Farmers Weekly Awards 2022: Pig Farmer of the Year finalists
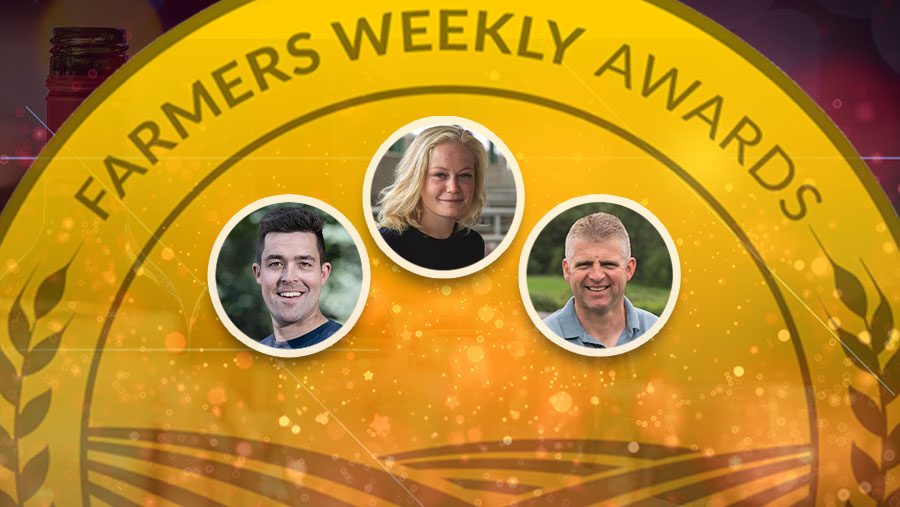
High technical performance and a sound knowledge of figures were the common themes among this year’s finalists.
They include two indoor producers, in Londonderry and Norfolk, and a “hybrid” outdoor breeding unit in Nottinghamshire.
See also: Find out more about Awards night
The finalists:
Matthew Burgess
Manton Forest Farm, Worksop, Nottinghamshire
David Fulton
Carricknakielt Farm, Magherafelt, County Londonderry
Lizzy Murrell
Railway Farm, Great Plumstead, Norfolk
The judges:
Richard Mellor
Last year’s winner
Charlotte Cunningham
Farmers Weekly deputy projects editor
Rebecca Veale
Chief policy adviser at the National Pig Association
Matthew Burgess
Manton Forest Farm, Worksop, Nottinghamshire
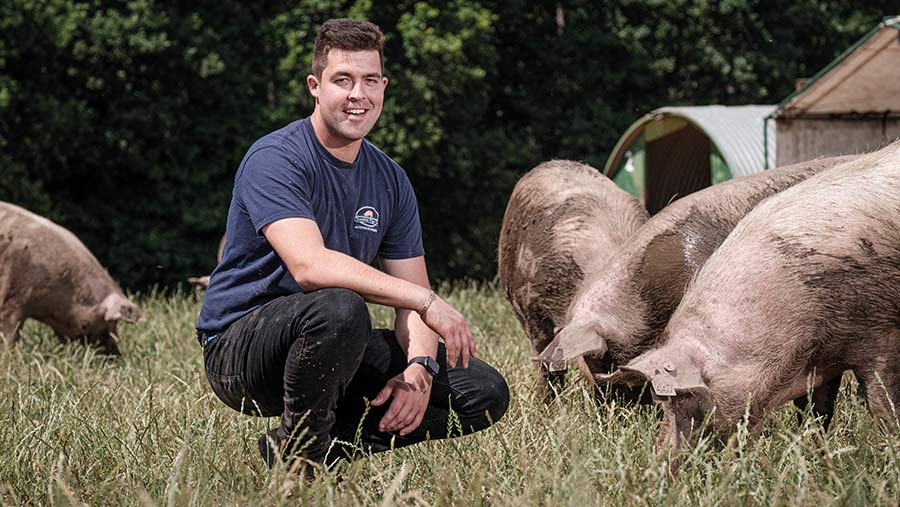
© Jim Varney
Despite setting up in outdoor production just three years ago, the 1,600 head Clumber herd is already achieving enviable results.
Headed by Matthew Burgess, Manton Forest is the epitome of a family farm. Matthew’s father, Kevin, and stepmother, Bev, are also on board and vital to the success of the operation.
This is the first outdoor unit the family have run, having previously been in the indoor sector.
The herd was established with stock from Rattlerow and started as an 840-sow breeding herd, farrowing batches of 120.
Since then it has expanded to 1,600 head, farrowing batches of 225 – with stock still sourced from that original unit and offspring sold on as weaners.
