Pros and cons of 5 dairy calf housing options
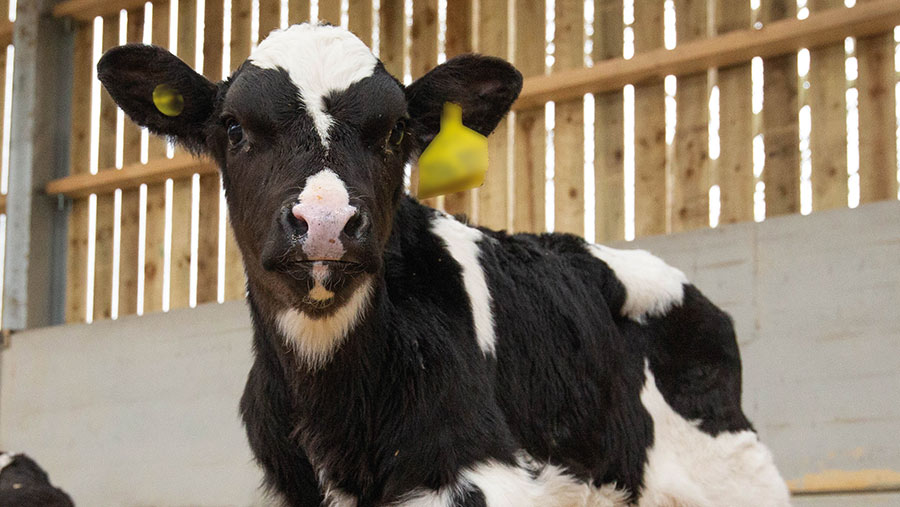
Numerous calf housing options are available and it can be difficult to decide which would suit your farm.
Farmers Weekly asked five farmers to set out the pros and cons of their systems to help you decide.Â
The systems are:
- Calf igloos
- Polytunnels
- New build
- Individual hutches
- Renovation
See also:Â WIYLS: Calf polytunnels enable switch to block-calving
Calf igloos
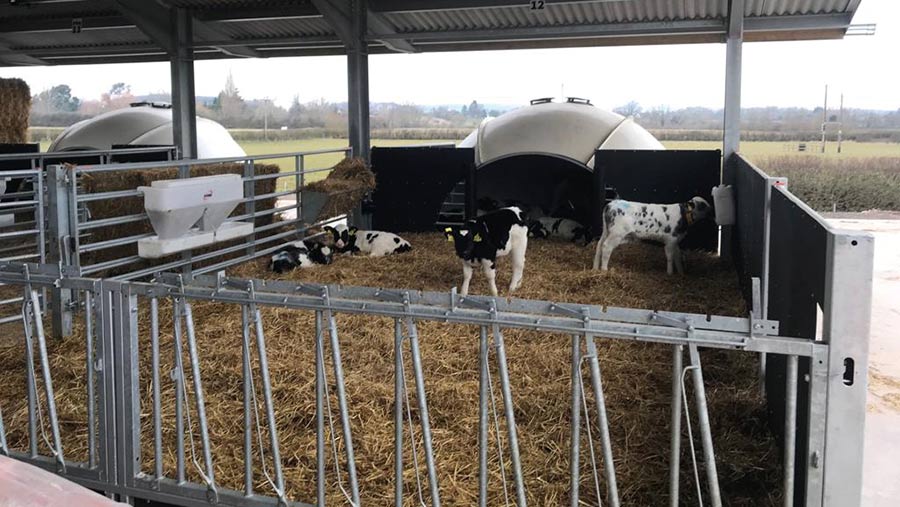
Cobblers Farm calf housing © Rob Collins
After two years of researching systems, Rob and Hannah Collins decided that domed, fibreglass igloos were the obvious choice for their new calf-rearing business.
With only a small existing shed on the greenfield site, the Collinses were keen to put up permanent structures and maximise calf health and performance.
“We were not driven by cost, but performance,” says Mr Collins.
They now have two calf-rearing buildings and a weaning building, each on a concrete base.
Farm facts: Rob and Hannah Collins, Cobblers Farm, Worcester
- 17ha (42 acres)
- 1,100-1,200 dairy-cross British Blue calves reared annually on a Meadow Quality contract
- Animals arrive at 65kg and are taken through to 130-140kg
- Unit is run alongside several agriculture-related businesses
Each rearing system has four pens, with one igloo and 15 calves, together with an automated milk machine stall. Each pen has locking head yokes.
