How sharing and renting farm kit can save money
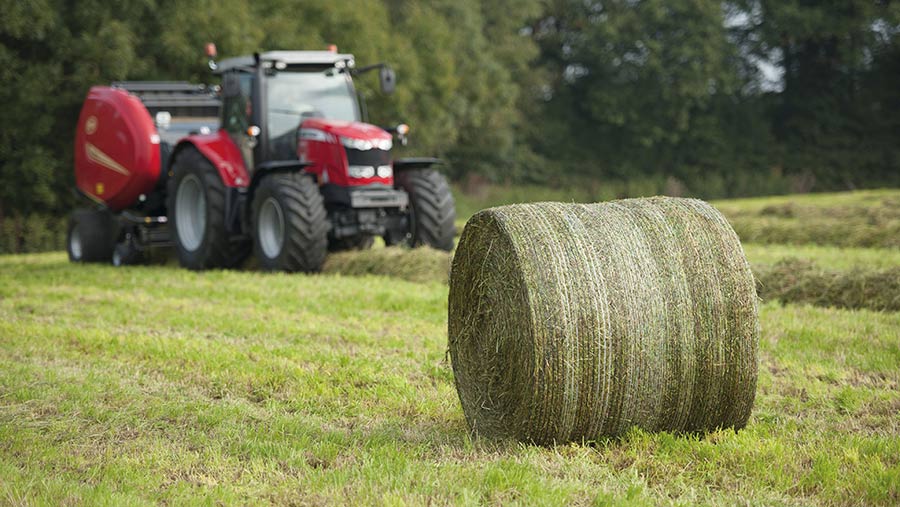
More farms are managing their fixed costs, depreciation and repairs by sharing and hiring machinery.
Many balk at the idea of relying on another farm’s machine, but even small operations can save thousands each year through hiring machinery or establishing co-operative agreements.
Successful arrangements can benefit from being based on formal agreements and prices, but others still hinge on trust and old-fashioned neighbourly co-operation.
See also: How a maternal breed is Brexit-proofing Northumberland estate
We look at two case studies – one in Midlothian, where a farm is renting a tractor from a neighbour and two farms in Leicestershire sharing machinery and silaging work.
Case study one: 1,000-ewe farm rents tractor to cut costs
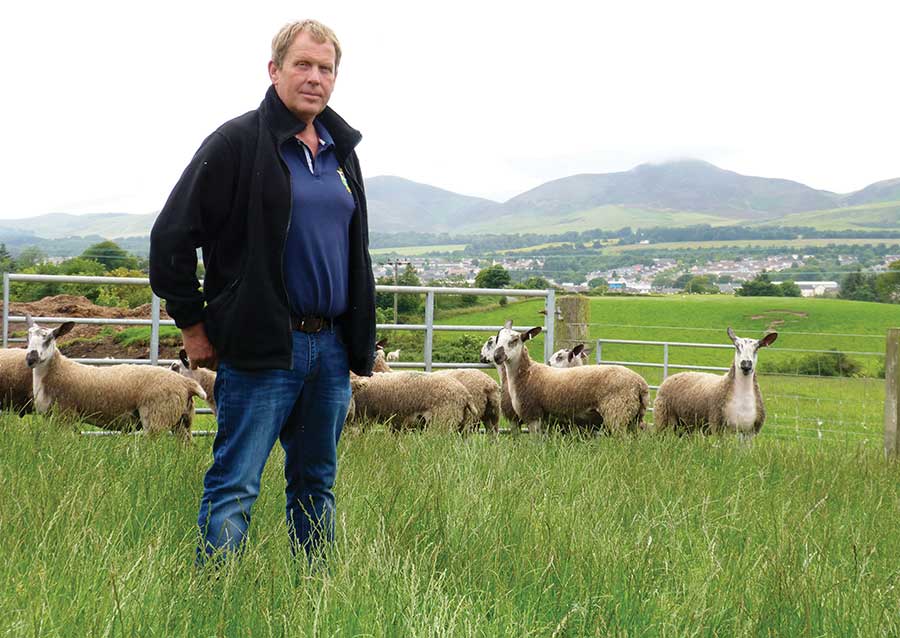
Derek Hall
A good working relationship with a neighbour is allowing a Midlothian sheep breeder to run 1,000 ewes with just a pick-up, quad bike and snacker.
