Analysis: How hiring apprentices helps solve labour problem
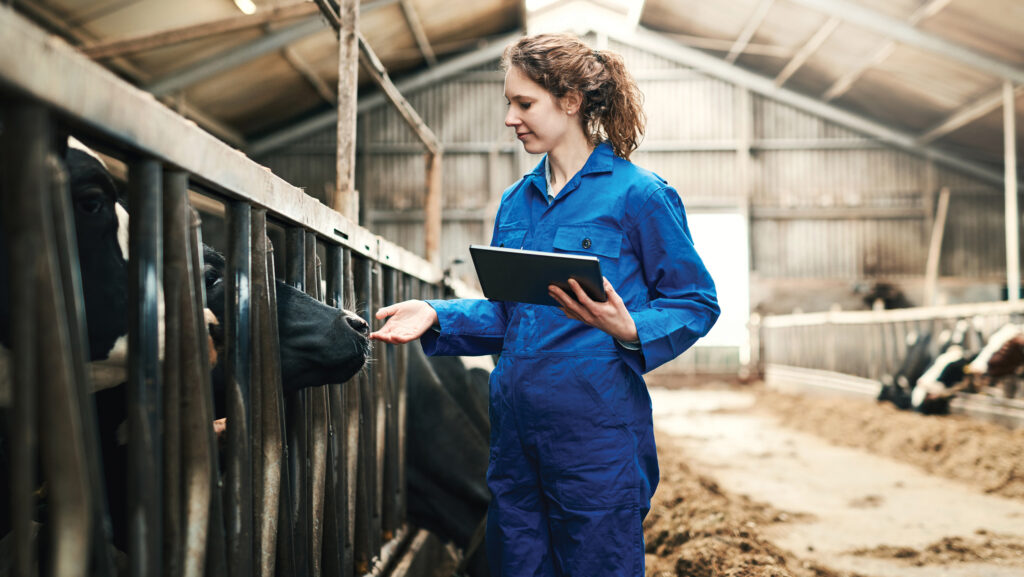
For years, a large portion of the workforce in dairy, poultry and horticulture has come from abroad.
However, since Brexit and with immigration policies tightening, this labour supply is no longer as reliable.
A recent NFU survey found that 77% of respondents struggled to find workers due to a shortage of applicants.
But as the demand for skilled workers rises, apprenticeships offer a valuable pathway to develop a workforce tailored to modern farming needs.
See also: What does the future hold for agricultural apprenticeships?
Tess Howe, head of partnerships and policy at The Institute for Agriculture and Horticulture (Tiah), says:
“As a responsible industry with a struggling workforce, we need to take collective responsibility to ensure we have the workforce of the future.
“Hiring an apprentice is a good way to do this. Together we can help mould the next generation of workers whilst reaping many business benefits.”
Financial incentives
The available financial incentives can be a key factor encouraging employers to hire apprentices.
The UK government provides funding to support apprenticeship programmes, which can alleviate training costs, particularly for small and medium-sized enterprises.
“These financial benefits make it more feasible for smaller businesses to invest in training new staff,” says Steph Stevens, careers and engagement manager at Lantra.
“Apprenticeships are a great way to recruit extra hands without straining cashflow.”
Apprenticeships must last a minimum of 12 months, and the going rate of pay is lower than the standard wage – currently £6.40 an hour.
Employers can also receive a one-off £1,000 payment for taking on an apprentice aged 16-18, or for older apprentices (aged 19-24) if they also provide an education, health and care plan.
Most apprenticeship training costs are also fully or partially covered by the government (up to 95%), enabling businesses to upskill their workforce on a budget.
