New rotary parlour doubles milking throughput
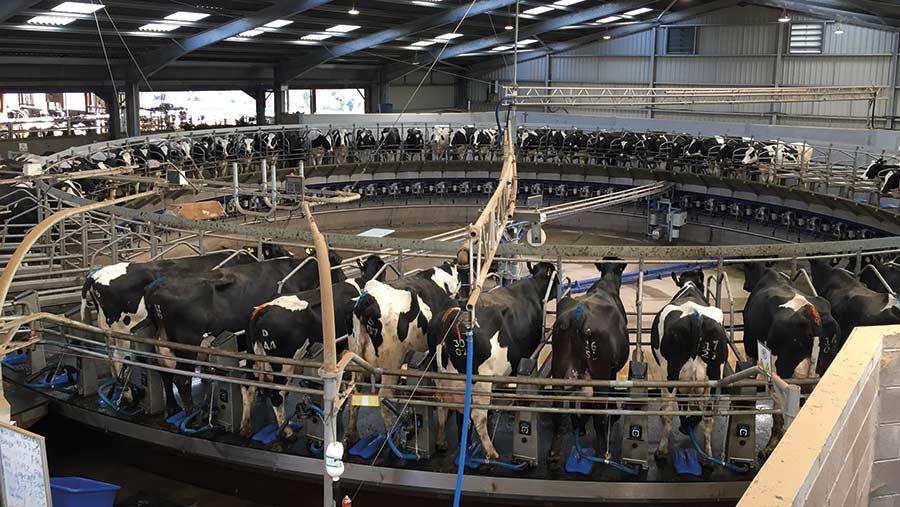
Installing a new parlour has halved milking times, improved cow comfort and increased milk yields by 1.5 litres a cow a day at Manor Farm in Somerset.
The farm installed a 70-point DeLaval rotary parlour last year as part of a wider ÂŁ3m investment in facilities.
These included 600 new cubicles, six concrete-panelled silage clamps and a new clay-lined slurry lagoon and sand separator to aid with herd expansion.
They were part of a complete system overhaul over the past decade, with the farm switching from an autumn-calving, grass-based, organic setup to a fully housed system, milking three times a day.
During that time, milking cow numbers have increased from 350 to 750, explains Velcourt farm manager Ross Edwards.
See also:Â How to light dairy parlours for cows, staff and milk quality
Farm facts
- Milking 750 cows plus youngstock (1,200 in total)
- 405ha (1,000 acres)
- Farm is owned by Radstock Co-operative and managed by Velcourt
- Renting a further 28ha (70 acres)
- Predominately Holstein-Friesian cows with one generation in four served to Brown Swiss to add hybrid vigour
- Milking three times daily
- Cows averaging 11,400 litres at 3.85% fat and 3.2% protein
- Milk sold to Muller/Co-op
The 405ha (1,000-acre) farm is owned by Radstock Co-operative and made the move to “sweat its assets”, explains Mr Edwards.
“There wasn’t enough livestock to saturate the assets. The farm is heavy clay which meant the grazing season was relatively short, too,” he adds.
About the parlour and key features
The parlour replaced a 16-aside GEA rapid-exit system and has been housed in a new building that also contains the collecting yard, a farm office and a 40,000-litre milk silo.
A rotary parlour was chosen to speed up milking times and future-proof the business, with the size allowing for further expansion, should this be required in the future.
It is thought to be the first parlour with an inward-sloping deck to be installed in the UK. This was an attractive selling point for Mr Edwards.
