How ear tag tech is improving Yorkshire pig farm’s efficiency
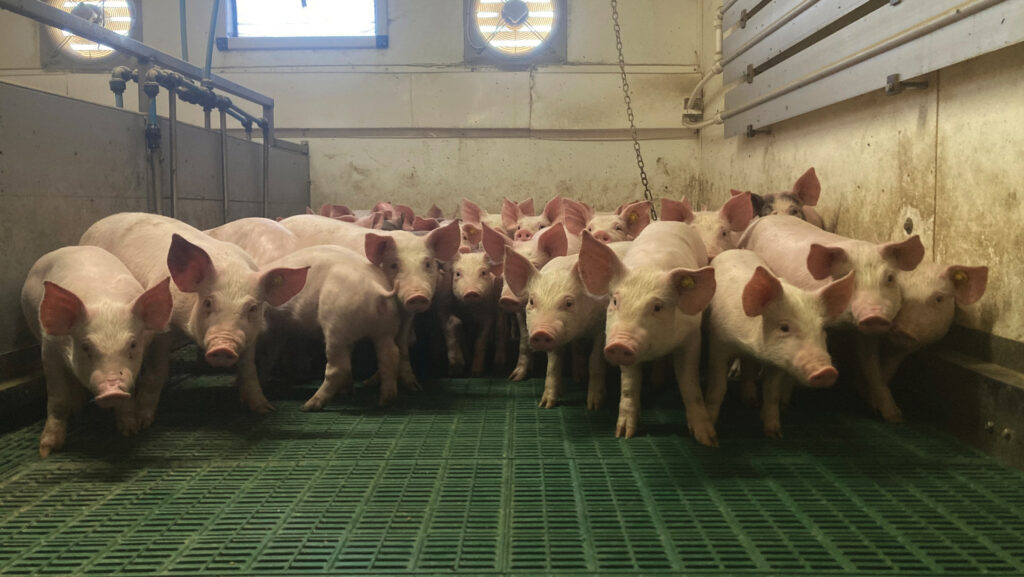
A family pig business is one of the first in the UK to monitor commercial pig performance from farrow to finish with electronic identification technology.
Infrastructure upgrades, marketing age, and sow culling decisions have been informed by the lifetime performance data captured by ultra-high-frequency ear tags on pigs bred on an independent multisite farrow-to-finish business near Ripon.
See also: Livestock leaders see ‘real potential benefits’ of cattle EID
The owners, who asked not to be named, say the system has resulted in obvious benefits and clear returns since installation in January 2023 (see “Data-driven improvements”).
The family started building a new pig unit in 2019, erecting grower and finisher sheds themselves using home-made fibreglass and insulated boards. The data are now helping them shape their plans for a new farrowing house with bigger pens.
Farm facts
- 700 sows and progeny taken from farrow to finish
- 648ha of arable ground producing home-grown feed
- Land and farms owned in a family partnership
- Selling deadweight and direct to a local butcher
- Sows sold at Thirsk market
How the data system works
The ear tags are slightly smaller than a 10p piece and are read by a handheld gun. This is set to read one tag at a time, as the system is focused on tracking individual performance. There are four stages in the process:
- Data capture The gun sends the identification number to a tablet, which logs it in an Excel spreadsheet and can be easily carried round the farm. Weight at birth, weaning and slaughter are recorded, as well as gender, date of birth and additional information such as health and medicine details, if needed.
- Data processing Raw data are transferred to the farm computer and processed by Microsoft’s Power BI analytics software.
- Data visualisation The software sorts and aggregates the data. Performance figures on growth, days to slaughter, mortality, diseases and medicine use can be grouped and analysed by batch, sow, farrowing or building and displayed on a dashboard as graphs or tables.
- Data access A built-in natural language query facility (much like a search engine) allows the team to pose questions such as: “Which sow has lost the most piglets to weaning?” or “Which batch had the lowest weight gain post-weaning?”
How the tagging works
Four coloured tags are used to denote the sire:
- Yellow Commercial (Rattlerow EBX)
- White Large White
- Red Landrace
- Green Duroc.
