Farmers Weekly 2024 Awards: Pig Farmer of the Year finalists
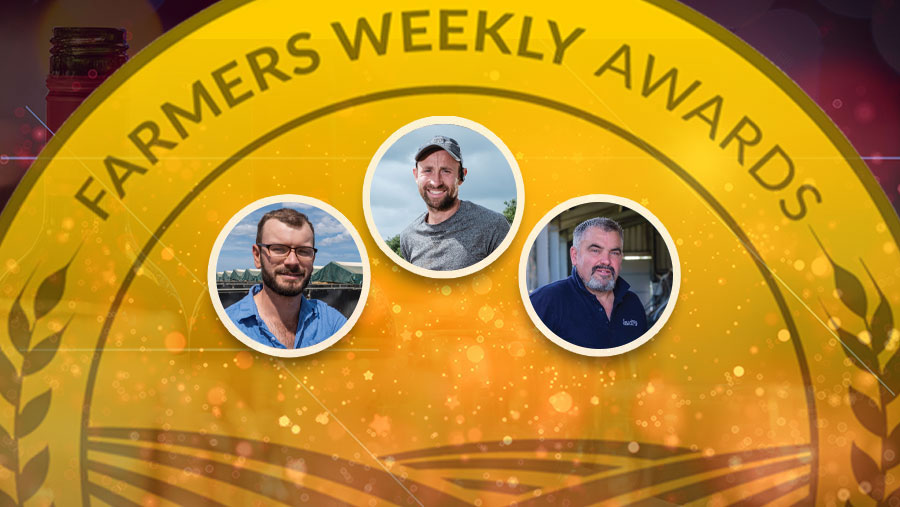
Three varied producers – an outdoor breeding unit, a tented nursery and an indoor finisher – all displaying sound business mind and a keen eye for detail.
The finalists
- William de Feyter, Dyballs Farm, Norfolk
- Paul Howland, Shingle Hall, Suffolk
- James Ross, BQP, Lincolnshire
The judges
Katie Jarvis Senior policy adviser for the National Pig Association, Katie has worked in agricultural policy for several years in the UK and Brussels.
Guy King Farmers Weekly‘s 2023 Pig Farmer of the Year, Guy is a first-generation farmer with more than 40 years’ experience in the pig industry. Today, he runs nine outdoor units in Norfolk and Suffolk.
Charlotte Cunningham Freelance journalist and former Farmers Weekly deputy livestock editor, Charlotte started her career in dairy and now writes across the breadth of the livestock industry.
See also: Farmers Weekly Awards 2023: Pig Farmer of the Year
William de Feyter, Dyballs Farm, Norfolk
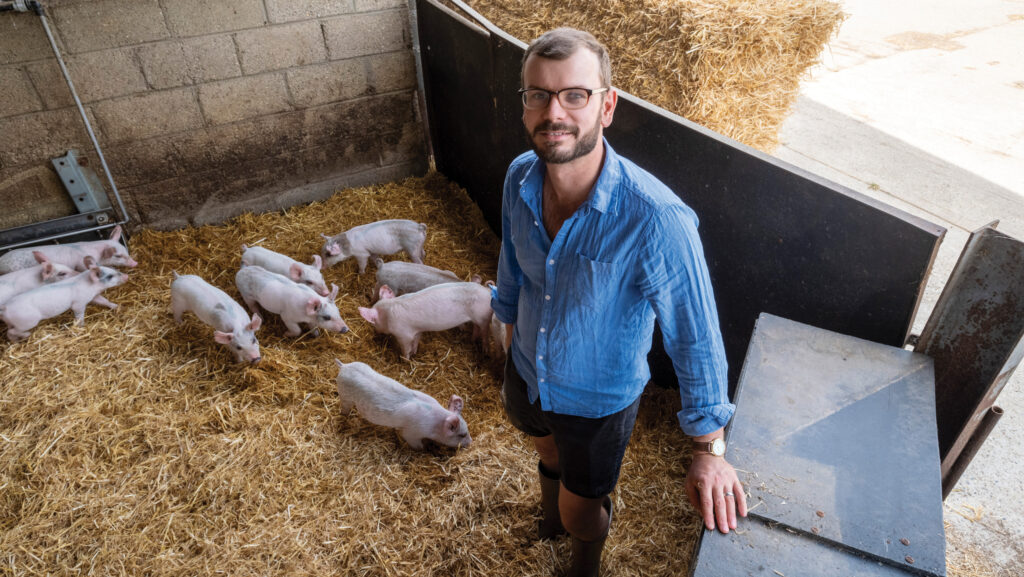
Williiam de Feyter © Jason Bye
While William de Feyter is an arable farmer’s son, he realised he was more interested in four legs than four wheels while “earning his beer money” on the pig unit at Harper Adams University.
