Feed and slurry key to pig producers’ emissions reduction
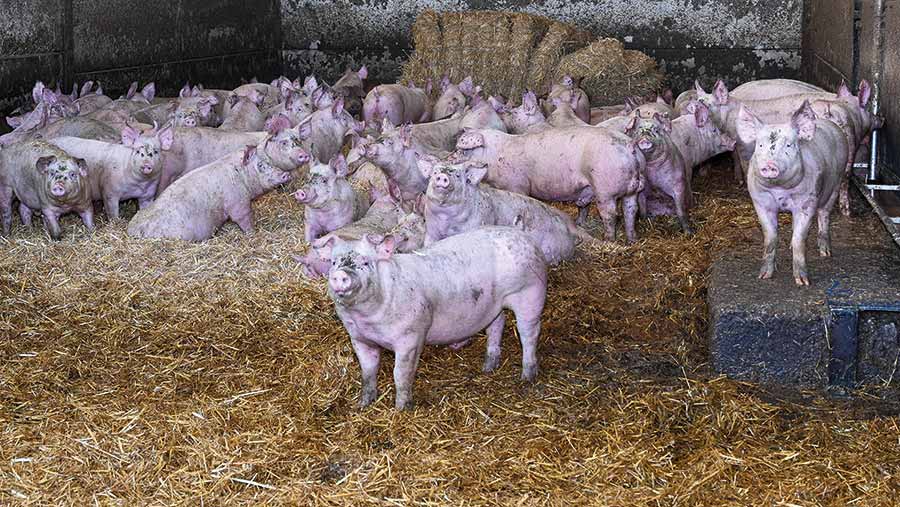
Livestock are often seen as key contributors to greenhouse gas emissions (GHGs) – including methane from ruminants and the carbon footprint of animal feed based on imported products such as palm oil or soya.
As well as GHGs associated with animal feed, emissions challenges in the pig sector are largely centred on nitrogen and phosphorus from manure management.
See also: 11 ways pig farmers can aim for net zero
UK pig emissions at a glance
A snapshot of GHG emissions associated with the UK pig sector is included in a recent report by the Centre for Innovation Excellence in Livestock (Ciel).
- Pigmeat production valued at £1.4bn in 2020
- Key challenges include the sector’s contribution to acidification and eutrophication due to emissions of nitrogen and phosphorus from manure
- Pigmeat is one of the sectors where the differences in carbon footprinting at farm level versus the National Inventory approach are relevant
- GHG emissions, as determined through life cycle assessment (using a carbon calculator), are mainly attributed to feed production (75-80%)
- Direct emissions from UK pig systems, as accounted for under inventory accounting, are mainly aligned with methane from manure and enteric fermentation (digestion), and nitrous oxide as a result of manure application.
Source: Net Zero and Livestock: How Farmers Can Reduce Emissions. Ciel
However, an increasing number of producers are seeking to reduce emissions in viable ways while helping to secure a sustainable future for British pork.
They include Yorkshire farmers Andrew and Stuart Wood, who are making use of soya alternatives and renewable energy to bring down the emissions associated with their 300-sow farrow-to-finish unit near Goole.
The herd is based on Genesus F1 types (a cross between Landrace and Yorkshire), using the criss-cross system to produce replacement gilts, and Genesus Duroc genetics for everything else, farrowing into individual slatted farrowing rooms.
Weaning takes place at five weeks with a target weight of 10kg.
Daily liveweight gain, averaging 840g from weaning to finish, is monitored throughout the production lifecycle.
Finished weights average 120kg at 23 weeks, with stock sold on contract through Beadle Marketing to Cranswick at Preston.
Farm facts: SD and AJ Wood, Goole, Yorkshire
- 300-sow farrow-to-finish unit
- All feed milled and mixed on farm
- 120ha (300 acres) of arable ground, growing cereals, maize and beans
- Finished weights: 120kg at 23 weeks
- Daily liveweight gain (wean to finish): 840g
- No zinc used for the past 10 years
Soya alternatives
As well as the pig enterprise, the farm has 121ha of arable ground. This provides key dietary components for the pigs such as cereals and maize, as well as home-grown beans for protein.