Bluefaced Leicester breeder Derek Hall of the Firth flock, Lilyburn, Penicuik, paid a high contracting bill this year (£7.20 a ewe) and rented a tractor (£1.80 a ewe), but he says it was worth it to keep machinery and depreciation costs down.
Firth Flock
- 150ha (370 acres) farm
- 20ha (50 acres) owned
- Running 1,040 ewes
- 80 crossing-type Bluefaced Leicester ewes
- 480 Scottish Blackface ewes
- 480 home-bred Scotch Mules
- Mule lambs sold at United Auctions in Stirling and privately
- Bluefaced Leicester tups sold at Kelso, Hawes and Carlisle
As a former Royal Bank of Scotland bank manager, Mr Hall knows what an economic drain machinery can be on a sheep farm.
Last year, the farm paid its contractor £7,200 for silaging 15ha. In some years reseeding 6-8ha means the cost is a little higher.
The quad bike costs £1,200/year in depreciation (£1.20 a ewe) and does 6,000km/year. The depreciation on the snacker is minimal as it’s over 20 years old.
For comparison, Quality Meat Scotland’s 2019 sheep costings found power and machinery costs of about £10 a ewe and depreciation of £8-£9 a ewe were common.
Tractor rental
Mr Hall rents a tractor from a neighbour half a mile away when he needs it. This is for winter silage feeding from December to when indoor lambing ends in April.
This costs £30/hour (includes fuel), typically for three hours a week to feed silage twice (1.5 hours at a time).
It takes about 60 tractor hours each winter to feed the ewes (£1,800/year), including time to drive a mile to the farm and back.
“The £1,800 helps my neighbour pay the depreciation on the tractor,” explains Mr Hall.
This is a big saving compared to keeping a £25,000 tractor going for 10 years, which would cost £2,500/year in depreciation, before running costs, he estimates.
The rest of the tractor work (mucking out, muck spreading, fertilising, silaging and reseeding) is done by one contractor.
“I don’t shop around for the cheapest contractor – I rely on one business. I try and give seven to 10 days’ warning prior to silage cutting.
“I’m not just saving on the cost of a tractor, it’s the muck spreader, and all the implements, too. Plus, the cheque I write the contractor gets the work done to a high standard,” he adds.
Case study two: Leicestershire farms pool £95,000 of silage kit
An excellent working relationship and regular communication is allowing two Leicestershire units to share machinery and silaging work, halving the cost of kit and sharing labour.
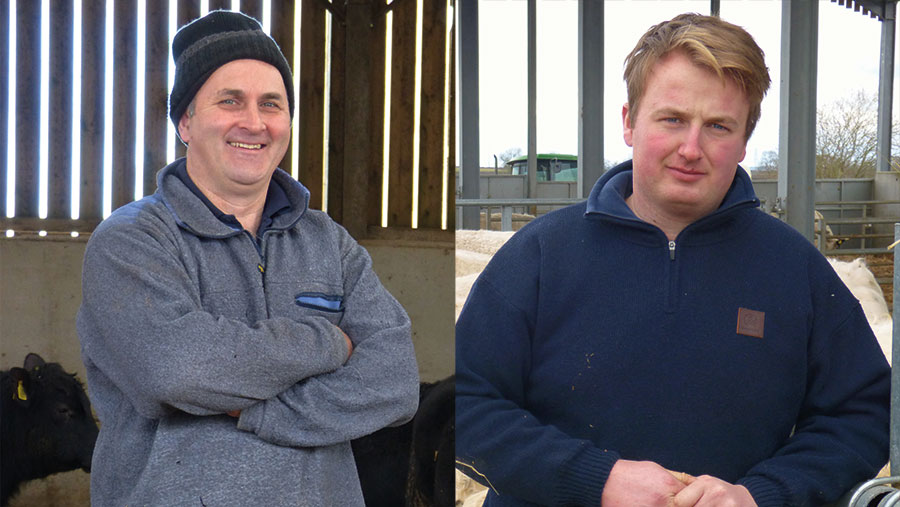
Mark Gale (left), Baytree Farm, and Leo McCourt (right), Northfield Farm
This gives Melton Mowbray beef and sheep farmers Mark Gale, Baytree Farm, and Leo McCourt, Northfield Farm, more flexibility and time to spend on their more profitable diversifications.
