4 ways to overcome labour shortages on UK dairy farms
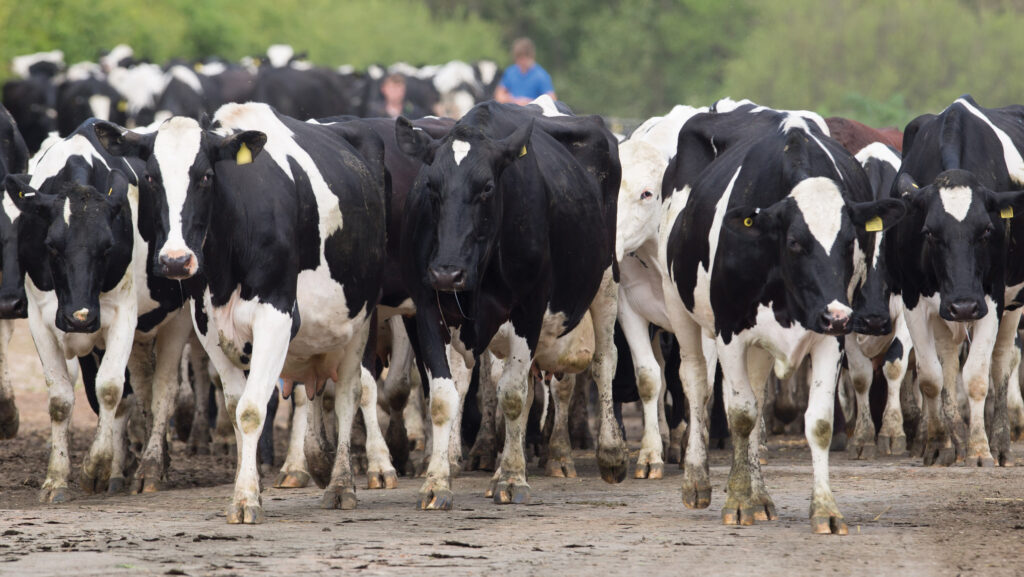
Automation, better staff packages, and using contractors could hold the key to addressing labour shortages on UK dairy farms.
Olivia Ward, farm business adviser at GFW, explains that Brexit, which stopped the free movement of people from the EU, has increased labour pressure on the dairy industry.
See also: What makes a good employer on a dairy farm
She says that a 2024 Arla survey suggested farmers were now having to pay staff 27% more since Brexit.
Research by Hogan et al (2022) revealed that milking, calf care and grassland management took up the most time on dairy farms.
Below, Olivia offers advice on how farmers could overcome labour shortages in these key areas.
Key facts and figures
In 2019, there were 47,100 EU staff on dairy farms. By 2021, their number had fallen by 28%.
A survey of 500 dairy farmers carried out by Arla in 2024 revealed that because of the labour shortages:
- 8.5% of farmers were reducing output
- 10.6% were reducing herd size
- 16% were considering leaving the industry.
1. Automatic milking machines
Installing automatic milking equipment can reduce the average time spent milking by 62%, from 5.2 hours down to two (Tse et al, 2018), including washing down.
But Olivia says there are several considerations to make before installing robots:
- Is it affordable? They are a high investment at about £120,000 each, plus building design
- Are there adequate sheds? Robots require large, free-flowing buildings to reduce waiting times
- Time must be spent training cows
- The number of robots needed may be a limiting factor – typically, one to every 60 cows
- After-sales support and backup are critical and may vary from area to area.
Grants such as the Improving Productivity Grant have made installing robots more appealing; however, it is currently not known if this grant will reopen, she says.

© Adobe Stock
2. Automatic calf-rearing equipment
Automatic calf feeding systems can reduce labour requirements by 20% (Dolezal et al, 2021) and contribute to better calf growth rates.
“Automatic feeding can save one minute per calf per day compared to manual feeding twice daily,” says Olivia.