All rations are milled and mixed on farm, giving the brothers greater control over what they feed to the pigs at all times.
This setup has also allowed them to gradually move away from reliance on emissions-heavy soya – without affecting pig performance.
Although soya is still fed, its use is marginal, and the majority of protein is sourced from alternative products.
The brothers work closely with nutritionist Faye Murch from Kingsgate Nutrition to meet both dietary and environmental targets.
However, soya usage has never been particularly high, as the farm has historically relied on whey as a key protein source.
Stuart says: “In the mid-1980s we started using whey, and we’ve always been liquid fed for the latter stages [of the diet].”
Today, the herd receives a liquid feed at most stages of production which includes co-products such as whey, potato puree and a wheat distillers’ syrup alongside the farm’s home-grown ingredients.
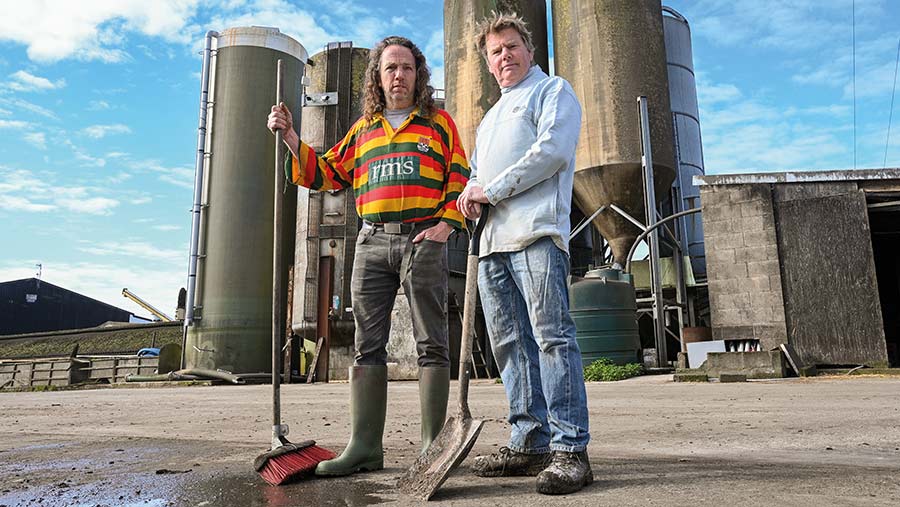
Andrew (left) and Stuart Wood © Colin Wallwork
“We have also been using crushed crisps until recently, but they’re a bit priced out of the ration at the moment,” says Stuart.
The management of the pigs is split into four stages, taking them through from weaning to finishing. At each stage, pigs are fed a different, bespoke diet tailored to their needs.
Andrew explains: “At the first stage, they are weaned into eight pens of 18 and fed a bought-in feed from ForFarmers, consisting of cooked cereals and whey powder, which is helping to achieve a daily liveweight gain of 500g over four weeks.”
From this stage, pigs are moved into bigger groups – about 70 – and wet fed a diet based on whey, potato puree and the farm’s own wheat and barley, as well as minerals and a small amount of soya.
“Over the coming weeks we’re also aiming to [start to] include brewers’ yeast as a liquid, which we hope will reduce our soya usage even more,” says Stuart.
Keeping wet feed consistent through the production cycle really helps with the transition at this stage, says Andrew.
“The piglets see their mothers being wet fed in the farrowing house and they seem to go straight to it at this stage.”
