40 years on an arable family farm – challenges and changes
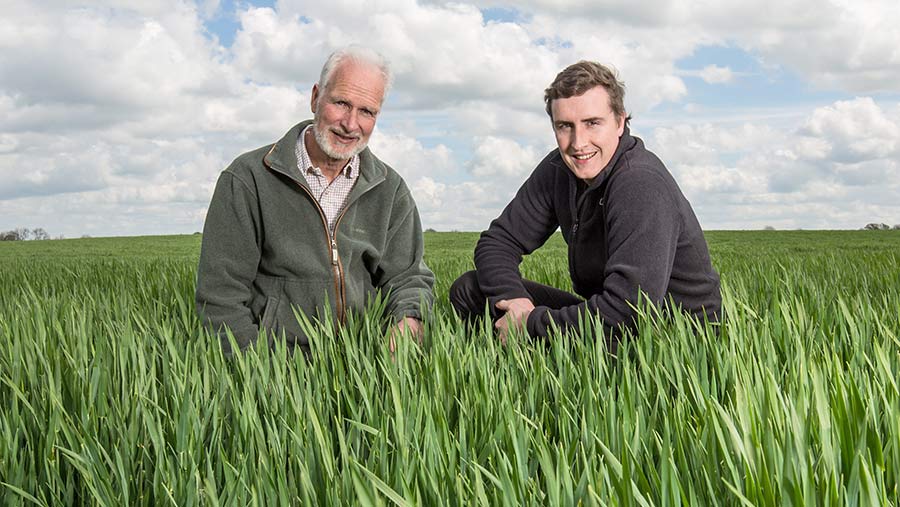
In the past 40 years, the Parker family has transformed Sherwood Farms from a traditional mixed farm to a technical arable enterprise, which is also home to 72,000 laying hens.
The 600ha Leicestershire farm, which has been in the family since the 1940s, has seen vast changes.
The area has doubled and winter wheats yields have risen from 4.5t/ha in 1979 to 11t/ha today on soils that range from heavy clay to sandy loam.
Michael is keen to carry on his father James’ good work, and with a cross-generational perspective, the pair hope to boost business efficiency and produce crops as economically as possible..
See also: Why one grower went organic to tackle blackgrass problem
The Parker Family at Sherwood Farms
James Parker
• Age: 65
• Started farming in 1976 and took over from his dad, Philip Parker, who was the first generation of the Parker family at Sherwood Farms
Michael Parker
• Age: 27
• Joined the family business after returning from Harper Adams University in 2014
What were the biggest challenges at Sherwood Farms when you first began farming?
James Parker (JP): The first 20 years of my time farming was spent building up the business and modernising buildings.
We had to update all existing sheds, particularly the laying and rearing units for the poultry enterprise.
We also established the packing shed, where we now pack 70,000 eggs/day and supply wholesalers.
Michael Parker (MP): Blackgrass is our main challenge now.
When my grandfather was farming, all fields were ploughed with a chisel plough, pulled by a Ford 7000 with solid metal wheels.
We haven’t used a plough in 20 years and are looking at different ways to resolve the weed issue by cultivating shallower, reintroducing spring crops and using cover crops.
So far, we have used a cover crop mix of wheat and vetch, but we are now looking at changing wheat as this is increasing take-all risk.
A Simba 23C set of discs working at a depth of 15-20cm replaced the plough, but for the past five years we have used a Vaderstad Carrier disc cultivator, working at a maximum depth of 5cm.
How have your rotation and cropping plans changed over the years?
JP: In 1976, the rotation initially included spring barley, sugar beet and grass leys for the 400 head of cattle and sheep.
We then switched to winter cropping, growing winter wheat for more than 30 years, which was very profitable for us.
We stopped growing sugar beet 40 years ago as it was too difficult to grow this crop on our heavy land.
MP: Five years ago, we reintroduced spring crops into our rotation (once in four years) to tackle our blackgrass issue.
We also began growing triticale eight years ago to eliminate second wheat crops in order to boost margins. Spring linseed was added two years ago.
The first linseed harvest yielded poorly, with less than 1t/ha as a result of poor establishment and flax beetle damage.
This year, however, yields averaged nearly 3t/ha after we doubled the seed rate and were lucky with the weather, which enabled the crop to get up and away quickly, with no flax beetle problems.
What has been the best machinery purchase from your generation?
JP: We built conveyors in the grain store in 2014, which allowed an easy transition of grain from the dryer, straight into the shed.
We used to run around with a tractor and loader, which was very time consuming, but the conveyors have saved time and fuel.
MP: Our latest machinery purchase will be a Sly Boss minimum tillage drill, which I hope will help tackle our blackgrass problem and have huge cost savings, by reducing the number of passes and cutting fuel costs.
It has been challenging to convince Dad that this will be good purchase, as we have always used tine drills rather than disc drills on the farm, but he’s slowly coming round to the idea.
