What’s in your livestock shed? Sushi-style feeding and GPS trackers
Farm technology guru Tim Gibson had to rely on his command of dairy gadgets when he increased his 200-cow herd to over 300 head in just three weeks.
Hunters Hill Farm, Bedale, underwent a raft of changes upon welcoming the Brymor herd’s 85 Guernsey cows and youngstock in March 2015.
This saw the flying herd of mostly Holstein-Friesian cows remodelled in under a month, meaning buildings were reconfigured and a Lely robot acquired at short notice to allow a smooth transition on the robotically milked operation.
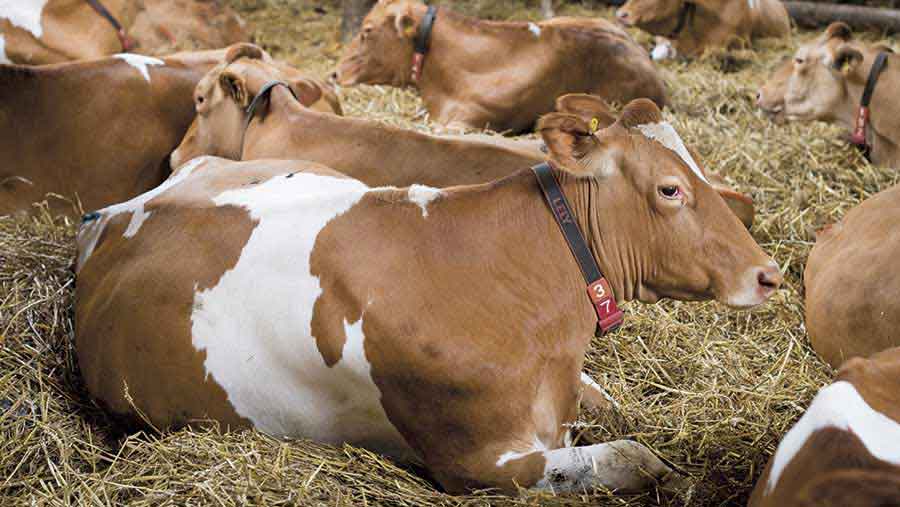
© Jim Varney
See also: A look at an £825k sheep shed
Building configuration
In order to carry on the great Brymor ice cream brand and product provenance, Mr Gibson negotiated a share farming agreement in a week.
The agreement means the Brymor cows are now milked on a “bed and breakfast” agreement and the same high constituent milk is transported back to the Brymor parlour as before. This means one of North Yorkshire’s finest dairy products remains intact.
“There were a lot changes to make in 27 days,” admits Mr Gibson, who houses cows inside and grazes dry cows on pasture through the summer.
“We needed to review the slurry channel and storage to suit the new group of cows and we had to turn the dry cow shed into a cubicle shed as well as put a feed system in.”
What has been your latest purchase?
Most recently we have started trialling barn location and rumination ear tags on the Guernsey herd, with excellent results so far.
SmartBow tags cost £129 apiece, but they’ll have paid for themselves in a year just by saving time looking for cows.
There’s a GPS tracker for every cow, letting us know where the cow is inside and outside powered by a simple watch battery that lasts three to four years.
Cow location then pops up on the herdsman’s iPhone. The system communicates from the cow’s ear to 10 Wallpoints – square boxes with two antennae on the top, which weigh 620g, and typically work with an indoor range of 30m.
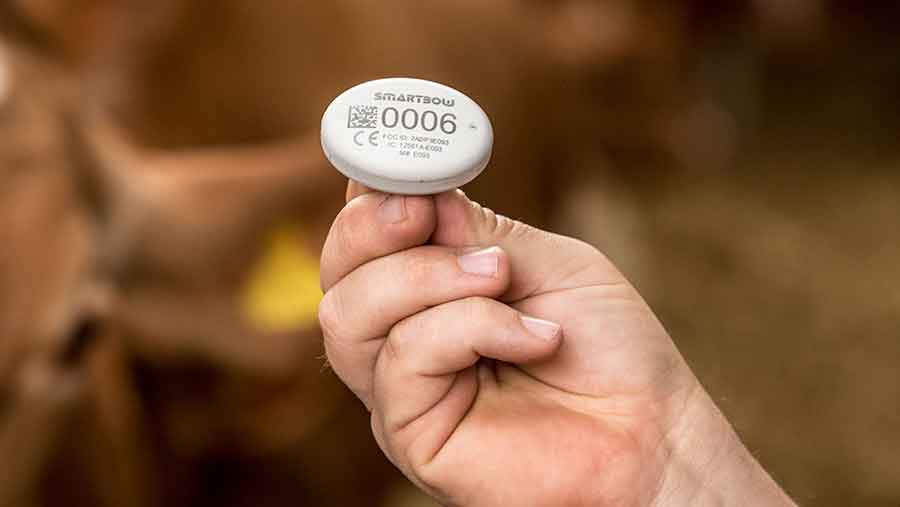
© Jim Varney
We’ve done trials on other systems like heat time, and various cow activity monitors to compare SmartBow. Now we are happy it’s working, we are tagging all the cows and we have all the tags in a box ready to go.
