How self-feed silage allowed autumn-block herd to expand
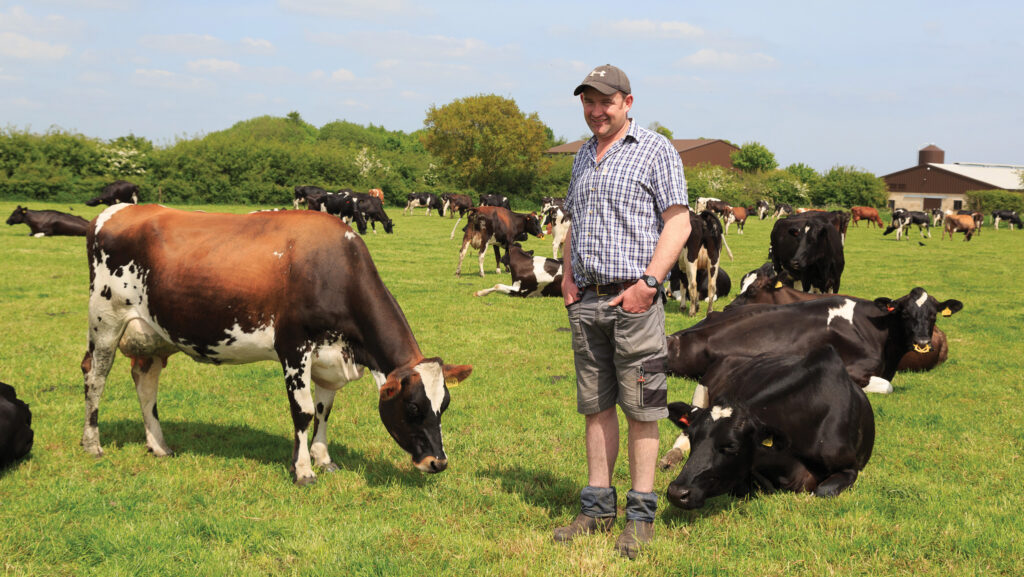
An autumn block-calving herd has moved to a new site on farm, replaced a mixer wagon with self-feed silage and increased herd size by 120 cows.
Cost of production for the setup – which achieves 54% milk from forage – is 32p/litre, based on a milk price of 40p/litre.
“We needed to reinvest to stay in dairying,” says Ben Walker, who farms with his brother, Tim, and father, Ian, at Attleborough Hall Farm in Norfolk.
See also: How to decide if autumn block calving is right for your farm
The £2.9m project has delivered a 300-cow unit on a greenfield site in the centre of the grazing platform, yet close to a road, electricity and water.
The building project took 240 days, from breaking ground to milking cows on 23 October 2023.
It replaces a 25-year-old parlour that used to milk 180 cows in outdated buildings and is now earmarked for conversion to office lets and light industrial use.
Farm facts: Attleborough Hall Farm, Norfolk
- 300 crossbred cows averaging 555kg milk solids
- Autumn block-calving herd
- Average yield 6,959 litres at 4.9% butterfat and 3.8% protein
- Average 4.5 lactations
- Average mastitis rate of nine cases in every 100 cows a year
- Replacements bred on farm; dairy beef calves sold to two local farmers
- Milk supplied to Arla, with vending machine for sales to local community
- Winter wheat, winter oilseed rape, spring barley, sugar beet, and 40ha maize for silage
The crossbred herd is free of leptospirosis, infectious bovine rhinotracheitis and bovine viral diarrhoea and unvaccinated.
Ben had been keeping replacement heifers in preparation for the expansion, but also bought in 100 cows and heifers, sourcing stock with similar health status from Antony Adorian’s herd in West Sussex.
Self-feed silage
There was a further advantage in sourcing cows from Antony.
Ben describes him as “the god of self-feed silage” and had visited his setup (as well as several others) in the run-up to building the new dairy.
Ben opted for self-feed silage at the new unit to drive down costs.
Cows have 24/7 access to the clamp. The feed wire is set 91cm above ground in front of the 60m-wide silage clamp and is moved forward by 150mm/day.
Wheat feed is layered in grass silage in the clamp, and maize with added rapemeal is put on top. This is also done for heifers, who feed from a separate clamp.
Calves are trained onto their own self-feed (grass) silage from 12 weeks. This ensures they have already learned the system by the time they are bulling heifers and maximises fertility.
“It’s gone really well – there is less reliance on machinery and labour now.
“It took the cows a while to adjust as they were not used to eating over a wire [as well as under it], so we’ll have lost milk this winter.
“But they are now trained – the cows from Sussex showed them how,” says Ben.
Activity monitors in ear tags fitted the winter before last have done away with night checks and midday checks for bulling.
