Video: Robotic cattle feeder on track for five-year payback
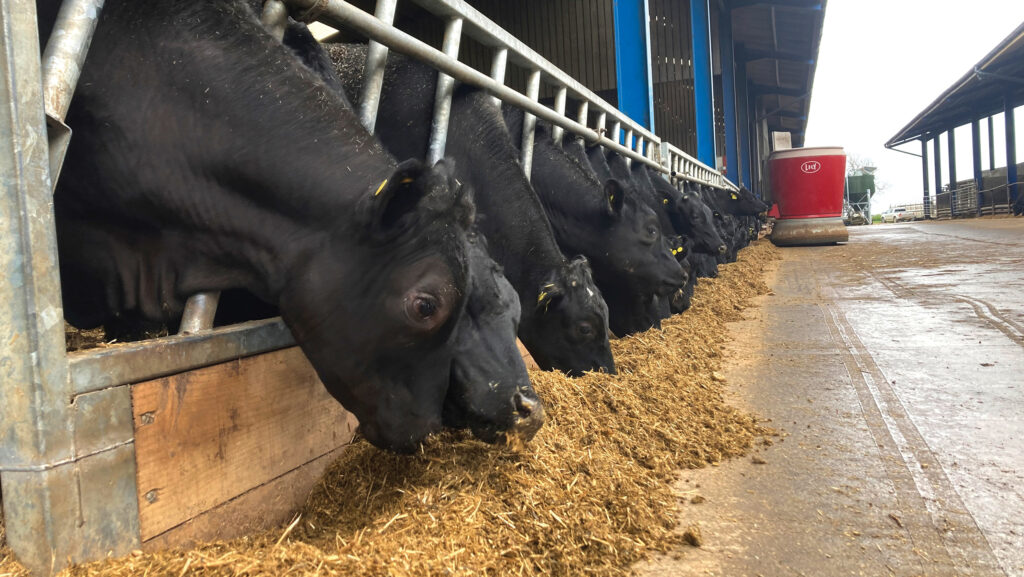
Labour requirements and fixed costs have been cut by an automatic cattle feeding system that has also improved grower-stage performance by 100g a day on a beef finishing unit.
James and Sarah Broadwith of Red House, near Ripon, installed a robotic feeder in October 2023 after two years of weighing up the benefits.
Their key objective was to cut cattle management time, but keep accuracy and precision. They had to be sure such a big investment stacked up financially.Â
See also: Video: How a robotic suckler beef feeding system cut costs by 75%
Watch the video below to hear from Sarah about how the benefits the new feeder has brought to the business.
Farm facts
- 100ha arable home farm on successional tenancy
- 562ha farmed, of which 260ha contract farmed for Sarah’s parents
- 350 cattle bought annually, on farm 16 months
- 59ha permanent pasture rented for summer grazing
- 90ha processing potatoes all stored
- Arable rotation, includes sugar beet, maize, potatoes, oilseed rape and first milling wheats
- 20ha maize and 12ha sugar beet (150t sold off farm) grown for cattle
- Three full-time employees plus extra regulars at peak times
Management change
After working closely with Sarah’s parents 14 miles away for several years, Sarah and James took full responsibility for the labour and machinery for her parents’ 260ha (642 acres), prompting the couple to look at time-saving technology.Â
Previously, cattle were fed with a mixer wagon once a day, requiring a tractor and load-all operator, and feed had to be pushed up at morning and night.
The Broadwiths first saw the Lely Vector robotic feeder at the Great Yorkshire Show in 2021 and became the second beef farm in England to install it.