What’s been your best bargain?
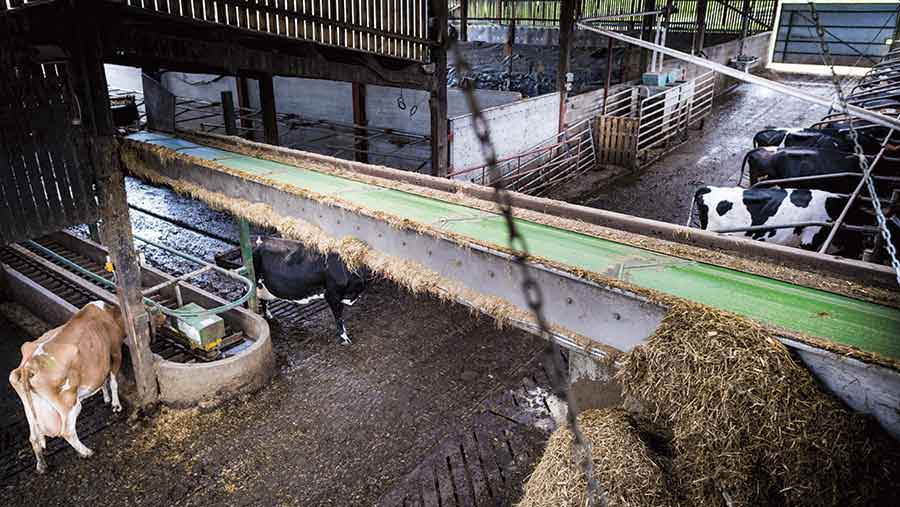
© Jim Varney
There’s been a few over the years, but the biggest money saver has probably been stainless steel conveyors I bought from eBay for £4,000.
They were second-hand from a packer supplying supermarkets and were a bargain because I had the job priced at £45,000.
They have allowed me to adapt the feeding system to accommodate the extra cows.
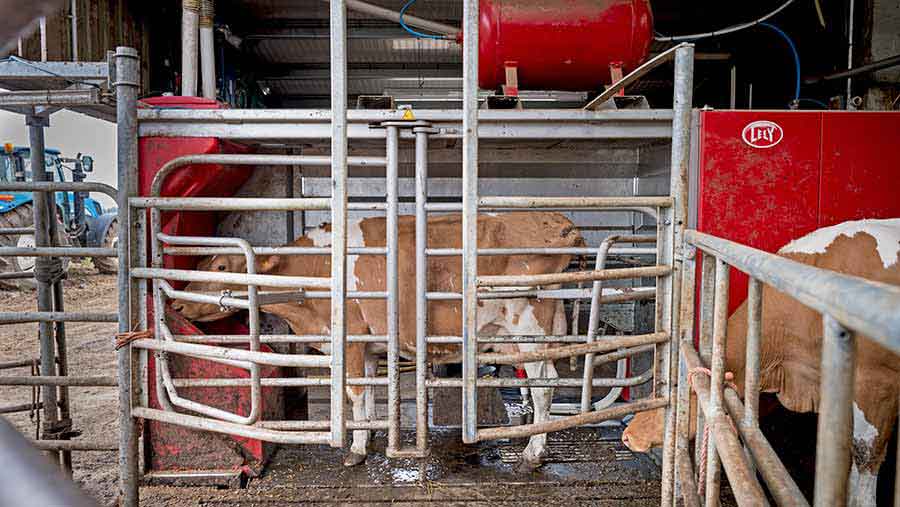
© Jim Varney
Another great buy that was key to the dairy expansion was a second-hand robot I bought for £45,000 and it came with a bulk tank. I couldn’t have bought a new robot [for that] and fitted it within a fortnight.
