How lean management saved pig business £50k
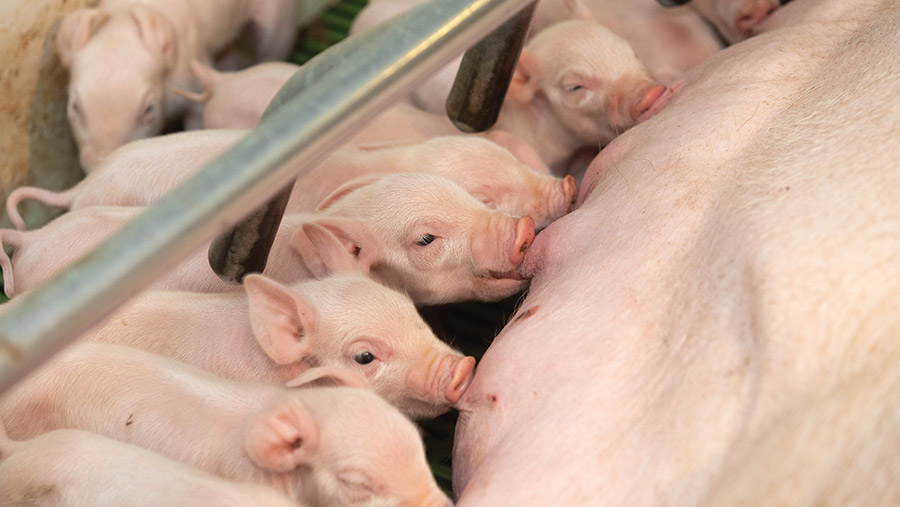
A farrow-to-finish pig business in East Yorkshire has improved pig performance and staff retention by making changes using lean management techniques.
This has meant less time spent on tasks and £50,500 of savings identified during the first year, with one-off investment costs totalling £15,000, mainly for new feeders.
See also: Pig farms making small changes see savings of £250k/year
Field team manager James Turner learned about lean management through AHDB’s SmartPork programme.
A “waste walk process” gave the team a structure to follow to help identify efficiencies on the two 1,500-sow breeding units and associated finishing units.
Benefits often come from many small marginal gains that can be made when a team maps out every detail of a farm’s routines and identifies waste areas for improvement.
“It is now an ongoing cycle for us. While we can’t change everything at once, the most important thing is stopping to look and recognising where the issues are,” says James. “Then we can prioritise what to do first.”
It is crucial to get middle managers or stockpeople together to do the waste walk and come up with ideas to improve things, he adds.
“They’re the people on the ground and it gives them a sense of responsibility; staff also feel they have been heard when they suggest changes and see them acted on.
“Overall, we have much clearer routines since we started lean management – we feel more on top of things, the team seems happier and more close-knit and staff turnover is lower.”
Labour savings amount to £20,000/year, with the rest of the savings attributed to lower maintenance, breakdown and repair costs, feed and vet costs.
James shares some examples of how they made the improvements, saving time and money.
1. Tools and maintenance
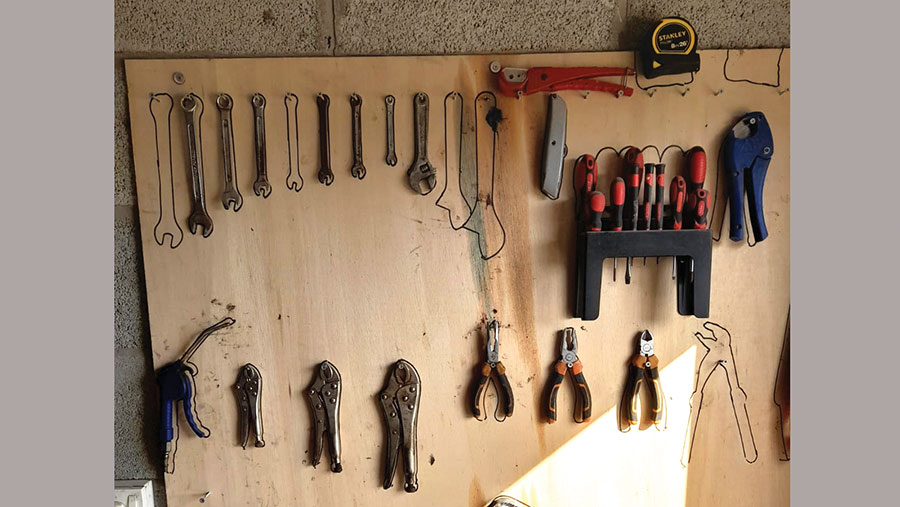
A simple shadow board means tools are available for small maintenance jobs © James Turner
Waste identified
- Keeping track of tools and getting maintenance jobs done was wasting a lot of time and feed. For example, if a feeder needed tightening up but there was no spanner available, either time would be wasted finding one, or it would not be fixed that day.
- The larger units with five or more team members now have a shadow board. This stores a general maintenance kit, and whenever someone takes a tool, they put their name in its place.
- The business has introduced “tidy Fridays” so that time is allocated every week to double-check or do any outstanding maintenance tasks. Anything left over, plus larger tasks, are allocated to the company’s maintenance person.
