Dutch pig farm rises from the ashes of a devastating fire
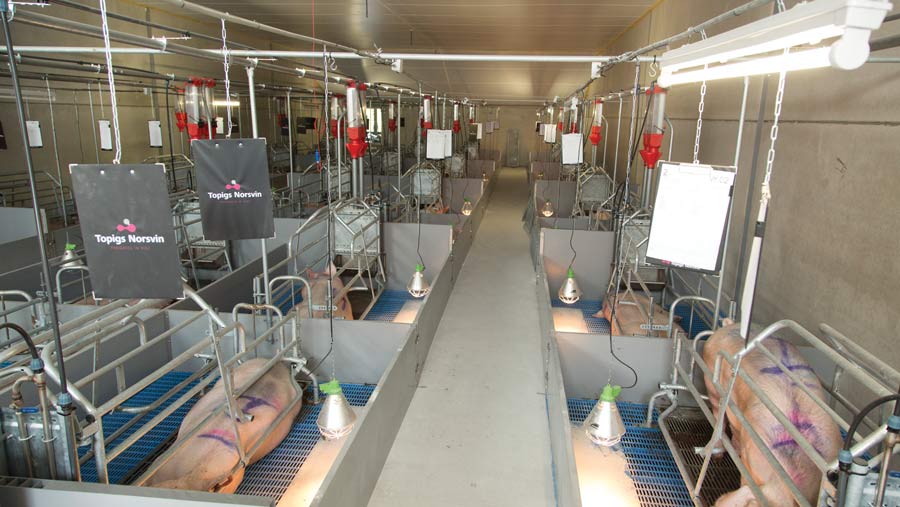
When a Dutch pig farm was devastated by fire in 2013, the owners rebuilt, creating a state-of-the-art, high-health, low-emission unit from the ashes.
More than half of Von Farm, Oirschot, owned by Kees van der Meijden and Wilma Welvaarts, was wiped out by the fire.
Despite the tragedy and shock in the aftermath, the owners refused to quit and decided to start from scratch, improving every aspect of production.
Seven years later the result is a 1,000-sow unit with 85% lower ammonia emissions, almost zero antibiotic use, saving €100,000 (£90,000) year in vet costs, and producing 33 piglets/sow/year.
Von Farm’s exemplary production standards saw it chosen as an ambassador unit on the pan-European EU Pig Innovation Group programme, led by the AHDB in the UK.
See also: A step-by-step guide to pig heats and insemination
Rebuild
The blaze was started by a spark in an air scrubber, located immediately behind sow and piglet housing. Flames spread quickly through the wooden buildings, which were razed to the ground within no time.
The speed at which the devastation occurred was shocking, putting fire prevention at the top of the rebuild programme.
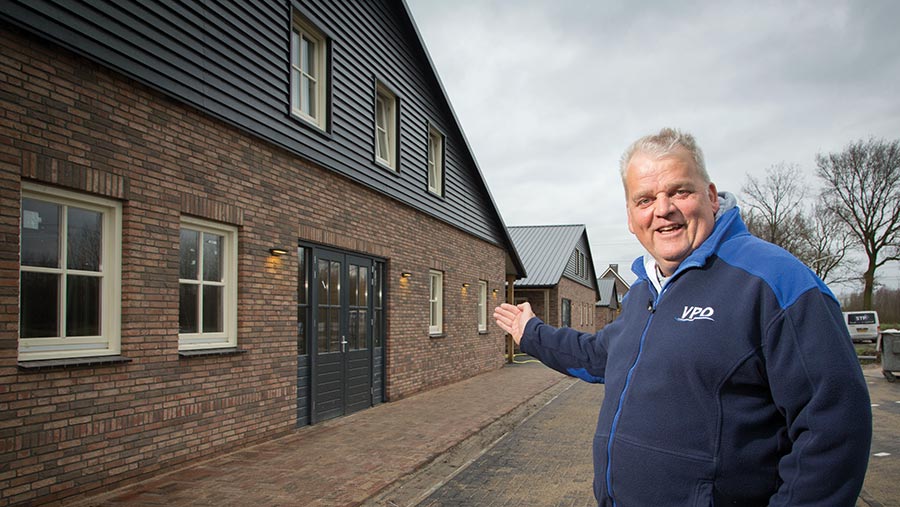
Kees van der Meijden © Mark de Jong
Fire retardant materials were chosen throughout the building process including, walls, slats, ceilings and all fittings. Mr Van der Meijden decided against available sprinkler systems because these did not operate until temperatures hit 58C at ceiling height.
Instead he and staff developed their own system that starts spraying water when temperatures rise by 5C within a 7sec period, a far quicker response.
Most of the animals that were killed, died of smoke inhalation and suffocation. In addition to the sprinklers, three ventilation units have been installed in farrowing rooms. These open automatically when the sprinkler starts spraying, safely venting smoke.