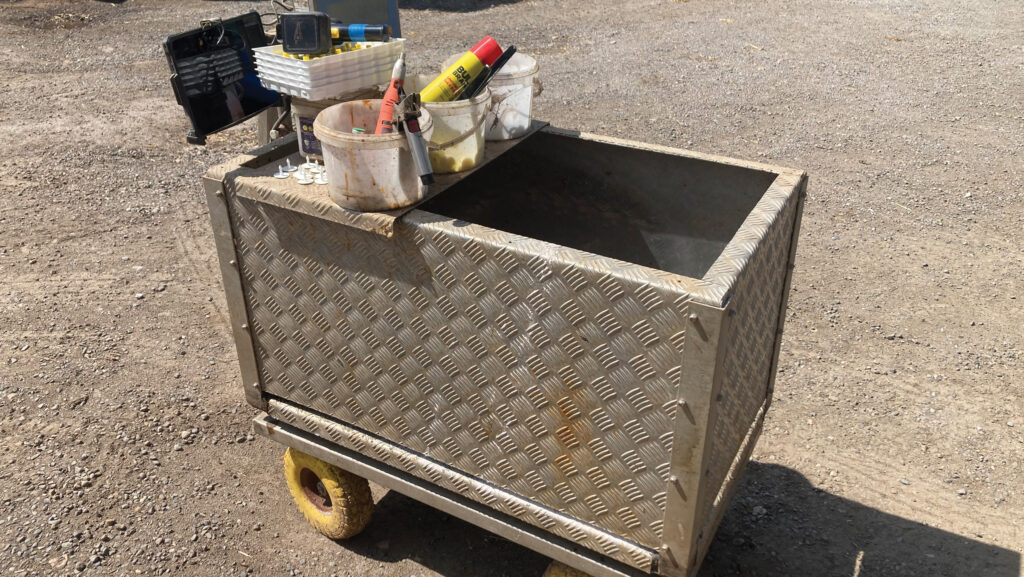
Tagging is done together with weighing © MAG/Michael Priestley
Newborn pigs are tagged and weighed as part of the routine farrowing process, taking less than 30 seconds. Similarly, when weaned pigs are vaccinated (for circovirus and mycoplasma pneumonia), they are also weighed.
Newborns and weaners are weighed on a portable stainless steel trolley scale. For speed, weighing is done by subtraction (weight of pig deducted from the weight of the group).
Slaughter weights for up to three bacon pigs at a time are taken on a weigh crate positioned in the central alley of the growing shed. However, this is a time-consuming task, and the family hopes the abattoir can report carcass data back to the farm instead.
Pigs are not tagged for two months in the summer, when fieldwork and harvest jobs take priority.
The system costs roughly £1 a tag, which covers the tag itself (48p), as well as software, setup costs, consultancy and data analysis.
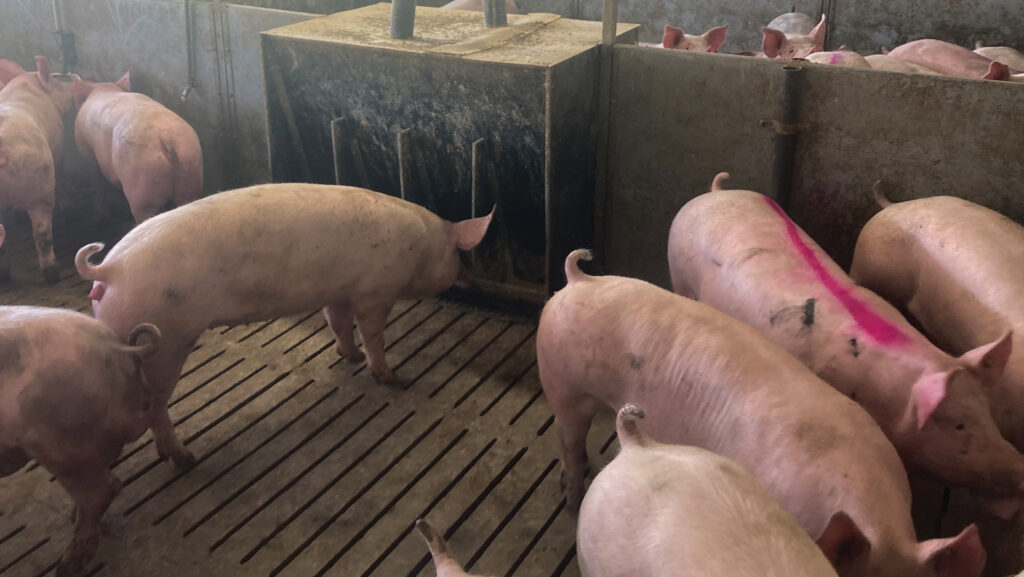
© MAG/Michael Priestley
Data-driven improvements
Benefit 1: Cashing in light pigs
Data
- The farm’s average bacon weight (liveweight) is 110.6kg at 174 days. Some pigs take 30 days longer than the average, with some stragglers and runts taking more than 250 days from birth.
Observation
- At a fixed cost of £2.20 a week and feed cost of £246.20/t, a pig that spends an extra 30 days on farm costs £32.80 more, meaning it is a loss-making animal.
Action
- Slow growers can be identified early in the finisher stage and sold as light pigs to a cutter outlet, saving on cost and earning more p/kg. In the long term, the hope is to identify these piglets early and see if there are problem sows to cull.
