How to reduce pressure on slurry stores and build new ones
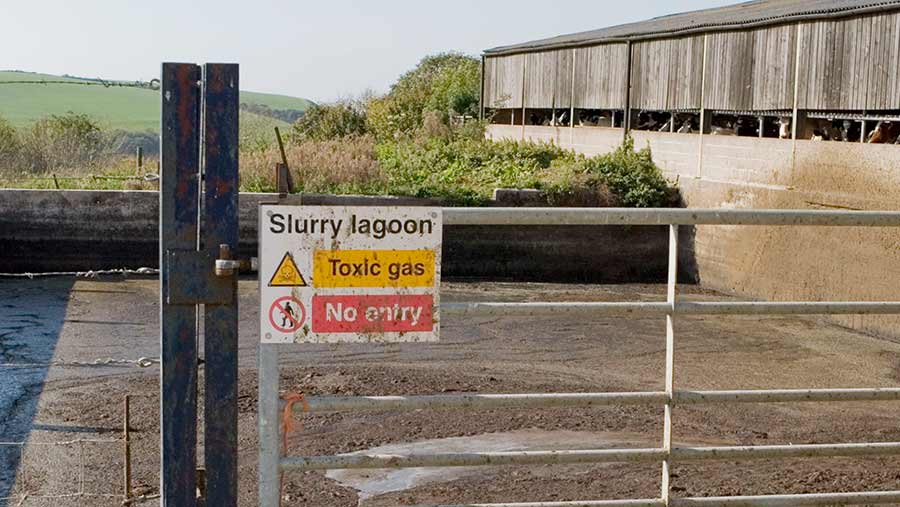
Slurry and manure storage is often a limiting factor when expanding your herd size or housing stock for longer but there are ways to reduce the pressure on existing storage
Options include covering collecting and feeding yards, separating clean and dirty water, roofing silage stores and improving track access for both cows and spreading equipment.
Of course, sometimes a new store is the only answer – and it takes significant planning to get it right, we look at advice on how to go about building one.
See also: New system could reduce slurry volume by 80%
1. Planning a new store – what you need to consider
There are four rules to slurry storage projects, according to Charles Bentley, senior consultant at Adas.
They will take longer than you thought, cost more than expected, are never big enough and when the next generation take over they will be slightly in the wrong place.
So getting the planning right is essential – and that involves looking at the farm as a whole, both now and in the years ahead.
The location, size and type of slurry store will depend on:
- the existing – and future – farm layout
- bedding type
- feed type
- soil type
- dilution
- handling facilities
A flexible option
“A lagoon is the cheapest and most flexible option if you have suitable soils with at least 20% clay content,” explains Mr Bentley.
“But once you have artificial liners and membranes you have to be careful with machinery and equipment.”
Bedding, feed and spreading considerations
Sand bedding is notoriously abrasive and can suit a simple system whereby liquid slurry is spread, leaving the solids to be removed mechanically once the pit is empty.
High starch feeds result in drier manure, while self-feed grass silage diets produce liquid slurry with a floating crust.
“If you’re spreading with an umbilical you’ll need wetter slurry, and therefore potentially more storage capacity,” says Mr Bentley.
Remote storage can be suitable for liquid slurry – pumping or even tankering it off site to where it needs to be used.
You may need to obtain planning permission from your local authority depending on the size and location of the development, so check with your council first.
Anyone building a store or substantially altering or enlarging existing facilities must notify the Environment Agency at least 14 days before starting construction work.
For information on calculating storage capacities visit the government website.
2. Regulations – how much storage you require by law and how to reduce pressure on those requirements
Under the SSAFO and cross-compliance regulations, cattle farmers require four months’ storage under assumed wet conditions.
Those in Nitrate Vulnerable Zones must have five months – but each farm should work out its own most efficient solution.
“Look at your acreage and location of land – in some places you may need nine months’ storage to make most effective use of the nutrients,” says Mr Bentley.
Technically, any water that has been contaminated with faeces, urine or bedding should be treated as slurry. Therefore, farmers should also think hard about where water from collecting yards or parlour-washings ends up.
This is where concreting yards and roofing them really comes into their own (see below).
Not only does roofing and guttering keep clean water out of the slurry tank, it offers the potential for rainwater harvesting and improves the environment for livestock and farmers, alike.
“A cold, wet cow uses more feed for maintenance, and wet silage deteriorates faster. If you have a warm, dry feed area it increases voluntary intakes. You could get 5-10% more performance from your existing silage,” adds Mr Bentley.
The value of roofing and guttering
Assuming 450mm of winter rainfall/800mm annual rainfall, 1sq/m of dirty yard area will cost £0.45-£2.70 a year in extra storage, plus £1.33 in spreading costs (10,000-litre tanker at £50/hr or the equivalent of 10cu m/hr so £50/10 = £5/cu m. Assume three trips/hr = £1.66/cu m x 0.8cu m water = £1.33sq/m yard area) .
