Slurry separator eases sand-bedding burden
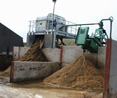
The benefits to mastitis prevention and cow comfort from using sand in cubicles make it a viable option in the fight to decrease cell counts. But the practicalities in terms of handling sand-filled slurry when it comes to muck management can seem too much of a burden for the wider system.
Sand bedding not only improves cow comfort, but also minimises teat-end exposure to mastitis-causing pathogens. And, with environmental mastitis becoming more prevalent in dairy herds, management methods which cut the incidence of these pathogens are key tools.
Sand clogs pipes, fills slurry storage ponds and wears machinery used for both spreading and pumping liquid, says Peter Russell, managing director of Midland Slurry Systems and responsible for installing the system at Robert Horton’s 350-cow dairy unit in Wiltshire.
“We often hear horror stories of pumps lasting one week because of having to deal with sand,” he adds. But by teaming up with McLanahan Corporation, which makes sandmanure separation (SMS) machinery originally designed to wash impurities from sand and gravel during mining operations, Mr Russell believes SMS systems are robust enough to cope with sand burden.
The system works on the principle that sand is heavier than both organic material and liquid, and hence harnesses gravity to do the heavy work, rather than requiring extra power.
The auger is continually fed at a slow rate, with sand-loaded slurry from the reception pit (see diagram). “What we want to produce are three materials, all with economic benefits to be directly transferred to the farmer: Liquid which can be pumped, solids which can be stacked and sand that can be reused in cubicles.
“We anticipate sand recovery to be 75-80% at its lowest and have results to suggest 95% is achievable, relatively soon after installation,” he adds. It can be anywhere from a week to a month before sand goes back into cubicles, he adds. “When supplies of sand are tight, it can be taken directly from the chute and spread thinly on cubicles.”
A key factor in the process is moisture content, as the drier the consistency the more wear on key components. But there is a fine balance, Mr Russell believes. “The crucial part of the process is having about 36,500 litres of clean water available to be pumped into the bottom of the SMS, which can be pumped back in from the lagoon.”
The separator can deal with 18,185 litres/hour from the 350 cows, which means running two 5hp motors five to six hours daily.
Payback on the investment takes into account not only the savings made in replacing sand in cubicles, costing ÂŁ16/t and amounting to more than ÂŁ20,000 a year, Mr Horton adds. “Previously, we have relied on contractors to spread dirty water, which cost about ÂŁ20,000, but this is now done entirely through irrigator pumps.
“We are working on a four-and-a-half-year payback, just in terms of sand savings. However, this doesn’t take into account the knock-on effects of installation, such as less compaction, reduced time spent managing muck and a higher fertiliser value of what is spread.”
The system has now been in place for more than five months and there have been no serious problems or changes to the initial system, adds Mr Horton.
Maintenance is all included in the service package, but Mr Russell highlights the simplicity of the system and parts used. “Most things can be fixed by operators relatively easily and there are only a couple of weekly greasing points.”
emily.padfield@rbi.co.uk