How a dairy farmer has integrated robots and grazing cows
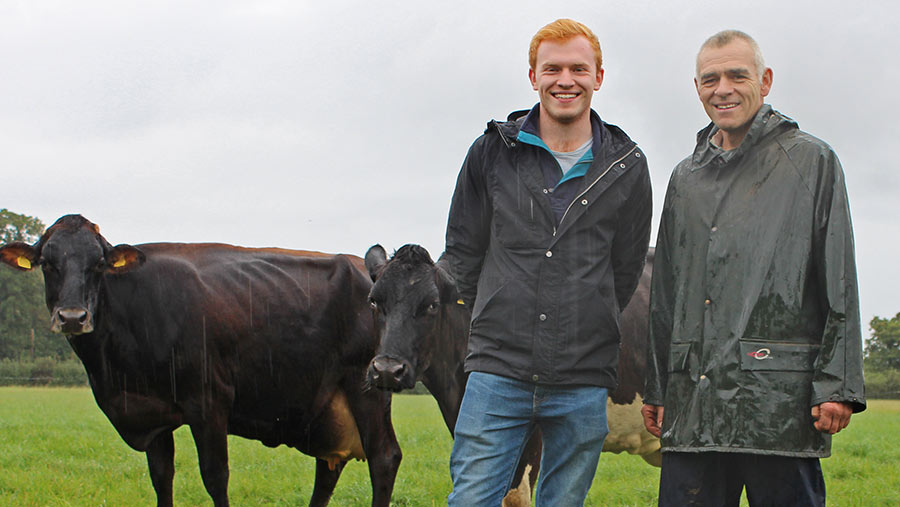
Installing a milking robot has freed up time for the Norton family to get better at grazing management and to design a system that maximises milk from forage on their existing set-up.
Having installed the robot in 2011, predominately to address labour challenges, the family have made numerous tweaks to the system over the past seven years, all with the aim of optimising intakes from grazed grass.
This has largely focused on reducing paddock size, moving to a three-paddock rotation every 24 hours and removing buffer feed during the peak grazing period.
See also: How to integrate milking robots into a grass-based dairy system
Farm facts
- 154ha
- Family team: David and Ruth, their son Jake, uncle and aunt Philip and Rona and their daughter Emily
- 60 cows – mostly Brown Swiss with some Swedish Red
- Calve July to December
- 9,000 litres a cow, 3.94% fat and 3.35% protein (2017-18)
- One third of milk processed on site, the rest goes to Arla
- Farm makes cream cheese, milk, butter and pouring yoghurt under the Nortons Dairy brand for sale through farm shops and markets
David Norton says the robot has enabled the team at Church Farm, Frettenham, to be more focused. He explains: “We’ve had more time to focus on grazing so we’re now managing the cows, rather than milking the cows.”
Creating a sustainable system that is less reliant on bought-in feeds is one of the main drivers of the business.
This means milk from forage and grazed grass is an increasingly important key performance indicator.
The fact that cows are grazed is also an important marketing message for the family, who produce various products under the Nortons Dairy brand.
While this summer’s drought has meant more concentrate has been fed, which has negatively affected this year’s performance from forage (see table), the herd has previously achieved 4,000 litres of milk from forage and this remains an ongoing target.
Grass allocation
When it comes to promoting grazing intakes, the Nortons view grass allocation as one of the most important factors on a robot system.
The aim is to provide just the right amount of grazing so that cows are not too full and therefore have an incentive to come back to the robot to either be milked or go through a selection gate to a fresh bite of grass.
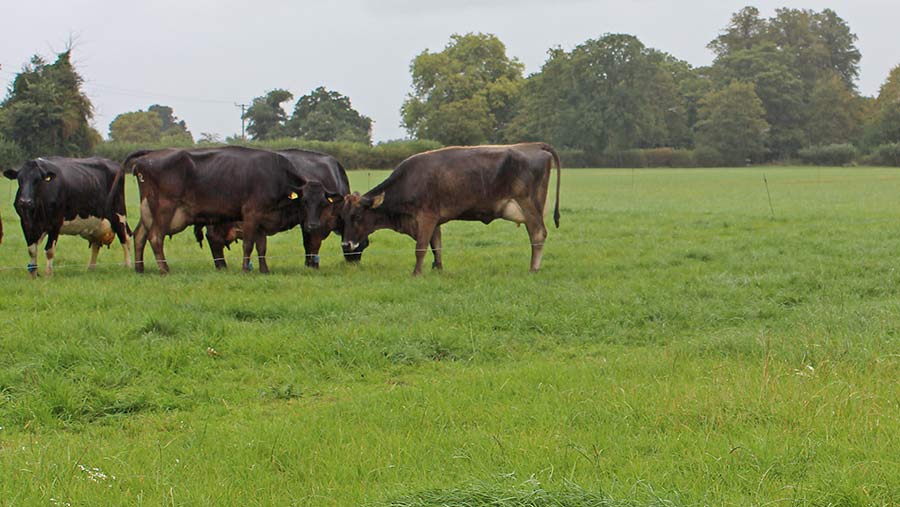
© Aly Balsom
Trial and error has shown that splitting daily grass allocations across three eight-hour feeds works best.
David explains: “When we first put the robot in we swapped the paddocks every 12 hours, but we found that the cows were quite lazy – especially the staler ones – and we were getting high hours before they came back to the robot.