Saving
- Each member of staff is taking less time to get more maintenance done, and less feed is being wasted.
2. Feeding routine
Waste identified
- Sow-feeding routines on the farm’s breeding units were taking three to four hours every morning, using buckets and barrows. This lengthy and manual task was also affecting team morale.
- For the short term, two members of staff now share the feeding in the morning.
Saving
- Feeding is now completed in two hours or less, with team members feeling less worn down and benefiting from someone else’s company. Investment in new feed lines is planned, which will result in bigger labour savings.
3. Communication and planning
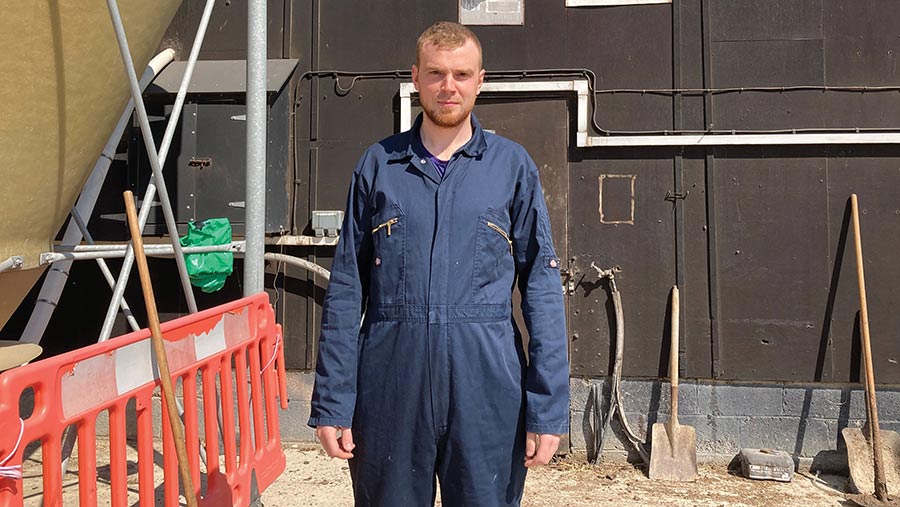
Field team manager James Turner © James Turner
Waste identified
- Keeping each other up to date on the breeding units and planning the day’s work used to be more ad hoc and time would regularly be wasted. For example, staff would not always know in advance what time they were needed to move gilts into farrowing pens. As a result, pressure-washing equipment might not have been tidied away beforehand and not everyone would be ready to start on time.
- Breeding unit teams have introduced a five-minute briefing each morning to prioritise and plan the day, so everyone knows what to do and when.
- Workload planning and resource management has been made more efficient by simple use of whiteboards, with a shared “to do” list. Staff members can tick off tasks when they are complete.
- The team of 12 fieldspeople now aim to meet at least once a month to discuss all aspects of their work and learn from shared challenges and ideas across the units.
Saving
- The briefings, meetings and boards have helped ensure that all team members are better informed, that more tasks are completed in a timely way and ideas for improvement are shared.
4. Keeping tidy
Waste identified
- A lot of straw is used for bedding, and bale strings used to be left hung over pen walls. This meant one day each month was then spent collecting them up. String could easily end up in the muck heap and sometimes caused muckspreader breakdowns.
- The team’s solution was to provide a barrel for each shed to put string straight into.
Saving
- The yards are now tidier, string is handled only once and collecting the full barrels is a much quicker job. There is also a far lower risk of additional hourly muckspreader costs – about £60/hour – while a breakdown is fixed.
5. Moving and handling pigs
Waste identified
- Extra people were needed to stand in gaps when moving pigs, and the task was taking a long time as pigs did not always move easily.
- Longer pig-herding boards were bought, which can be wheeled along and left in position to fill a gap.
Saving
- Pigs move more easily with a solid barrier in the gaps and a clearer way ahead, so moving now takes one to one-and-a-half hours, half the time if took before. The extra people are freed up to do other tasks.
6. Small pig management
Waste identified
- Smaller piglets, whose performance fell behind at weaning, also seemed to have more problems during rearing and finishing, such as poorer feed conversion ratio or a need for veterinary treatment.
- James set up a trial to investigate this, tagging the smallest 40 pigs from two batches of 1,000 pigs and recording their performance and mortality through to finishing. The results showed that more than 50% of pigs that died in each batch were from the tagged groups of piglets.
- The aim was to improve average weaning weights and lessen variability in weight, to give piglets a strong start post-weaning. His trial data gave them the evidence to guide management changes, including trying different creep diets and weaning the smallest pigs at five weeks old instead of four.
- Progress is ongoing, with weaning weights now averaging 8kg, up from 6kg, but there is still work to be done to reduce variation in weight across the batch to reduce numbers of small pigs further, he says.
- When store pigs are moved into the finishing stage at 40kg, all the smaller pigs are put together in four or five pens of 20 pigs, so it is easier to give them extra attention.
- If a different ration or medication is needed for these smaller “focus” pigs, it can be given manually, and only to those that need it.
Saving
- By feeding a higher-protein ration to 100 pigs, rather than all 1,000, feed savings are significant, and it takes less time each day to check all pigs thoroughly.