8 ways to produce award-winning silage
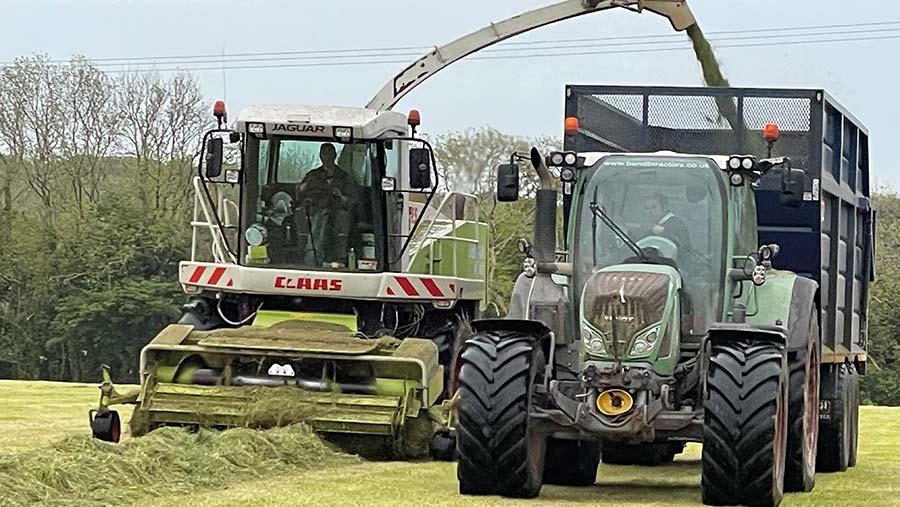
Producing a first-cut silage with a metabolisable energy value of 12.76MJ/kg dry matter and 14.7% crude protein does not happen by chance.
That level of quality requires attention to detail at every stage, especially harvest timing, at Parc-y-Marl Farm in Pembrokeshire, where siblings Nigel Williams and Joy Smith farm with their mother, Moira Williams.
See also:Â How to cut silage spoilage and on-farm plastic use with HOB film
“The first week of May is the most important time of the year,” says Mr Williams. “If you miss that opportunity, it messes everything up for the whole year.
“You lose the quality once the grass passes the peak of its performance.”
This mindset, coupled with attention to detail at harvesting and consolidation, produced the winning entry in the 2021 Federation of Welsh Grassland Societies’ (FWGS) All-Wales Silage Competition.
The family has been dairy farming at Parc-y-Marl, Llysyfran, for 69 years. The 205 Friesian Holstein cows are run on a split block-calving system with an emphasis on the spring block.
The herd produces an average annual milk yield of 7,500 litres, with 4,400 litres produced from forage.
This is achieved by growing high-quality grass for grazing from mid-March to mid-October and by producing the very best silage.
Farm facts
- 186ha (460 acres) farmed
- Closed herd
- 23.5 months – average heifer age at first calving
- Rolling average of 4.5% butterfat and 3.5% protein
- 1.3t a cow of concentrates fed
- Milk sold to First Milk
- Sexed semen used for first two inseminations
- 62% conception rate to sexed semen
- One full-time member of staff
- Beef cattle reared, fattened and sold direct to slaughter at 20-24 months
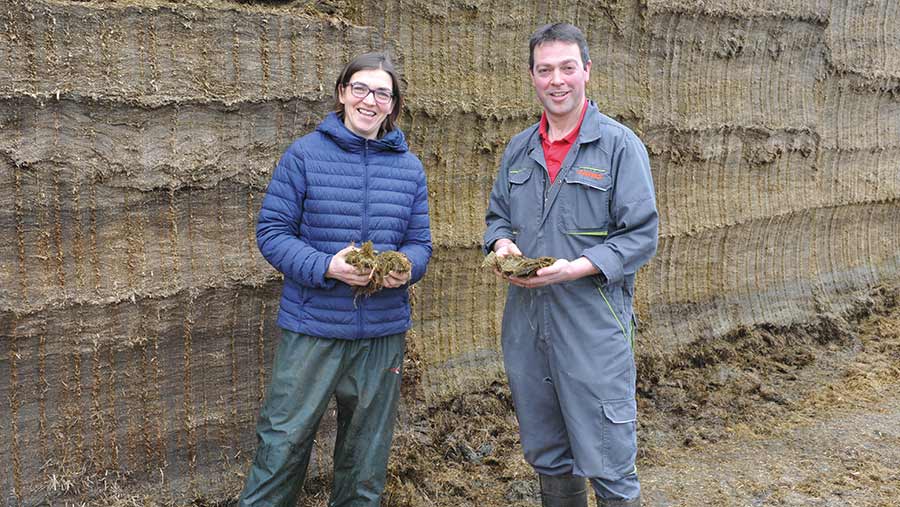
Joy Smith and Nigel Williams © Debbie James
Below are the silage management practices followed by the family to ensure silage of a consistently high feed value is produced.
