Inside the UK’s first robotic rotary parlour
Combining robotic milking units and a rotary parlour has solved a dilemma for Somerset farmer and Glastonbury Festival founder Michael Eavis.
The 2014 Gold Cup winner wanted to switch to three times a day milking to ease the pressure on his high-yielding cows but was keen to alleviate staff pressure too.
This is why he resolved to invest in the latest in German engineering – a 36-unit robotic rotary milking parlour from GEA.
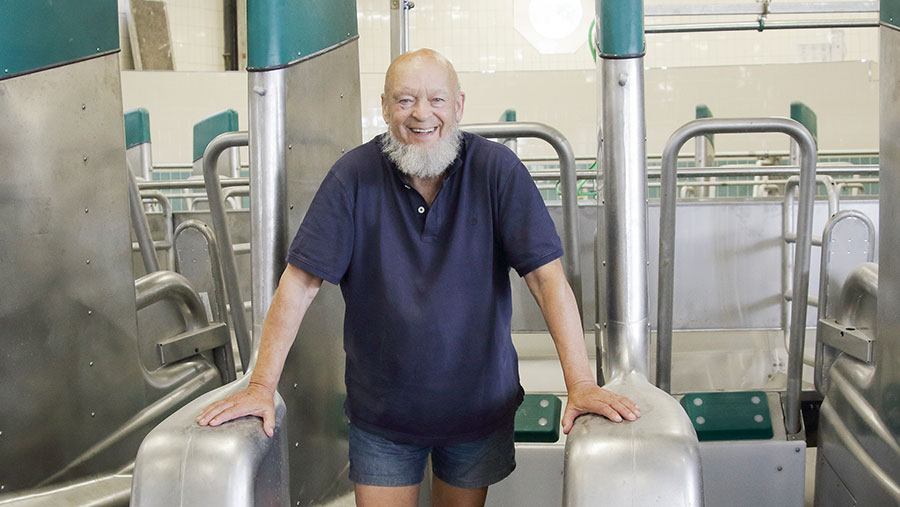
Michael Eavis at the 36-unit robotic rotary milking parlour © Geoff Pagotto
DairyProQ is the only robotic rotary on the market equipped with individual robotic arms at each stall.
Each robotic module handles every step of the milking process including teat cup attachment, pre-dipping, pre-milking, milking and post-dipping in one single attachment.
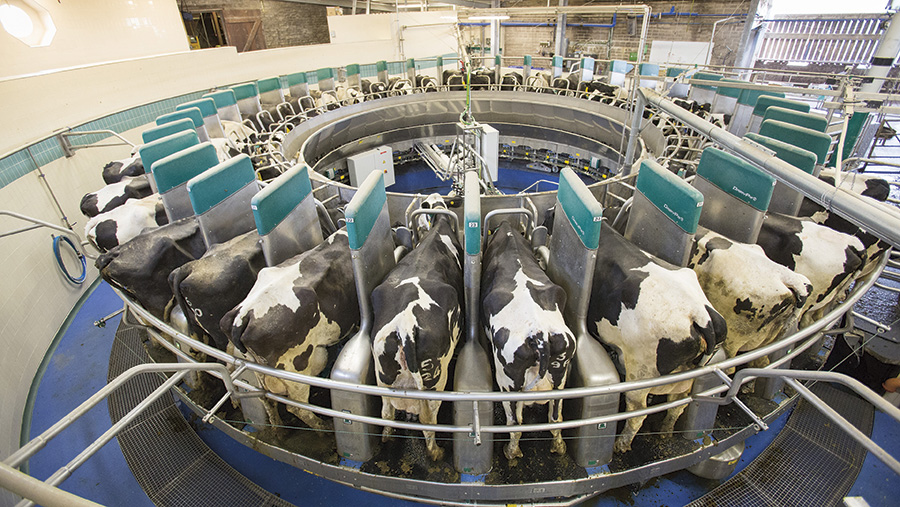
© Geoff Pagotto
The unit then automatically removes and back flushes between milkings to clean the clusters.
See also: Five steps for top returns from your dairy housing
Installation
Installation started in March and took three months, with work put on hold for the Glastonbury music festival.
