Faster turnover key to improving beef profits
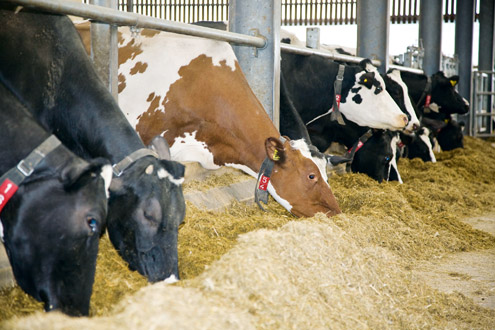
Improved growth rates and feed efficiency are just part of the answer to maximising beef margins, and considered in isolation fail to fully account for either feed cost or rate of finishing.
According to KW nutritionist Dave Collett, cost per kg of liveweight gain (p/kg LWG) is one of the most important drivers for improved margins, with cattle turnover the critical factor in translating that into profit.
“If you have a finishing unit with a capacity of 200 cattle, maximising the income from that unit lies in how many kilos of meat can be produced per annum,” he states. “And as long as each extra kilo produced achieves a positive margin over costs, then the result is more profit.”
The key is to aim for high growth rates and quick finishing, but at minimum p/kg LWG. However, hitting target grade as regularly as possible is still important to maximise carcass value, as is selling cattle as soon as they are finished.
“The efficiency with which cattle grow decreases over time, so any extra days an animal is taking up space in the shed after it’s finished is reducing productivity,” Mr Collett adds.
Calculations show a 36-day reduction in the time taken to finish a continental-cross steer from 400kg LW to 620kg LW (from 183 days to just 147 days), results in a 25% increase in turnover.
The result is a gross margin per head improvement of £23 a head as a result of lower cost of growth, plus an additional 98 cattle finished each year on a 200-head finishing unit.
This equates to an overall gain of £29,709 per annum (see Table 1).
“Thinking in terms of what can be achieved from each ‘animal space’ is definitely the way forwards,” Mr Collett claims. “It then comes down to how best to improve those finishing times without disproportionately increasing p/kg LWG, and that’s where good feeding strategies come into play.”
To maximise lean tissue growth and frame development in growing cattle, Mr Collett recommends a diet containing 15-16% crude protein (CP) at 11.5MJ ME/kg DM. For finishing, a higher energy: protein ratio is required, typically 13-15% CP at a minimum of 12.0MJ ME/kg DM.
“The focus is on fast, efficient growth, while using feeds that are the best possible value in terms of nutrient supply. Often it’s the higher quality feeds that offer better value despite a higher cost per tonne, particularly when the result is faster growth and a lower p/kg LWG.
“Moist feeds are generally more cost-effective than their dry equivalents, and will also drive intakes by improving ration palatability,” he explains. “Feeds like processed bread are a great source of starch energy, while the distillers’ moist feeds will supply good levels of protein and the digestible fibre needed to help buffer the rumen against acidosis.
“Liquid feeds are another option to make rations more palatable and increase intakes, particularly where moist feeds are in short supply. For starch, consider the various confectionery or bakery co-product blends as an alternative to cereals.”
Significant cost savings can be made by switching from a traditional beef-finishing ration, capable of achieving the higher growth rate of 1.5kg/day, to using alternative feeds (see Table 2).
For those without a TMR (total mixed ration) feeding system, an alternative feed blend (Option A) is clearly better value than a compound, while also giving better control over the feed ingredients used. Blends are even now finding favour with many straights users thanks to less capital tied up in individual straights, greater consistency when fed and a reduction in storage and labour requirements.
“Finally, don’t forget the basics for efficient conversion of feed into meat,” Mr Collett concludes. “Ensure access to sufficient structural fibre to encourage efficient rumination, with 0.5kg/day of chopped wheat straw an absolute minimum, and consider a live yeast to minimise acidosis if high levels of starch are being fed.
“Offer fresh feed each day in clean troughs, plus clean drinking water and clean bedding, and keep a watchful eye on health and growth rates. You can’t maximise efficiency without close attention to detail, and that’s what this approach is all about.”