How time working off-farm can bring new skills home
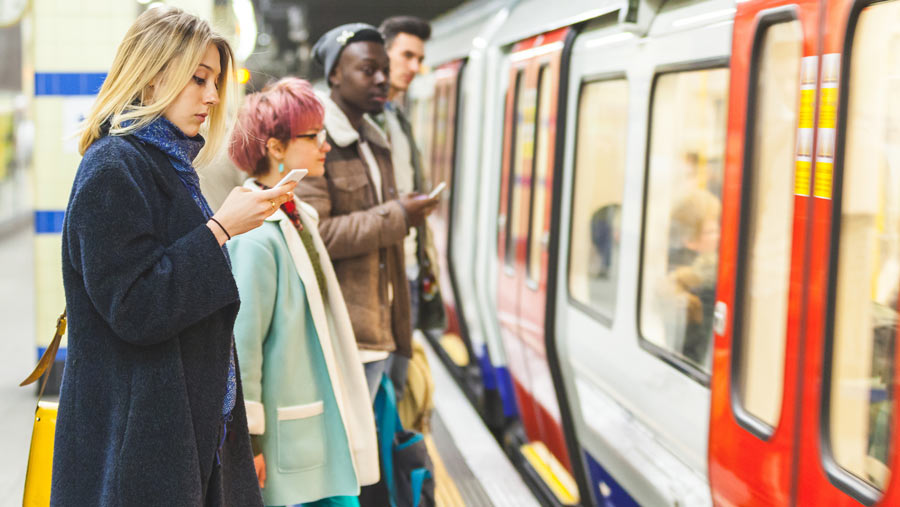
Born-and-bred livestock farmers can benefit hugely from working off-farm before coming home to continue in the business.
Whether it is a job on another farm, within the industry, or outside farming altogether, finding out what it is like to be an employee, learning new ways to do old jobs, or getting fresh business ideas is invaluable.
See also: 7 staff management tips from a dairy farmer
A Farmers Weekly mini-poll showed that 35% of livestock respondents who had worked off the farm did so outside of agriculture before settling at home to farm.
A further 25% had worked on another farm. (Being employed in the industry was selected by 17%, and 23% had worked both in and outside farming.)
Such off-farm experience is a valuable opportunity to see how other businesses operate, and Becky Miles, senior partner at recruitment company Real Success, says it is very positive that 23% have had multiple career experiences to bring back to the farm.
“It bodes well for the future of the livestock sector that we have people returning who have seen and learned from other industries or sectors.
“They will be more likely to have a broader view of what, and how, issues on the home farm could be tackled to improve efficiency and profitability,” she says.
Working on another farm will introduce new ideas and ways of working. “You can learn new skills, use different machinery and techniques, see farming in another region or landscape with the associated challenges or benefits.
“You return home with ideas for the business, experience of how other systems work and a deeper understanding of how you will treat staff in the future.”
Working as an employee
But regardless of job role, being treated as an employee means being expected to be self-starting and motivated, adds Becky.
Although she says that the benefits as an employee will be approved rates of pay, regular time off and employee rights, it can also mean learning to deal with difficult co-workers.
It might also include using poorly maintained kit or being given jobs no one else wants to do.
“You will have your lunch in the staff room with other employees – not in the farmhouse – so will learn to see things from their perspective.
“[Particularly on a farm] is there an operational toilet with handwashing facilities? Is the staff room warm, with table and chairs? Can you dry your wet clothes? Are work clothes provided?” says Becky.
What also applies to all jobs is whether everything about the position has been clearly explained – and who to report to if things are not clear, or there is a problem, she says.
“Perhaps your employer won’t be the best people manager, but from this experience you will be a better people manager when your time comes, as you will understand how it feels to be the employee.”
Case studies
Jake Norton, Church Farm, Norwich, Norfolk
Jake Norton runs 60 Brown Swiss cows on one robot, averaging 10,000 litres. He is expanding to 120 cows, swapping the robot for a 10/20 swingover parlour.
After agricultural college, Jake worked on two other dairy farms for more than two years.
“You learn different ways of doing things and a different point of view,” he says. “Being an employee, you learn what it’s like to be on the other side and understand what it’s like in their shoes.
“There is a different set of regulations being an employee, you have regular time off and are better paid than at home.
He says the experience gave him the confidence to push forward with expansion plans.
He changed the farm’s handling practice, introduced different mastitis treatments and started doing more tasks in house, such as foot trimming and inseminating, that he had learned on the other farms.
“I’ve also learned not to do stuff that we are not specialists at. I don’t enjoy arable work and have taken someone on to do it; I want to focus on cows and grass.
“It’s good to go out of your comfort zone into a different part of the country where no-one knows you – not a friend’s or relative’s farm – and you can create your own stamp.”
Joe Adams, Gulpher Farm, Felixstowe, Suffolk
Joe Adams is milking 150 Holstein Friesians averaging 10,500kg and will be installing three robotic milkers and new cow accommodation in 2024.
He worked for a nutrition company as part of his university placement and for a year after graduating.
“Dad always had the opinion I should go off and do something else,” he says.
“Working for a nutrition company definitely helped on the technical side and seeing other farms.
“I learned about nutrition and cow management, and I did a lot of work on adapting old sheds and calculating feed trough and cow spaces.
“There were lots of technical facts I wouldn’t have picked up had I just worked at home.”
Joe says he benefited from seeing more varied dairying systems, breeds, grazing and robots.
He also learned how to analyse data such as milk recording, fat and protein ratios, and drawing up cull cow lists. “Because I didn’t know people, I went on farm as me,” he adds.
He thinks there are further skills he could have learned off-farm to benefit the business:
“I would love to have had a few years working with specialist builders on livestock buildings to learn modern products and techniques, such as concreting, slatted floors, cow spacing and getting the fall right.”