Rotary parlour saves time and cost
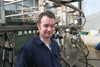
Making the decision to change milking systems is never easy but for a Cheshire dairy farm building a new rotary parlour has paid dividends. Andy Collings reports
When it comes to milking systems, the rotary parlour still retains a certain mystique – despite it having been used by dairy farmers throughout the world for several decades.
The concept of a rotating carousel on to which cows obediently step aboard to be milked and then, after a full rotation, step off, is for many too far removed from traditional herringbone systems to be seriously considered.
In the UK at least, the rotary concept remains a niche system. But as herds become larger and the income derived from milk (hopefully) continues to increase, it is the rotary parlour which is now receiving more than a wishful glance from an increasing number of dairy farmers.
For Riverside Farms, based at Byley, Middlewich, Cheshire, the drudge of spending five hours at each end of the day milking 250 cows through an 18×18 herringbone parlour was not considered to be sustainable.
“The time it was taking two of us to complete the milking was just too long,” says farm partner Andrew Shaw. “It got to the point that even the dog didn’t know who I was when I came home.”
The decision to invest in a new rotary parlour was made after considering the options that were available.
Any extension of the existing parlour was out of the question – the room was not available which meant that a new start had to be made on a fresh site – whatever system was selected.
“We thought about installing a 30×30 herringbone and I went and saw one but when I discovered just how long they actually are, and the distances we would be walking as a result, I was not encouraged,” says Mr Shaw.
“Our feed system also requires the cows to receive concentrate in the parlour and I was not convinced that having this number of feeders was going to work – we have enough to do looking after the milking without having to worry about feeder operation.”
What eventually clinched the decision to go for a rotary parlour was the discovery that, in terms of cost, a suitably sized herringbone was not going to cost that much less to build or run.
The site chosen for the new rotary parlour, which was to be supplied by Crewe-based dairy equipment provider Green Oak, called for the demolition of two barns and the linking of the new building to an existing barn which would provide the collecting yard area.
With the old barns cleared to ground level, work began on the erection of the new building which would house the parlour. This was specified with galvanised girders and a roof which had ample areas of clear plastic to provide a light and airy working environment.
A shutter door through which a loader could gain access to the carousel was also installed to allow the removal of a cow that might have gone down while on the milking platform.
“It’s not a pleasant thought but it was something we had to make provision for,” explains Mr Shaw.
Meanwhile the construction of the focal point of the new building was also under way – the large circular pit in which the carousel would be placed.
“We had to excavate down to more than 1.5m below floor level which could have led to drainage problems – some installations have to use a pump to remove washing water – but we were lucky in having quite a steep fall on one side of the building which takes the liquids to the slurry lagoon,” he says.
The sides of the pit were constructed from glassfibre-reinforced concrete using shuttering – which was about two-thirds the price of using pre-cast sections – and set in the middle of the concreted floor was a central “pin” which would become the pivot point for the carousel.
With the pit and surrounding floor completed, the metal work for the carousel arrived and was assembled. The platform runs on a rail supported by a series of nylon rollers, each of which is designed to take a load of over 10t.
Drive for the rotation is supplied by a hydraulic motor which can, if electrical power fails, be operated from a tractor’s hydraulic system to allow cows to exit the platform. Rotation speed is about once every ten minutes but this can be adjusted by the herdsman to suit the speed of milking.
Mr Shaw opted for a parlour that could hold 44 cows at a time and also one where the operator stands on the outside to put the milking machines on the cows. There are versions where the cows are milked from the inside of the parlour.
For concentrate feeding, feed is delivered from a single point to each cow as it passes beneath. Individual cows are recognised and given a measured amount of feed to match yield – 1kg of feed is delivered in one second so control is via a timer.
Two weeks after the start of the carousel build it is ready to have the vacuum lines, milk lines, milking clusters, pulsators, automatic cluster removal, teat spray, recording systems and all the other equipment required by modern milking parlours installed.
“We decided to retain our existing milk tanks and cooling systems,” he explains. “But this meant piping the milk under the roadway to the where the tanks were if we had put the pipes overhead someone, somehow, would have managed to knock them down.”
Power for the new parlour needed to be three phase, which the farm does not have. Instead, a diesel powered generator is fired up each milking time. “It’s not very satisfactory, particularly with the price of fuel, but the cost of putting in three phase is pretty prohibitive,” he says.
Five months after starting the project, the parlour was ready for its commissioning.
“The first milking was a stressful occasion for the 11 of us who turned up to help and also for the cows. It took about five hours to complete and the amount of milk was pretty dismal – as you could expect. Every cow had to be cajoled to step on board – all 250 of them.”
Even so, after just three days calm had returned and the cows became settled – more so than they have ever been, comments Mr Shaw.
“Milking time has been cut to a leisurely two hours, including a tea break. As a result, there is so much more time to actually manage the herd – rather than just milk them,” he insists. And the cows really are more settled. They step on board when a space arrives, the teats are cleaned and the cluster attached – and that’s it. When the milk flow reduces to a pre-set amount, the clusters are automatically removed and the teats sprayed before the stroll off.”
In terms of operation, the system has been pretty trouble-free apart from a few teething problems that perhaps could be expected.
Mr Shaw points out that the system has resulted in lower labour costs and easier milking – the cows come to you rather than you having to walk miles up and down a dimly lit sunken pit. It has been relatively easy to find relief milkers prepared to work on alternate weekends and cover holiday periods.
“Overall, I am convinced we made the right decision to invest the ÂŁ250,000 we have into this project,” he says. “We can now increase our cow numbers to the 500 we plan to have – and still milk them in an acceptable time frame. And when I get home in the evening, the dog still knows who I am.”