How an Indonesian dairy will expand to 3,500 cows
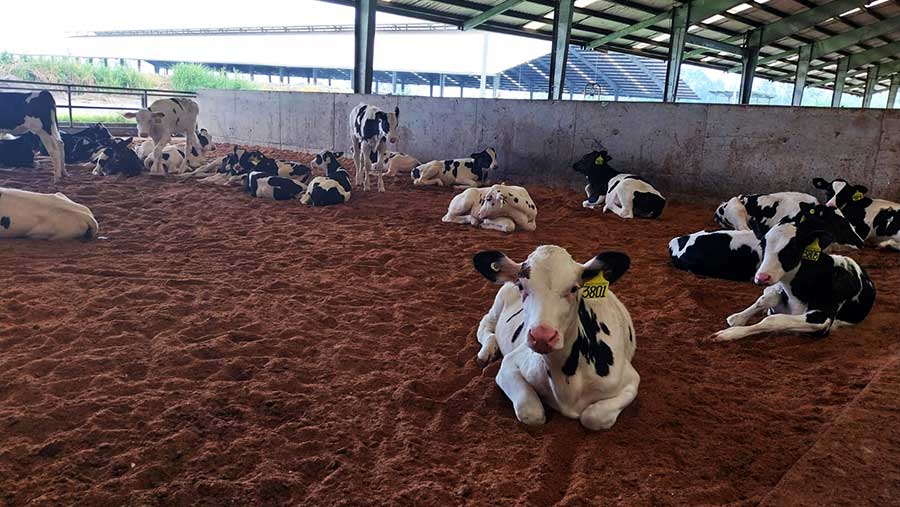
A British herd manager is overseeing the strategic expansion of a 1,900-cow farm in Indonesia, adding two new barns with close to 1,000 cow spaces and a 90-point rotary this year.
Herd manager Brendan Wilkins has managed Ultra Sumatera Dairy Farm on the island of Sumatra since October 2020 during a critical expansion period.
The herd was started in 2019, when 2,000 head were imported from Australia.
The aim is to reach 2,900 cows by 2026, with the 90-point rotary being big enough to eventually support a 3,500-cow dairy.
See also: A guide to mitigating heat stress in housed cattle
The current performance is as follows:
- Average herd yield is 27-32kg/day, with a long-term goal of 35kg/day
- Peak cow groups total 42-44kg/day
- First-lactation heifers are housed separately and have given 32-35kg/day this year.
Farm facts
- 1,900 Holstein-Friesian cows
- 1,600 youngstock
- Conception rate of 27% and pregnancy rate of 15%
- Average daily yield is 27-32 litres
- 50p/litre milk price for three years – Ultrajaya is a premium UHT milk
- Milk is powdered on farm and shipped to the island of Java and processed into UHT at Bandung near Jakarta
- Cows bedded on recycled manure solids
- Uses six-row barns and a herringbone parlour
Dairy demand
Analysts predict the collection of 17,500 islands known as the Republic of Indonesia, and home to 274 million people, will see compound growth in dairy demand of 6% by 2026.
The dairy is owned by Ultrajaya, the premium UHT milk brand in the region.
UHT and flavoured UHT milk are the company’s main dairy products because of the warm climate and the lack of refrigeration in the supply chain.
Large-scale dairying was introduced to Sumatra by Pak Sabana, Ultrajaya’s owner.
Harper Adams graduate Brendan Wilkins was brought in partly because of his experience of working in challenging climates in Vietnam, Thailand, Malaysia and at Almarai dairies in Saudi Arabia.
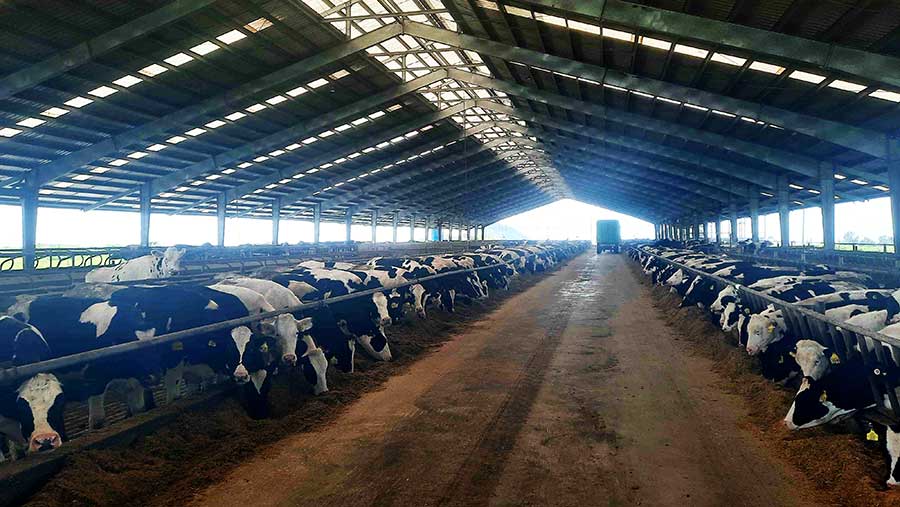
The current youngstock shed at Ultra Jaya © Ultra Jaya
Challenging climate
The farm gets 2,600mm of rain a year and temperatures range from 13C to 30C. February is the driest month with 119mm of rain.
Humidity (85-90% year round) costs at least 1kg of milk a cow a day, says Brendan.
“The temperature humidity index costs us even more in fertility,” he admits. “Our pregnancy rate is around the mid-teens.”
Rainwater is collected and used to flush the passageways, keeping flooring clean and saving on labour and automatic scrapers.
Forage
European grasses do not thrive on the island, but fibrous grasses (Odot and Napier, or elephant grass) are harvested at mature stages as dry cow and youngstock feed.
