A dairy farmer’s guide to switching to robotic milking
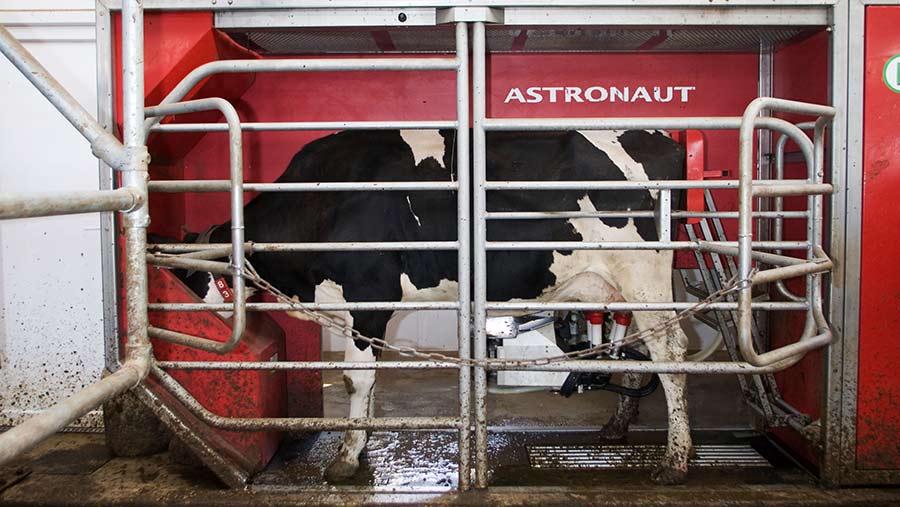
Installations of robotic milking machines have surged over the past three years, taking the number of farms using the technology to between 900 and 1,000, or one in 10 UK herds.
The increase in popularity is mainly due to improved technology, the prospect of saving labour and the availability of grant funding.
But while robot milking systems can be an efficient, high-welfare option for dairy herds, costs are high and a decision to invest must be carefully weighed up.
Kite Consulting’s Chloe Cross sets out the key points to consider before making a switch:
Q. How many units will be needed?
The number of units required depends on cow numbers and yields. Guidelines suggest one unit is sufficient for 65 lower-yielding milkers.
See also: 5 tips to prepare for dairy cow winter housing
However, Holsteins producing 10,000l+/lactation need less pressure and more space. Therefore, stock about 55 cows per robot. Higher yielders take longer to milk and cows will start to hang around if there are not enough robots.
Bigger cows waiting will put off any smaller, younger animals and the yield benefits of more frequent milking and buffer feeding could be lost.
Q. Can units be sited in existing sheds?
With a robotic system, the cow is effectively asked to find her own way to the milking unit and milk by herself. She will no longer have the guidance and encouragement from the stockmen to walk long distances or navigate around blockages and through bottlenecks such as – potholes, changes in lighting, sharp bends, low rooflines or draughty passages.
Therefore, there should be an uncomplicated and unhindered route to the milking machine that will allow the cow easy access, several times a day.
The simplest way to achieve this is to construct a purpose-built shed with good ventilation, comfortable cubicles, ideal lighting and easy footing with clear robotic access. However, this will be beyond the budget of many businesses. It is possible to incorporate robot milkers successfully into existing setups using old buildings, but it’s vital to ensure any bottlenecks are eliminated so cows are able to milk frequently enough.
Q. Do robots work in grazing systems?
Yes, they can do. It’s important in grazing systems to keep a tight rein on intakes at grass.
If the cows are grazing sufficient amounts of grass they won’t get hungry and be tempted to visit the milking parlour shed, so buffer feed should be restricted to the shed to encourage visits.
Q. Will a robot parlour reduce labour?
Reducing dependency on a human workforce is a common reason cited for installing robots, but most tasks still need to be carried out by competent workers.
The robot itself requires attention and milking units are designed to send alerts to mobile phones 24 hours a day. If there is a mechanical, animal or software anomaly it must be dealt with around the clock.
It is better then not to think of a robot milker replacing staff members, but rather reallocating them from the traditional daily milking routine into a more flexible work pattern.
Q. What staff training and recruitment changes are needed?
Installing a robot system is a fundamental change that might mean disrupting a lifetime of work routine and sleeping patterns for some staff.
It also means learning new skills while retaining those of the traditional stockman.
Workers will need to be able to:
- Manage the robot – rebooting or clearing alerts, carrying out mechanical adjustments or repairs and inputting data on issues like milk-withdrawal periods for individual cows
- Maintain accurate records to check that those withdrawals are being made by the robot
- Analyse the data that is produced. A robotic unit can produce 200 separate pieces of information for each cow, every day
- Spot key information within that fast-flowing data stream, to identify performance or health issues
Robot manufacturers should provide at least two training days and it is vital to get as many people from the farm on these days as possible.
Q. How do cows make the transition to robotic milking?
Along with staff training, the cattle also must break a lifetime of routine and learn to milk themselves. Training is, therefore, a slow task and could be carried out in blocks of about 30 cows.
Modern robot units have a training mode that familiarises the cow with the process by making all of the mechanical noises without actually drawing milk. This programme could be run at least twice before cows calve.
Post-calving, the cow should be prepared for her introduction in a slow and calm manner. Without making it a habit, you can cut the first milking short to allow the cow to get out before she panics or feels constrained, it avoids a negative association with the process.
Training must be carried out day and night using all the units available or cows will all make a bee-line for the same machine at the same time of day.
What does a robot system cost and what are the finance options?
Dodd & Co’s Rob Hitch says farmers should look at the potential benefits of higher yields and more-efficient labour use and set those against all the costs involved in purchasing and running a robot unit:
Set-up
Each unit costs in the region of £100,000 to £120,000; a considerable outlay when multiplied up to match the herd size.
In many cases, a new shed is also required, at a typical cost of £75,000 – requiring a farm with 100 milkers to invest about £300,000 in total.
Most farm businesses will seek to spread the cost of bank borrowing over 15 to 20 years.
But robotic units typically need replacing after about 10 to 15 years, and additional borrowing may be necessary within the normal timeframe.
Depreciation
Replacement rate means the depreciation charge is significant.
Assuming the unit value drops to about £20,000 after 10 years, there is a depreciation charge of between £80,000 and £100,000 spread over the 10 to 15 years of use, and this must be included in plans.
Running costs
Running costs must be fully accounted for in cashflow plans.
The robot uses electricity to run pumps, cleaning cycles and monitoring systems 24 hours a day, which can amount to £2,000 a year per unit.
Because the robot is operating 365 days a year, most manufacturers offer maintenance packages, typically costing £5,000 to £6,000 a year per unit.
When the depreciation and running costs are included for a unit, it can amount to about £15,000 a year.
Grant funding
One of the reasons why farms are installing robot units now is due to the availability of a sizeable EU productivity grant that provides 40% of the capital costs.
The scheme requires the purchase to be completed before funds are released, so, again, this period must be accounted for in cashflow plans.