Farmer’s engineering skills make farm net electricity producer
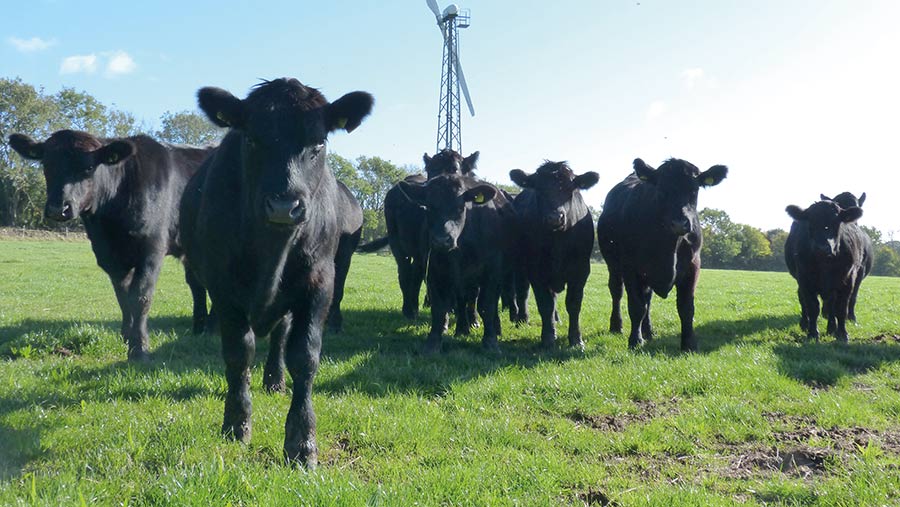
A mechanically minded Yorkshire farmer has made the family farm a net electricity producer by capitalising on tariffs and applying his engineering skills.
Former oil industry engineer and mixed farmer Mark Hutchinson, of Spikers Hill Farm near Scarborough, returned home in 2008.
On his return he bought a second farm – Magdalen Grange, 10 miles away near Filey – and installed solar and wind power on both holdings to supply power.
See also: Farm businesses facing energy bills increase of up to 400%
The big investment came in 2016, when the farm bought a gas-fired, combined heat and power (CHP) unit using woodchip. This made the business self-sufficient in electricity.
He made the most of the Renewable Heat Inventive (RHI) payments, Feed-in Tariffs (Fits) and Renewable Obligation Certificates (Rocs) on offer at the time, many of which run for 20 years.
Today, the farm sells about two-thirds of the electricity it produces back to the grid.
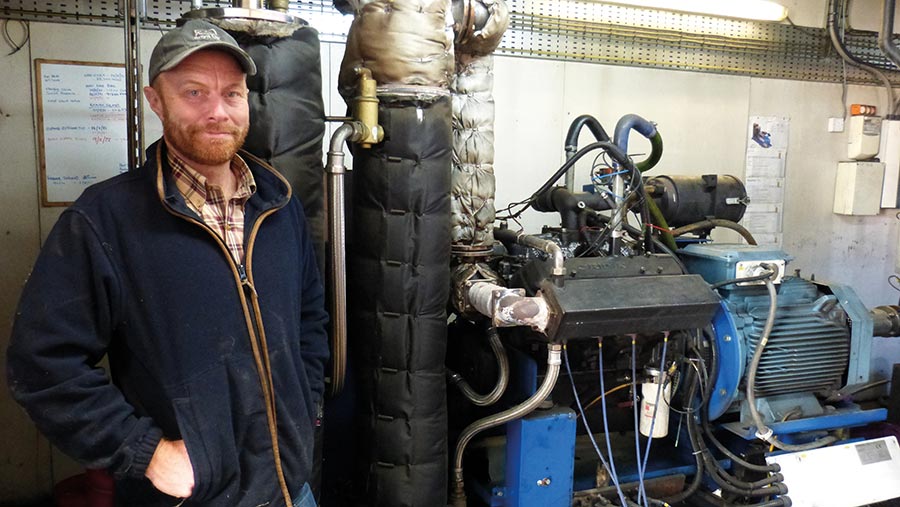
© MAG/Michael Priestley
Farm Facts
- Finishing 120 Angus-cross cattle
- Supplying Dovecote Park
- Close to 240ha (1,000 acres) farmed, of which 24ha (59 acres) is grassland
- 295ha (730 acres) owned, the rest is rented
- Growing malting barley, feed wheat, beans and rape and renting out land for potatoes
Early adopter
After completing an engineering degree and spending 15 years in oil exploration, energy was at the forefront of Mr Hutchinson’s mind at the start of his farming career.