Herd management
All breeding stock are Rattlerow Whiteroc, which Matthew says stand out for their ability to breed consistently, their good longevity, excellent temperament and natural mothering instincts.
Matthew describes the farm as a hybrid unit, which makes use of both indoor and outdoor facilities at the farm.
At the heart of this is the “engine room” – a series of buildings which are used for servicing and retaining smaller piglets at weaning. From weaning, all sows are housed until after servicing.
A bespoke indoor service area enables a team of three to serve 225 pigs over a five-hour period, and an indoor post-service shed, fitted with artificial lighting to minimise fertility issues in darker months, ensures sows are in the best possible condition before they go back outside.
The indoor facilities also include a shed dedicated to synchronising oestrus in maiden gilts. This is made up of 50 crates with drop down feeders which allow the staff to mix the hormone in with the feed.
All piglets under 7kg at weaning are retained and cared for indoors by Bev. This approach means mortality in this group remains low.
Performance and technology
Outdoors, farrowing accommodation is provided via insulated Aardvarks.
Matthew says these have proven to be much better than traditional green huts, bringing benefits such as lower mortality rate both in warmer weather and cold winter months, ease of checking and bedding pigs, and an automated back window which opens and closes with a wax strut, depending on the inside temperature.
Specially constructed sow “footpaths” enable animals to walk leisurely around the farm and means handling and moving stock does not involve a trailer, which keeps stress levels low.
Helping him to run all of this is a team of seven full-time employees. Technology also aids management.
Electronic identification tagging was introduced last year to improve accuracies in record keeping and minimise handling of animals to improve welfare.
Collaboration with other businesses, such as a muck-for-straw agreement, is also fundamental to the unit’s success.
One of Matthew’s greatest achievements to date was receiving a clear audit recently on a retailer inspection.
Challenges and future plans
With costs identified as one of his main challenges, Matthew says the farm tries to manage them by forward contracting all feed.
This has resulted in huge savings over the past 12 months, and he already has feed supply contracts in place to August 2023.
Benchmarking of data is also routinely and regularly used to adapt management decisions when needed.
Expansion is on the horizon, with plans already in place to put down a similar unit soon, and a third unit in 2023.
What the judges say
Matthew is managing a large number of pigs and a big team of staff effectively and hitting excellent production targets and financials. There is a clear emphasis on optimising animal welfare at all times.
Matthew Burgess summary
The judges liked…
- The same care, diligence and enthusiasm displayed by all staff members during the judging visit
- Good working relationship between Matthew, his father and stepmother, to ensure optimum efficiency right across the production cycle
- A clear vision for the future
Farm facts
- 1,600-sow “hybrid” breeding unit, using indoor and outdoor facilities
- Offspring sold on as weaners
- All piglets under 7kg at weaning are retained and kept indoors to encourage growth
- Electronic identification technology used to simplify stock tasks and minimise handling
- Operating a muck-for-straw agreement with a local farmer
The numbers
- 1,600 sows at Manton Forest Farm
- 91% Conception rate
- 12 Average piglets weaned a litter
- 28.46 Piglets weaned a sow a year
- 2 Frequency of hedge cutting (years) to encourage nesting birds and provide windbreaks for sows
David Fulton
Carricknakielt Farm, Magherafelt, County Londonderry
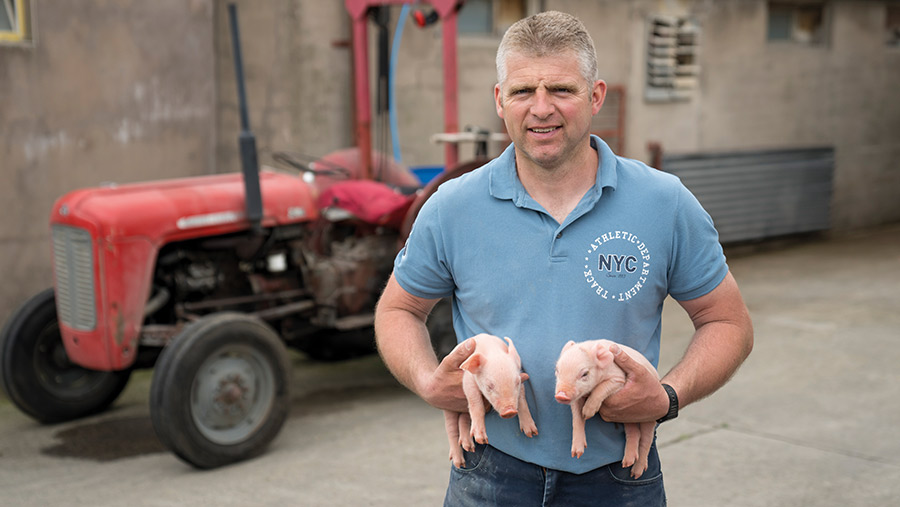
© Steffan Hill
With pigs, sheep and cattle on one site at the 65ha (160-acre) Carricknakielt Farm in Northern Ireland, paying close attention to detail is fundamental to the success of David Fulton’s business.