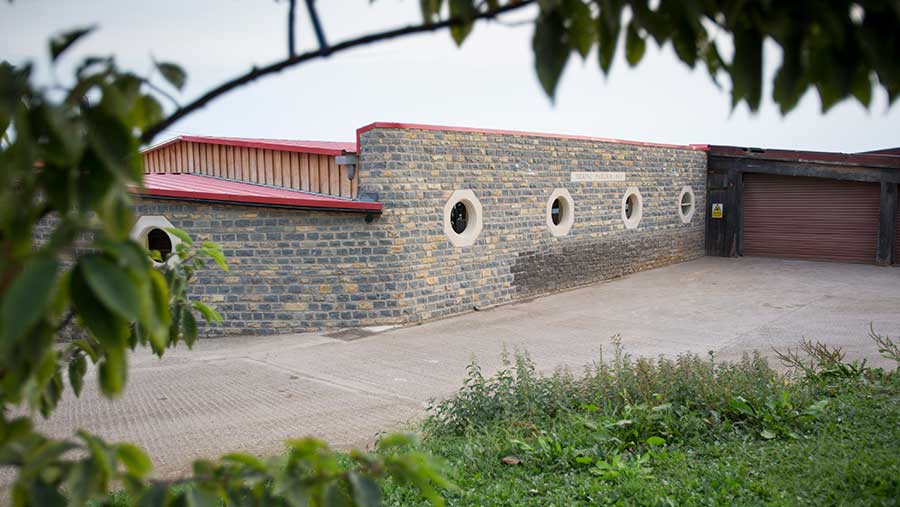
The rotary parlour has been retrofitted into an existing building previously used as straw yard housing © Geoff Pagotto
Wiltshire-based dairy engineers RMS Limited carried out the installation on behalf of GEA and they will also carry out maintenance.
Still on the old routine of two milkings (starting at 4am and then again at 3pm), the GEA DairyProQ, which was only installed one month ago (25 July), will hopefully facilitate the introduction of a third milking (5am, 1pm, 9pm) by mid-September.
Mr Eavis says the switch to three-times-a-day milking will help increase milk yields and improve udder health.
“I looked long and hard at the system and I thought that this was obvious the way to go,” says Mr Eavis.
Mr Eavis and his herd manager John Taylor expect a 10% increase in milk yields from the 387-head herd of Holstein once the system is properly bedded in.
Both believe averaging 12,535 litres a lactation means the farm is better off milking three times a day.
But while the desire was there to add in a milking to the routine, there was no desire to increase labour.
They also expect a positive effect on mastitis and cow comfort, but stress the impact on staff is also critical.
Labour reduction
One month into its working life the UK’s first robotic rotary dairy is on course to reduce milking parlour labour by 75% while increasing cow throughput by 75%.
Previously, four parlour operators were required for a four to four-and-a-half-hour milking at 80-90 cows/hour.
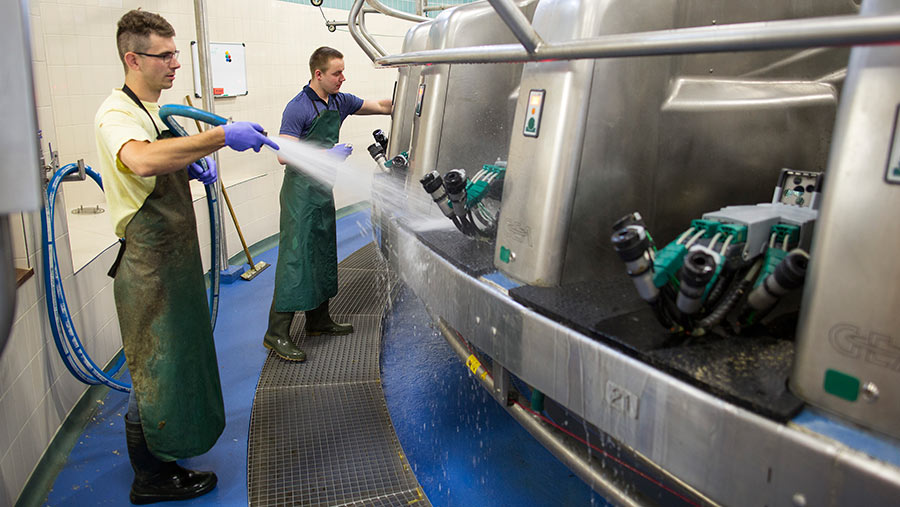
© Geoff Pagotto
Now the same cows will soon be overseen by one person at a rate of 150 cows an hour milked over two-and-a-half to three hours.
