Advice on buying and retrofitting slurry scrapers
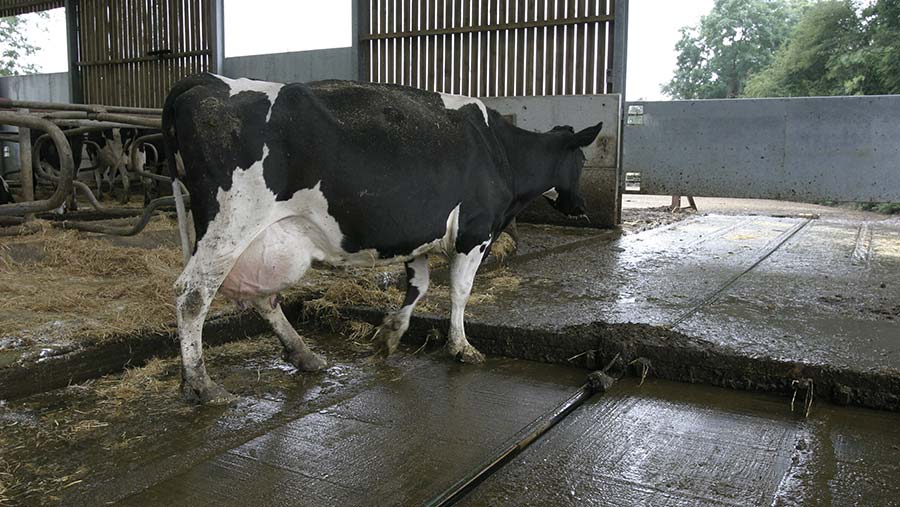
Many farms still opt to install and replace automated slurry scraper systems despite a wide variety of other options coming to market in recent years.
Automating slurry management in cubicle houses now includes robotic slurry vacuums and pushers, but scrapers remain a popular option.
See also: Guide to safe storage and spreading of slurry and fertiliser
Yields of 8,000-11,000 litres a cow are far more commonplace on family dairies than 20 years ago, and with that extra milk comes higher dry matter intakes and higher slurry volumes.
Labour is increasingly expensive and becoming harder to find, making automatic slurry scrapers the go-to option for medium to large herds of 150-600 cows looking to save half a labour unit.
This is according to Giles Russell at Midlands Slurry Systems, a family company that has installed all brands and systems of scrapers since it was founded in 1985.
Farmers Weekly asked Mr Russell for advice on retrofitting scraper systems.
What bedding type works best?
All types of systems can be adapted to work for all beddings if the appropriate considerations are made.
Sand
- Sand is heavy and abrasive. All systems should cope with sand, but they will wear out faster
- With sand systems, slurry can be dropped into a channel at the end of the passage. In this case, a specially designed slurry channel should be made, or the sand can be mechanically moved with a chain or auger
- Most manufacturers compensate for sand’s abrasiveness by using hardened materials on wearing parts that are most vulnerable, for example hardened and bushed corner rollers on chain scrapers and heavier tracks on hydraulic scrapers.
Sawdust
- Being relatively soft, it is suited to all systems
- It flows well down a level slurry channel fitted with weirs. A slurry channel is typically designed to run perpendicular across the end of the passageways and measure 1m wide by 1m deep with a 22-23cm weir at the bottom. Weirs are typically spaced every 10m along the bottom of a channel to help the slurry flow to the storage/separation area.
Green bedding/recycled manure solids
- Green bedding tends to be dry and absorbent and when dropped into a channel can have more difficulty flowing
- The same issue can occur with paper bedding
- Provisions can be made to add water to aid flow.
Straw
- Straw is not widely used but, like sawdust, it’s not abrasive and can work well in any system
- Watch out for straw length as this can cause blockages and, in slatted systems, prevent straw dropping through slats.Â
Mattresses
- Make sure that mattresses can’t move around easily and must fit well to avoid protrusion into passageways where they can be damaged by scrapers or cause them to drag.
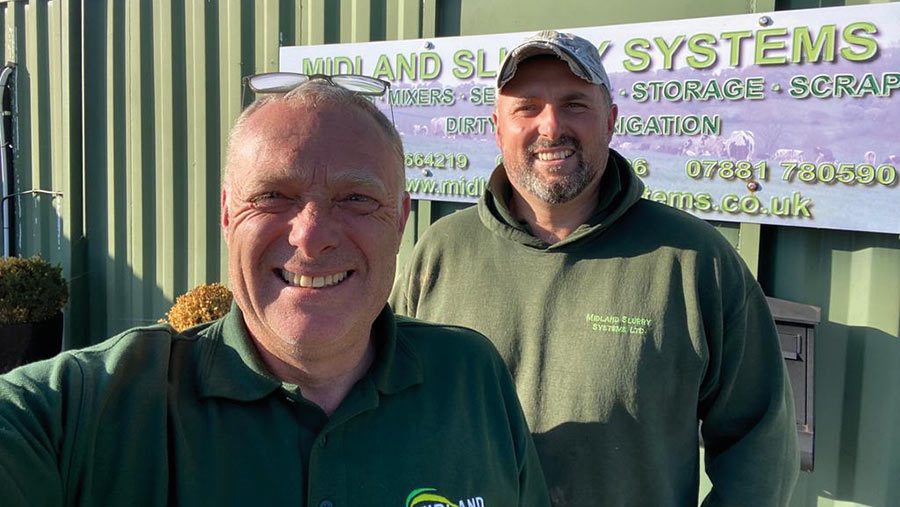
Giles and Ben Russell © Midland Slurry Systems
What are the power requirements of automatic scrapers?
