Farmer Focus: Wool needs a tech boost to save money
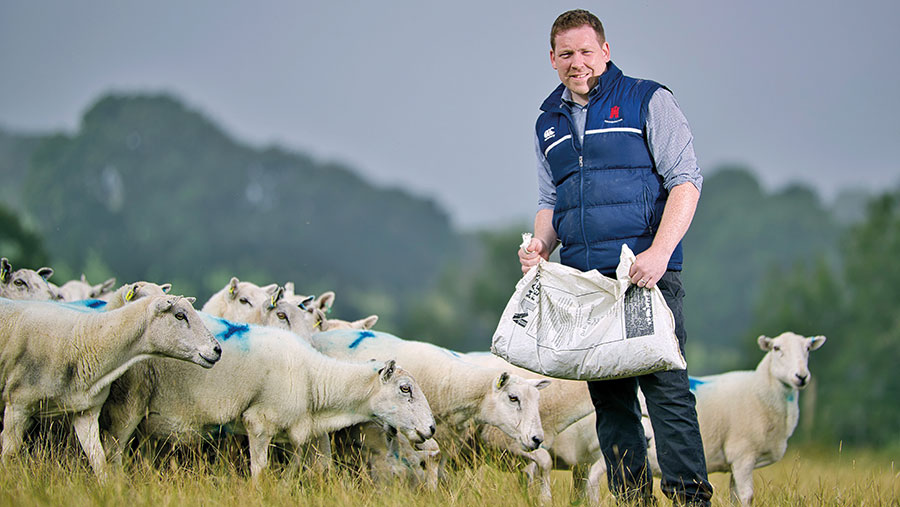
I haven’t always been positive about the prospect of the wool industry and have seen wool as a by-product of sheep.
It was suggested I visit British Wool to see how value is added to our wool. So, a couple of weeks ago, I took some students from the college on a visit there.
See also: Traceable wool scheme launched to help secure price premiums
We went to the grading plant in Bradford, along with a neighbouring scouring plant, to see the whole process.
The work that British Wool does is fantastic. I was impressed as soon as I walked through the door with the professionalism and presentation of the building, which considered the history of wool across the ages.
I was also impressed with their marketing room, which showcased the products available from wool – everything from yarn for knitting right through to bedding and mattresses. (By the way, I can advocate a wool mattress, as I have had one for the last couple of years).
We then went through to see the grading tables where graders – who have completed a three-year apprenticeship – assess every single fleece that comes through the door into one of 120 grades of wool.
From talking to the graders, I can see that British Wool has invested in technology to streamline the process, while adding value. But it has also kept the unique selling point of grading every fleece by hand.
We then drove down the road to the scouring plant. With only two such facilities in the UK, it was obvious from the outset it was a very busy place.
The senses were working overtime with the unique smell, noise, and sights that we saw, and it was a great experience for the students.
What was immediately noticeable was the energy required to process the wool. Wool is washed and dried and then fibres are carded to create the amazing finished product.
This uses a lot of energy, which probably doesn’t quite sit well with the sustainable story of wool and is where a lot of cost is added in the process.
With so much cost in processing wool, it is no wonder that the price paid to farmers is so low.
Investment is needed to drive efficiencies in wool processing, and this should be the priority for the wool industry.