Leaving the old herringbone parlour, a cramped and muggy parlour with a sharp 90deg turn for cows entering from the collection yard, and starting with the new system means jobs can be reallocated and holiday can be taken without jeopardising parlour routines.
The future
While 36 robots would typically be enough to milk 1,200 to 1,300 cows, Mr Eavis says the high hourly throughputs will allow for three milkings to be undertaken by one member off staff per shift.
All all three milkings take place in under nine hours of the day, capturing labour savings and allowing staff to be reallocated to different tasks.
It also brings the benefit of being able to expand cow numbers in the future and the freedom to turn off robots that malfunction, allowing an engineer to come in more sociable hours, he adds.
More importantly, the farm can still make the best use of summer grazing, which takes a month break for the Glastonbury festival and then typically extends into late October.
Getting cows to use the new parlour
Normal service is resuming in terms of cell counts and cow behaviour, stresses Mr Taylor. However, he admits getting cows into the units was a challenge.
“The cows are more than happy to use the rotary now but if you’d told use that on the first day I would have laughed,” explains Mr Taylor, who feed a high-energy sugar beet pulp pellet at parlour, which he says helped train the cows.
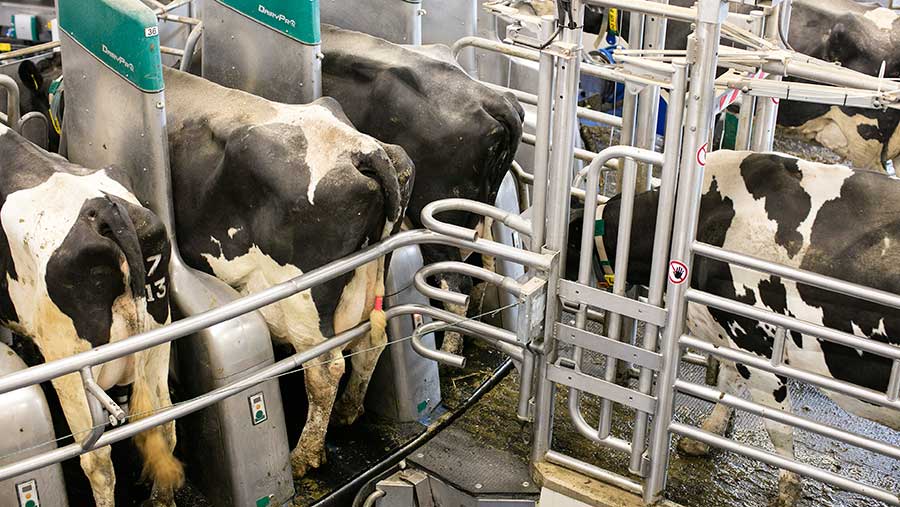
© Geoff Pagotto
“We had to push and persuade cows to go in on the first day.
“It took a little getting used to but there was only one cow that we couldn’t get milked on the first day and on the second morning she walked in by herself.”
The system is only one of its kind using an automated pellet feeder, which delivers a special parlour cake supplying selenised yeast and vitamin E to support the udder cells and protein at 16% and crude fibre at 12.5%.