The advanced monitoring they offer can detect diseases much faster, reducing calf care time by up to 40% (Johnson et al, 2020).
However, having calves drink from the same machine can increase disease risks, and cleanliness is very important, she stresses.
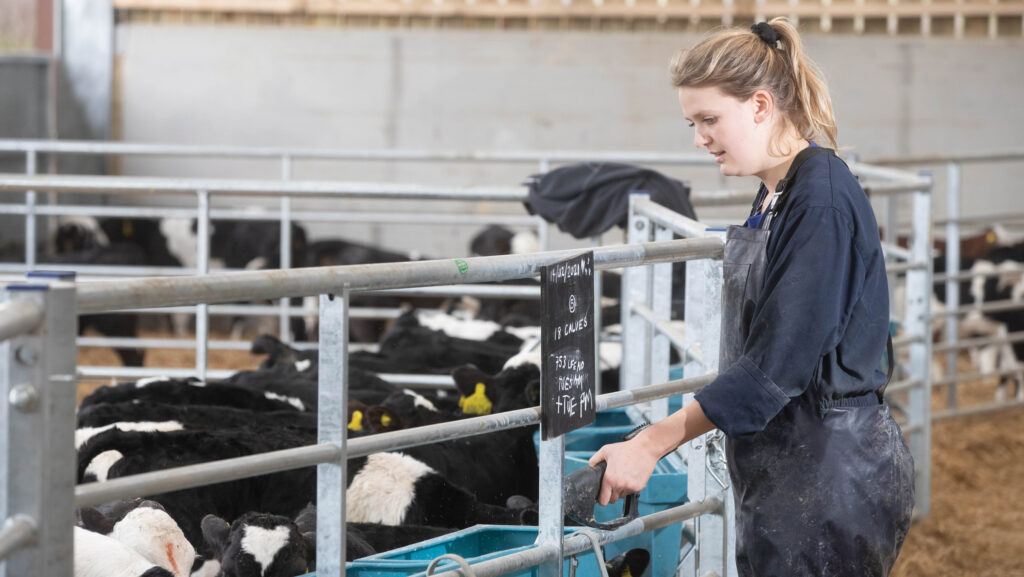
© Tim Scrivener
3. Use farm contractors for specific jobs
Contractors doing the work can reduce labour costs by 15-30%, according to a study by Baker and Thomas in 2021.
“As farm size increases and the number of cows increase, the amount of work being contracted out increases,” explains Olivia.
“You know the contractor will come with state-of-the-art equipment, and you get the machine and driver to do it.”
She says using contractors also helps reduce machinery capital expenditure and maintenance costs. However, she warns that getting contractors to come during busy periods can be tricky.
4. Offering staff incentives and part-time hours
Offering better pay and benefits can reduce staff turnover rates by 20%, the National Dairy Farm Association has found.
Olivia believes this could include offering accommodation, a vehicle, competitive annual leave, a pension, or long service and production bonuses.
She says the same survey found providing continuing training improved staff retention by 15%.
Furthermore, research by Johnson and Lee in 2021 suggests offering shorter shifts to multiple people is more attractive; for example, offering 30-hour weekly shifts to two people as opposed to one 60-hour shift.
She adds: “Employing more staff on a part-time basis, rather than full time, could help reduce bottlenecks with sickness and annual leave, and give you more people to fill roles.”