- Scraper motor sizes vary from 0.5kW-2.2kW depending on passage width, length and bedding type. This is a much lower power input compared with the alternative tractor scraper
- Most scrapers are available in single- or three-phase versions – the existing power supply on the farm will dictate which one to choose
- It is advisable to link your scraper system to the existing generator in case of power cuts
- A good-quality generator should always be used, as the low voltage-control components that are installed in the control panels are susceptible to damage if the voltage fluctuates
- All scraper system control panels are fitted with safety features to stop the blade if there is any obstruction such as a downer cow.
What about shed layout and design?
- Passage width: Typically, scraper widths range from 1.4m to 4.4m, although wider options are available. Other options are longer wings. As standard, scrapers are 60cm deep. Folding blades are also an option, as well as offset blades for hydraulic systems
- Passage length: Most passage lengths are catered for as long as the floor is level. Common lengths range from 40-100m
- Passage symmetry: Chain and rope systems are designed to run in two symmetrical passages. Hydraulic systems will cater for passages of unequal lengths
- Number of passages: Most control panels will run four passages or more
- Flooring: Most scraper blades are galvanised or painted steel and run directly onto concrete, although they can also be installed on rubber matted floors. Extra care should be taken to ensure the matting is of good quality and well-fitted, so the blades don’t catch
- Add-ons: Blades can be fitted with rubber edges for an extra-clean scrape. On slats, blades are usually fitted with rubber and scrape in both directions to work the slurry into the slats.
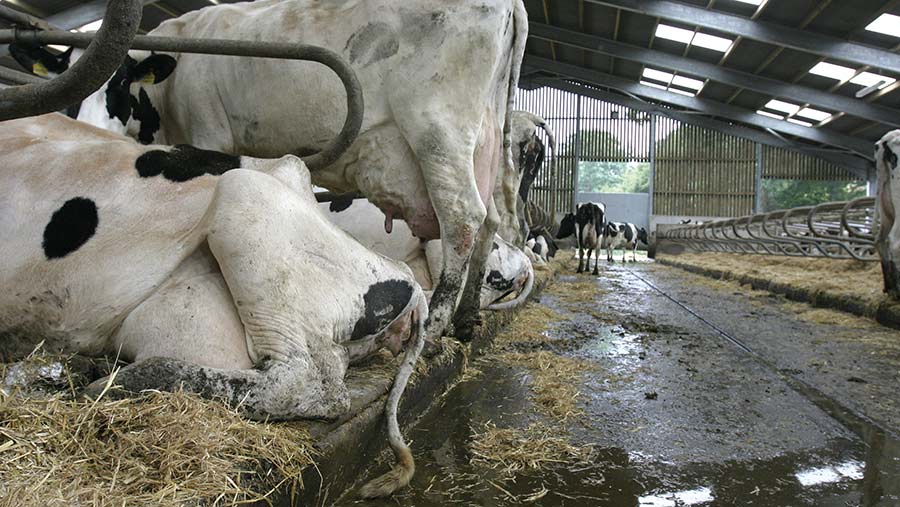
© Adobe Stock/A Linscott
Managing your scraper system
- Wear and tear: On softer, non-abrasive beddings such as sawdust a good long life can be expected from your scraper system of up to 10 years before any major expenditure is required, providing regular routine servicing is carried out such as oil changes, corner roller greasing and visual inspections. Costs will be higher on sand due to the abrasive nature of the material. Hard metals such as tungsten can be used for scraper paddles, but these wear out flooring. It’s far cheaper to replace a set of blades for £750 or so than to replace floors
- Running times: Typically, scrapers run every three hours depending on passage width and length
- Grazing half the year: When cows are grazing and the scrapers haven’t been used for a few months, it is recommended that passageways are wetted down to provide lubrication and then a few test runs are carried out before the cows return for the winter. On hydraulic scrapers, any dry slurry should be cleaned off the track to improve traction, and on chain and rope systems the corner rollers should be greased as they will be dry from lack of use. The grazing out period is a great time to book your pre-winter service with your supplier.
- Housed all-year-round: Scraper systems that are installed in 365-day housing should be serviced as recommended by your supplier.
Installation tips
- Where to put drive units: Most drive units are completely weatherproof and can be installed outside, so there is flexibility when fitting a system. Control panels are often installed inside the building somewhere out of the way of the cows but accessible to farm staff
- Making servicing easy: Service intervals depend on usage, but anything that is likely to need replacing should be installed with easy access in mind
- Slopes: Most dairy passages have a slope, working with gravity. Take full advantage of this when fitting a system
- Getting started with scraping: Run the scrapers on a manual basis during the day to start with, to check the cows and staff are happy, before introducing automatic run times.
Pricing
- Standard hydraulic system: About £12,000 (including £300 delivery, installation about £1,695)
- Standard two-lane rope system: £10,340 (including £300 delivery, installation about £1,350)
- Standard chain system: About £12,000 (including £350 delivery, installation about £1,350)
Prices are for a basic two-lane 50m passage with a width of 3.2m. Note that costs vary according to size of order and fluctuations in market prices, which are particularly volatile at the current time.