1. Maintain soils at the correct nutrient status
Soils have an average pH of 6.5 and an index of 2-3 for phosphate (P) and potash (K).
In 2021, lime was applied to 50% of the farm in anticipation of higher nitrogen fertiliser prices, to ensure the best response to inputs.
2. Maximise the nutrient value of farm slurry
In the past 10 years, the business has focused on ensuring the whole farm has an application of slurry.
“Our contractor has a flow meter on the spread bars so we can see exactly what quantity is going on,” says Mr Williams.
The business also invested £1,000 in a swivelling slurry spreader attachment that was retrofitted onto the rear outlet of the tanker. Mr Williams describes this as “£1,000 well spent”.
The swivel mechanism is designed to reduce odours and improve the accuracy of digestate placement. The droplets produced are larger than a standard plate deflector.
“The ammonia goes into the ground, not into the atmosphere, and it gives a nice, even spread,” he says.
Three thousand gallons of slurry are applied to silage fields before first cut, followed by 100-113kg N/ha, topped up with P and K. This is followed by liquid N fertiliser sprayed directly onto the sward.
On the grazing ground, an application of 344kg/ha N is injected in liquid form in March, to release slowly.
3. Follow a programme of reseeding
About 20% of the farm is reseeded annually – with 20ha (49 acres) of winter and spring barley grown for wholecropping or crimping as part of the programme of grassland rejuvenation.
The preference is for an autumn reseed with late-heading varieties. Clover is added to the seed mix; after experimenting with different quantities, the family has found 1.2kg/ha works best in their system.
4. Manage winter grazing
Sheep graze the fields on tack from October to January and this helps with tillering.
“The sheep are a really good management tool,” says Mrs Smith.
5. Set cutting windows
The farm does three silage cuts. First-cut silage is taken between 6 and 12 May, with a six-week interval before the second cut and a further six weeks before the third.
The cutting window for the first cut is non-negotiable, but there is room for manoeuvre on the six-week rule with subsequent cuts.
“We don’t mind letting the second cut go to seven weeks, so we have a bit more fibre, because we generally ensile the first and second cut in one clamp,” says Mr Williams.
About 2,500t are produced over three cuts.
Big square bales are made specifically for dry cows from 8-10ha (20-25 acres) of first cut which has been allowed to grow on until the first week of June.
6. Plan to allow for timeliness
A machinery-sharing agreement with Mrs Williams’s brother, Anthony Phillips, and his son, Richard, who are also dairy farmers, allows silage to be made in-house; this has been in operation for more than 50 years.
Mr Williams says this agreement is key to the silage-making operation. “We share the cost so we can have good, decent-sized kit.”
7. Stick to cutting protocols
Grass is cut when the sugars are at their highest level, avoiding the early and late parts of the day.
The mower is set at a height of 7.5-10cm. “We don’t like to shave it; we like a reasonable stubble,” says Mr Williams.
The grass is wilted for 24 hours, and it is only tedded if weather conditions hinder the drying process.
“We have a spreader on the mower and if we can get away without tedding, we will, because the less time we mess with it the less the risk of contamination,” he says.
The silage is treated with an inoculant combined with a specific citrate.
A recent investment in 18t silage trailers fitted with wide wheels and a four-rotor grass rake reduces traffic over the fields, minimising compaction.
“We were running five trailers, but with the new trailers we only need three to keep up with the harvester,” he says.
“This has the added benefit of a steady flow of trailers into the clamp.”
An important feature on one trailer is a weighing system that can monitor weights to improve accuracy for additive application. It also allows for the monitoring of the performance of individual fields.
8. Ensure good clamp consolidation
Another “best buy” is a silo compactor. This is a set of rollers for consolidating the clamp.
“It reduces waste, and it also means the weight of the top grab of silage is the same as the bottom because it is being constantly rolled in thin layers. This way we are packing a lot more into the clamp,’’ says Mr Williams.
The clamp is sealed with oxygen barrier film followed by a 500-gauge black sheet and a secure cover, and then topped off with tyre sidewalls.
Mr Williams is strict about sealing the clamp as soon as it has been filled. “Whether we finish carting at 11pm or 3am, that sheet is going on.”