He admits that it could be harder now for businesses to make investing in renewables stack up, but the higher electricity prices mean the savings are bigger.
The farm business benefits from the CHP unit, as it can dry grain for no cost. About half of the 2,000t of grain the farm produces was dried this year – each crop is dried in one go as a 500t batch over a vented floor.
The woodchip – mostly from local sawmills – must be chunky and have a low bark content, and is heated to produce a gas.
Woodchip costs about £40,000/year, but saves £30,000-£40,000 in fuel and generated £100,000-worth of electricity last year.
The cattle sheds at Spikers Hill run east to west, meaning a south-facing roof can be used to position solar panels.
A multipurpose shed supports the solar panels at Magdalen Grange, which also has a south-facing roof.
Cattle are checked using a rechargeable all-terrain vehicle, powered by the farm’s electricity. Cattle are bedded on straw in winter, as the woodchip is relatively expensive.
Tips for farmers
- South-facing roofs are best for solar panels
- Estimate wind speed considering prevalent winds, hills, and trees before siting a turbine. (Lowering the tower on the Gaia turbine from 18m to 15m due to planning restrictions when relocating almost halved production from 40,000kWh to 22,000kWh)
- Insulation is the best investment – look at flooring and walls as well as roof cavity
- Solar and wind sources benefit from free fuel, but CHP/biomass options are not weather dependent
- 1kW of wind gives 3,0000kW/year, compared with 1,000kW of solar
- Planning permission and grid connection can be the biggest drawbacks – seek advice if needed
- Three-phase power is needed for larger projects. Small projects are fine on single phase
Pros, cons and earnings of renewables |
||||
|
Generation method |
Positives |
Negatives |
Income and use |
Solar panels
|
20kW at home placed on cattle shed roofs
10kW at Magdalen Grange on multi-purpose shed
Both installed in 2012, capitalising on Feed-in Tariffs |
Makes use of otherwise idle roof space
Does not take up farmland
No labour input and very simple to run |
More intermittent form of energy
Not much production from November to March
Low energy generation – 10kW equates to about 35 panels |
10kW of panels produces about 10,000kWh/year
Tariff = 15p/kWh
Panels at Spikers Hill cost £10,000 and were paid off in about seven years |
Wind turbines
|
A 13kW Gaia turbine cost £30,000 in 2010
A larger 50kW Endurance turbine cost £250,000 in 2021 |
Good performance from both
A 20kW wind turbine produces three times the power of a 20kW solar system |
Big bills when things go wrong
Facing a £30,000 cost to replace blade holders
Relocation halved output on Gaia |
Gaia 22,000kWh/year
Endurance will produce about 190,000kWh/year
Tariff= 30p/kWh
Together they bring in about £70,000/year |
CHP unit
|
Installed in 2016 for £250,000
Heat is used to dry woodchip and grain through a vented floor
Runs 7,000-8,000 hours a year
|
Produces huge amounts of energy (350,000kWh/year) and not weather dependent
Both heat and electricity from gas produced from heating woodchips (pyrolysis) can be used by the farm |
On a bad day it can take all day to fix
Big outlay but quick payback of five years
Woodchip cost £40,000/year |
RHI = 640,000 kWh at 6.7p/kWh
Rocs = 350,000kWh at 9.5p/kWh
Can export power to grid at 15p/kWh
Produces about 90% of the farm’s renewable energy
Brings in about £80,000/year |
Ground source heat pump
|
Installed in 2019 for three holiday lets at Magdalen Grange for £30,000 |
Not much work
Very little visual disturbance
Constant, low-energy source
Heating costs reduced by 60% compared to original wall-mounted electric heaters |
Needs well insulated properties to benefit most |
Paid off in 10 years with RHI alone (10p/kWh)
But paid off in five years when factoring in the electricity savings |
Biomass boiler
|
Installed January 2010
Heats five properties at Spikers Hill, including farmhouse |
Only requires 500 bales of straw/year
Easy to operate, fill and maintain |
Higher installation cost than oil boiler, at £30,000 |
RHI = 9p/kWh up to 110,000kWh/year
RHI paid off investment in three years |