The buildings are open with 3m height to the eaves. Calves can shelter in the igloos, which are positioned around the edge, or go into a pen at the front. The weaned shed is 4m to the eaves, with two igloos for 30 calves.
Since 2018, the unit has had an average mortality rate of 0.5%. Mr Collins puts this down to the environment in the igloos, feeding and good husbandry.
Pros and cons
âś… Good ventilation – testing has shown the air changes every 15 minutes in the igloos
âś… The igloos can be moved, and it’s also possible to get moveable “verandas”
âś… Easy to clean – can be picked up with the loader and power-washed
❌ In windy or cold conditions, straw bales may be needed for protection
Top tips
- Seek advice on appropriate planning and building design
- Siting is important – consider the direction of the prevailing wind. Ideally, it should hit the corner of the shed
- Provide a gap the width of a shed between buildings, so there is no shared air
Cost
In 2018, one 60-calf unit, including planning, the shed, build, concrete base, igloos, metalwork and milking machine cost ÂŁ100,000.
With rising costs, Mr Collins admits if he did it now, he would question spending the same. Instead, he would look at building a less permanent structure for the igloos himself, which would be cheaper.
Polytunnels
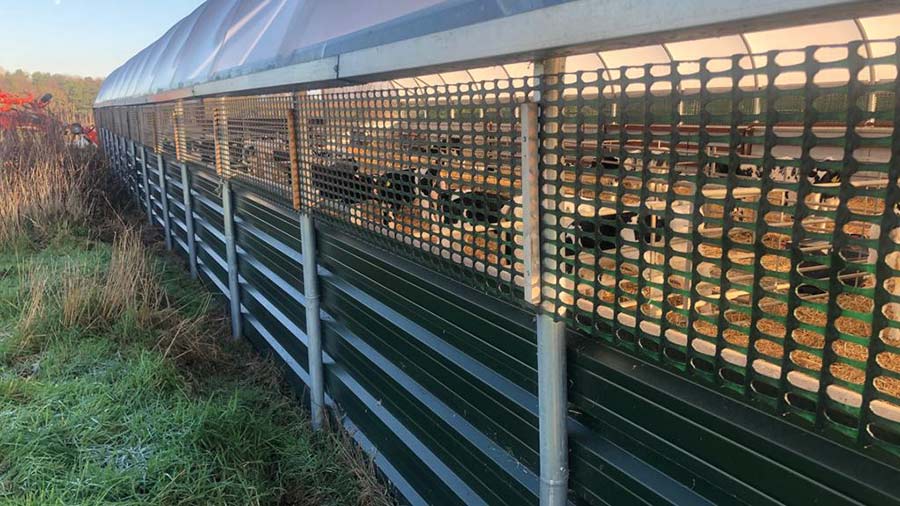
Lower Shadymoor Farm calf housing © Michael Oakley
When Michael Oakley decided to make better use of an existing shed housing youngstock and convert it to dry cow cubicles, polytunnels proved a cost-effective alternative for calf rearing.
Mr Oakley and his son, Miles, now have three polytunnels on a hardcore base, with plans in place for a fourth.
Farm facts: Michael Oakley, Lower Shadymoor Farm, Shrewsbury, Shropshire
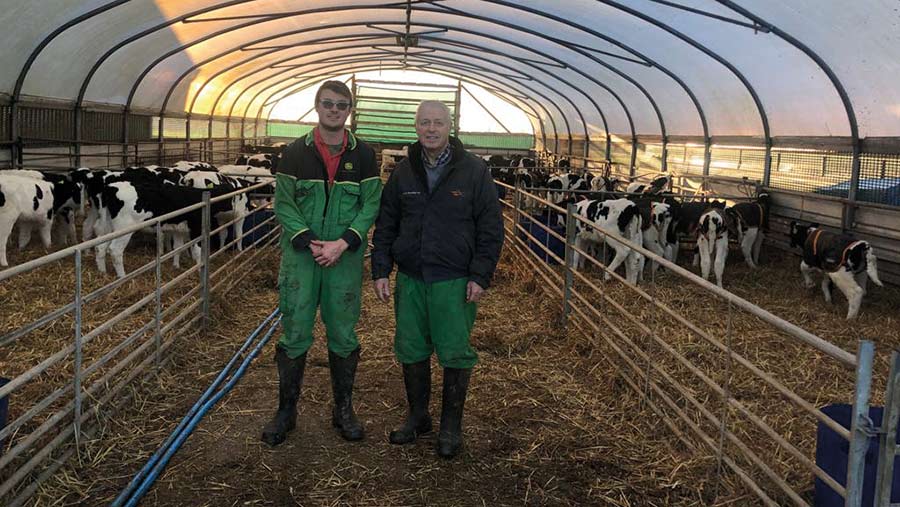
Miles and Michael Oakley © Michael Oakley
- 567ha (1,400 acres)
- 1,500 cows housed year round
- 11,000 litres a cow a year at 4% fat and 3.2% protein
- Recently started to rear replacements
- Aim for 40-50 heifers a month, rest served to British Blue
Each polytunnel is 25x9m and includes seven pens of nine to 10 calves. There is 1m of sheeted tin along the side, and 0.5m of mesh with 3.8cm holes above it.
