How two dairy farms achieved a better work-life balance
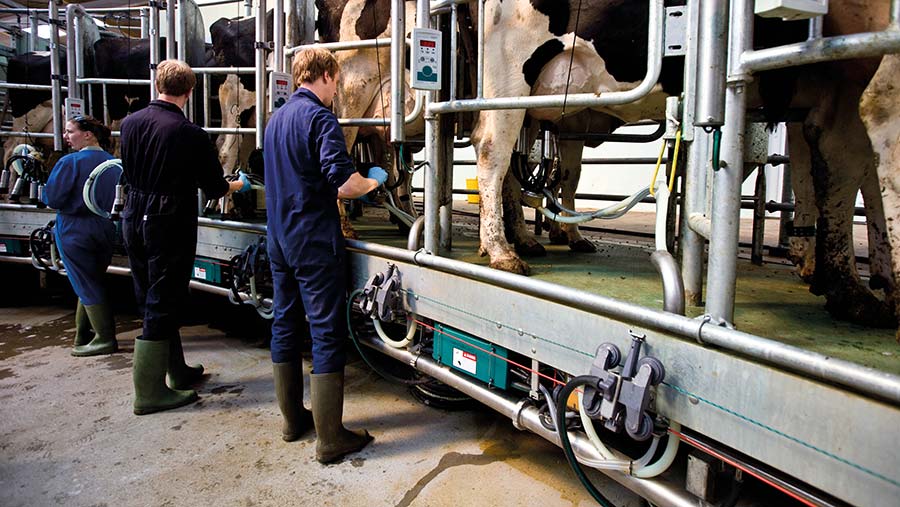
Work-life balance will mean something different to everybody. There are some who will scoff at the term while, for others, it is a key part of business management.
With the ongoing challenge to secure and retain good labour in the dairy sector, it is an area some farms have been looking at – for employees and themselves.
Becki Leach, head of people at Kite Consulting, says the main stumbling block for many farmers is the cost and complexity it can add to the system.
See also: How 10 in 7 milking helped work-life balance and cow health
It usually means employing more staff to allow for different shift patterns and reduced working hours, which increases overheads, and looking again at rotas, which requires management.
It can also mean simplifying systems so protocols are easy to follow for larger teams. Therefore, farmers will only make it work if it is a core objective of their business.
Effect of poor work-life balance
Ms Leach says it is worth considering the effect of a poor work-life balance on productivity because the cost of poor labour is not just in the wages bill – technical mistakes have a cash cost to the business, too.
“If you look at your typical dairy shift pattern of 55-60 hours a week, it’s very hard to be productive for that level of time for 48 weeks a year, if we’re giving them 28 days’ leave.”
When it comes to the farm owner, improving work-life balance may mean recruiting more senior staff and delegating responsibilities to them.
We look at two farms that have effectively integrated flexibility into their working patterns.
Case study: Flexible shift patterns – Dourie Farming Company
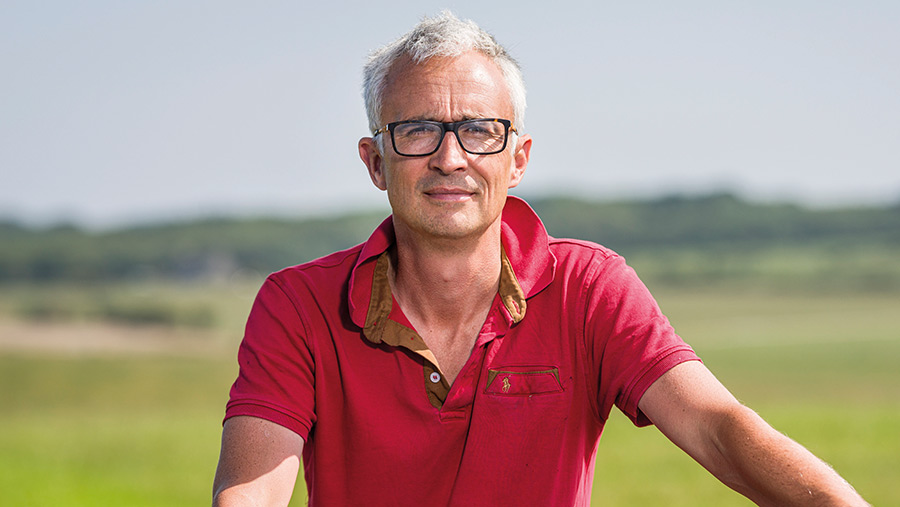
Rory Christie © Judith Armstrong
Farm facts
- 900ha (2,234 acres) in Wigtownshire
- Milking 1,100 cows
- Spring-block calving
At Dourie Farm, the Christie family offers staff flexible shift patterns to improve employees’ work-life balance and attract strong candidates to their roles.