Case study: Ben Hembrow, Huntham Farm, Somerset
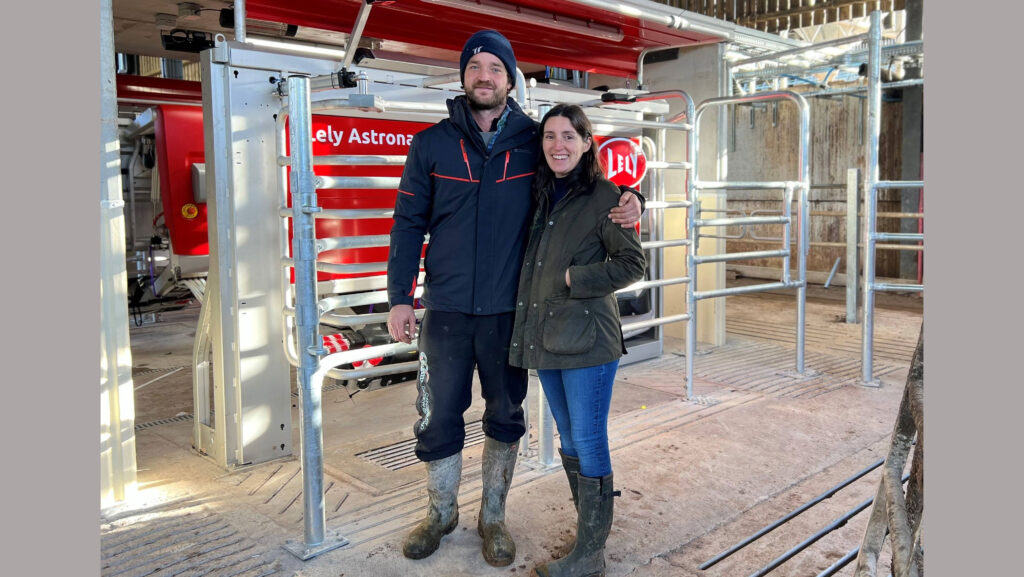
© Ben Hembrow
Somerset dairy farmer Ben Hembrow says milking efficiency has improved by 60% since installing robots.
Previously, his herd of 850 cows was milked three times daily through a 20-year-old 24/40 swingover parlour.
Ben says at the time he thought it was a “relatively efficient system”, taking six to seven hours at each milking.
However, he foresaw labour challenges on the horizon and decided to install 12 robots in June 2023.
Improvements
Milk output has increased from 1m litres of energy- and fat-corrected milk a person to 1.6m, excluding youngstock and tractor operations.
“We’ve had a 60% increase in milk output per labour unit, and we’ve been running for 12 months, so we feel confident with that number,” he says.
Cows are averaging 36 litres daily, up from 32 litres. Meanwhile, staff numbers have been reduced from 12.5 to nine full-time employees.
They cover youngstock and cow-related jobs, as well as field work.
Ben says working hours have not changed (10-11 hours/day), because the team is the same, and employees did not want to reduce their hours.
However, he says automation has improved flexibility, and working hours could be changed in the future.
Time is now spent fetching cows to be milked, training heifers or carrying out health checks and artificial insemination, rather than being “tied to the pit”.
“The team perceives it is a much more varied job since the introduction of robots.
“We can have specialist roles among our team, too, which we think is an advantage,” he adds.
Challenges
However, he says scraping and bedding are more challenging in a robotic system because cows never leave the shed.
To overcome this, he has invested in three manure collectors.
“I think automatic [slurry collectors] are critical. But the way we bed up in our three-row shed is a real challenge, and it’s something we must look at to see how we can improve that from a labour point of view [so cows don’t have to be held in one alley].
“We took that for granted in a parlour scenario.”
He says they are also much more reliant on highly skilled support – though their local engineers do “a great job looking after the robots” and are a key part of their team.
“When I started, I didn’t quite appreciate how important that would be. In some ways, we have outsourced out-of-hours work to engineers.
“Your relationship with them is important, and needs much consideration,” Ben advises.
Despite these challenges, Ben says he wouldn’t go back to milking in a parlour and believes everyone has better job satisfaction.
Currently, 60 fresh calvers are still milked in the parlour, but another robot is being installed to allow the parlour to be switched off permanently within the next few months.
“We anticipate another 20% more milk per labour unit over the next 12 months based on that change,” he says.
Olivia Ward and Ben Hembrow were speaking at Dairy-Tech 2025.