Guttering is above this, and then clear plastic sheeting over hoops, which makes the roof. Two air vents provide an air outlet.
Mr Oakley says: “There’s never any smell or stale air, as you have the mesh right around the polytunnel.” The farm has a pneumonia rate of 2% to weaning and a mortality rate of 1%.
Pros and cons
âś… Low capital investment
âś… Classed as a temporary structure
âś… Quick to put up – took four to five days to erect on a prepared site
❌ May be limited to 9m width
❌ Can get warm in the summer, even with the sheeted gates open
Top tips
- The base needs to be higher than the surrounding area to prevent water entering
- Space the tunnels about 4m apart
- Cleaning would be easier if the polytunnels were on a concrete floor, but this would add an estimated ÂŁ6,000 for each tunnel
Cost
ÂŁ7,000 for each polytunnel, stone base and drainage, plus about ÂŁ1,000 for electricity and water. With 70 calves in each polytunnel, this equates to ÂŁ114 a calf.
New build
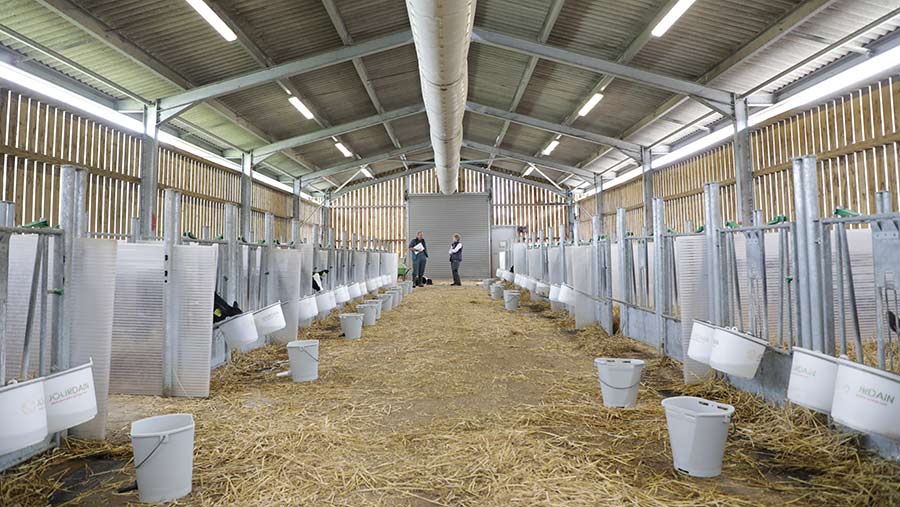
Batsons Farm calf shed © AHDB
When Robert and Bryony Symms and their son, Jake, started to run out of space for hutches, they decided to invest in a calf shed to meet their requirements.
A farm assurance inspection had raised the fact calves were unable to touch each other in single hutches.
There was also not enough space to add on the additional number of hutches needed. As a result, the Symms family decided to build a 29×9.6m shed for 40 calves.