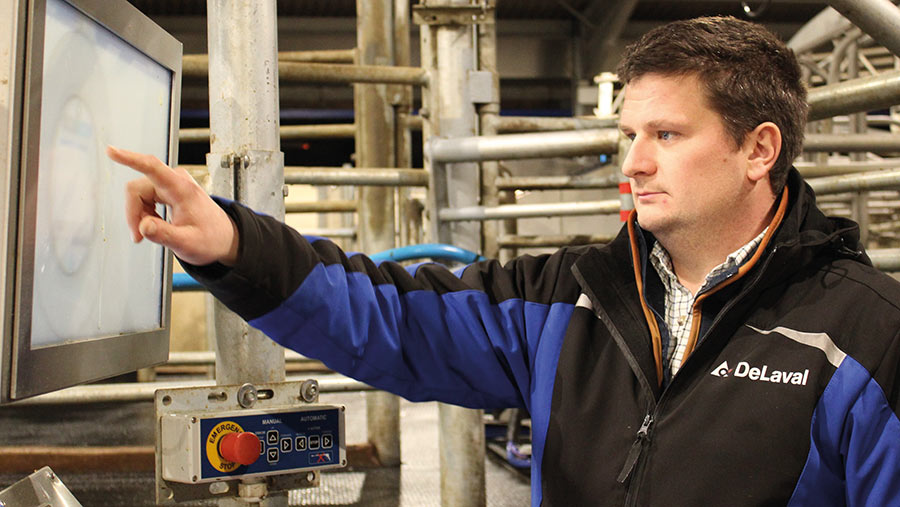
Ross Edwards © Agribusiness Communications
“It is hard work washing muck uphill, and when you’re milking you don’t really want water running back down your legs,” he explains.
“It’s improved operator comfort and because the cows are standing downhill their udders stand out, making it easier to attach the units.”
Another asset of the E300 model is the bail design, which sits at 15deg as opposed to 90deg. This helps the cows exit the rotary more easily, Mr Edwards reckons.
Another feature he really likes is the robotic teat sprayer, which the team has nicknamed Tessa.
This addition has meant they haven’t had to increase the number of milkers required from the previous two, with one wiping and one putting the units on.
“She [Tessa] is reliable and doesn’t need any holiday. She only misses 3-5% of cows, which are mainly cows that stand really awkwardly [in the bail],” says Mr Edwards.
The parlour contains a touchscreen “cockpit” which allows the operator to control each stall and cow individually using electronic identification (EID).
This means cows can be automatically segregated for treatments, for example.
“We had EID before in the old parlour but if a cow came in and backed out it would muck up all of the yields because it wouldn’t recognise that cow [again on re-entry].
“Now, the EID tag is read, a camera checks the cow is in the stall and re-reads the tag.”
It’s also a “foolproof” way of identifying cows that need extra attention – those with higher cell counts or fresh calvers – with all of this flagged up on the screen, says Mr Edwards.
“If you’re worried about mastitis, it will double-check that cow is OK, and it will also tell you if the cow is producing less than 80% of her expected yield.”
Teething problems
One thing that Mr Edwards would change, if he could build the parlour again, would be to increase the drainage capacity in the washroom.
“I only put in a four-inch drain in the washroom and I should have gone bigger. When the circulation wash is going through the parlour it’s not quite big enough to take the volume of water, but it doesn’t cause us any issues really.”
Multiple benefits
Completion took 13 months from knocking down the old building to the first cows being milked in August, although Covid delayed things slightly, admits Mr Edwards.
Since completion, milking throughput has increased from 140 cows an hour to 300 cows an hour.
This has reduced milking times from five hours for each milking – a total of 15-18 hours/day – to just 3.5 hours a shift from start to finish.
Milk yields have edged up by 1.5 litres a cow, but Mr Edwards is hoping this will continue to improve as building work is completed and cows settle into their new environment.
“Cows are definitely more content because they are only being disturbed for three hours and are not standing about for as long,” says Mr Edwards.
Teat condition has also improved thanks to the Evanza cluster, which has a clover-shaped liner, adds Mr Edwards.
“Probably one of the biggest benefits is fewer [cluster] knock-offs. It was about 10% before but now it’s less than 1% so the cows are definitely a lot more comfortable when they are being milked.”
Future
No further expansion is on the immediate horizon. Instead, the focus is going to be on honing all the basics, says Mr Edwards.
“The target is to do 100 things 1% better. We have the facilities, it’s about maximising production and health.”