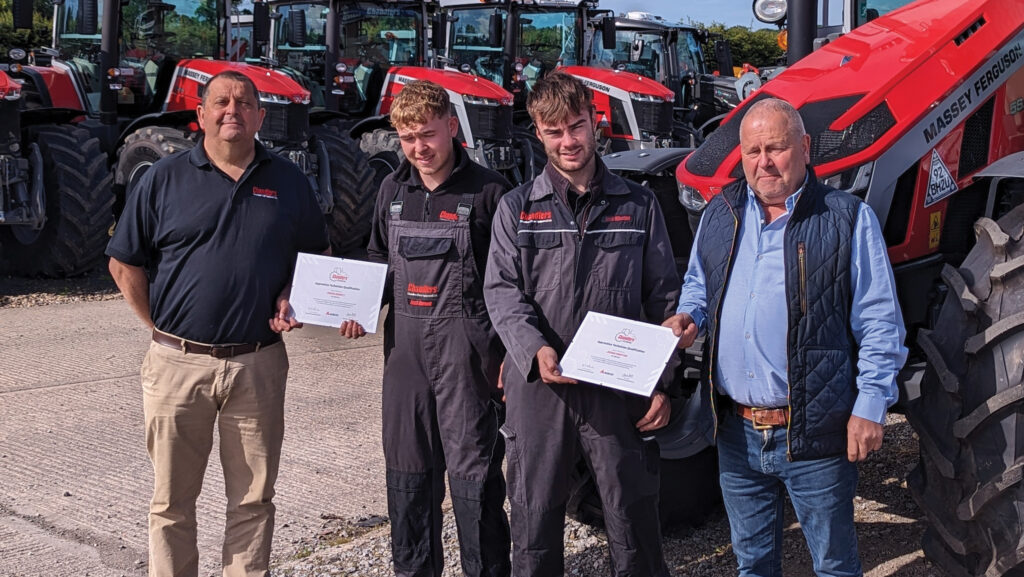
Chandlers in Lincolnshire now has 37 apprentices © Chandlers Academy
Tailored training
According to survey results, 86% of employers say apprenticeships help them develop staff skills relevant to their organisation.
Ms Stevens says: “The apprentice usually comes with the right work ethic, having chosen a sector that demands practical work in all weathers. Employers can shape an apprentice’s skills to align with their specific practices.”
Bespoke training often leads to greater loyalty, as apprentices feel more connected to employers who invest in their development.
Despite the ability to shape skill sets, Ms Howe emphasises the need to focus on the apprentice, not the employer.
“While you can teach them the specific methods you use, there is a required structure to follow,” she says.
“You can certainly train them in your ways, but it’s important to keep the apprenticeship framework in mind.”
Fresh ideas
The government reports that 92% of businesses that hire apprentices see a more motivated and satisfied workforce.
Similarly, Tiah has found that 78% of employers experience a productivity boost as a result of apprenticeships.
Ms Howe says: “When you bring in someone new, especially if they lack experience or have a different background, they bring fresh ideas and challenge the status quo.
“New perspectives push you to consider alternative ways of doing things, which can drive development and improvement.”
This dynamic can foster a more engaged workforce, as existing employees share their knowledge and mentor apprentices, creating a culture of teamwork.
Ms Stevens agrees. “Apprentices come to the industry without bad habits and bring new energy to the business. By bringing in young talent, employers can cultivate essential skills and ensure long-term industry sustainability.”
Strategic recruitment
By promoting their commitment to training and development, employers can attract potential employees seeking opportunities for growth.
Ms Stevens says: “An apprentice can help bring new life into the industry and attract people from non-farming backgrounds.”
Ms Howe further explains: “Apprenticeships bring in new people, ensuring the long-term viability of a business while providing a valuable learning experience.
“Even if apprentices move on, you’re investing in someone for a longer period, which offers stability during their apprenticeship.”
Both Ms Stevens and Ms Howe have observed that retention rates and staff satisfaction are high among employees in apprenticeship programmes.
How to hire an apprentice
The agricultural industry recognises the value of apprenticeships, and several organisations have developed resources to assist employers.
Lantra offers an employer toolkit to help small businesses hire apprentices, providing step-by-step guidance based on extensive research.
These resources help employers navigate the process and make informed decisions about hiring apprentices.
Another approach is to reach out to local agricultural colleges for assistance. In some cases, apprenticeships can be carried out on family farms, if suitable.
Information can also be found on the UK government website.
Q&A: How taking on apprentices can benefit both parties
Andrew Silvester, academy manager, Chandlers Farm Equipment, Belton, Lincolnshire.
Why did you start offering apprenticeships?
The farming industry is facing an ageing workforce.
Investing in apprentices not only secures the future of our business, but also ensures we’re not relying on others to fill the experience gaps.
Apprentices bring fresh talent and help us grow sustainably.
How long have you been offering apprenticeships?
We’ve always had apprentices, but since launching our academy in 2021, we’ve seen the numbers grow. We now have 37 apprentices across different year groups.
We focus on land-based service technicians and partner with Agco and JCB, offering training on products such as Massey Ferguson, Fendt, Valtra and JCB.
Why are apprenticeships so important for agriculture?
Agriculture would struggle without apprentices. As the workforce ages, we need fresh talent to step in.
Apprentices not only fill the gaps left by retiring workers, but they’re also trained in new technology and sustainable practices.