Farm facts: The Symms family, Batsons Farm, Sherborne, Dorset
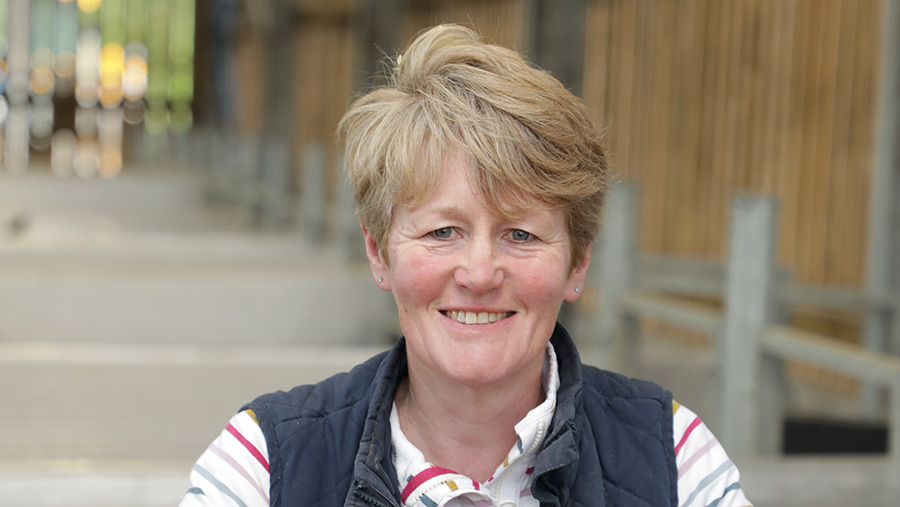
Bryony Symms © AHDB
- 182ha (450 acres)
- 220 housed Holsteins calving year round
- 11,000 litres a cow a year at 4.1% fat and 3.23% protein
- Muller Co-op contract
- Calves reared to 12 weeks before going to a contract-rearer
Key attributes of the shed include:
- Plastic dividing board between each pen helps prevent disease spread. This can be slid out to change pen size
- Concrete walls up to about 0.9m, with spaced weather boarding above
- Raised ridge
- Locking head yokes
- Pen floors and the central passage have a 5% slope to the drains in front of the pens
- Stock board at back of pens with a gap between that and the outer wall to provide insulating air gap
- Positive pressure tube ventilation (PPTV)
- No milk preparation done in shed – mixed in dairy 20m away and moved on trolley to avoid water being introduced to building.
Pros and cons
âś… The building meets the Symms family’s requirements
âś… Concrete floor means the shed is easy to clean and disinfect
âś… Drier environment for calves and people compared with uncovered hutchesm, so less bedding is used
❌ Bryony Symms believes pneumonia is harder to manage in a building than in hutches, where it’s easier to stop disease from spreading as calves aren’t housed together
❌ The shed doesn’t have curtains. Mrs Symms says curtains would be useful when it gets hot
Top tips
- Use a third party that understands the planning process to put in an application
- Get a professional to design the shed
- Use someone who has undertaken the Wisconsin University PPTV course so that the ventilation system is set up correctly
Cost
ÂŁ90,000, including the building, pens, PPTV and electrics
Individual hutches
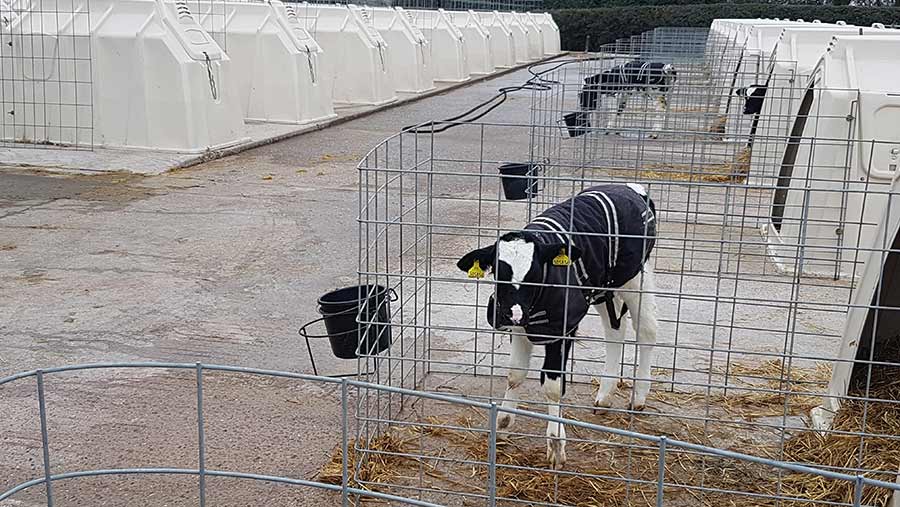
Rushey Field Farm calf housing © Paul Butland
Neville Kirkham has housed calves in individual hutches for the first three weeks of life for the past 20 years and sees it as the best way to manage baby calves.