The rotary parlour in detail
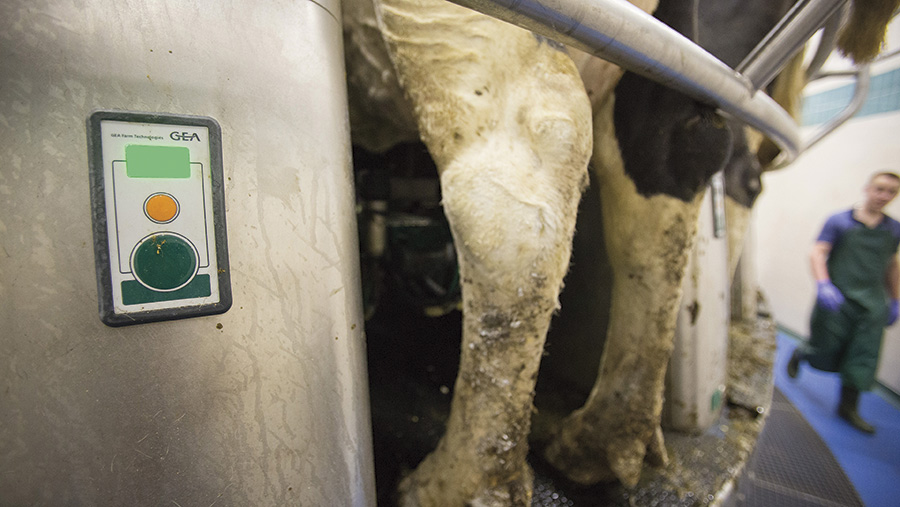
The rotary parlour’s conductivity and colour sensors trigger cow inspections with red lights © Geoff Pagotto
Conductivity and colour sensors
- Triggers farmer to inspect cows with red light
- Report on computer shows an inconsistency (for example, high conductivity, blood in the milk)
- Cows can then be marked for manual milking (for example, currently only five cows at Worthy Farm)
- Red light comes on for a suspect cow and milk is automatically dumped, per quarter or the whole udder when known to be infected.
- If operator is away the cow is segregated for inspection
Clusters
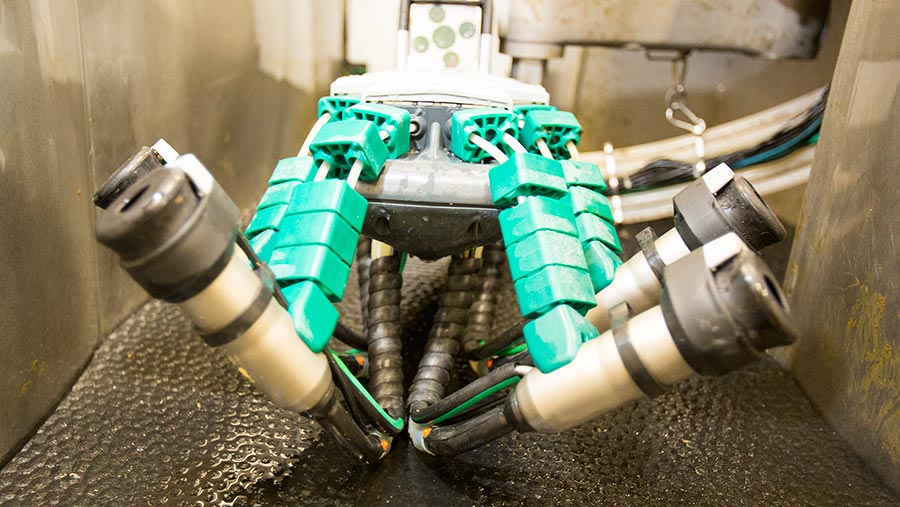
© Geoff Pagotto
- System attaches, pre-dips, cleans, stimulates, foremilks, milks, post-dips and detaches, quarters individually and automatically
- Diverts milk per quarter and reattaches any kick offs immediately at any point
- Flexible fixing on udder allows for cow movement
- Versatile system allow operator to take over with manual attachments
- Udder wash uses water at cow body temperature
- Infrared and 3D camera system guides cluster on to teats
- Camera cleaned automatically after each milking with jet of water and dried with a blast of cold air
- Every cluster can be viewed via camera and wifi on a herdman’s laptop
Viewing panel
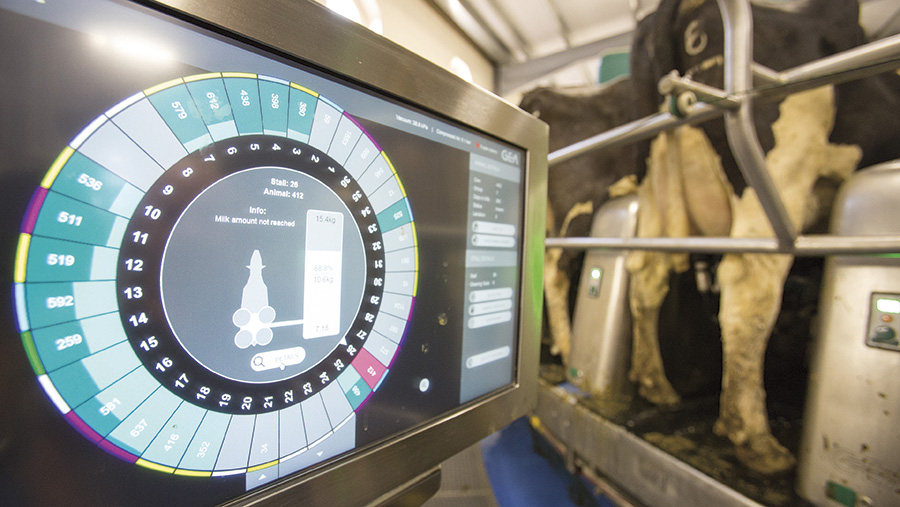
The viewing panel can help in highlighting any problems with milk quality © Geoff Pagotto
- Problems can be identified and units switched off individually or on mass
