6 steps to optimise milking machine settings for your herd
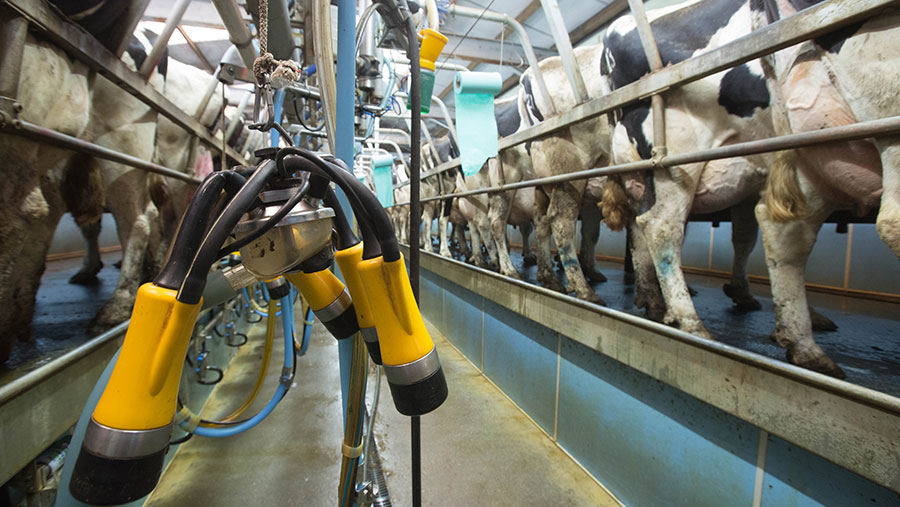
In the past, there were few differences between individual milking machines. But huge genetic variation between dairy breeds has led to significant variation in milk yield, milk flow rates, teat size and teat shape.
The range of milking strategies across different herds is also broader than ever.
This means a one-size-fits-all approach is no longer appropriate, and milking machine performance needs to be adjusted to reflect each individual farm’s situation.
See also:Â How teat health can be used to evaluate milking performance
1. Establish priorities for milking
To establish specific priorities for machine milking, the first step is to assess current performance:
- How is the machine affecting milking efficiency, based on dynamic test results?
- How comfortable is milking for each group of cows based on cow flow, fidgeting and kick-offs?
- What do the teats tell you about milking performance based on herd-level teat scoring?
- Do the milking team have any ongoing problems, such as liner slip or drop-offs?
Herd priorities will vary, but may include shortening unit-attachment time, reducing teat-end hyperkeratosis or teat oedema, improving cow behaviour – less kicking or fidgeting – and eliminating liner slip.
2. Identify limitations to machine performance
Factors other than machine settings may limit performance or even make certain forms of machine optimisation counterproductive. They include:
- Poor milk let-down – if uncorrected, this limits the scope to reduce unit-attachment times
- Herds with naturally low flow rates – these may need more gentle machine settings
- Pointed teat shapes – these are more prone to hyperkeratosis and require different milking conditions
- A wide range of cow types within the herd – compromises in performance may be necessary to ensure all sections of the population are milked safely and comfortably
- Restrictions in the flow of milk away from the cow – these can prevent the machine settings from translating to the intended performance at cow-level.
A pragmatic approach to achieving milking priorities may be needed where these limitations apply.
3. Vacuum settings
Conversations about vacuum often refer to system vacuum or the figure displayed on the vacuum gauge.
However, to give a reliable indication of vacuum at cow level, the vacuum inside the short milk tube of the liner needs to be measured during milking.
The short milk tube vacuum is affected by how much vacuum “reaches” the cluster (basically system vacuum minus losses) and how effectively the machine is at moving milk away from the cow.
Inefficient machines may have substantial drops in short milk tube vacuum when cows have very high flow rates.
The target short milk tube vacuum depends on liner choice, and each liner has an optimum working range.
Higher vacuums will promote higher milking speeds, but increase the risk of teat-end hyperkeratosis. Lower short milk tube vacuums increase the risk of teat oedema and slower milking speeds.
4. Pulsation settings
The key measure to consider is the resting phase (D-phase) of pulsation, with rate and ratio being set to achieve the appropriate D-phase length.
Minimum D-phase recommendations are often based on theoretical “perfect” conditions. In practice, a minimum D-phase of 220ms is appropriate for most situations, being both safe and efficient.
Higher D-phases may be required to mitigate effects of drops in short milk tube vacuum in inefficient plants. And some liner types may require specific pulsation phase lengths.
5. Automatic cluster removal settings
Traditionally, automatic cluster removal (ACR) settings in the UK have promoted a very “dry” milking.
With more efficient parlours and faster-milking liners the resultant overmilking is a significant risk for teat-end hyperkeratosis and oedema.
When choosing a flow rate to trigger the ACR:
- Consider your milking frequency – for example, 600ml/min may be suitable for a herd milking twice daily, while 900ml/min may be more suitable for the same herd milking three times a day
- Account for milk let-down performance – poor let-down limits scope for optimising take-off settings
- Remember that milk meters may have variable accuracy in real-world conditions. Recheck for overmilking with a dynamic test after changing settings
- Monitor bulk tank volumes – if volumes are normal three days after adjusting the flow rate, you are not undermilking at a herd level.
6. Detachment settings
Milking units are commonly dragged off the udder while still under vacuum. This is uncomfortable for the cow and increases the chance of bacteria entering the teat at this point.
To avoid this:
- Adjust the lag time between vacuum shut-off and ACR cord retraction
- Aim for the cord to catch the unit just as it drops off the udder, but before it hits the platform
- Ask your engineer to show you how to alter this setting so you can adjust it yourself. There is often a bit of trial and adjustment in achieving the perfect catch.
Quick guide to machine optimisation
- Set priorities for milking using data from dynamic testing, teat scoring and efficiency KPIs
- Be realistic about limitations such as milking team performance, cow anatomy and infrastructure
- Alter system vacuum to give the appropriate short milk tube vacuum for the liners to achieve your priorities
- Review pulsation rate and ratio to give a D-phase that is sufficient for adequate rest, but not longer than this
- Adjust automatic cluster removal (ACR) settings according to your milking frequency and your milk let-down performance
- Audit detachment to ensure the correct delay between vacuum shut-off and ACR cord retraction
About Tom Greenham
Tom Greenham is a director of Advance Milking, a consultancy service for all aspects of udder health and milking machine performance.
Advance Milking works with dairy farms across the UK and Ireland to optimise udder health, milk quality and milking efficiency.
Mr Greenham also provides research, training and independent support to the dairy industry internationally.