How three huge roundhouses are improving beef performance
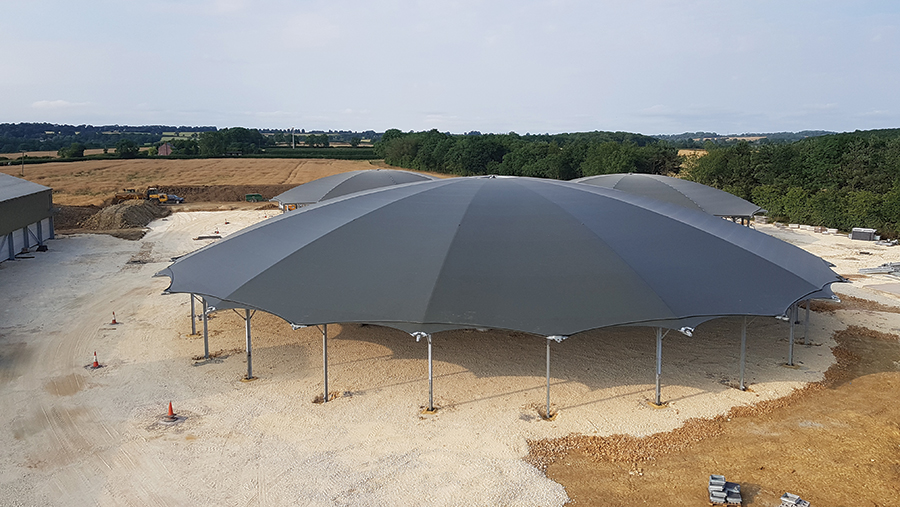
Farmer and entrepreneur David Shelton is nearing the end of building an entire beef and arable unit from scratch on a greenfield site in Leicestershire.
The site at Saxelbye Top Farm extends to about 283ha of pasture and arable land and Mr Shelton aims to grow crops and finish about 900-1,000 continental crosses once the mammoth engineering project has been completed.
The farmland had been sitting idle after the National Coal Board ceased operations there a few years ago, explains Mr Shelton.
See also: What’s In Your Livestock Shed visits high-tech beef and sheep business
Now though, it has undergone a transformation, with three roundhouse buildings, almost four miles of concrete track installed, 2.4ha of concrete laid, huge silage and feed clamps constructed and a range of other storage bins and buildings put in place.
The project
- One 45m roundhouse
- Two 30m roundhouses
- 2.4ha (6 acres) of concrete hard standing
- Almost four miles of concrete track
- Machinery store
- 5,000t grain store
- 3m deep reception pits
- Attenuation storage tanks
- Two balancing ponds
- Middens
- Feed bunkers
- Office
- Control room
- Straw barn
The beef housing
At the heart of the operation are three enormous circular beef sheds in what is the largest single installation ever undertaken by framed building designer Simpson and Allison (S&A), which produces the roundhouse.
Two 30m and one 45m diameter roundhouse cattle sheds are nearing completion and dominate the central area of the farmstead.
The first beef cattle will be brought in from grazing in early October, says Mr Shelton, who is from a farming family but amassed a fortune selling cars.
After a career building up the Motorpoint Group, Mr Shelton was able to come back to agriculture and bought a farm adjoining the new site in 2012.
It was here that he first used a 30m roundhouse to finish continental cross cattle bought in at about 12 months old.
The conventional pole buildings were run down and a roundhouse offered a ready solution to the problem, he explains.
“We moved cattle into the roundhouse and straight away started to see benefits – the cattle were calmer, disease levels were minimal and growth rates rose above 1.5kg a day.
“We were selling the cattle within 12 months over 700kg, killing out at 380-400kg and hitting R4 to U grades.”
Stocking capacity
The improved performance in the cattle is the reason why Mr Shelton has opted for three of the circular houses at Saxelbye Top Farm, which he bought after the Motorpoint Group was floated on the stock exchange.
The aim is to increase the herd from 750 to 900 head grazed on about 500 acres.
The farm’s arable area will produce some of the feed, while newly-constructed storage bins will hold maize, waste potatoes, brewers’ grains, sugar beet and wheat straw. This will be put through a Keenan mixer wagon and fed through the winter after housing.
Each 30m roundhouse will hold 120-150 cattle, while the 45m version will take 240 to 300 animals.
This allows 4.7 sq m for each animal and provides a 60cm of feed space/head at the troughs, which run around the circumference of the circle.
Building design
Even at the higher stocking rates, the air in a roundhouse is fresher than the conventional building, even on still, mild foggy autumn days, Mr Shelton says.
Company founder and managing director of S&A, Geoff Simpson explains that this is due to the shape of the roundhouse, which aids natural ventilation.
The design means the whole building acts like a chimney.
As the cattle’s body heat warms the air in the open space under the roof, it rises, travelling, uninterrupted along the underside of the curved inner surface.
The warmed air exits the building through the hole around the centre pole at the top of the dome. The air exiting at the top is then replaced by cooler, fresh air drawn in through the open sides and this helps to reduce respiratory disease levels and boosting production.
The improved performance seen on Mr Shelton’s existing unit is in-line with expectations of a 15% uplift, Mr Simpson says.
A further reason for the improvement in performance could be due to the design’s effect on stress levels.
Farmers who bought units have noted that stock were calmer and that new stock quickly settled down.
Mr Simpson suggests this is due to the high-visibility open span and visual contact with the rest of the animals under the roof.
“It is also due to the wide open space around the whole circumference of the construction. Cattle can see all around them, mimicking a situation where a herd rests at grass,” he says.
Construction and cost
Construction
In summary, this is a 15-month build project inspired by the client David Shelton together with S&A, and grain drying specialist JW Installations, explains Mr Simpson.
Despite the long timespan for the project, the roundhouses have taken the least amount of time to construct and can typically be erected in as little as four days, he adds.
The 1t PVC-coated polyester roof is constructed on the ground and attached to the lattice rafters. The steel columns, located on the outer edge, are also attached during this phase.
Then the roof is slowly raised up on hydraulic rams and the outer supports swing in underneath it as the roof reaches the final height.
The sheer amount of concrete at the unit has caused additional hurdles. The Environment Agency has insisted that two large balancing ponds and attenuated storage were installed to ensure run-off from the large concrete areas is contained.
In all there is around 2.4ha of concrete under the roundhouses, clamps and storage bins along with an additional four miles of newly-laid concrete farm tracks.
Cost
With the excavation bill to create drainage, balancing ponds and storage tanks for run-off higher than originally envisaged, the projected final total cost will be more than £3m, says Mr Shelton.
The bill for concrete is about £100,000/acre, while the total for feed clamps, grain drying and grain storage facility will break the £1m mark.
The above-ground cost of the roundhouse is £60,000 for the 30m units and £130,000 for the larger 45m set-up.
Timeline: from bare land to fully-functioning farm
2017
- June Planning application lodged
- November Site clearance starts
- December Foundations and steel erection for machinery store
2018
- March Machinery store complete
- January Foundations laid for 5,000 tonne grain store
- April Major construction of 3m deep reception pit begins
- May Steel erection of the plant tower and grain store starts
- June Roundhouse construction underway
Balancing pond and attenuation storage created
Middens and feed bunkers begun. - August Office and control room begins with September completion date
Straw shed work starts with September target for completion. - September Drying equipment installation starts
Grain store floor concreting
Final Roundhouse nearing completion - October First cattle to be housed