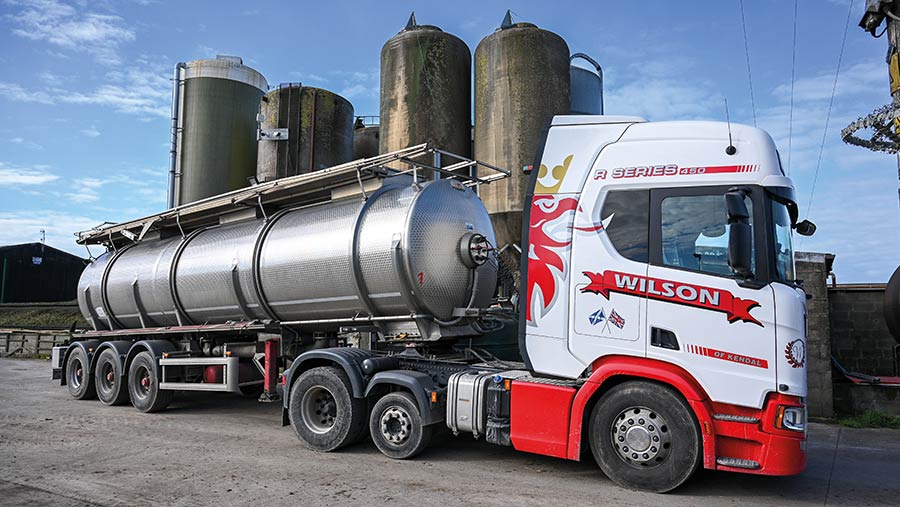
© Colin Wallwork
Four weeks later, pigs move to a straw yard and stay on a liquid feed consisting of the same ingredients as before, but in different proportions.
The final weeks are spent in the fully slatted finishing house, where pigs are split into groups of 18 based on weight.
The same base wet ration is fed but formulated slightly differently to accommodate finishing requirements, says Stuart.
From weaning to finishing, the farm is using a total of 5-7% soya in the diets, and he says that once they move on to the brewers’ yeast this will come down to less than 5%.
Processing and transport also contribute to feed emissions, but Stuart says this is resolved by sourcing almost all co-products from within a 50-mile radius.
Investing in technology
To strengthen links between the pig enterprise and the arable business, the Woods have invested in slurry technology.
This has reduced their reliance on bought-in fertiliser for the arable crops and lowered the associated emissions.
“We put in a slurry separator about three years ago to improve consistency of the slurry,” says Stuart.
“We get that analysed, so we know what the nutrient content is, and then we know how much we need to put on to grow a decent crop of wheat or barley.
“Last year on one field of wheat, we did 10t/ha and didn’t use any artificial nitrogen at all – we just put the slurry and some compost on.”
Stuart says they are going to replicate this in the coming season on a larger scale, with the aim of growing 40ha of wheat without any nitrogen.
There is an economic benefit too, adds Andrew: “You’re not applying it [the slurry] for nothing, but we’ve got it here already so we don’t have to buy it in – we only have to hire a contractor to apply it.”
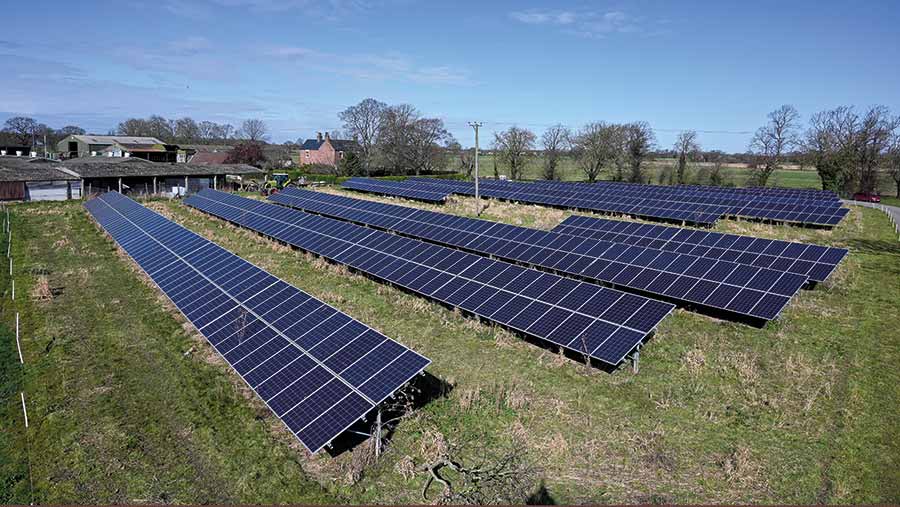
© Colin Wallwork
The farm also makes use of renewable energy sources to reduce its overall environmental impact, and has a 250kW solar panel plant.