The new drill will also enable us to sow companion crops, creating new opportunities for growing oilseed rape and other crop mixes.
What are you doing to help future-proof your business for the next generation?
JP: We have a diverse range of enterprises that help spread risk across the farm business.
These include arable, laying hens and 450KW of solar panels across a mix of roof-tops and fields.
We also have a green waste removal business, where we take the local council’s garden waste once a week, and a small horse livery.
We have an on-farm biomass boiler that helps cut costs by using straw bales to heat the poultry rearing sheds to a temperature between 32-34C, for chicks that are one day old.
On average, 1.5 bales of straw are used every day with linseed and OSR straw used, as this generates more heat than wheat and barley, which we instead sell to local dairy farmers.
We are also considering bringing back grass leys into our rotation.
MP: I am really focused on improving our soil health so that our system is easy to manage.
We are currently spreading 2,000t of green compost and 3,000t of chicken manure at 19kg/t of nitrogen across the 600ha each year with soil organic matter levels at 7%.
We are going to implement a controlled traffic farming system with 36m tramlines, where machinery will pass multiples of three (12m) in order to minimise compaction risks on our soils.
However, there are difficulties with this system when it comes to picking up straw bales.
Increasing our area of cover crops is another priority in boosting soil health.
Although I’m not the biggest fan of sheep, I feel that in the next five years they will be back on farm and used to graze off cover crops.
I also think that in the next 10 years there will be huge changes in how the arable industry operates, with new developments in robotic technology.
This is definitely something we would be interested in here at Sherwood Farms, as robots are able to work 24 hours a day, which would bring increased efficiencies.
Most valuable thing you’ve learned from each other?
JP: Michael is always helping me out with the computer work in the office, whether it’s with a Word document or on the mobile phone.
MP: Learning how to grow a good crop.
I’ve been to university and studied agriculture, but there’s nothing quite like being at home and learning on the job with your family.
What is your best farming memory?
JP: Moving back to the family farm.
MP: When Dad said that he would never get the sprayer stuck and later that day that’s exactly what he did…
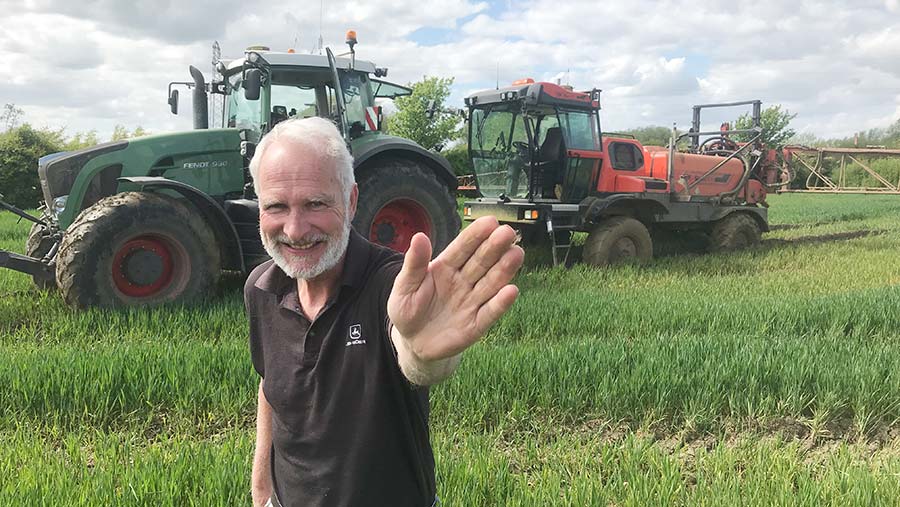
© Michael Parker
What has been the greatest short-term challenge the farm has been faced with recently?
JP: The weather this autumn has been extremely challenging for us. We planted 90ha of winter wheat and only 30ha is surviving, as soils are completely waterlogged.
No winter barley or triticale will be grown this year either as we haven’t been able to get on the ground.
MP: Establishing oilseed rape since the neonicotinoid ban has been a major challenge for us, with yields dropping from 5t/ha to 2.7t/ha.
We normally grow 140ha, but this year we planted just 100ha.
Destruction from cabbage stem flea beetle and slugs has left just 40ha surviving.
We have tried drilling late and leaving volunteers in neighbouring fields to distract the pest, but these methods haven’t worked.
Now and then
2019
• 600ha arable (OSR, wheat, winter barley, triticale, beans, spring barley and spring linseed)
• 72,000 laying hens producing 50,000 eggs/day
• Two Fendt 724 tractors
• Fastrac 2170
• New Holland CX8.85
• Amazone Cayena
• One full-time arable worker, 20 across all enterprises
1976
• 300ha arable (spring barley, sugar beet, grass leys)
• 30,000 laying hens
• 200 cattle
• 200 sheep
• Ford 7000, Fordson major, four Ford 5000s
• International 611 tine drill
• Four full-time arable workers and additional part-time workers during harvest, plus 20 more on other enterprises