He came home in 2014 with a desire to incorporate pigs into the family business and began his venture by renting sheds from his father and finishing 160 pigs for BQP.
“It was the starting point for William de Feyter – pig farmer,” he says.
Two years later, the opportunity arose to take on another unit – an 850-head, wean-to-finish indoor unit.
However, this was short-lived after the buildings were redeveloped for holiday lets.
Taking on a 450-place indoor nursery unit instead (rearing pigs to store weight) filled a void, then an opportunity to purchase 35 second-hand tents in 2022 allowed William to pivot in a new direction.
He set them up on 4ha of grassland, rented from his parents and signed a five-year agreement with BQP to rear 4,200 pigs from 7kg to store weight, in partnership with his wife, Sarah.
The system
Piglets (supplied by BQP) arrive on farm at five-weeks-old and leave after eight to nine weeks when they weigh 40-50kg.
On arrival, they are split-sexed and vaccinated for enzootic pneumonia, porcine circovirus type 2 and porcine reproductive and respiratory syndrome (PRRS), using intradermal vaccines to reduce recover time for the piglets.
Extra troughs are put in place for up to 10 days after arrival to facilitate greater feed space, which has led to creep feed being eaten quicker and subsequent improvements to daily liveweight gain.
After this, they move onto a weaner ration, followed by grower pellets during their last week on farm – all supplied by BQP.
The smalls from the tented nursery are finished at the 160-place home farm to ensure the onward finisher farms only receive the best pigs he has to offer, says William.
Each tent holds 120 pigs, on average, and is bedded with straw, provided for all three units via local muck-for-straw agreements.
“Straw usage is recorded after every time the pigs are bedded up to help manage straw stocks and ensure those in the straw-for-muck agreement receive the correct amount of muck.”
Technology
Each unit is equipped with a select doser, but following a salmonella outbreak, a second select doser was installed along with an additional water line, which has enabled specific treatment and more responsible usage of antibiotics, says William.
Pigs from different sources are not mixed, to minimise disease outbreaks, and he works closely with the vet to implement a quarterly updated herd health plan.
The future
William has recently applied for the Annual Health and Welfare Review to improve biosecurity and understand how he can tackle PRRS, if there was ever a breakout on-farm.
He has also sought grant funding – via the Farming Equipment and Technology Fund – for another loading ramp and hurdles to make a semi-permanent race/lairage for loading pigs out and unloading piglets, which should improve loading times.
The outdoor nursery was budgeted on a three-year payback, which William will have achieved by next year.
“This, in turn, will allow the business to look at purchasing more tents for the existing site or, if a significant number can be acquired second-hand, the potential is there for another site to be set up.”
The numbers
- 2.81% average mortality in tents
- 614g/day average daily liveweight gain in tents
- 1.9:1 average feed conversion in tents
- 120 average number of pigs in tents
- 2 self-employed pigmen: John Bell and Toby Pearce
Farm facts
- 4,810 pigs, split across three units
- 4,200 in tents and 450 indoors
- Rearing five-week weaned pigs to store weight
- Up to 160 smalls finished indoors
- Red Tractor and RSPCA assured
The judges liked
- Innovation and motivation to build a business from scratch
- Sound business acumen applied to all areas
- A clear understanding of areas to improve with action plans to achieve this
- Strategic use of technology
- Abundant ambition
What the judges say
“Despite William’s business being relatively young, he has already proven its value. He demonstrates applaudable business acumen and there is no doubt it will continue to be a success.”