“We swear by them: we don’t do any physical checks now and rely on them totally. Submission rate previously was 75% – now it’s 90%,” he adds.
Dry cows strip-graze standing hay and mainly calve outside, with heifers integrating into the herd on the calving paddocks.
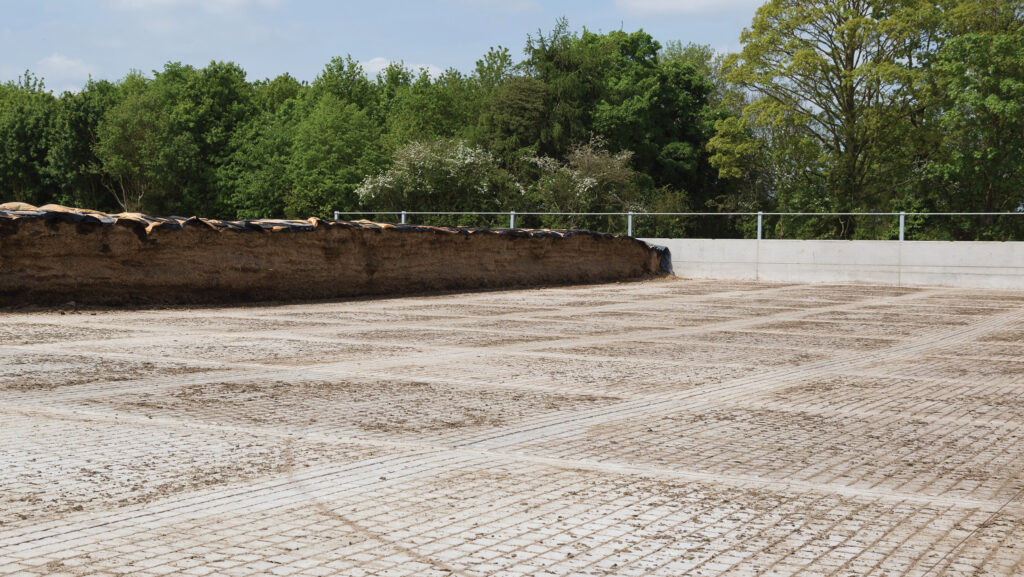
Self-feed silage clamp © MAG/Judith Tooth
Winter housing
Housing is in 320 wooden cow kennels chosen because “it was a third the price of a steel-framed building”.
“We only house for five to six months so all the woodwork has a chance to dry out. The building has a 25-year life expectancy, but I think it will do longer,” adds Ben.
The kennels are on a chalk base, bedded with deep straw which is topped up three times a week using a straw blower.
There is a separate 80-kennel building for heifers, and a youngstock building complete with calf kitchen, set alongside their respective self-feed silage clamps.
Heifer kennels are set at 1m spacings, 20cm narrow than for cows.
Next to them is an open yard with a line of self-locking yokes where concentrates are fed each morning as bait, which helps with artificial insemination.
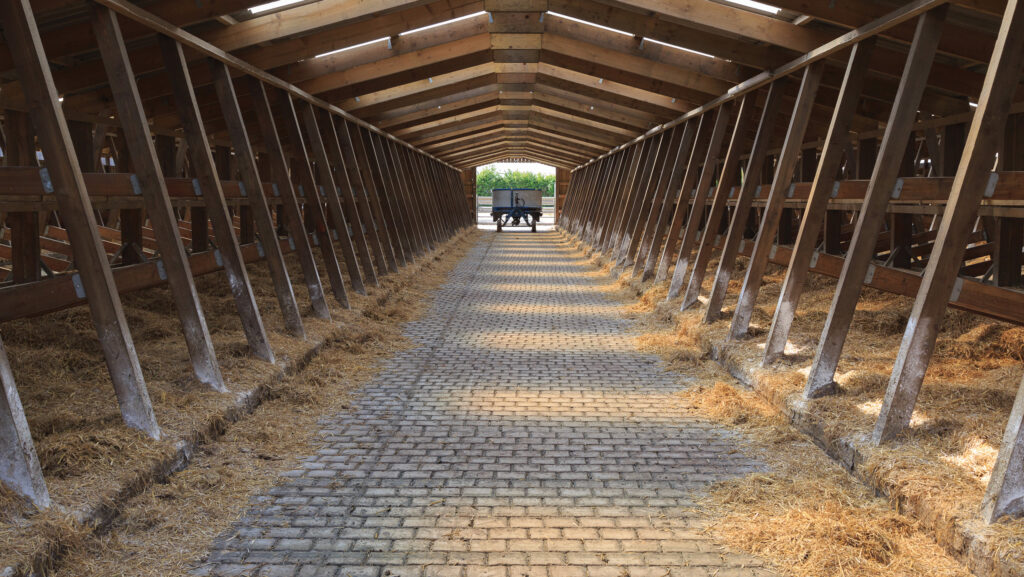
Wooden cow kennels were chosen for their competitive price © MAG/Judith Tooth
Muck and slurry
Muck is pushed into a 4,500cu m slurry lagoon, while dirty water and rainwater harvested from the dairy unit’s roofs go into a separate 15,000cu m lagoon.