“So we moved to ABC grazing. That way you get more robot visits and consequently grazing is much better.”
This system works by splitting the grazing area into three main blocks: A (18 acres), B (12 acres) and C (15 acres). Each block is then split into six to eight paddocks, which are strip grazed in eight-hour allocations.
Since the robot was introduced, average paddock size has been halved to about one acre each. “That gives us a bit more control of the grass as you can get over the paddock better,” David explains.
“There’s perhaps two or three feeds on a paddock and you can keep grass at its optimum. We’re utilising grass a lot more now. We used to waste a lot by trampling and fouling.”
Grazing rotation
The grazing selection gate on entry to the shed is set to change at specific times of the day to segregate cows into new pastures, depending on individual permissions.
An example paddock rotation could include:
A block – 6am-2pm
B block – 2pm to 8pm
A block – 8pm to 6am, on a different strip to the morning.
Cows currently come back to the shed from pasture and enter the building through a free access gate. They tend to learn at what time the grazing gate changes to let them go into a fresh paddock and go through the grazing selection gate at these times.
If they are due to be milked, they will be directed to the parlour where they are fed to yield. If not, they will be let on to the new paddock.
If cows come back before the paddocks are changed, they can go straight to the parlour to be milked. If they have milking permission they will be milked. If not, they will be kicked out of the robot.
Measuring grass
Using weekly grass plate metering, and being brave enough not to feed buffer all year round, have also proved vital to the success of the system and were part of a strategy suggested by consultant Max Sealy of The Farm Consultancy Group.
Plate metering allows the family to budget grass and plan ahead, and allows paddocks to be grazed at the optimum time. The aim is to begin grazing at about 2,800kg DM/ha down to 1,600kg DM/ha.
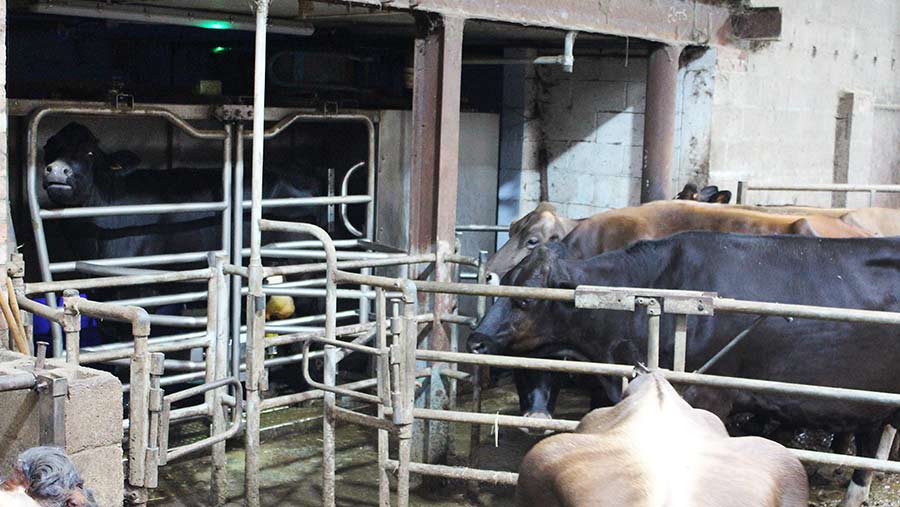
© Aly Balsom
The Nortons used to buffer feed maize through the grazing season, but this was found to negatively affect grazing intakes.
Cows now receive buffer only if grass growth is insufficient. In a “normal” year this usually means the maize, grass and blend buffer is introduced in September. However, this year’s drought meant it was started in July.
David’s son Jake believes balancing buffer with grazing is that bit harder because cows always have access to the buffer when they come in because of the building’s layout.
In the long-term, the plan is to double herd size and install a second robot, which may include a more controlled traffic system where cows have access to buffer only at specific times.
Jake adds: “We’re currently thinking about the site of the new shed. It may be across the road where there’s access to more grass. Grazing will always be important.”
Nortons Dairy: Performance from forage |
||
|
2016-17 |
2017-18 |
Yield (litres per cow per year) |
9,652 |
9,000 |
Milk from forage (litres per cow per year) |
3,633 |
2,582 |
Production from forage |
38% |
29% |
Milk from grazed grass (litres per cow per year) |
1,635 |
876 |
The summer drought has had a negative impact on yields and this season’s performance from forage |
Research on ABC systems
An EU-funded Teagasc research project, looking at making the most of robotic milking systems on a spring block calving, grazing system, found that a three-paddock system worked best.
A herd of 72 cows were grazed full time, milked through one robot and received less than 500kg concentrate a cow a year through the robot.
The grazing was split into A, B and C sections with cows going to A from midnight to 8am, B from 8am to 4pm and C from 4pm to 12pm.
Daily grass allocation was split between the three sections. The idea of the system is to facilitate cow movement as cows learn that a decrease in grass is an indication they need to go back to the robot where they will either be milked or go to a new field, says Dr Bernadette O’Brian, principal research officer for Teagasc
“The idea is you’re sending cows back to a fresh bite,” she says. “You need to allocate precisely. When grass starts to decrease in availability cows learn a new break is next door, but they need to move to the milking unit.”
In a separate trial Teagasc is currently assessing whether a four-paddock system works better for larger herds.