What’s been the biggest management change at Hunters Hill recently?
Without doubt that would have been the decision to incorporate the Brymor herd. We currently have the unit and overheads to run 300 cows, but we are down to around 250.
Farm facts
- Flying herd of 200 Holstein-Friesian cows, including dry cows
- Contract farming 85 Guernseys for Brymor ice cream
- Arable operation historically providing wheat, barley and maize as feed
- Beans added this year for Greening measures
- Supplying milk to Payne’s Dairies
- Two herds grouped separately
- Robotic milking: three Lely A2s and one Lely A3
- Two full-time staff and an assistance student
I took the decision to stop buying cows for the flying herd with the way milk prices went. I’ve bought a few recently but we will see where things head.
The Guernseys arrived in March 2015 and we started milking on 1 April, meaning we were after milk quota termination.
What’s next on your wish list?
A three cubic metre distribution bucket to feed specialist rations incorporating more straw for smaller groups of cows.
This will be fed on a Kramer 680T telehandler and is from Dutch manufacturer Sieplo.
It is not practical to feed a separate mix in the 24cu m static mixer for 20 or so dry cows or small groups like the maternity group or close-up cows – it’s like using a sledgehammer to crack a nut.
We feed a quarter rate of TMR and then add straw through the auger. This has the benefits of being simple for us and simple for the cows as they can get their rumens tuned into the TMR.
What kit couldn’t you live with?
A computer system called Uniform-Agri that links the Lely robots and the Trioliet automated feeding system. It controls everything from BCMS to the medicine book, passport applications and movements.
If a cow calves it applies for the calf’s passport and adds that cow into the milking group and puts it on a fresh cow diet.
It tells the Lely robot all of this and cows are milked with four days of colostrum discarded automatically.
What would you do differently?
We would have budgeted on the cows not doing as well in the first year. We underestimated the effect of moving them in terms of how much milk they dropped and should have looked closer at the herd, in particular the number of days in lactation and the number in calf, as there were not that many calving in the first six months.
What’s your best invention?
Probably the automated feeder system I have adapted for our 1960s/70s farm buildings. This uses conveyor belts and floorscrapers to transfer TMR from the Trioliet static feeder on to a sushi bar-style feed bunk.
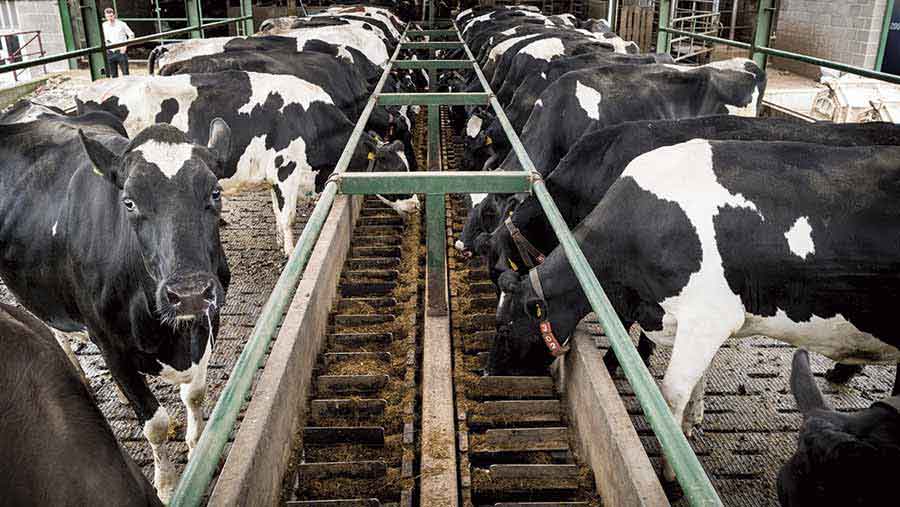
© Jim Varney
I’d looked around for something similar in the Netherlands but nothing was available in the UK. The belts go every two to three hours and feed the milk herd in the cubicle shed through the day.
We just added a new Trioliet mixer six months ago, which runs off 100 litres of diesel/week on a three-phase generator.
We couldn’t get in the shed with a mixer wagon and as we expanded cow numbers room got even tighter. This forced me into using a series of feed conveyor belts to take TMR around the building.