“The aim is to keep as much liquid as possible out of the slurry lagoon, so [the material] is quite solid,” says Ben.
“Some goes on the maize ground with a muckspreader ahead of drilling, with the balance on arable stubble after harvest.”
Dirty water is used to irrigate grass paddocks via a 90mm ring main and Roto Rainer irrigator.
This delivers the equivalent of 5-50ml rainfall, depending on the speed of the irrigator across the paddock.
Milking parlour
The milking parlour is a “nice and airy” Delaval 26/52 swingover with automatic cluster removal and milk meters, but no automatic identification and a simple flat-rate feeding system of an 18% cake at an average 4kg/day.
“Limited electronics means there’s less to go wrong,” reasons Ben, who employs two full-time dairy staff, plus relief staff over winter.
One person can milk 12 rows of milkers sensibly in 2.5 hours.
An automated backing gate keeps cows moving forward in the collecting yard, however, he says in practice this is only needed for the last two or three rows and when calving heifers.
A square-print barrel roller was used to produce a smooth and level, but grippy, surface for the concrete flooring (across the site).
Cows exit via a formalin footbath every weekday morning, up from three times a week to tackle an increase in lameness caused by the acid in the new concrete. Ben is confident this will settle down in time.
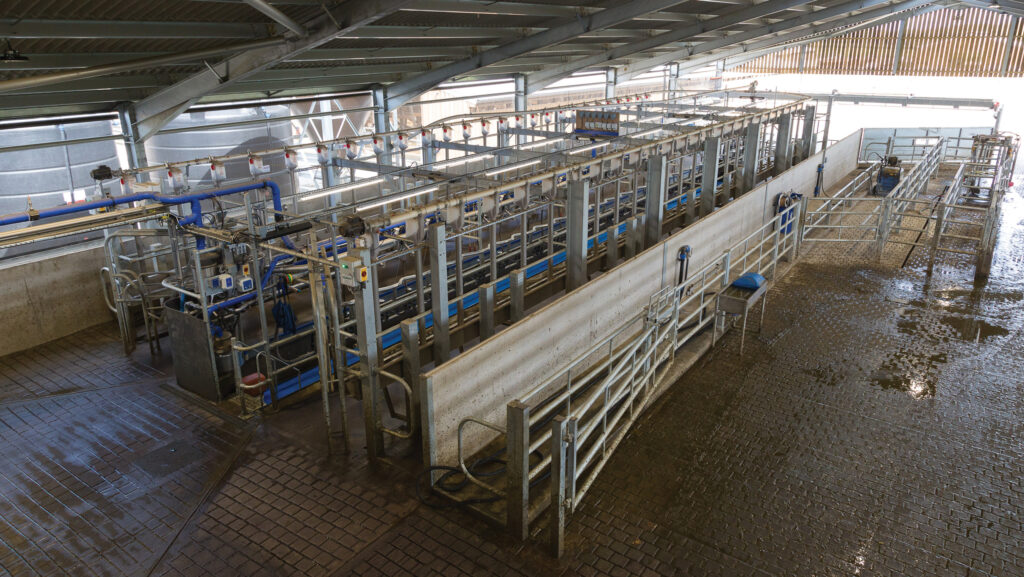
The farm opted for a Delaval 26/52 swingover © MAG/Judith Tooth
Grazing platform
To produce enough grass for the larger herd – and to replace 21ha (52 acres) of grassland sold for housing development to fund the new dairy unit – 75ha (185 acres) of the farm’s heavier land has been taken out of arable production over the past two autumns.
The total grazing platform now stands at 109ha (269 acres).
“The sale of land covered the project cost, but we could have justified borrowing on a 10-year to 12-year payback depending on milk price,” says Ben.
“We created our own seed mix using four varieties from Recommended Lists – one mid- and one late-heading diploid perennial ryegrass (PRG) and one mid- and one late-heading diploid PRG.
“Then we sprayed for weeds and stitched in white clover using a harrow and seeder box, and some direct-drilling.”
Ben plans to stitch in other species in the autumn to qualify for the £382/ha payment for herbal leys under the Sustainable Farming Incentive.
“We have to make good-quality forage for an autumn block, as cows hit peak milk while we’re feeding them.
“We’re working towards a multicut silage system to maximise grass quality and aim to cut maize at the optimum time – we want as close to 32% dry matter as possible and select varieties for starch production.”