Paul Howland, Shingle Hall, Suffolk
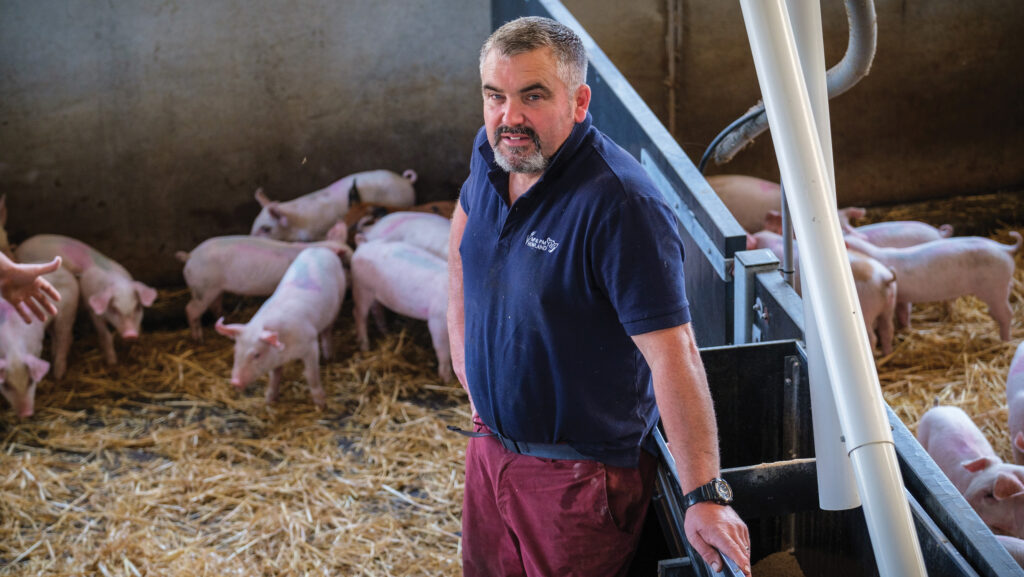
Paul Howland © Jason Bye
Paul Howland can peg his passion for pigs right back to being two years old and watching his father farrow a sow on the family farm in Essex.
Since then, the family has moved around settling at Shingle Farm when Paul was 18, but dipping in and out of pig production, running alongside an arable business.
Paul established his own herd in 2010 on a contract finishing agreement with BQP.
“We put up the first shed in 2010, and then in 2012, put up a second [enabling] us to hold 1,500 pigs in total,” he says.
The system
Weaned pigs arrive on-farm at five weeks old and are vaccinated and separated into male, female and smalls, using a sexing and injecting table to minimise pig stress and streamline the process.
Feed is provided by BQP, with specific rations tailored to each stage of the growth cycle. While Paul has little involvement in this, he works closely with the company to improve quality.
“I have held trials looking at different rates of blowing the feed in, as well as different engines which blow differently.”
He also sieve-tests every load to ensure he is feeding only the best quality to his pigs.
Inside the shed, beds are straw-based, with Paul supplying extra straw to ensure both pig comfort and provide material for enrichment.
Feed spaces have recently increased from five to eight, which has resulted in less queuing time at the feeder for bigger pigs and has also led to a dramatic reduction in tail-biting.
“This can only be a positive thing,” he says. Drinking stations have also increased from five to nine nipples a pen.
Technology
Electric curtains have been fitted to both sides of the shed and are wind, rain and temperature controlled.
Water consumption is monitored digitally – with text alerts set up to notify Paul of any changes to consumption levels.
Two years ago, he fitted solar-powered cameras to the feed bins which take photographs of feed levels and predict how many days’ worth of food is left in each silo.
“This makes ordering food a week in advance a lot more effective,” he explains.
Herd health is major priority for Paul, who works with his vet to implement a robust health plan.