Biosecurity
Biosecurity has been reinforced and strict rules applied, with the unique addition of coloured zones.
The farm is divided into clean and dirty zones. Clean areas encompass livestock, equipment and feed areas, while the dirty zones include delivery roads, visitor entrances and stock-loading ramps.
A hygiene “air lock” has been created for visitors to shower and change before entering the unit and a registration process imposed that documents their recent movements.
Within the clean zone, strict biosecurity measures apply. No staff are allowed to move between separate livestock areas without changing overalls, while equipment never leaves its post.
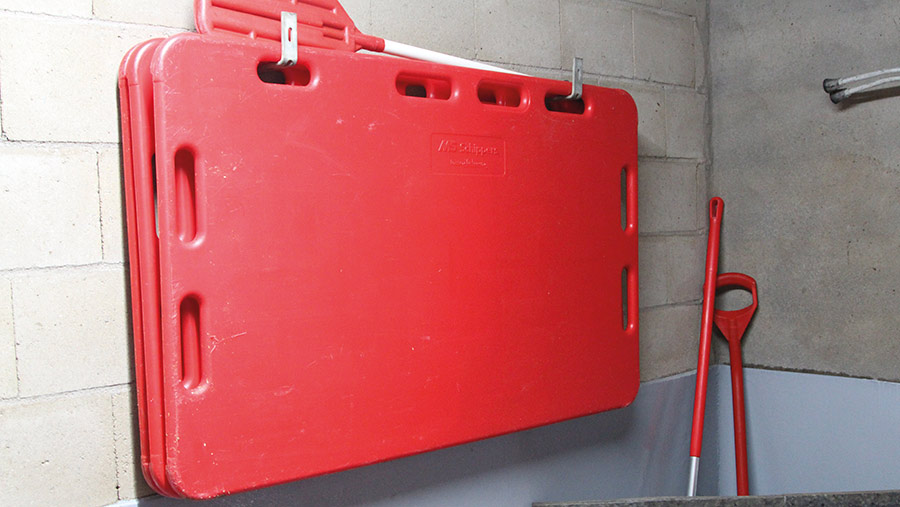
© MS Schippers
As a visual aid the flooring in each distinct zone is assigned a colour. Staff in each individual area wear overalls, PPE and boots which match the floor colour.
Equipment and tools are also painted with the matching colour which means it is immediately apparent if anyone strays from their work area or moves tools and apparatus.Â
Colouring in different zones:
- Sows: green
- Farrowing unit: blue
- Weaners: yellow
- Rearing unit: red
To remove any chance of cross-contamination vet treatments are chosen that can be administered without the use of syringes.
Training
A staff training and education facility has been built on the unit. Staff training manager Ruud van Loon explains that all staff undergo training in the importance of biosecurity and hygiene, so each member understands their role in minimising disease transmission.
A daily protocol and checklist, overseen by managers, underlines biosecurity and ensures tasks are completed and performed in a uniform way that limits the likelihood of disease transfer.
Cleaning and disinfection
Pigs are not mixed across age groups and the system has been changed to an all-in, all-out set-up. Downtime between batches is used for a rigorous cleaning procedure.
As well as using a degreaser, all organic matter is removed and the walls soaked. No disinfectant is applied until the house is completely dry to make sure the active ingredient is not diluted and remains at maximum efficacy.
Routine cleaning extends to the water supply. Biofilm build-up in the pipework is prevented through the use of chemical purification and this is backed up with routine microbiological checks to test for pathogens.
In addition, water is acidified to about pH3.4 to improve gut microflora.
Ammonia emissions
Mr van Loon says the farm understandably wanted to avoid using the same ammonia scrubbers that led to the fire, so needed to create a low-emission system without their use.
The business opted to use manure coolers to cut emissions. Temperature is one of the three key factors that affect ammonia release, along with pH and urea concentration in urine. Lowering the temperature of slurry therefore reduces the release of ammonia.
Each pen was fitted with a tray cooler connected via a series of cold water pipes to a central thermal exchange unit. Drawing the heat from beneath the pen reduces manure temperatures to between 12C and 15C.
The energy recovered from cooling the slurry is then used to heat the pig unit’s water to 35-50C. The trays also cool incoming air, providing a steady 18C at stock level for the sows, which helps reduce the transmission of disease.
Because ammonia is removed earlier from the system, air quality around the stock is improved. The result is fewer cases of respiratory disease, which has cut antibiotic use to almost zero.
Production, costs and savings
The combined benefits of all these changes have boosted performance and cut costs. Pigs are reaching slaughter three weeks faster, output has lifted and mortality has been reduced.
Meanwhile, veterinary costs have dropped from €130/sow/year (£120/sow/year) before the fire to just €30/sow/year (£27/sow/year) or €100,000 (£90,000) a year across the unit and the heat recovery has cut energy bills by €12,000/year £10,750/year).