The native grasses also have surplus effluent spread on them after slurry is recycled for manure bedding, says Brendan.
Maize grows year round and is the main forage, sourced from traders that buy it from local farmers.
The narrow, rough roads and fields mean a forage harvester cannot be used.
Instead, maize is loaded onto a conveyor belt to be fed into a static forage harvester and ensiled on the farm. The farm processes about 150t/day of maize this way, with milking cows eating 22-45kg/day.
Hay is imported from Australia and Italy. A shipment of Italian new-season alfalfa currently costs £438/t to get to the port near Medan, 70 miles away.
More land will be acquired to grow crops for the larger herd, but land deals on the island are very secretive, says Brendan.
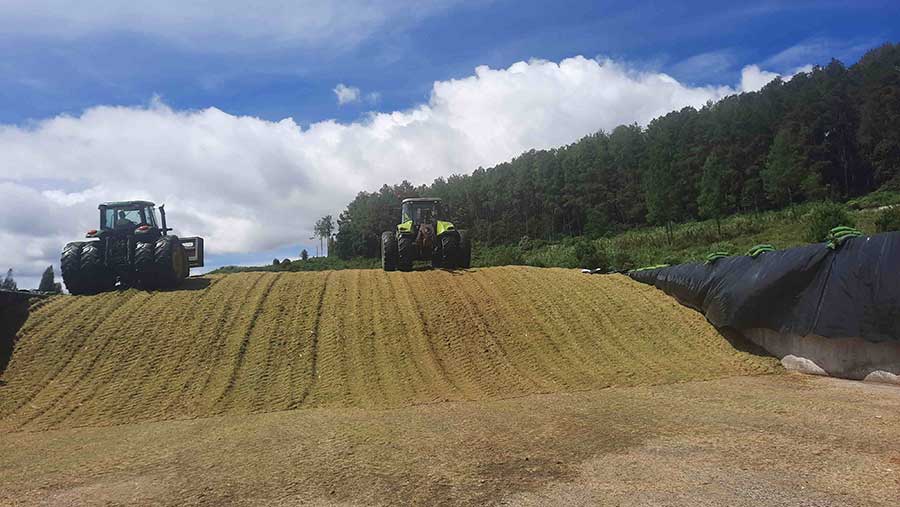
Maize being consolidated in the clamp © Ultra Jaya
Herd manager role
The dairy is seeking a herd manager as an eventual replacement for Brendan Wilkins when he retires.
Applicants must speak good English and have experience in artificial insemination and herd health. They can find Brendan on LinkedIn.
People management
The site employs 163 in total across the dairy, milk powder plant, cropping, administration and construction enterprises.
Brendan manages the team using the following principles:
- Training All jobs have written standard operating procedures. Farming in an isolated location means vet, insemination, machinery maintenance and parlour repair work are all done in-house.
- Delegation Cropping, farming, construction, and administration are all distinct departments, each managed by a graduate. Department heads run specific operations (for example, calf rearing and milking feeding). Brendan delegates a large amount of control to department heads because this gives a clear line of responsibility and empowers them within their own area.
- Communication Department heads attend a monthly performance review. For example, the milking team head reports on on milk recording results, yield, butterfat and daily income figures to all the other department heads.
At the end of the meeting there is an open discussion on the month’s results and suggestions for improvement.
Technology
The key software packages are as follows:
- Farm overview Milking, feeding, reproduction, health and financial performance on a herd, group and cow basis are pulled into one place by DelPro, a DeLaval software system. Automated alerts highlight when targets are missed.
- Breeding Breeding and heats are tracked and recorded through Bovisync. This helps to monitor the double OvSynch and tail painting programme, which aims to get everything bred by 72 days. A rapid resynchronisastion is done, followed by standard OvSynch and tail painting thereafter.
- Diet Ration alterations are managed through TMR Tracker, which reports rations mixed, fed out and consumed. High cow, high heifer, medium, low, dry, close-up (anionic salts), in-calf, bulling heifer, maiden heifer, and weaned calf diets are formulated. These are uploaded into the mixer wagon’s computer system from a USB stick.
Expansion plans
Brendan Wilkins has made the following decisions about expansion:
- Buildings Two 480-cow cubicle sheds are being built. Both are four-row barns, with a central feed passage and two open sides for natural ventilation. This will help with feed access and airflow. Five 80-hutch calf sheds will be built in the future and used in an all-in, all-out system to wean calves at 56 days.
- Airflow There are six fans in the milking parlour, but the two new barns will have 12 fans each, plus 25 fans in the rotary parlour to help keep cows cool. The old parlour will be maintained as a fresh cow/hospital parlour.
- Cooling cows Sprinklers splash the cows’ backs with big droplets of water to help cool them. Fine droplets of mist are no good as it adds to the humidity. Sprinklers will be installed every 2.4m at the feed face. Cows will have a mid-afternoon feeding – the warmest part of the day – to draw them to soaker lines.
- Cow highways High-traffic areas, including around drinking troughs, will be covered with thick rubber matting to minimise lameness issues. Cows will stand on two rubber strips (for front and back legs) at the feed face to improve comfort and, therefore, help increase intakes.
- Cubicle comfort Rubber partitions on cubicles with foam/polyurethane mattresses will help promote lying times and minimise abrasions.
- Genetics The herd will continue using high-yielding genetics from Worldwide Sires (Moonshiner, Moonwalker, Gibson, Magnum, Frostbite, Mayback, Draft and Tahiti).
- Labour Switching from a herringbone to a rotary parlour is expected to bring labour savings, so the current 60 staff (managing 1,900 cows and 1,600 youngstock on three shift patterns) working on the dairy should be sufficient.