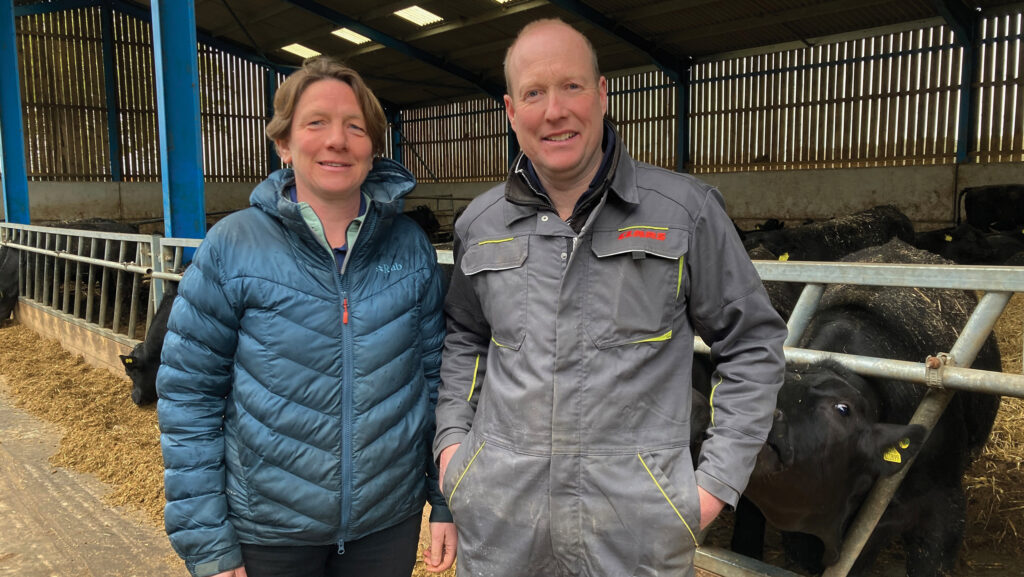
Sarah and James Broadwith © MAG/Michael Priestley
Cattle system
The Red House system feeds a total mixed ration (TMR) to 540 dairy-cross Angus-sired cattle from September.
Finishers are all sold deadweight to Dovecote Park by June.
The ration is based on home-grown maize silage, chopped sugar beet, spey syrup, wheat distillers, rolled barley, chopped straw and minerals.
No grass silage is grown, as the arable harvesting and potato grading (from January to July) is prioritised.
Heifers and steers are loose housed on home-grown straw and are managed in the following three phases:
- Calf grower Cattle arrive in five batches of 50-90 head between September and February, weighing about 160kg (just over four months old) and are fed calf pellets for 10 days and transitioned onto a 16% protein TMR. Cattle are weighed at key points throughout their life and are turned out in spring at about 370kg.
- Summer Cattle graze low-input grassland (mostly rented) to grow frame until October housing.
- Grower/finisher Cattle are transitioned back onto a grower diet (mainly sugar beet and maize) analysing at 10% sugar and 19% starch. A finisher ration with barley is fed from 500kg, with the aim of producing a 660kg animal and a 347kg carcass at 20 months.
Robot system
The feeding element of the new system is a 600kg tub mixer and feed pusher, filled by a feed grabber that takes chopped beet, maize silage and chopped straw from a feed kitchen.
The kitchen has three concrete-floored bays, two large feed bins (for wheat distillers and barley) and four mineral bins. It has capacity to be filled every three days.
The old feeder wagon will be replaced with a large chopper bucket to chop beet every other day.Â
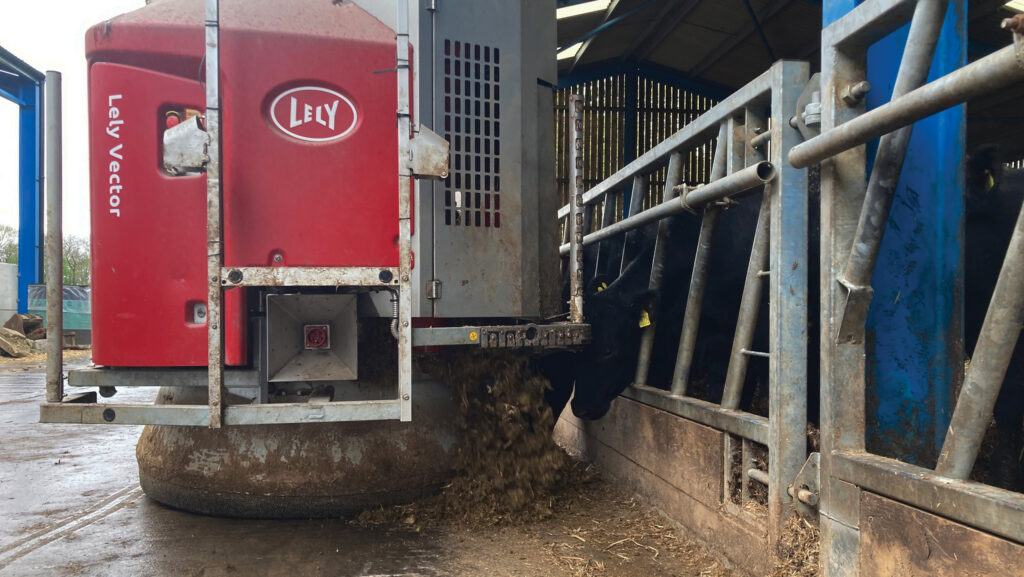
© MAG/Michael Priestley
The robot navigates its way around the farm 24 hours a day, using ultrasound guidance along the feed barriers and using a metal strip to guide it across the yard.Â
It also measures feed height in front of the pens by laser to assess whether more needs putting out.