“I’m not in control of the health of the pigs that arrive on farm, but I always do my utmost to pull them around.”
The batch is depopulated typically at 18-20 weeks, though his most recent batch left the farm at 17 weeks and 4 days.
Between batches, the units are stripped out, cleaned and disinfected and left to sit for two weeks before the next batch arrives, with the muck utilised by the arable operation.
The future
Plans are in motion to improve the environmental impact of the farm.
This includes muck and soil analysis to better understand the value of the muck being provided to the arable side of the business, as well as covering the muck heap, and recently joining the Sustainable Farming Incentive.
Paul would also like to expand the pig side of the business, and hopes this will be made possible when his son returns home from Australia in the near future.
Following his own challenges with mental health, Paul spoke at the Yana conference this year and says this is also something he’d like to be able to do more of in the future.
“Farming is a lonely way of life – the biggest thing I’ve learnt is we need to talk more, offload problems, and when someone offers help, say yes.”
The numbers
- 1.73% mortality rate
- 0.98kg/day average daily liveweight gain
- 124.1kg average liveweight at depopulation (between 18-20 weeks)
- 2.14kg/day average daily feed intake
- 17 weeks and 4 days for batch start-to-finish period
All figures according to last batch, July 2024
Farm facts
- 1,500 pig straw-based bed and breakfast unit
- Finishing pigs for BQP
- Situated on 240ha arable farm
- Red Tractor and RSPCA assured
- One full-time employee: Jimmy Balls
The judges liked
- Good production across his business
- Good use of technology to improve pig welfare and comfort
- Great working relationship with BQP, so he is able to push for improvements and new technological solutions
- Openness to discuss mental health in farming and offer solutions to improving it
What the judges say
“Paul’s enthusiasm and passion for his pigs is clear. He has an innovative mind and is constantly working with his supplier to improve both production and wellbeing of his animals.”
James Ross, BQP, Lincolnshire
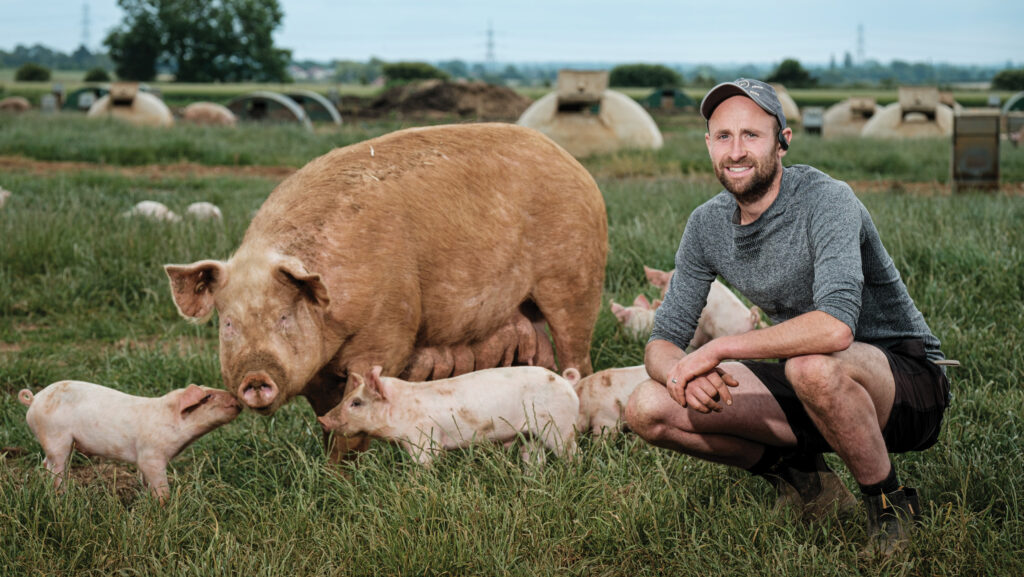
James Ross © Jim Varney
Despite a non-farming background, James Ross has been working in the pig sector since he undertook a Higher National Diploma at Cannington College, Somerset, learning his trade at a local indoor unit between his studies.