Fixing broken guttering also pays back extremely quickly. A 100x80ft shed with the above rainfall will generate over 500cu m of rainwater a year. If one of the four downpipes is missing, and assuming a spreading cost of £1.66/cu m (see above calculation), that equates to £207.50 a year – or £830 if all the downpipes are broken.
Replacing all the steel gutters and downpipes would cost about £25/m – or £1,000+VAT. With grant funding of £11.40/m available, the payback period – on spreading costs alone – drops from two years to just one. When you take into account the cost of storage that could fall to just 13 weeks’ payback.
Without grant funding, roofing will pay back over 15-30 years, but with funding it’s 40% less. If you add in rainwater harvesting and offset the cost of mains water at £2/cu m, it cuts the payback period even further.
Areas to invest in to reduce slurry store pressures
1. Cover slurry and silage stores
Covering slurry and silage stores can also be extremely useful, reducing storage requirements and crop wastage.
“A lot of silage clamps have 20-25% wastage,” says Mr Bentley. They should be designed with a narrow face but the ability to be filled rapidly, can be backfilled with earth to give more support and must have an external effluent channel to collect any waste.
Clamps should have an impermeable base and sides, and the effluent tank needs to be capable of containing 20 litres of effluent/cu m capacity, up to 1,500cu m – or 6.7 litres/cu m above that.
2. Improve grassland tracks
It’s easy to forget about farm tracks when making slurry storage plans – but they are inextricably linked. The longer cattle can be out at grass the less slurry there is to deal with. In addition, better tracks enable muck to be carted for spreading without damaging the fields.
Grant funding
Countryside Productivity Scheme
The RDPE Countryside Productivity Scheme provides funding for projects in England which improve productivity in some sectors, including farming.
The grant comes from the European Agricultural Fund for Rural Development (EAFRD), and details on whether it will continue are yet to be clarified.
For the latest information, see the government website for guidance on the Countryside Productivity Scheme.
Case study: James Yeatman, Sherborne, Dorset
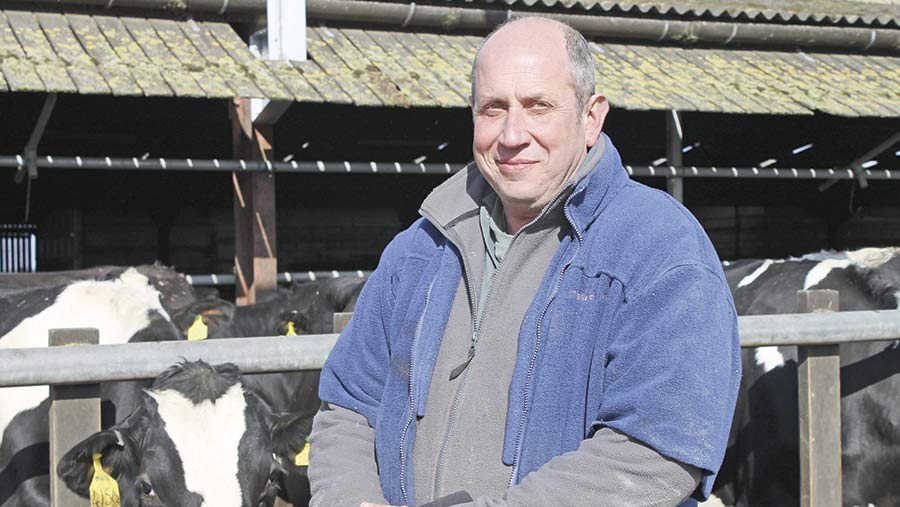
James Yeatman © RBI/Olivia Cooper
James Yeatman milks 340 cows in partnership with his family at the 97ha Grange Farm, Sherborne, Dorset. Block calving in the autumn, the cows average 10,000 litres anually, and are grazed over the summer but housed on sand cubicles in the winter. “We’re on very wet clay so have six or seven months’ storage, and we’re trying to reduce our slurry volumes,” says Mr Yeatman.
He has a simple concrete-floored lagoon system, with the first lagoon fed by a tractor scraper. Gravity then filters the more liquid slurry down to a second and then a third lagoon, where it can be spread using an umbilical or top-filled slurry tanker. “We clear the sand out once a year using a Keenan spreader.”
Being in a Catchment Sensitive Farming area, Mr Yeatman has secured a number of Mid Tier grants – at £62sq/m – to roof over collecting and feed yards. “We have a lot of open concrete on the farm so it’s going to make a big difference,” he says. “Ultimately, we hope to harvest the rainwater, which will help, too.”