- Provides animal details, yields, parturition, cow number, cell count
- Flags up milk quality issues by cow and by quarter
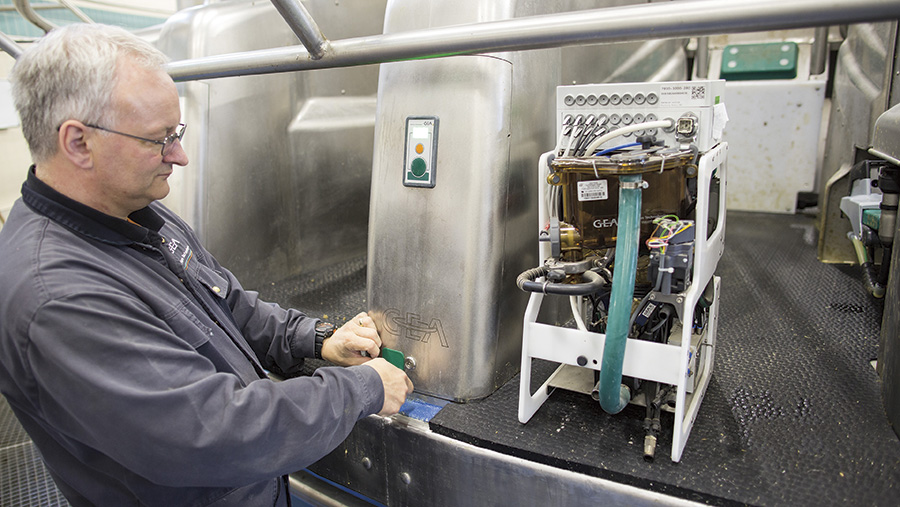
Modules can be taken away from the milking platform for servicing © Geoff Pagotto
Quick service module
- Spare parts service module sits in farm office in case of break down
- Engineer can then work on it in the service room or back at depot – doesn’t need to stay on the platform or indeed the farm
- Unit can have module replaced and carry on working in interim
- Worthy Farm keeping two “substitute” modules.
DairyProQ in numbers
- 36-unit system at Worthy Farm (available in a range of sizes from 28-80).
- One robot per stall ensures the same throughput as a conventional rotary and minimal down time
- 28-unit typically caters for up 1,000 cow herds (80-units equals 3,000)
- Seven minutes average milking time (cow 37 requires 23 minutes)
- Only 11 in use in the world. Eight in Germany, two in Canada and one in Somerset
- Revolves five to six times/hour
Oliver Moore, GEA head of milking and dairy farming sales says: “The DairyProQ really become cost effective for herds of more than 600 cows.
“If you took 600 cows to require 10-12 conventional robots (depending on yield) to milk them three times on average per day the milking investment without building or ancillaries would be similar to a 28 stall DairyProQ.
“However, the 28 stall DairyProQ could milk up to 1,000 cows three times a day, which is at least a 33% increase in milking capacity (number of cow milkings/day) off a similar investment.”