Video: How a robotic suckler beef feeding system cut costs by 75%
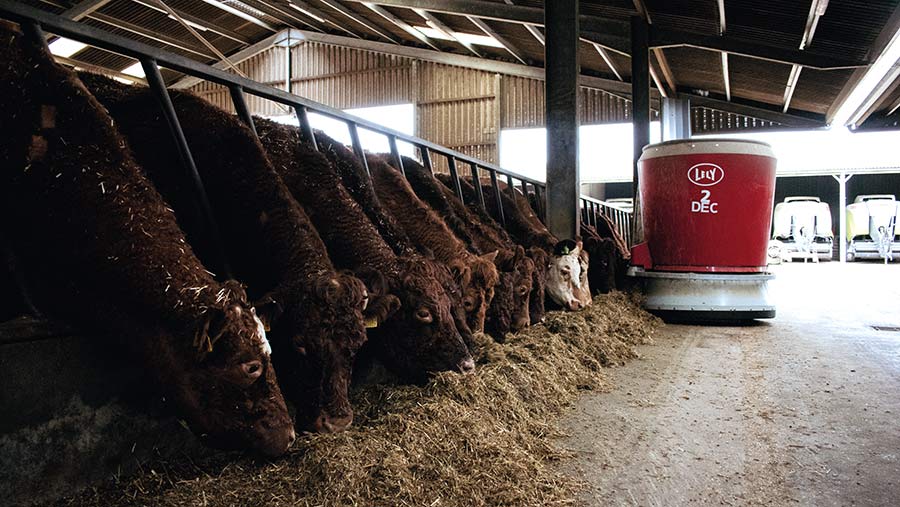
Feeding-out costs and labour requirements have dropped dramatically on a 300-head suckler finishing unit following investment in an automated feeding system.
First-generation farmers Pete and Richard Burbage were the first beef producers in Great Britain to install a Lely Vector, in 2021.
As well as the suckler herd, the brothers run a large-scale contracting business and are about to launch a dairy enterprise at Oakfields Farm, near Northampton.
For them, maximising efficiency across the entire business is key.
See also: 6 ways to improve udder health in automatic milking systems
Farm facts: Oakfields Farm, East Haddon, Northamptonshire
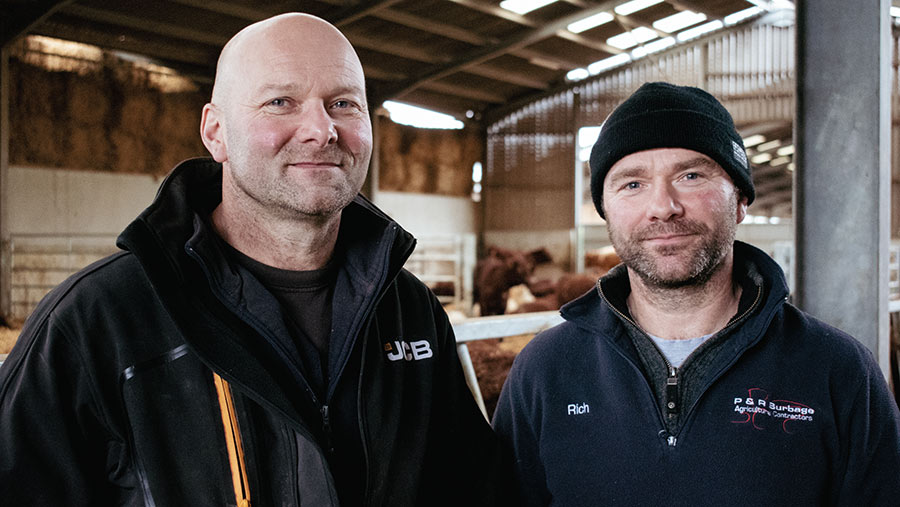
Pete and Richard Burbage © MAG/Charlotte Cunningham
- 405ha (1,000 acres) of grassland and arable
- 300-cow Salers-based suckler herd, bred to Charolais as a terminal sire
- Breeding all own replacements
- Rotationally grazed throughout the summer and housed over winter
- All stock finished off grass/forage
- Finished stock sold deadweight to ABP
- New 120-head dairy unit with robotic milking starting in March
- Small anaerobic digester plant producing some of the farm’s electricity requirement
Until 2021, feeding up during the winter housed period had been done via a tractor-drawn wagon mixer.
However, with the mixer coming to the end of its working life and continued pressure from scarce labour resource, the Burbages began to look for a replacement.
