Livestock Event 2014: Tips to increase slurry storage this winter
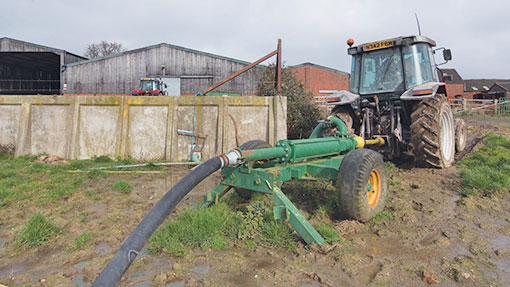
Slurry storage and handling is a big concern for livestock farmers, especially after wet winters. Paul Spackman examines the options for increasing capacity.
When slurry stores fill quicker than expected and storage capacity gets tight there are several options open to farmers.
Start by identifying all ways water enters the system and where clean water can be diverted away from stores, says DairyCo extension officer Richard Davies. Yard and silage pit runoff is a big contributor so covering such areas may be an option. But this is often difficult and costly, so other options may be more appropriate, he says.
“Do the simple things first, like ensuring gutters and downpipes work properly to take roof water away. Once you’ve done all you can to keep clean water out then look at other options like separators or extra capacity.”
Slurry separators
Separating slurry into solid and liquid portions can be a cost-effective way of increasing capacity, says Mr Davies.
“Separators give you around 20% extra storage depending on the type of bedding used. But they cost money to install and run, and they add complication to the slurry system.”
A typical separator has a 5-10kW motor, but a pump (maybe another 10kW) will also be required. Running costs vary considerably, but separation systems typically run for 1-2 hours a day per 100 cows, he says. Timers let you keep costs down by using cheap-rate electricity at 6-7p/kWh instead of nearer 12p/kWh.
Storage space is needed for the solid portion, but generally separation makes the liquid easier to pump and apply, especially as it does not leave the same taint on grassland that unseparated slurry does, Mr Davies adds.
Build more slurry storage
Building additional storage is the obvious way to relieve pressure on existing capacity, but it is costly, site-specific and planning may be an issue.
Concrete or metal tanks can be the most flexible option in terms of location, but they are expensive, typically costing ÂŁ30-40/cu m of storage, says Mr Davies.
Lagoons are considerably cheaper at £5-10/cu m, but they need the right site and take up a large area. “It’s possible to have a lagoon for 200-300 cows with a footprint of one acre.”
Extending an existing earth bank, clay-lined lagoon is one of the cheapest ways of increasing storage capacity, but is reliant on having enough space and the right site to do so, Mr Davies says. “It is possible to extend plastic-lined lagoons, but it’s quite a challenge and more expensive.”
Constructing an off-site lagoon may be worthwhile if space is limited around the main store. Slurry can be periodically pumped out of one store into the lagoon, which may be strategically situated closer to where slurry is applied.
“You can use a contractor and lay-flat hoses to pump slurry, so you don’t have to buy the kit yourself.”
Planning may be required to extend or build a new store, so Mr Davies advises farmer to check with their local authority. Getting the Environment Agency involved at an early stage can also be worthwhile, as they can provide a covering letter to support the need for additional storage.
Worthwhile investment
Installation of a slurry separator at Plas Meifod Farm, near Denbigh in North Wales, cut slurry storage requirements by around 25%, says Rhodri Wynne.
The separator was installed two years ago at the same time as the underground slurry store was extended to 2.25m litres, ahead of an increase in cow numbers. It cost ÂŁ60,000, but was part-funded by a 40% Glastir grant.
The system handles all slurry and dirty water (including yard runoff and parlour washings) from the 160 milking cows, plus 250-300 youngstock from a heifer-rearing enterprise. “In a normal winter we have about five months-worth of storage,” says Mr Wynne.
The 5.5kW separator and 11kW pump run on a timer for five hours a night to use cheap-rate electric.
Solid material is collected in a 9t silage trailer and stored in empty silage clamps until it can be spread on maize ground, or after first-cut silage. “It’s a fine material that spreads easily and is a good soil conditioner,” says Mr Wynne.
A contractor pumps and spreads stored liquid using an umbilical and trailing shoe system, at a cost of £65-75/hour. “We’re normally putting on about 2,000gal/acre every month from May onwards. It’s much better to use than slurry and cows can graze soon after.”
It provides a readily available fertiliser source, with typical analysis of 10.5 units nitrogen per tonne, five units phosphorus, and 10 units of potash.
All roof water currently goes to a soakaway, but Mr Wynne is considering rainwater collection.
Slurry lagoons are a much cheaper storage option than building metal or concrete tanks.
More information on Cost–effective slurry storage on farms and Effective water use on dairy farms