Benefit 2: Culling sows on progeny data
Data
- Occasionally, a health issue such as swine erysipelas or Actinobacillus pleuropneumonia can lead to 2-3% mortality in a batch. Sometimes the tags reveal that all mortality for one of the above reasons comes from a single sow in the batch. Pigs with ruptures can also be traced back to sows.
Observation
- Very occasionally, an entire litter may fail to reach slaughter, and one multi-parity sow lost a third of her piglets.
Action
- Culling of a small number of sows has been carried out on the basis that a maternal or genetic issue may be responsible.
Benefit 3: New facility design
Data
- A trial weaning pigs at 6.5-7kg rather than 9kg or more, to assess required farrowing accommodation size in a new building, showed those pigs required an extra 30 days to finish.
- An old farrowing house had growth rates 50g/day lower from birth to bacon weight, costing £10 for each pig put through that shed in variable and fixed costs. Working on a conservative estimate of 11 pigs weaned per farrowing and 12 farrowings a year, a new £6,000 farrowing space would be paid off in four and a half years.
Observation
- Every extra day in the finisher pen costs £1.10 in feed and fixed costs, so investing in larger, freedom-farrowing crates and new facilities is soon paid for.
Action
- A new farrowing house will be built with 6.5 sq m pens that will have sufficient room to wean pigs at 28 days of age or more. This is what the industry wants and what pays.
- Improvements to the worst-performing farrowing house included better insulation and ventilation, brighter lighting and better heating in the creep area.
Farm-specific system
The electronic identification ear tag system has been designed to suit the farm by independent pig and poultry consultant Dom Charman of CharmanAg.
“This system allows the family to evaluate whole-life performance of the finished pig, whereas traditional sow performance evaluation stops at weaning,” explains Dom.
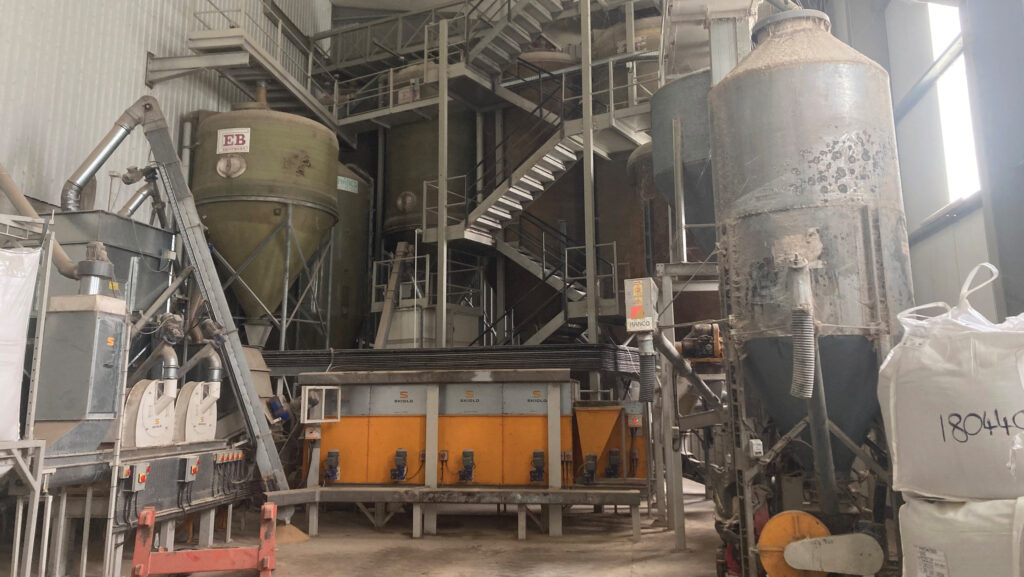
The on-farm feed mill produces 5t/hour © MAG/Michael Priestley
The farm runs a weekly farrowing system, with three breeding units and two finishing sites.
The arable ground produces feed for the pigs and the pig units supply the arable with fertiliser.
Market exposure to feed price volatility is limited by an automated feed mill.
Typically, the farm requires a production of 5t/hour and 90t a week.
The farm makes its own second starter pellet, as well as creep feed, grower and finisher feeds as a meal. Sows are on a wet-feed system.
This means the business buys in first starter pellets for piglets; fish meal; soya meal; soya oil and minerals.
Home-grown wheat, barley and lupins make up the rest of the ration.
Future
In time, the family hopes to integrate kill sheets with breeding herd data.
“But to do that, they need abattoirs to identify individual pigs on the kill sheet so farms can see which ones have specification or condemnation issues,” explains Dom.
This could lead to improvements in health, productivity, traceability, consistency of product and genetics, he adds.