They bring new ideas and, under the guidance of experienced technicians, learn to adapt to the industry’s ever-evolving challenges.
How do apprentices impact skill development?
Apprentices really make a difference, especially when it comes to safety. They bring a fresh set of eyes, helping us spot areas for improvement.
With 80% of their training done in-house, they’re developing the specific skills we need, which boosts productivity and quality across the board.
What about productivity and costs?
Yes, apprentices need mentoring, which can take up time from our experienced staff in the short term. But the long-term benefits are huge.
We’re investing in a skilled workforce that helps drive productivity and reduces the costs associated with hiring experienced technicians who come with higher salaries and recruitment fees.
Apprentices also spark innovation and creativity in the team.
What’s your retention rate?
Our retention rate is 89.5% for apprentices who complete their qualifications.
Many go on to become full-time technicians, and some have settled down, started families, and see Chandlers as more than just a job – it’s a place where they can grow and build a career.
What’s the future of apprenticeships at Chandlers?
Our apprenticeship programme has been a real success. We’ll keep investing in apprentices to ensure we’re developing skilled technicians who are aligned with our values.
By bringing in young talent, we not only secure our future, but also help raise our profile as a company that values learning and growth.
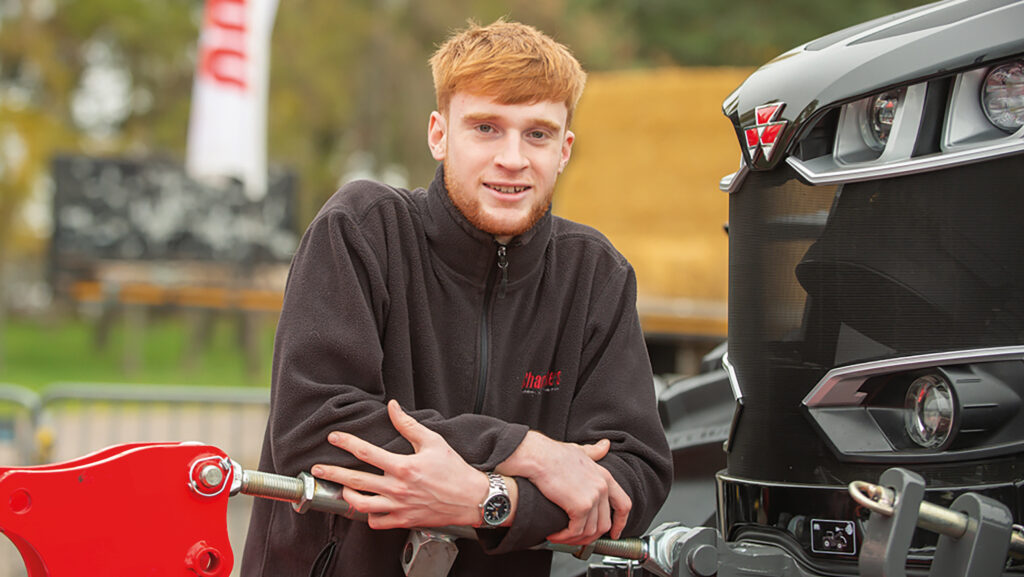
Apprentice Kieren Snowden © Chandlers Academy
Kieran Snowden, 23, land-based service technician apprentice at Chandlers, Belton
What motivated you to choose an apprenticeship in agriculture?
My grandparents lived and worked on a farm in Chelmsford, so from a very young age I was involved in the agricultural sector and got the farming bug there.
I developed an interest in the machines and decided to pursue a career in the industry after taking a year out to work for a local agricultural engineer.
What aspects of the apprenticeship attracted you most?
No two days are the same, and the satisfaction of completing a job is a great feeling. Playing with kit of all sizes is also a bonus.
My favourite kit is the Fendt 1050 Vario tractor as it has 517hp – alongside all the other Fendt products.
Any challenges?
The greatest challenge I face is learning the ins and outs of new products to conduct and provide a good service.
How has your apprenticeship helped you understand the agricultural industry?
I feel very fortunate that my working day varies; I could be in the workshop in the morning and then out on site in the afternoon.
There’s always something to do, so there’s never a boring moment.
What do you consider the biggest benefit of being an apprentice?
Earning while learning is a huge bonus, but the most important element is knowing that I will receive an up-to-date, industry-recognised qualification.
What advice would you give to someone considering an apprenticeship in agriculture?
Go for it. It’s an enjoyable and rewarding path.