This was installed in December 2015 and powers the pig housing as well as the main farmhouse.
“We toyed originally with wind turbines and a biomass boiler, but solar panels seemed a better fit for us,” says Stuart.
“We’re using as much as we can from that. On a nice bright day [in winter] we use a lot of solar power and not as much from the National Grid, and as we get into the summer we’re actually able to export it to the National Grid too.”
Tweaking the system
Their approach recently saw the Woods crowned Finisher of the Year at the National Pig Awards, But the brothers remain humble, saying this is the way they have inherently wanted to run their business for the past 10 years.
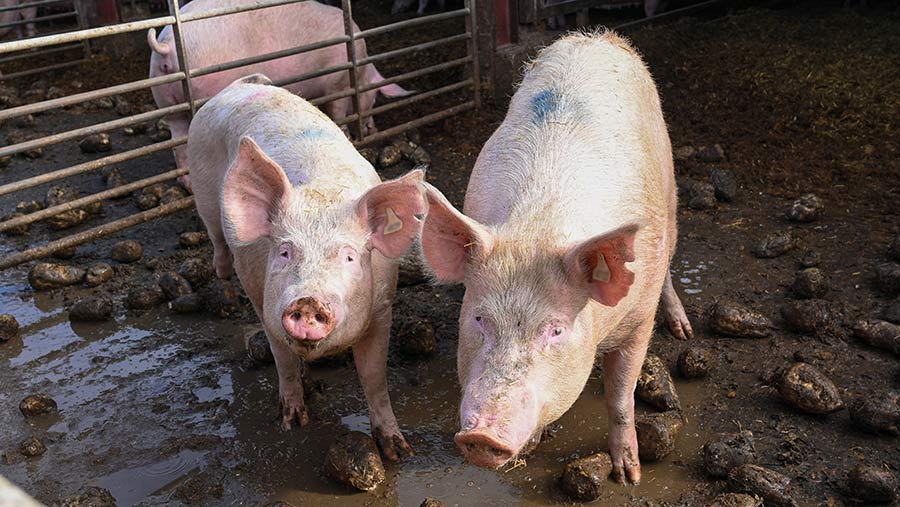
© Colin Wallworth
“It was an accident,” laughs Andrew. “But ultimately, it is more cost effective for us to have a lower carbon footprint.”
An official carbon audit has yet to be carried out. Until then, the Woods say the focus is making small tweaks where possible to ensure overall business efficiency.
In turn, they believe this will help reduce their environmental impact.
“Though there isn’t [carbon emissions] pressure from [our processors] yet, supermarkets are now starting to put pressure on processors to get carbon footprints down, so it’s inevitable,” says Andrew.
The brothers say there’s not a lot more they can do at the moment to reduce their carbon footprint without spending a lot of money.
However, something they are interested in is making more from their muck, which could be beneficial to agricultural emissions in general, as well as offering a financial opportunity for the farm.
“There’s quite a lot of work being done at the moment looking at the gases in slurry. There’s quite a bit of hydrogen that can be harvested from slurry,” says Stuart.
“It’d be nice to be able – if there’s something there – to capitalise on that.
I understand that there is the equivalent of £20 worth of hydrogen produced by a bacon pig in its lifetime. Well, if we’re selling 8,000-9,000 pigs a year, then there’s an opportunity there.”
Ways to reduce GHG emissions in pig production
Research into a range of mitigation strategies for reducing livestock emissions was carried out recently by a group of scientists for the Centre of Innovation and Excellence in Livestock (Ciel), headed by Elizabeth Magowan from the Agri-Food and Biosciences Institute.