Hutches are rectangular, plastic houses. Small hutches can house individual calves or larger hutches are available for those preferring to keep calves in pairs or groups.
Farm facts: Neville Kirkham, Rushey Field Farm, Woodhouse, Leicestershire
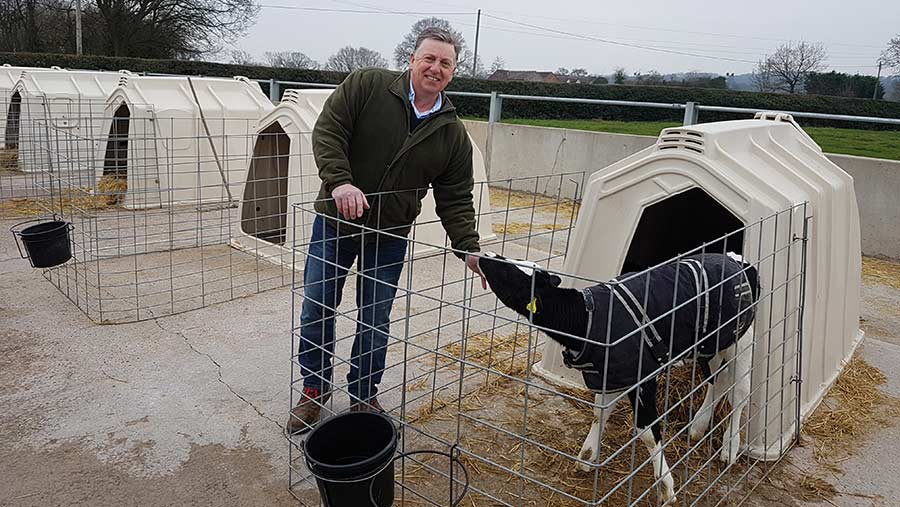
Neville Kirkham © Paul Butland
- 413ha (1,020 acres) farmed – grass and cereals
- 300 Holstein-Friesians
- 9,000 litres a cow a year at 4.3% fat and 3.41% protein, supplying Arla
- Graze in summer
- Rear replacements and finish all beef
At Rushey Field Farm, individual hutches are positioned in four rows on a concrete pad. Each hutch has its own outside pen.
Mr Kirkham thinks the setup provides the best of both worlds. “I believe it must be a natural environment, where the calf can decide where it needs to be – indoors or outdoors.”
Mr Kirkham says keeping calves separate also helps prevent disease spread and ensures calves are strong enough before they move into groups of 10 in a mono-pitch building.
He says few calves suffer with pneumonia.
Pros and cons
âś…Â The calf has a choice whether to be inside or out
âś… If a calf is sick, it is contained in one area
❌ Individual hutches may mean more time is required for feeding and cleaning
❌ More space is needed than for a conventional shed
❌ Individual hutches are unsuitable for some milk contracts, which stipulate calves are kept in pairs throughout. Red Tractor assurance says calves over eight weeks old should be housed in groups of two or more
Top tips
- Hutches should be east facing to avoid wind and rain blowing in
- It is worth investing in a concrete standing for ease of cleaning – Mr Kirkham initially had a hardcore base, but struggled with cryptosporidiosis. Investing in a concrete base has reduced the challenge
- Place hutches on a camber so contamination runs away and not into other units
- Use calf jackets when temperatures drop below 15C
Cost
ÂŁ220-ÂŁ230/hutch, plus ÂŁ20,000 for the concrete base for 52 hutches (2015). Total: ÂŁ31,440-ÂŁ31,860
Renovation
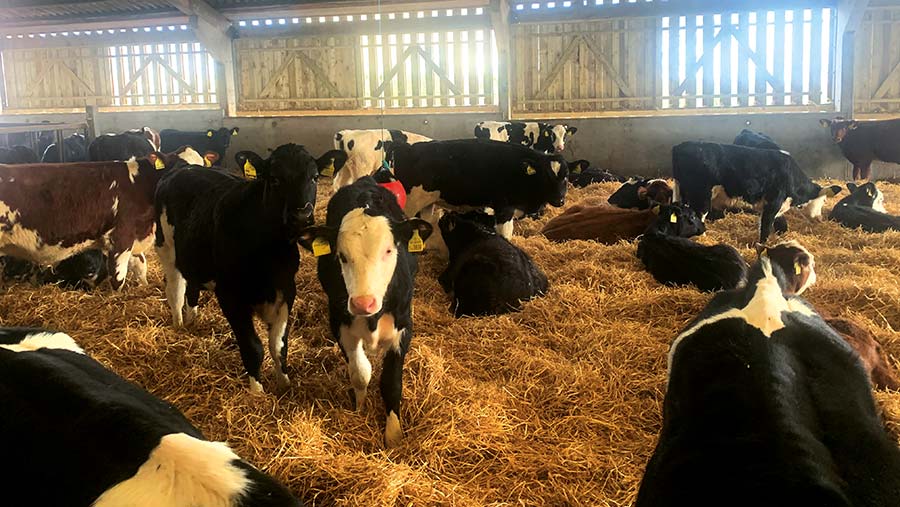
Perry Farm calf housing © Kenton Bennett
Kenton and Charlotte Bennett have chosen to adapt existing buildings with the aim of rearing healthy calves in a cheap system.