After failing to secure a job in the UK, put down to lack of experience, pig recruitment specialist Roadhogs found James a position on an outdoor unit in Iowa, US.
Once he had progressed to a managerial role, he returned to the UK with his new skills and worked on a new unit in Dorset.
In 2018, he headed to Lincolnshire to set up what has now become a 1,750-sow business, where he is farm manager.
The system
Two outdoor units run on a two-week batch, five-week weaning system, producing weaned pigs for BQP.
While both farms operate independently of each other (including staffing and machinery), Dyke Farm is a multiplier herd, producing its own replacements and F1s for Elms Farm.
The highest index animals – according to PIC Pictrac – are served to pure Landrace to achieve genetic gains, with purebred female Landrace piglets tattoo tagged at birth.
“[This] is to build up a herd index and allow each piglet to be traceable through her mother’s and father’s lines,” explains James.
Replacement boars and gilts are grown to 10 weeks and then serviced, with the F1s, served with Large White semen, moving onto Elms Farm at this point.
Aardvark XL farrowing arks are used to house sows, set up in a radial to enable easy handling and serving in the central insemination tent.
James has a very strict breeding/culling policy – taking into account factors including posture, conformation, index, and a minimum of 16 teats.
Over the past 18 months, porcine reproductive and respiratory syndrome epidemic (PRRS) has had a huge impact on performance.
However, James acted quickly, doubling down on biosecurity (including a full vehicle wash upon entry) and implementing a mass vaccination programme.
This has paid dividends, leading both farms to recover.
“The figures for Dyke Farm are now better than pre-PRRS levels,” says James, who credits the hard work of his staff (he has seven full-time employees and one part-time) saying: “None of it would be possible without their hard work.”
Technology
A whiteboard and Whatsapp group play a key role in the success of his management, enabling all staff to keep up to date with exactly what is required on a day-to-day basis.
Outside work, James takes staff on regular comedy nights, meals out and trips to the cinema as he believes this help improves team cohesion on farm.
Thorough training is also provided to all employees to ensure they know the farm wants to invest in them.
In terms of environmental protection, James establishes grass leys before re-siting pigs, to protect the soil and improve structure, with grass strips and wildflowers on headlands to aid pollinators. Recycling and reusing, as much as possible, is also key.
Future plans
James has aspirations to increase weaning weights to 10kg and also achieve 30 pigs a sow a year. He plans to do this through improvements to feeding – particularly for gilts. He also wants to continue to drive forward genetic improvement.
“We can be at the leading edge of genetic improvement by only serving our highest indexed animals to pure Landrace semen. [As a result], we will be increasing our average herd index figure [and] constantly improving the herd.”
The numbers
- 9kg average weaning weight
- 28.5 pigs weaned a sow a year
- 2.2 litters per sow a year
- 14.7 pigs born alive a litter
- 12.8 weaned pigs a litter
Figures for Dyke Farm
Farm facts
- 1,750 sows across two outdoor units, Elms Farm and Dyke Farm in Lincolnshire
- Operating on a two-week batch, five-week weaning system on both units, producing weaned pigs for BQP
- Using largely single-sire purebred Landrace genetics
- Red Tractor and RSPCA assured
- Seven full-time staff and one part time, plus James and business owner
The judges liked
- Attention to detail across two separate businesses to ensure they run symbiotically
- Careful breeding policy prioritising both genetic gain/performance and animal welfare
- Rigorous biosecurity
- Clear display of resilience, ambition and tenacity when facing challenges
- Good approach to staff retention and business management
What the judges say
“This business is reaping the rewards of James’ passion for pigs and keen eye for detail, from production figures to staff retention.”
A word from our sponsor
“As the UK’s number one higher-welfare pig farmer, we are delighted to sponsor the Pig Farmer of the Year award. Congratulations to this year’s finalists – all three are shining advocates for the British pig industry.”
Fábio Brancher, operations director, agriculture, Pilgrim’s Europe