“There is no doubt that the industry needs a better work-life balance.
“I often live in a constant state of anxiety due to the pressure of being a dairy farmer, and having great difficulty finding good labour increases that,” says Rory Christie, who runs the farming business alongside his brother, Gregor.
When recruiting, they offer a potential pattern of four days on, four days off, or even an “oil rig-style” eight days on and eight days off.
However, it can be challenging to find the right people to make this work because they need to be able to learn the job between extended periods off rota.
It is also not for everyone because making income stack up for employees can be challenging in non-salaried roles.
“What we are currently finding is that most people enjoy is a 10-four rota, which is four days off within 10,” says Mr Christie.
“There are not many folk that’ll work 12 days on, two days off, nowadays. The truth is you have to be flexible – interview them and find out what they want and need.”
The expectation when working six days in 10 is that an employee would generally do 40 hours a week.
Top tip: Consider different shift patterns to suit different employees. Crucial to making this work is having well-organised rotas.
“Hours will stretch for six weeks in February-March when we are calving, but 48 hours is enough. The working time regulations were made for good reason,” Mr Christie says.
He does not pretend management is simple – rotas can be complex, with the equivalent of 13 full-time staff on varying shift patterns, especially to manage continuum.
“It requires organisational management skills, which we have got – we have an extremely able ex-navy farm manager.”
The other thing Mr Christie does to improve work-life balance is help all his team find good homes to live in and integrate socially, introducing them to clubs such as rugby or Young Farmers, so they can enjoy time off-farm.
“I don’t want people just to work here, I want them to live here – their happiness is important to us,” he says.
Top tip: Help younger staff make the most of their time off by having a plan for pastoral care, which includes social opportunities in the local area.
Case study: Changing the farming system – Hollings Hill Farm
Farm facts
- 200ha (494 acres) in Herefordshire/Worcestershire
- Milking 350 cows
- Calving year-round
Austin and Faye Knowles have “worked every hour of every day” for decades and are now adjusting their system to relieve pressure and free up time to spend with family.
“We are trying to get a better work-life balance. We are not there yet, but we are not giving up on achieving it,” says Mr Knowles.
The first change at Hollings Hill Farm, spurred on by staff loss and a large TB outbreak, was dropping milking from three times to two times a day and reducing cow numbers.
However, each milking now takes longer and, while the rush for lunchtime milking has gone, the system has elongated the day.
Top tip: Get a good herdsperson to take pressure off the business owners.
Therefore, the Knowleses have to decide between putting in a larger parlour to decrease milking times, which would mean increasing the herd size to service the debt, or reducing herd size even further.
Cutting cow numbers will allow the couple to spend more time with their four children, and create a business wit a range of options that is attractive for the next generation, rather than being restricted by scale and debt.
“The challenge now is profitability, but at what point is profit more important than work-life balance?” says Mr Knowles. “There’s got to be a balance.”
Five months ago, they employed a full-time herdsperson, which has given them more time off farm.
They also use professional advice to improve staff management, and this has included personality profiling across the team.
All the people on the farm have got to buy into what you are trying to achieve. Mutual respect is key – if everyone gets on, we can teach the technical skills,” says Mr Knowles.
Top tip: Only retain staff who fit with the farm system. Employees need to be team players first and foremost and support the farm’s goals.