Second-generation farmer David runs a 180-head birth-to-bacon indoor unit, producing pigs for the largest pig processor in Northern Ireland.
Herd management
About six years ago, he decided to switch to Danish genetics to improve herd performance.
To get the best from these genetics, a major overhaul in the management of the unit was required, and while this resulted in short-term challenges, the longer-term benefits have included improved numbers of live born and better growth rates.
Among these management changes have been alterations to feeding. As David mills all his own feed, he can tweak diets quickly and formulate rations to suit the specific needs of the pigs.
Last year, zinc was removed from diets in anticipation of a ban on its use, with no ill effects, and all medicine is now administered via water.
This water system is also used to administer other supplements such as vitamins. Antibiotics usage is very low, at 9.67mg/kg a year.
Benchmarking is central to management, with David using multiple sources and platforms to compare current figures with his own historic performance, other producers and national averages.
He reviews data at least once a month so management can be adapted quickly to prevent any small issues becoming big problems.
Performance and technology
Technology plays a big role in maximising efficiencies and helps reduce reliance on labour.
A recording app is used daily to record sow data and highlight any issues within the herd, which helps David optimise labour and prioritise which animals need attention first.
Feeding technology is also helping him maximise labour. This includes a system which supplies milk to a cup in each farrowing crate, ensuring pigs have access to milk from day five to weaning.
David has also installed a computerised feed system in the farrowing house with a pneumatic wheel dispenser that measures feed. Each portion is delivered in small doses according to the animal’s appetite and its ingestion rhythm.
A trough inspection system in the bottom of the trough automatically enables the distribution of feed each time it detects an empty trough.
The sows eat at their own pace and appetite, according to their feeding curve – with no wasted feed – and each serving is delivered with a dose of water.
Between meals, water distribution curves can be pre-set, allowing David to see exactly what each sow is eating, or not. He can then use this information to decide whether to increase the ration.
These elements improve the sow’s consumption and lactation, and the system itself has reduced labour as there are no troughs to be cleaned out and no waste.
Challenges and future plans
Like many producers, labour has been a challenge for David, but he has a clear vision and succession plan for the future, which involves bringing his two sons into the business.
Both have recently finished at agricultural college, with youngest son Nathan now off to complete a foundation degree before coming back to join his brother, Daniel, and David on the farm.
He also has plans to expand the business over the next two to five years.
What the judges say
David takes an impressive and meticulous approach to benchmarking, which enables him to optimise management and production of his herd and continuously go above and beyond industry targets.
David Fulton summary
The judges liked…
- Attention paid to the “little things” such as cleaning out the slurry store every year to avoid losing space to sediment build-up
- Turning challenges into learning opportunities and improving performance or management as a result
- Involvement in multiple farm-led knowledge exchange discussion groups
Farm facts
- 65ha (160-acre) site in Magherafelt, County Londonderry
- 180-sow birth-to-bacon unit
- Closed herd with all gilt replacements bred on farm
- Using Danish genetics
- 120-head of beef and a 400-head of Mule cross Texel sheep
The numbers
- 5.85% Post-weaning mortality in 2021
- 847g Daily liveweight gain from weaning to finished weight
- 32.3 Pigs weaned a sow a year
- 9.67 Carricknakielt Farm’s antibiotics usage (mg/kg) in 2021. Industry average for birth-to-bacon units was 57.781mg/kg
- 8,000 Metres of hedges planted over past 15 years
Lizzy Murrell
Railway Farm, Great Plumstead, Norfolk
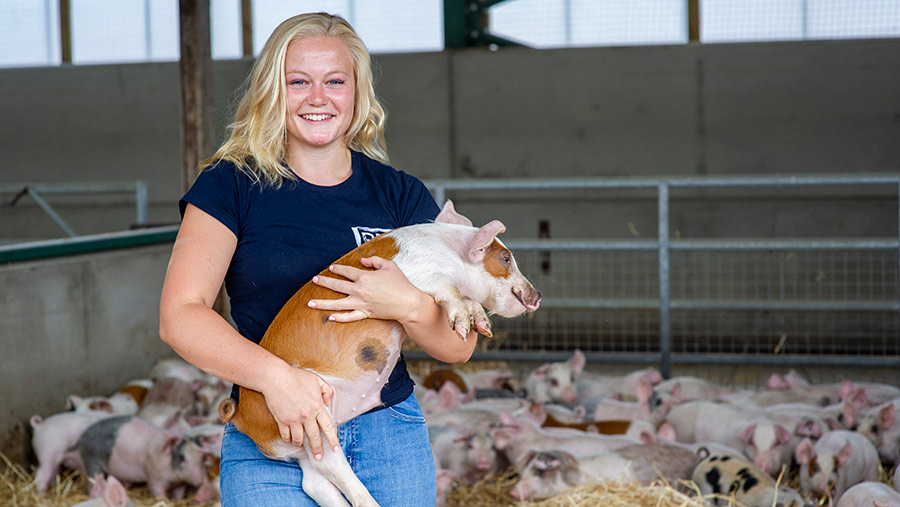
© Jason Bye
Single-handedly managing a 2,000-head finishing unit on contract for BQP, new entrant Lizzy Murrell has already made a name for herself in the pig sector.
