triggered when the sow lifts itself off a ground sensor, the early version – still in operation in some of the farrowing houses at Patrick Dean Piggery – sees the piglet slat lower, preventing piglets being crushed.
“With the first sets, mortality went down to 1% of born alive in the first five days,” says Mr Smith, who has worked on pig units since before he left school.
Newer versions of the Nooyen Balance Crate – which instead sees the sow slat rise to a safe height when activated by “fingers” positioned above the animal – were then installed in a new build on the site in 2005.
In 2014, two farrowing houses of 24 were converted into two rooms of 26 and the newer version installed.
In these houses, pig mortality due to overlaying averages at 0.5-0.6%, says Mr Smith.
“Performance is much the same, but the ‘fingers’ more accurately read the position of the sow than the floor sensor,” says Mr Smith.
“If the sow is standing on the floor sensor when it rises, the floor won’t move, and if not laid on properly by the sow, the floor won’t rise again, meaning piglets don’t have access to milk.”
Extra meat
Patrick Dean Piggery is home to around 580 sows.
Mr Smith looks to farrow 26 sows a week, producing a target of 330 piglets a week and a yearly average of 28 piglets a sow.
Nowadays, every crate designed for sow and litter in each of the farm’s five farrowing houses is fitted with a Nooyen Balance Crate.
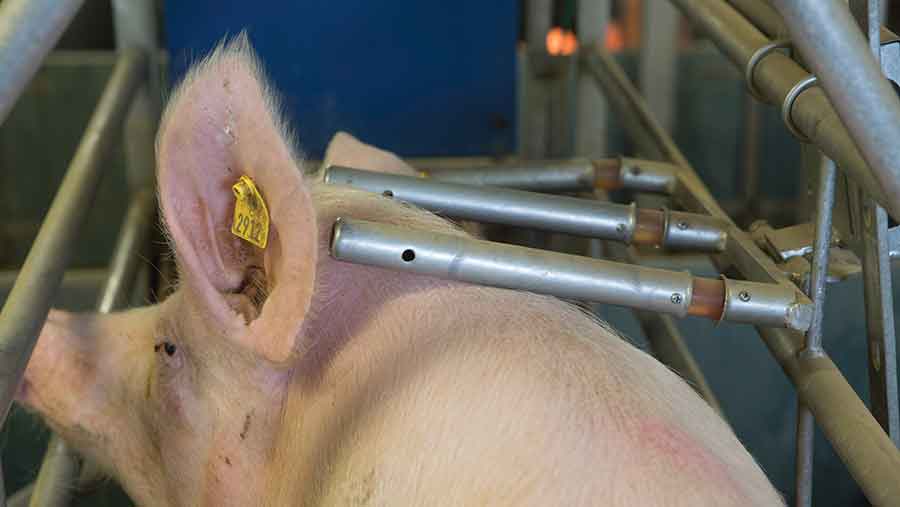
Sow activating raised floor © Tim Scrivener
Piglets are weaned at 28 days in the farrowing houses before they move on to one of the farm’s 10 nursery rooms and then on for finishing before being sold to Woodheads, a wholly owned division and supplier of Morrisons.
The Nooyen crates are turned on for the first seven days after birth. After that, piglets are considered strong and quick enough to avoid being crushed by their mother or adoptive sow in the crate.
See also: RSPCA slammed for change to standard size for pig pens
Prior to the farm’s investment in Nooyen Balance Crates, they were losing 7% of piglets to overlaying – or 21 from an output of 300.
With the earlier sensor-activated Nooyen model, 1% are lost as a result crushing, or three from a total of 300, but with the “fingers”-triggered model, mortality from overlaying averages 0.6% or two piglets from 300.
Taking into account 4.5% pig mortality post-weaning, Patrick Dean Piggery is figuratively 17 piglets better off each week.
At an average deadweight of 85kg, Mr Smith says there is the potential to come away with an additional 1.4t of pigmeat a week when compared with output prior to the Nooyen investments.
With each of the five farrowing houses used 10.5 times a year, that’s an extra 14.5 tonnes a house a year or in excess of 70 tonnes extra in total, he says.
Costs
Mr Smith says Patrick Dean Piggery has also realised labour cost savings since the Nooyen systems were installed with less extensive monitoring of the farrowing pens required.
“Labour-wise, it also takes half the time to power wash compared to the solid floor system we used to have,” he says, adding that additional electricity costs are minimal.
“The compressors [which drive movement of the slats] only work in two rooms at a time,” he says. “And you’ll hear it running for five minutes then you won’t hear it again for a while.
“There is an additional cost, but I wouldn’t think it is a huge cost.”
See also: Farrowing house electricity costs higher in summer than winter
On the whole, the cost of installing the Nooyen Balance Crate is justified, he says.
He says the first set of Nooyen Balance Crates bought in 2004 paid for themselves in two years.
“The best mortality rate we ever achieved before [the Nooyen crates] was 6%, so it was a no brainer,” he says.
“To replace flooring in 26 conventional farrowing crates it would cost about £800 a space. To convert a conventional space [and install the Nooyen floor] would could in the region of £1,200.
“It is more expensive, but if you break it down it is only £400 difference per space.”