Mr Gale has been a director of Melton Meat, a sheep and goat abattoir, since 1998 and has run the slaughterhouse on his farm since 2012.
A mile away, Mr McCourt is growing a successful farm shop brand – Northfield Farm – based at home and at Borough market in London and selling named-sire, forage-reared meat.
Like his father, Jan, Mr McCourt has continued enjoying a good neighbourly relationship with Mr Gale, with Melton Meat slaughtering Northfield lambs. They also share a cattle crush, trailers and labour.
Farm facts
Northfield Farm
- 20 White Park herd and 100 Lleyn cross and Charollais ewes supplying butchery
- 60ha (150ac) of permanent pasture, half rented
- Farm shop and butchery, and shop in Borough market, London
- Processing 12 to 25 lambs, one to two cattle and six to 10 pigs a week
Baytree Farm
- 121ha (300 acres), of which 40ha (100 acres) is rented
- 100 ewes and 40 pedigree Aberdeen Angus cows plus followers
- 80ha of wheat, oats, barley, fodder beet and grass in five-year leys
- Growing 12ha of fodder beet for home use and sale
- Home of Melton Meat abattoir
- 80kw wind turbine
Sharing agreement
There is no formal agreement, with both parties contributing equal amounts of new machinery (see table).
Any breakages are written down in diaries – a workshop at Baytree Farm allows for some repair work to be done at low cost.
“We have a reckon-up now and again,” says Mr Gale. “But money will only have to change hands to even it up once or twice. We both benefit hugely from co-operating.
“Compared to the diversifications, the farming is a secondary thing. I think it works because we have the same attitude. We talk every day or two and that helps us arrange machinery sharing.”
How silage machinery is split |
|
Northfield Farm |
Baytree Farm |
Bale wrapper £13,000 Mower conditioner £7,600 Bale trailer £7,500 Rear discharge muck spreader £20,000 |
Baler £25,000 Rake £15,000 Grass tedder £7,000 |
Total value roughly £48,100 |
Total value roughly £47,000 |
*Note, prices are approximate prices as new |
Tips and costs on equipment and kit sharing
Tips
- Machinery should not be sat around – loaders and muckspreaders are the main offenders. For example, £90,000 spent on a loadall could buy 90 cows, 900 ewes or rent or buy land
- You must be organised and know what machinery input your system requires to rationalise essential kit and what gear can be hired
- Items to consider: How handy is the machine? How much are you saving by not buying your own? Can you get it whenever you need it?
- If you can’t agree terms and fees, ask a consultant to calculate a borrow charge
- A machine can be rented from someone else who owns it 100%, or you can buy a stake in the machine relative to your likely annual usage
- Communication is important – you need to plan ahead, particularly when sharing silaging equipment
- Costs incurred while in use (fuel, breakages and tyre damage) are covered by the person using it
Scenario: Buying v hiring a loadall
A new £90,000 loadall that needs replacing in five years:
- Depreciation cost: £18,000/year (residual value is spent in the uplift on the cost of the next machine)
- Repair cost: £4,000/year (5% of asset value/year, but you change the tyres yourself, hence not £4,500)
- Return on capital: 10% of £90,000 = £9,000/year
- Total cost is £31,000/year, which divided by 52 weeks = £596/week
- Farms are hiring loadalls for £310/week to return at the end of winter
- Over an 18-week winter this will cost £5,580 (£310×18), giving an annual saving of £25,420
Scenario: How to calculate an hourly rental fee for a tractor
Machine: Second-hand 120hp tractor with a loader on with 4,000 hours is valued at £36,000.
- Deprecation cost: Keep it for four years and write off the £36,000 = £9,000/year, which divided by 1,000 hours/year = £9/hour
- Repair cost: 10% of purchase cost = £3,600, divided by 1,000 hours = £3.60/hour
- Fuel, oil and insurance: £4,000, divided by 1,000 hours = £4/hour
- Return on capital: 10% of £36,000 = £3,600, divided by 1,000 hours = £3.60/hour
- Total = £20.20/hour
Source: Tony Evans, senior farm business consultant at Andersons