Simple steps to improve energy efficiency on poultry farms
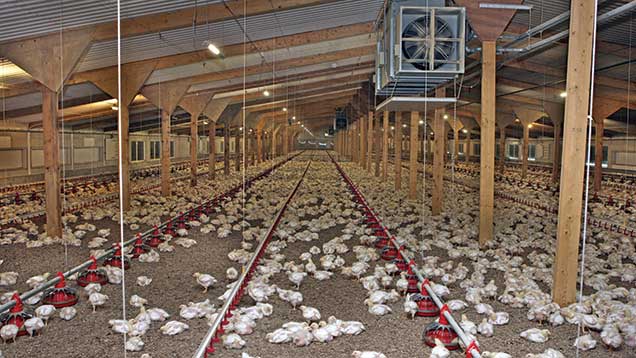
The large energy requirement for heating, ventilation, lighting and feeding in poultry units means simple energy efficiency measures can yield significant savings, especially in older buildings.
The first step in understanding and improving energy efficiency requires knowing how much is used, where and when, advises independent consultant Stephen Raasch.
This can be done at a basic level by regularly recording utility meter readings, or fitting advanced data logging equipment. This information allows energy consumption patterns to be identified and performance to be benchmarked.
See also: Farm Energy articles from Farmers Weekly
A standard 240 x 60ft, 27,000-bird broiler house (without renewable energy installed), on average consumes 36-40,000 litres of LPG a year and 35,000kWh of electricity, Mr Raasch says.
“Once you know the consumption, you can identify ways to reduce it.
“Many measures are fairly simple, yet have a considerable payback.
“Pay attention to detail and make energy efficiency part of routine procedure at every cycle prior to bird placement.”
Control airflow
Insulating buildings and reducing air leakage by sealing gaps in walls, around doors, windows, louvres or fans are priorities, says the Farm Energy Centre’s Andrew Kneeshaw.
“Poultry buildings are designed to be ventilated, but you must have control over airflow, especially in winter.”
Mr Raasch adds: “A lot of houses work on negative pressure, so a good way to test for leaks is to close all vents and switch fans on to see what pressure you get. If 20-30 Pascal cannot be reached in a standard house with four fans, there’s likely to be serious leakage.”
Improving insulation keeps heat in and reduces “solar gain” in the summer, helping to keep the inside cool, reducing energy requirements for heating and ventilation.
About 400mm of insulation is recommended, which is double previous standards, notes Mr Raasch. “Adding insulation can be difficult in older houses, but it’s a relatively easy and cheap additional build cost for new units.”
Mr Kneeshaw reckons many existing poultry units fall well below that, with 100mm (4in) or less of insulation typical, despite young birds often being kept at 30C, 24hrs a day.
Payback from sealing buildings can be less than a year, while adding insulation is nearer seven to eight years, he notes.
Indirect benefits
Indirect heating systems where the boiler is located in an annex adjacent to the poultry building and transfers heat via a radiator system within the house are more efficient than direct acting systems, says Mr Raasch.
While costly to install, new systems typically offer 93% efficiency, compared with 60% from older box heaters, and are likely to retain efficiency better by not being within the poultry house, he says.
The “dry heat” also means less ventilation is needed for removing gases and water vapour, and there are bird health benefits too, he notes.
Biomass boilers have found favour with poultry producers since the introduction of the RHI and still offer a relatively short payback of 4-5 years, says Mr Kneeshaw.
Key energy efficiency measures
Ventilation
- Match duct and fan sizes to the ventilation system
- Regularly clean and maintain fans, ducts and louvres to improve airflow
- Replace old fans with energy-efficient models – a fan consumes its own value in energy in about 18 months. Belt-driven fans use less (about one-third) energy than direct-drive units
- Use recirculation fans (cost about £300) to improve heat distribution (especially for direct acting heating systems) – heating fuel saving likely. Link to first-stage fans to maintain normal airflow
- Seal gaps around doors, walls, windows and ventilation louvres to reduce air leakage – increases static pressure and improves ventilation efficiency and natural air mixing
- Fit proprietary “bell-mouths” to fans or “cones” to outlet fans to increase aerodynamic efficiency by typically 10%
Heating
- Position thermostats carefully to avoid overheating buildings (avoid draughts/doors)
- Insulate roof, floor and walls (insulate concrete mass walls to the ground)
- Link heating and ventilation systems
- Use heat recovery to pre-heat incoming air with warm extract air – heat energy savings of 10-25% are achievable
- Service boilers regularly – clean heat transfer surfaces
- Replace ageing boilers with energy-efficient models or renewable energy systems (or example biomass boiler, ground/air-source heat pump, solar thermal)
- Consider radiant heaters to directly heat floor area and minimise general air temperature rise
- Restrict chicks to smaller areas with zonal control/brooding curtains –ensure a tight seal
Lighting
- Reduce lighting (within regulations) – current minimum is 20 lux over at least 75% of floor
- Replace old incandescent and tungsten halogen lights with energy-efficient fluorescent systems inside and high pressure sodium or metal halide lamps outside
- Consider LEDs – modern LEDs are dimmable and fit existing sockets. Cost is higher than standard bulbs (£9/bulb versus £0.25-0.30), but lifespan is longer (50,000hrs v 1,000hrs) and use less energy (8W) to produce twice as much light
- Use photoelectric sensors to control lighting in buildings with windows.
Other
- Use multiple electronic sensors at bird height to improve ventilation and heating accuracy –consider systems that record temperature/ventilation data to aid management
- Inverters (variable speed drive) to speed up or slow down fans as required (rather than just on or off)
- Commission an energy audit