Advice on setting up a new pig unit
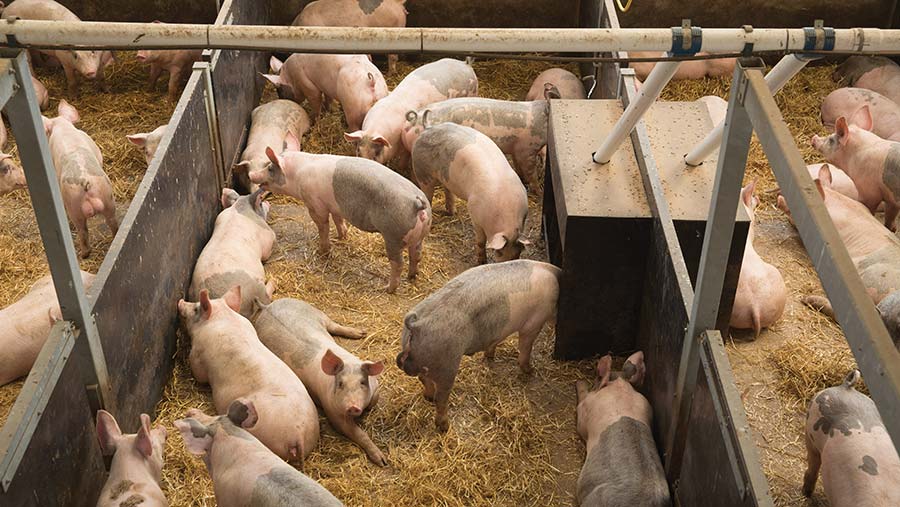
Price swings are synonymous with the UK pig sector, but with the five-year outlook indicating promising times for the industry, pig production could be a viable option for some farming businesses.
A farrow-to-finish enterprise is the most common system in the UK, but setting up a new pig unit needs some careful planning.
Debbie James asks industry experts for some pointers on how to set started.
See also: WIYLS visits a dairy to pig conversion in Carmarthenshire
Minimum number of sows required to make it viable
For indoor units, AHDB Pork recommends 500-1,000 sows and for outdoor systems 800-1,000 sows
It says smaller units can be profitable, but these numbers make a system very workable for staff.
Set-up costs
Outdoor
Depending on equipment specification, for outdoor units budget £230-£420 a sow place, £35 a grower at 7-35kg (huts) and £76 a finisher at 35-110kg (huts).
These costings exclude land rent, tractors, trailers, bowser, feeder, bins, straw, water connection, staff facilities, electric connection and site access improvements.
Indoor
For new, fully slatted finisher accommodation, expect to pay £290-£390 a head.
A new indoor farrowing unit will cost in the region of £3,500-£4,500 a pig place depending on specification, feed system and scale.
Bear in mind that setting up a new pig unit will incur large costs without income until payment for the first sales is received, but there are ways of shortening this gap. You could buy in 100kg gilts to serve and the first bacon sales can be achieved within nine to 10 months, for example.
Include projected feed costs in your budget – latest figures from AHDB Pork for a purchased, ready formulated diet are £279.38 a sow/year, £20.44 for a rearer animal (7-40kg) and £38.85 for a finisher (40-110kg).
Download AHDB’s feed and forage calculator.
For more information on costs of production in pig units, refer to our guide on the options for pig farming.
Breeding
Acquire high-quality genetic material and breeding stock – do your research to ensure you buy from a reputable source.
Pig breeds to consider for indoor UK systems are the Large White, Landrace and Duroc.
The best breed of pig to choose will depend on the market in which you are trying position yourself, so do your research first.
It is always advisable to engage with breeding companies to inform your final decision.
Infrastructure required – and retrofitting
A land base and a good supply of quality water are imperative.
Don’t skimp on the building and equipment as this will pay dividends further down the line.
Performance will generally be higher in purpose-built housing rather than converting existing buildings.
A slatted system is more expensive to build, but is efficient to run both in terms of labour and energy input.
In comparison, a straw-bedded system is cheaper to build but is more labour intensive and requires the purchase of straw.
However, straw-based systems are favoured by some processors because of welfare perceptions, and for outdoor systems seeking to finish pigs on a simple, flexible system, a straw-bedded finishing building can be a good option.
Seek advice on slurry storage and ensure you have sufficient land around the unit for disposing of manure and slurry.
Speak to suppliers about options for ventilation, feeding and water systems.
Good access for large lorries in all weather conditions is important.
Stocking densities
With slatted housing, allow at least 0.65sq m a finished pig place of uninterrupted lying area and for straw-bedded designs, allow 0.545sq m of uninterrupted lying area a pig, plus additional dunging area.
To comply with Red Tractor standards, stocking density in outdoor systems must not exceed 30 sows a hectare.
According to the new pig buildings design guide from AHDB Pork, a typical design for a supported roof, truss-style traditional finisher building with slatted floor, for about 1,000 places, will have 40 pens – 20 per side – each measuring 3×5.7m per pen and designed to hold 26 pigs up to slaughter weight.
This building will nominally be 61.265×12.458m, but will vary according to individual manufacturer’s specifications.
A standard, solid-floor, straw-bedded finisher building for about the same number of pigs will have 23 pens and separate dunging and lying areas.
The nominal dimensions of the outside of this type of building are 61.1×15.25m.