For the pig sector, the aim was to look at the impact on GHGs of strategies such as removing soya from the diet and genetically improving pigs to emit less, as well as how easy and cost-effective this might be.
These strategies were split into three areas: animal, feed and manure/fertiliser.
The table below highlights some of the measures pig producers can consider – and how effective they might be when it comes to setting strategies to reduce overall on-farm emissions.
Effect of farm management changes on emissions and output |
|||||||
Strategy |
Cost |
Ease of implementation |
State of readiness to implement |
Potential GHG mitigating effect |
Impact on carbon footprint |
Other impacts |
Accounted for in the National Inventory |
Animal |
|||||||
Genetic improvement |
Low |
High |
Now |
Methane and nitrous oxide reductions |
Low |
Phosphorus and ammonia reductions |
Yes |
General health improvement |
Low |
High |
Now |
Methane and nitrous oxide reductions |
Low |
Phosphorus and ammonia reductions |
Yes |
Feed |
|||||||
Precision feeding and management to improve feed use efficiency |
High |
Medium |
Later |
Methane and nitrous oxide reductions |
Low |
Phosphorus and ammonia reductions |
Yes |
Specialist ingredients focused on improving feed utilisation |
Low |
High |
Now |
Methane and nitrous oxide reductions |
Low |
Phosphorus and ammonia reductions |
Yes |
Higher co-product inclusion level |
Low |
Medium |
Now |
Product dependent |
Medium |
|
No |
Use of alternative ingredients to soybean meal |
Medium |
Medium |
Now |
Product dependent |
High |
|
Yes |
Lower crude protein diet |
Low |
High |
Now |
Nitrous oxide reductions |
Low |
Ammonia reductions |
Yes |
Manure/fertiliser |
|||||||
Anaerobic digestion |
High |
Medium |
Now |
Methane reductions |
Medium |
Odour and ammonia reductions |
Yes |
Acidification |
High |
Low |
Now |
Methane reductions |
Low |
Odour and ammonia reductions |
No |
Covered stores |
High |
High |
Now |
Depends on what cover is made of |
Low |
Odour and ammonia reductions |
Yes |
Low emission spreading and precision application of manure |
High |
High |
Now |
Nitrous oxide reductions |
Medium |
Ammonia reductions |
Yes |
Source: Ciel. Notes: Impact on carbon footprint was assessed via a carbon calculator. The National Inventory and inventory accounting are used by the government to measure carbon emissions and carbon capture at a sectoral and national level. Soyabean emissions are often attributed to the country of production, so they will reduce overall pork emissions but have a lesser effect on “local” emissions. Low ease of implementation = more difficult to implement. May require infrastructure or full system changes. |
Barriers to net zero
Although some producers are making significant progress towards net zero, instability in the pig sector could be a barrier to further improvements, says National Pig Association chief executive Lizzie Wilson.
“I guess what we need first and foremost is for the whole supply chain to be able to sustain a profit to enable reinvestment in infrastructure such as buildings and equipment, and animal health and welfare, to improve productivity and efficiency and mitigate our environmental impact as much as possible,” she says.
“We’ve already got a good story to tell as an efficient and proactive sector, but producers need whole supply chain support and investment when trying to deliver solutions like sustainable soya, as they can’t do it on their own – either practically or financially.
Retailers are all being driven by their Scope 3 obligations but after two years of financial loss, producers are in no position to be solely accountable in delivering their commitments.”
Government intervention is needed, she says, with regard to planning in particular.
“Currently the Slurry Infrastructure Grant scheme could well run into trouble if planning applications for slurry stores aren’t approved by local planning authorities.
“Hold-ups are due to the Habitats Directive, associated nutrient neutrality issues – whereby local planning authorities may only sanction new development if it will not result in any more nutrients impacting a protected site than previously – and the lack of recognition of betterment.
“Even if producers can financially reinvest in their business and buildings, this issue threatens to halt any progress on achieving our net-zero ambitions.”