At just 23, she has already been crowned the 2021 Growing Stockperson of the Year at the annual BQP breeder and grower ceremony and is currently on her eighth batch of pigs, after deciding at age 19 to venture into finishing her own pigs.
The new unit at Railway Farm was designed by Lizzy’s grandfather, from whom she rents the farm. It comprises three housing sheds, a straw barn and two workshops, situated within 24ha (60 acres) of arable land in the east of Norfolk.
Herd management
Piglets arrive as weaners at 7kg and are fed on a creep starter pellet, before moving over to a larger weaner pellet.
Lizzy tweaks her feeding regimes to improve pig behaviour, when needed. When faced with a particularly restless batch she requests naturally sourced additives, such as seaweed, to be added to her order of feed.
Lizzy says she finds this calms the pigs, without affecting daily liveweight gain and growth rates.
Each shed is split into eight pens and features a double dung passage, which Lizzy says makes overall management and husbandry tasks a lot more efficient.
The pens are also larger than the recommended size and standard for a new build. Measuring 15.2×5.2m, these pens provide more space, air circulation and gives pigs the freedom to express natural pig behaviour.
With pigs bedded on deep straw, and an average of 1,000 bales needed a year, a muck-for-straw agreement helps Lizzy resource adequate supplies, while making best use of her muck.
After each batch, a sub-contractor is brought in to wash down the entire unit.
Performance and technology
On one of her recent batches of pigs, Lizzy achieved a feed conversion rate (FCR) of 2.2:1, which saw her awarded the accolade of BQP’s Finisher of the Month. BQP offers structured incentives for achieving FCR targets, which she has been achieving consistently.
Daily liveweight gain averaged 864g/day and mortality sat at about 4.37% across this batch.
This is compared with her first batch, which averaged a FCR of 2.32:1, daily liveweight gain of 811g and 4.68% mortality, demonstrating the conscious effort she has made between batches to improve production.
The use of technology helps to simplify management of the unit. Each shed has a select doser fitted to enable the quick delivery of water medication when needed.
A simple interface unit highlights water usage, with daily intakes monitored in every shed to enable quick detection of any potential issues.
Since last year, Lizzy has also been making use of a new app for recording mortality which contains data on the current batch – including repopulation numbers and which farms piglets have come from – as well as overall mortality percentages.
Any sudden spikes in deaths are automatically flagged up to BQP.
Challenges and future plans
Acutely aware of the challenges the industry faces, Lizzy cites backlogs and world market volatility as some of the most acute, but also recognises what she can do to overcome them.
This includes careful selection of fat pigs to go to slaughter and ensuring all aspects of the business are streamlined as much as possible to overcome any future challenges.
What the judges say
Lizzy demonstrates tenacity and natural leadership skills, not only in the way she manages her pigs, but also how she works with her suppliers and vet. Her attention to detail is evident in the contentedness of her pigs.
Lizzy Murrell summary
The judges liked…
- Overall enthusiasm and passion for the pig industry and a strong belief in its future
- Her approach to collaboration, including a muck-for-straw agreement
- Good use of both the hospital pen and the “smalls” pen which are helping to keep mortality low
Farm facts
- 2,000-head wean-to-finish unit on contract to BQP
- Situated on 24ha (60 acres) of arable land
- Piglets arrive as 7kg weaners and are taken through to finish
- Brand-new unit comprising three sheds, a straw barn and two workshops
The numbers
- 7kg Weight of piglets when they arrive on farm
- 2.2:1 Average feed conversion rate
- 864g Average daily liveweight gain a day
- 1,000 Round bales of straw needed annually for bedding
- 19 Lizzy’s age when she took on her first batch of pigs