“Staffing is getting harder and harder to find,” says Pete.
“We’d seen the Vector on farms before, and we liked it, but we didn’t think we could justify it.
“We wanted to future-proof our next feeder wagon to increase longevity, but when you start looking at these highly expensive wagons, it does open your eyes to what else is out there.”
The brothers decided on Lely’s automated feeding system, at a total cost of £200,000 – which included all associated building work and installation costs.
“Robotics [now] gives us a lot more control over our time and labour,” says Richard.
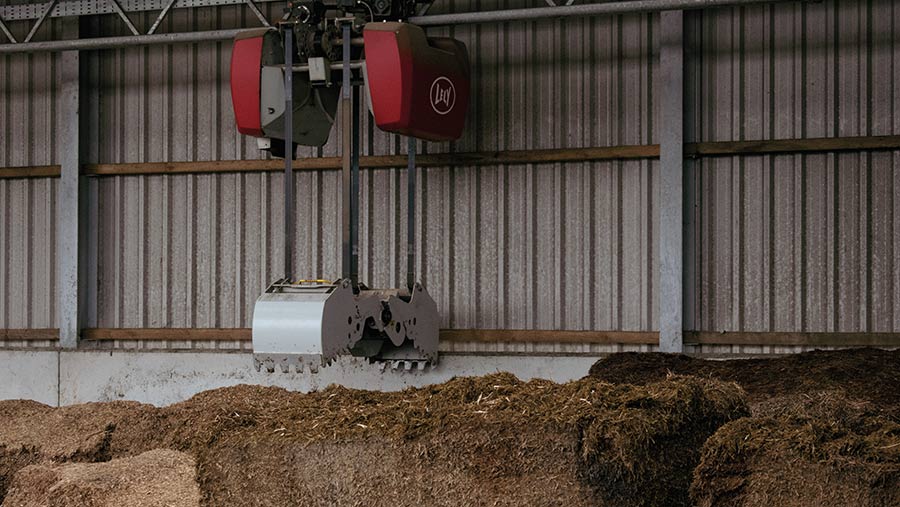
The robotic crane grab in the feed kitchen © MAG/Charlotte Cunningham
How it works
The system at Oakfields Farm comprises two stainless steel robotic mixing tubs and augers, which are guided by metal strips from a base shed to the main cattle housing.
Next to the mixing tubs is a feed “kitchen” where the feed is stored, selected and picked up via a crane system, which runs in the roof space between the kitchen and the mixing tubs.
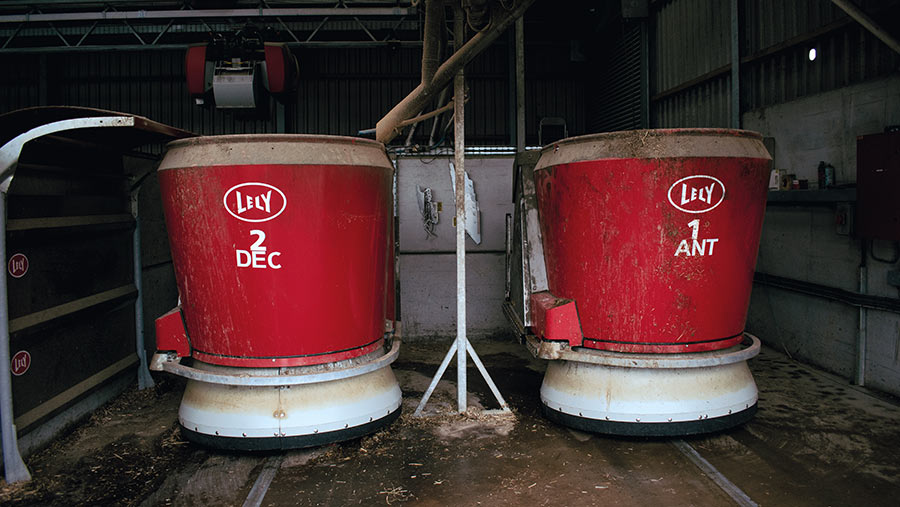
Ant and Dec, the twin mixing tubs © MAG/Charlotte Cunningham
Attached to the crane is a feed grabber.
This uses laser technology to automatically select the correct block of feed or silage – depending on the mix – and the required weight for that ration, before loading it into the mixing tubs.
Once the ration is formulated, the mixing tubs set about their journey down the shed, delivering specific rations to the 12 groups of cows.