Planning considerations
Planning permission is required for all building and engineering works, but how this is interpreted at local level is subject to the opinion of the local planning authority.
A proposal may be classed as general permitted development and might only require a formal notification, but if full permission is required, arrange pre-application advice with the planning authority to establish how an application may be determined in line with local planning policies.
Consult the authority on building regulations because it can enforce changes to ventilation, lighting, drainage and fire prevention if they don’t meet minimum standards – it is cheaper to get these right from the start.
Secure a contract
Secure a market for your pigs before starting production. For new entrants, a contract in hand from a major producer or corporate supplier is often necessary to secure a bank loan for infrastructure.
Contracts can be found via main marketing groups, although good partnership agreements when setting up a new outdoor unit are available via the main integrators.
Some larger producers have helped new entrants into the industry with share farming agreements, although Andrew Palmer of AHDB Pork warns that this can be a disadvantage.
“The production numbers tend to run in higher group sizes to fit finisher batches but there are independents with smaller herds breeding and finishing with good financial returns,” he says.
To set up a unit with little or no capital reserve or security is difficult but there are longer-term finishing rearing contracts that give longer term security for ‘bed and breakfast’ operations.
Other routes to market
Some smaller scale producers have diversified into selling direct to consumers via on-line, farmers markets and farm shop outlets.
This can give good returns, says Mr Palmer.
“It can take several years to build a brand or product but the rewards are often better than larger scale operations and suit smaller business set-ups where individuals can utilise skills learnt in previous employments such as marketing, butchery and customer relations.’’
Setting up larger units with a reliance on extra labour can be a stumbling block as skilled staff command a premium salary.
Training to develop your stockmanship
Good sources of advice include:
- Contract providers
- Vets
- Feed suppliers
- Other pig farmers
- The AHDB Pork Stockperson Development Scheme covering each stage of pig production from service to slaughter and aimed at industry newcomers. Workshop sessions (currently on hold due to Covid-19) focus on basic knowledge and everyday tasks.
- In Wales – Menter a Moch
Case study: The Williams family, Home Farm, Leweston, Pembrokeshire
High demand for pork from a dairy farm’s pig diversification has allowed the business to increase the herd size threefold.
The Williams family established a herd of Welsh Pigs on their Pembrokeshire farm in 2019, buying sows from an established breeder.
They now have 65 sows and agreements to supply up to 70 weaners monthly to a farm shop to grow on and 25 to a butcher.
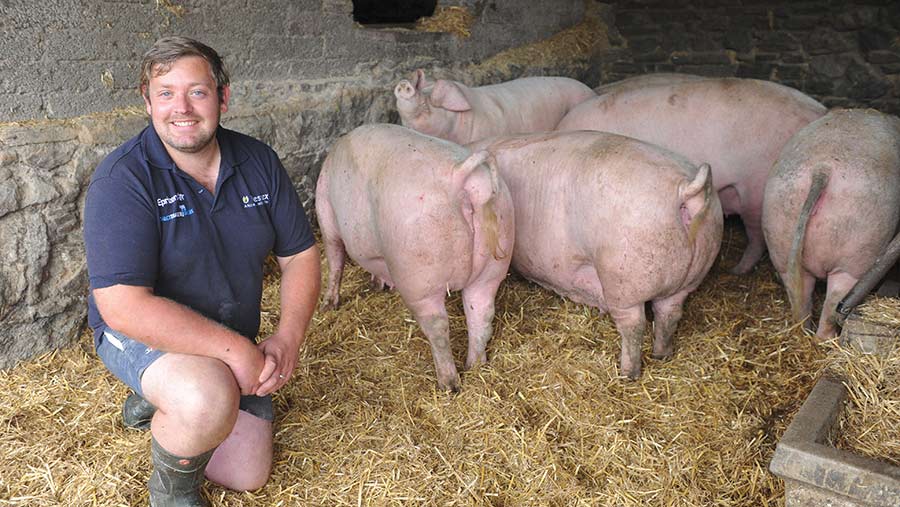
© Debbie James
Stuart Williams, who farms with his parents, Philip and Sharon, had contemplated keeping pigs since he studied the species as a module at Harper Adams University.
Establishment
He saw the potential of creating a second business on the family farm at Home Farm, Leweston, instead of scaling up the dairy herd.
Eighteen months on, and while the dairy business is under pressure from bovine TB, the pig unit has provided welcome support for cashflow.
Former cattle sheds were converted to straw-bedded pens which are well suited to this traditional breed.
With some of the sows now producing their fifth litter, the herd is at a point of profit.
“The first litter paid for the sow, the second for the infrastructure and on the third we started to get a return on our investment,” says Mr Williams.
Production
The herd produces 2.4 litters a year with an average of 13.2 pigs born a sow and 10.6 pigs weaned a sow.
All weaners are sold at seven weeks, two weeks after weaning when they have adapted to their new diet in familiar surroundings.
All service is natural using six Welsh Pig boars, including a reserve champion at the 2019 Royal Welsh Show.
Demand has driven expansion but the business would not have increased sow numbers without a written supply contract.
“That is key to, we wouldn’t have made that investment with just a verbal agreement,’’ says Mr Williams.
Making a success of the pig diversification had encouraged him to consider other opportunities for the business.
“If you put your mind to it you can do anything. I never envisaged us one day having pigs, but we have and it is working well.”