Calves are housed in a range of buildings that have been renovated to improve ventilation. In an old brick building with a slate roof, the windows have been taken out.
Sheets of plyboard have been cut so they can be tied up with twine to block the gap if the wind is strong.
Second-hand timbers and “stuff that had been lying about” have been used, making the cost “peanuts”.
Farm facts: Kenton and Charlotte Bennett, Perry Farm, Dorset
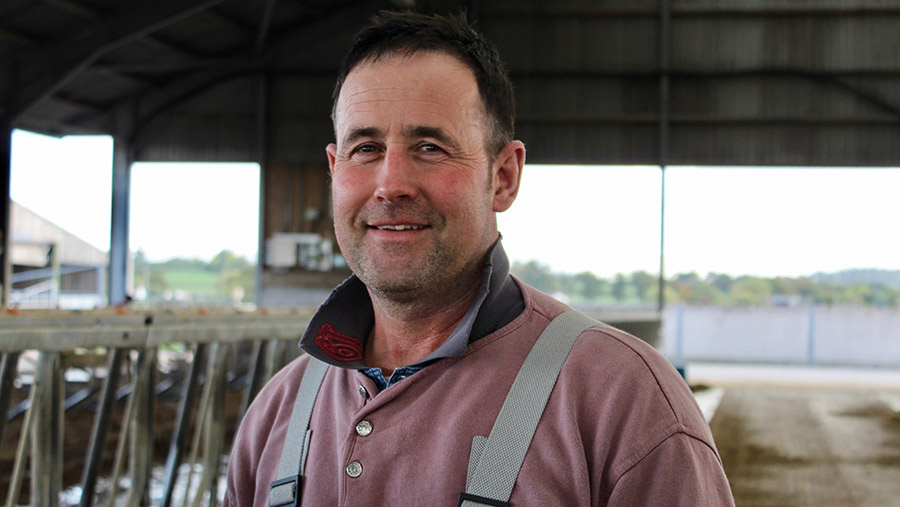
Kenton Bennett © Aly Balsom
- 144ha (356 acres)
- 141 predominantly Holstein-Friesian cows
- Autumn-calving
- 8,500-9,000 litres a cow a year at 4.38% fat and 3.48% protein
In another shed, fibre cement sheeting has been taken off and a mix of old and new space boarding installed with 50mm gaps between, as well as a home-made “sliding louvre”.
An old chicken shed extractor fan has also been installed. The ridge has been lifted using 50x100mm timber struts.
An additional site, which had been used for straw storage, bulling heifers and dry cows, has been converted to house heifer calves on a computerised milk-feeding system.
Two apex buildings sitting side by side meant air flow was a problem. A ÂŁ1,800 extractor fan has been installed with a 40% grant to tackle the issue.
Gates that were no longer in use elsewhere were then used to create pens.
Pros and cons
✅ Didn’t cost much
âś… As research is always changing, you can adapt the system as you go and won’t have lost money putting up a new shed
❌ The setup relies on manually opening and shutting doors
❌ It’s always a compromise
Top tip
Design and manage everything around the calf
Cost
A few thousand pounds plus materials lying around the farm, and time.