The robot achieves the following:
- Capacity Average feed processed and fed last winter was 11.422t/day.
- Fresh feed It has fed up to 18 pens of cattle to appetite on average five times a day. It organises its own workload to combine pens that are on the same ration where feed levels are lowest and below the threshold set.
- Feed pushing The Vector pushes up any feed it passes every time it goes out to deliver more and also heads out separately to push up when no feeding is required.
- Downtime The robot is not used in July or August when the finisher cattle are all gone and the younger cattle are out at grass. All recharging is done when the machine is being filled up.
- Rationing The robot feeds an average of seven diets a day (three more than the feeder wagon system). Diets can be slowly transitioned to allow rumen microbes to adjust – accuracy is at least 95%.
Benefits
Automatic feeding has brought economic benefits and makes the running of the farm easier, offering more flexibility around cattle feeding and freeing up weekend time, says Sarah.
Sarah manages the robot as part of her working day, allowing James to focus on the arable unit at busy times.
Cost and benefits: Lely Vector and estimated payback period |
||
Item |
Value |
Comments |
Lely Vector System |
ÂŁ140,000 |
Lely Vector and installation (control system, grabber and feeder) |
Kitchen and electrical supply |
ÂŁ50,000 |
Two feed bins, one spey syrup tank, electric galebreakers, phase converter, concrete panels and floor and electrician work |
Total cost |
ÂŁ190,000 |
Over 15 years of expected life = ÂŁ12,667/year |
Benefit |
Saving each year |
|
Fuel |
ÂŁ7,266 with electricity at 28p/unit; diesel at 75.5p/litre |
Ration feeding, mixing and pushing up = 8,360 units/year = ÂŁ2,341 plus ÂŁ1,216 of forklift diesel to get feed to kitchen. Old system cost ÂŁ10,823 |
 Labour |
ÂŁ7,330 from automating feeding (accounting for loading the kitchen) |
Based on £14/hour – saving time pushing up and feeding out  |
Depreciation |
ÂŁ15,507 based on ÂŁ14/hour depreciation. Feeder wagon was written off at ÂŁ20,000 over five years |
Saves 575 tractor hours, 247 telescopic hours and £4,000 for a feeder wagon. Servicing/repair savings have not been included  |
Cattle growth rate |
ÂŁ9,341(350-head a year gain an extra 0.1kg/day over 161 days = 16.1kg) |
ÂŁ5/kg at 52.6% kill out = extra ÂŁ42.34 a head. 70.84kg extra feed (4.4:1 feed-to-gain ratio) = ÂŁ15.66 a head. Extra deadweight minus extra food = ÂŁ26.69 a head |
Payback |
4.82 years |
ÂŁ190,000 divided by ÂŁ39,444 total savings |
Getting going
Minor adjustments were required to reduce mix filling times. The maize was being bucketed into the feed bunk and the straw bale was placed in and the strings cut.Â
Instead, Lely suggested using the farm’s straw spreader to create a more consistent material for the grabber to work with, and a second-hand block cutter now places the maize, which frees up time and increases accuracy.
Future
Sarah says the robot is improving feed access for shy animals, because there is always food at the feed fence, and rumen health should be improved by offering fresh food “little and often”.
“We calculated a five-year payback from investing in the system and are on track. We expect the system to last at least 15 years so will have 10 years of significant financial benefits,” she says. Â
“We are pleased we are getting more growth on young cattle when their feed conversion efficiency is at its best and hope to see improved growth rates on finishers too.”