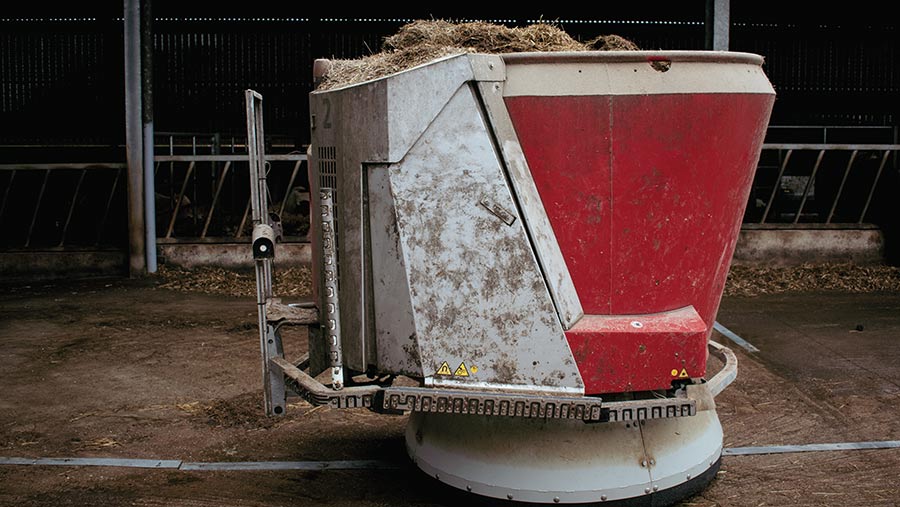
The robots can deliver feed as needed 24 hours a day © MAG/Charlotte Cunningham
The system is claimed to have accuracy of up to 98% and can store up to 18 different rations.
Importantly, it feeds to demand, 24 hours a day. A laser scans the feed face every 60 minutes to measure how much remains on the ground and assess whether another feed is needed.
The individual rations are formulated by the farm’s nutritionist, Simon Smith, and programmed into the in-shed computer, which controls the entire process.
See a video of the robotic feeder in action.
The benefits
The reduced cost of feeding out has arguably been the biggest benefit (see table “Oakfields Farm fixed costs”), largely owing to the lower labour and diesel demand of the automated system.
Pete says that even with rising electricity costs of late, it is still a more cost-effective system.
The brothers have identified a number of other advantages:
- Labour-saving They estimate a time saving of two-and-a-half hours a day, allowing them to focus on other projects and areas of their businesses, such as the new dairy unit, which is due to start milking in March. Filling the kitchen takes just two hours, twice a week.
- Profit insight The Vector software automatically generates daily reports such as feed intake and feed cost. Daily monitoring allows the farm to keep a close eye on costs and tweak a ration quickly if needed.
- Improved feeding Automation means each ration is mixed the same – in terms of quantities of ingredients – every time. The Burbages are currently achieving 96% accuracy, compared with an estimated 75% previously. Cows now also receive consistently fresh feed, as and when they need it, rather than being fed the total ration once a day.
- More flexibility The herd has moved from receiving three different mixes to seven, to meet specific requirements of groups of cows. Mixing so many small batches of feed would not have been viable with the old system.
- Cow behaviour More frequent feeding and pushing up of feed has reduced competition and bullying at the feed fence.
- Less waste Trough waste has been reduced from 5-8% of the ration to just one wheelbarrow a week. Precision cutting has also cut clamp waste.
Oakfields Farm fixed costs |
||
Tractor-drawn mixer wagon |
Unit frequency |
Total cost |
Labour |
||
Loading up, filling, feeding out |
17.5 hours/week |
£262.50 |
Pushing up |
3 hours/week |
£45 |
Cleaning out troughs |
1 hour/week |
£15 |
Power |
||
Diesel: loading, mixing, feeding out and pushing up |
420 litres/week |
£210 |
Running costs |
||
Total weekly |
£532.50 |
|
Total annual (29 weeks) |
£15,442.50 |
|
Automated feeding system |
Unit frequency |
Total cost |
Labour |
||
Filling and maintaining kitchen |
4 hours/week |
£60 |
Power |
||
Diesel: cutting forage and filling kitchen |
60 litres/week |
£30 |
Electricity: loading, mixing, scanning, feeding out, pushing up |
36kWh at £2.52/day |
£17.64 |
Running costs |
||
Total weekly |
£107.64 |
|
Total annual (29 weeks) |
£3,121.56 |
|
Source: Lely/Burbage Brothers. Note: Data calculated at time of Vector purchase in November 2021. Running costs exclude service and electricity standing charges, and machinery/equipment depreciation. |