How changes in pig unit staffing raised weaning weights
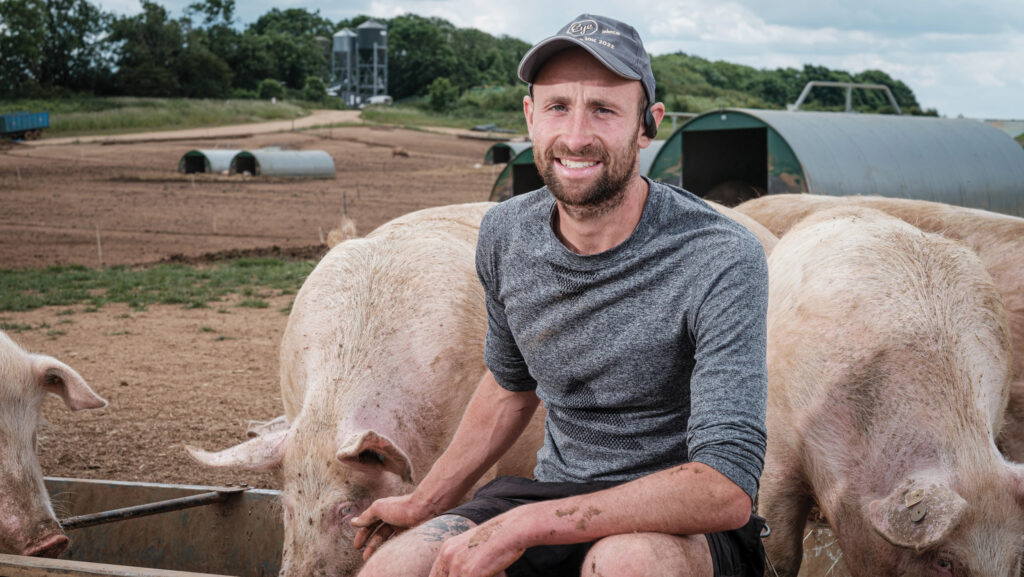
Employing a former car sales executive has helped pig farmer James Ross improve weaning weights on his two outdoor units in Lincolnshire.
Piglets are now 0.7kg heavier at five weeks of age, thanks to a more efficient and accurate approach to feeding sows.
James says he has always focused on nurturing staff to ensure their retention.
Having struggled to get into farming himself as a keen 18-year-old, he remains passionate about bringing in people from outside the industry and devotes a lot of time to training.
See also: Farmers Weekly Awards 2024: Pig Farmer of the Year
“As a result of winning the award, we had two new girls start in December who had read about us in Farmers Weekly,” he explains.
“One of them [Ellie Nobbs] had been working on a boar stud unit and got in touch to see if we were taking on any permanent staff. Of course, we always are.
“She came with experience that has been really beneficial to the business.”
Farm facts
BQP Pigs, Lincolnshire
- 1,750 sows across two outdoor units
- Operating a two-week batch, five-week weaning system
- Using largely single-sire, purebred Landrace genetics
- Produces weaned pigs for BQP, target weaning weight of 10kg
- Red Tractor- and RSPCA-assured
Ellie now carries out all the serving alongside another member of staff, as well helping with general dry sow management.
A few weeks later, Ellie’s partner, China Smith, got in touch, wanting to make a move from a career in car sales to farming, explains James.
“We had her [China] out for a week’s trial – as we know pigs in December aren’t for everybody – and she took to it like a duck to water.
“They’ve both been a huge success,” he says.
Weaning weights
Since then, James says the farm has made significant improvements to weaning weights, moving from an average of 8.7kg to 9.4kg – getting them closer to their target of 10kg.
He attributes this largely to China, who is responsible for managing the farrowing and feeding and has made the whole process more efficient.
“We feed the sows differently now and almost treat them like an indoor unit,” he explains.
Detailed information about every farrowing row and individual hut is kept in the tractor, so each sow can be fed “exactly what she should be on that day, following the feed curve”.
“Before, we just generalised a row and went by an average of what they should be eating.
“Although it takes longer now, it’s far more accurate, and the proof’s in it [the weaning weights]. You can see the results.”
James is also now using suckling pods to foster weaker piglets.
This has involved modifying existing hutches with hurdles to create enclosures for the piglets.
“We go through [the piglets] a couple of times a week and pull off anything that is not keeping up with the rest of the litter.
“We then put them in with the cull sows and create what we call ‘bonus litters’,” he says.
Work-life balance
As well as the benefits to pig production, the increased staffing has also meant a better work-life balance for the whole team.
“We almost sit now slightly overstaffed, but it means that everybody is getting regular time off – me included,” he says.
“I now look after my son two days every other week while my wife works, so I’m starting to get the family-life balance a bit better, too.”
The 2025 Farmers Weekly Awards
The 2025 Farmers Weekly Pig Farmer of the Year Award is sponsored by Pilgrim’s Europe.
Enter or nominate at fwi.co.uk/awards25