How to maintain milk hygiene in robotic dairies
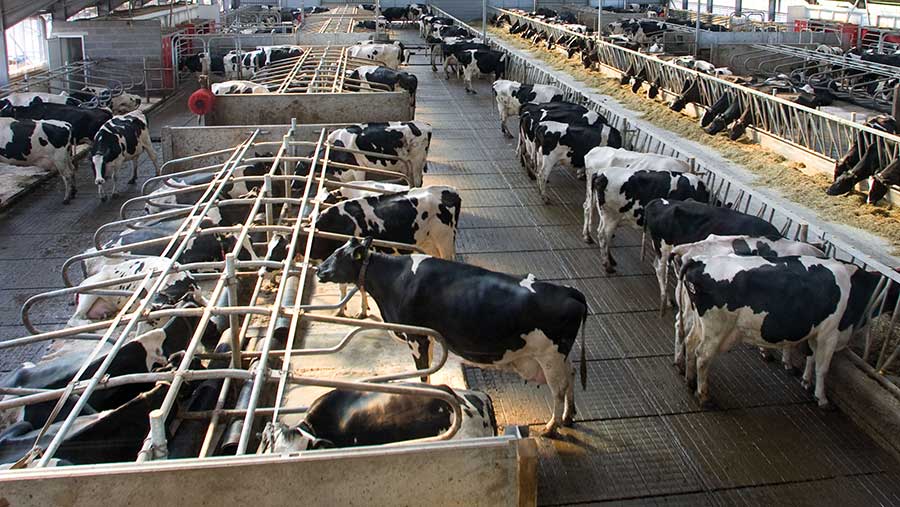
Achieving low levels of bacteria can be challenging for any dairy, but automatic milking systems (AMS) have some unique additional risk areas.
Knowing these risks allows operators to mitigate the chance of poor milk hygiene.
See also: How to make the most of technical data from robots
Environmental contamination
A dirty environment increases the bacterial load on cows’ teats. This can overwhelm the capacity of the robot for pre-milking disinfection, leading to higher levels of bacteria in the milk.
- AMS buildings always have cows in place, meaning cleaning and bedding cubicles can be difficult to achieve efficiently. If insufficient time and labour is allocated to maintaining bed hygiene, bacterial load increases on the cows’ teats.
- Slurry management in AMS must also work around the cows, leading to the use of slats or automated systems such as blade scrapers, flood washing or robotic scrapers. These systems can increase teat skin contamination unless well managed.
- Obstructions around the robot prevent automated slurry management in this area. Instead, manual cleaning is needed to reduce contamination risk to cows.
- AMS setups that include grazing often have difficulty maintaining pasture hygiene. To achieve a high number of daily visits, cows cannot graze too far from the robot. This restricts the area of the grazing platform, reducing pasture rest periods and increasing contamination of the paddocks.
Top tip: Optimise cubicle neck rail and brisket locator position to improve cow position and bedding hygiene
Teat cleaning and disinfection
Pre-milking teat cleaning by the robot has some key limitations, regardless of the system used by each model.
- Sensor technology to allow a response to dirtier teats is not yet fully developed, so environmental management is crucial to minimise teat contamination.
- Brushing tends to give a better visual clean if teats are heavily soiled but is vulnerable to inaccurate location of the teat.
- Incorrect brush height can lead to the transfer of dirt from the udder skin to the teat.
- Cup cleaning can give better disinfection, provided soiling is not too heavy, but is vulnerable to inaccurate attachment or kick-offs.
Top tip: Use extended teat-cleaning protocols – this will also improve milk flow rates
Udder health
If mastitis detection is good, infected quarters will be identified and the milk withheld from the bulk tank. However, if milk from infected quarters is allowed into the silo, certain bacteria may contribute to a high Bactoscan.
Mastitis detection in AMS is a complex issue. Testing methods are highly sensitive but tend to give a very high number of false positive cases.
Many AMS herd managers adapt to this by only responding to those mastitis alerts they think are likely to be true positives. This can lead to inconsistent detection of cases, allowing infected milk into the tank.
Top tip: Minimise the overall mastitis rate to reduce the impact of limitations in the detection system
Robot cleaning and disinfection
Disinfecting the AMS box is usually very successful, with problems limited to a few key areas:
- Incorrect chemical concentration caused by wear and tear on the dosing equipment
- Incomplete cleaning of internal surfaces as a result of perished seals, membranes and valves
- Poor transfer pipe design, leading to “dead” regions that do not get washed (this is common at splitters between buffer tank and bulk tank)
- Low cleaning frequency, which is sometimes used to cut disruption to cow visits.
Top tip: Regularly calibrate wash chemical dosing
Milk cooling
With robots milking only one cow at a time, milk transit through the system is slow, affecting milk cooling. Problems are greater if the robot is distant from the bulk tank.
- Insulating pipes can help reduce issues with milk cooling.
- Air purge systems can reduce the amount of time the milk is sat between box and tank. This is especially helpful in herds with a low number of visits each hour.
- If cooling takes place near the box, the milk can re-warm when sat in the milk line; but if cooling takes place near the tank there can be a long delay before milk is chilled.
- Cooling at the robot and again at the tank is possible, but some manufacturers are reluctant to do this because of concerns about increased lipolysis risk.
- Buffer tanks are rarely refrigerated, so milk can stay warm for extended periods during bulk tank collection and cleaning.
- Bulk tanks often do not start chilling until a certain minimum volume is reached. Milking cows individually results in a slow build-up of milk volume, delaying the start of cooling.
Top tip: Monitor cooling speed and insulate milk transfer pipes and buffer tanks
Bulk tank cleaning
The key difference between AMS and conventional systems is that AMS also have a buffer tank that requires cleaning.
A larger volume of cleaning fluid/litre of tank capacity (compared with bulk tank cleaning) is recommended for these smaller tanks.
Not all buffer tank washes are automated. For manual washes, the milk residue goes uncleaned for longer if the tank is used for overnight milk collections, increasing the risk of bacterial growth.
Top tip: Clean buffer tanks promptly after use